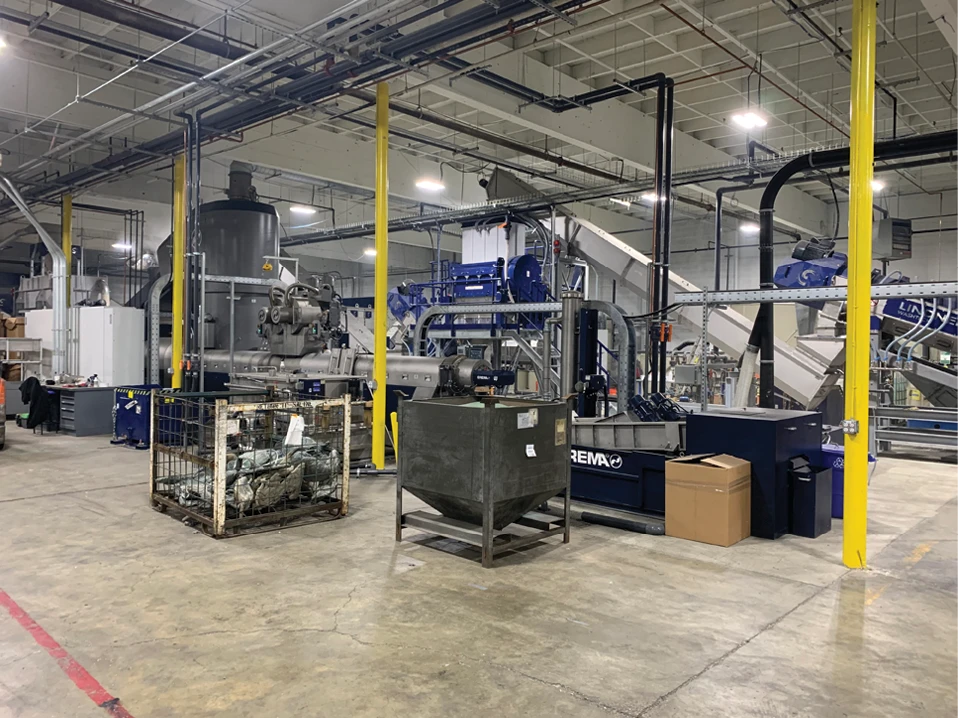

ACI Plastics began implementing sorting technology about 25 years ago; however, the Flint, Michigan-based thermoplastics processor and recycler became more focused on sorting and separating technologies about 12 years ago.
The company began removing paint from car bumpers in 1998 and separating instrument and door panels in 2001. About 12 years ago, Melton says he noticed some of its customers were using scrap without sending it to ACI Plastics for processing.
“They were taking the easy scrap and reusing it,” Melton says. “That led me to working on commingled scrap that they can’t separate in-house without more equipment. For at least the past 12 years, we have been focusing our business on separating commingled materials.”
ACI Plastics operates facilities in Flint; Columbus, Nebraska; and Liberty, South Carolina. The company can shred or grind 34 million pounds of material per year and separates 17 million pounds of material annually across its three locations. It also extrudes about 50 million pounds of material annually and removes paint from about 12 million pounds of material per year at its Flint facility.
“We process mostly materials that require some sort of separation: removing paint [as well as] separating auto parts that have foam, skin, metal [or] other plastics,” Melton says.
“Demand for what we’re doing is very strong.” – Scott Melton, president, ACI Plastics
ACI Plastics applies several technologies to sort incoming material, including density separation, electrostatic separation, fine and metal sorting and optical sorting. The Flint site features all these sorting technologies, while the Columbus facility features fine, metal and density sorting and the Liberty facility features fine and metal sorting. Across the company’s three locations, Melton says ACI tries to use the same type of grinders, float-sink separators and metal separation systems.
Each location uses different equipment depending on its processing needs. For example, the company uses density separators in Flint and Columbus to separate medical syringe bodies to recover polypropylene (PP).
“We remove the needle, plunger rod [and] rubber stopper by sinking them out and floating the PP,” Melton says.
When recycling automotive scrap, ACI uses a float-sink separation system to separate coextruded automotive parts by density. That method relies on the specific densities of the various materials relative to the density of the base solution in the tank. Material will sink or float depending on its density. The specific gravity of the base solution typically can be changed as necessary.
ACI uses electrostatic separation at its Flint location to purify streams, removing impurities from automotive materials by separating glass-filled nylon from epoxy sprayed on the parts.
Upgrading capabilities
ACI Plastics has been expanding operations at all three locations over the past few years. Last year, the company invested $4 million to open a 138,000-square-foot facility housed on 51 acres in Liberty to recycle postindustrial and preconsumer scrap supplied by molders across the Southeast. According to ACI, the site provides size reduction (granulation) and proprietary separation processes, with plans to add density separation later this year and extrusion equipment in 2024.

Earlier this year, the company invested $10 million in a new film processing line at its Flint site, making it one of the largest postconsumer film producers in Michigan. The new line can process up to 24 million pounds of film per year and features a shredder and wash line from Austria-based equipment manufacturer Lindner, a twin-screw extruder from Austria-based extrusion equipment provider Erema as well as a water treatment system. That facility also provides size reduction and storage for various other resins, and Melton says these upgrades have enabled ACI Plastics to process A- and B-grade postconsumer film as well as more medical scrap.
“The system started operations Feb. 7, and [we have] been selling every pound we make,” he told Recycling Today this past February. “Demand for what we’re doing is very strong.”
ACI Plastics received funding for the film line investment through a $300,000 Renew Michigan infrastructure grant from the Department of Environment, Great Lakes and Energy and a $150,000 Business Development Program performance-based grant from Michigan Economic Development Corp.
ACI also teamed up with plastic resin distributor Ravago, headquartered in Luxembourg, to ship its recycled plastic pellets to customers throughout the U.S.
Melton says over the past three to four years, ACI has increased the volume of postindustrial and preconsumer medical scrap it processes, including syringe bodies, and produces white or colored recycled PP that has “terrific properties.”
Although medical scrap can pose challenges—such as ensuring the scrap is properly sterilized and free from associated odors and sorting the regrind to remove everything except PP and polyethylene (PE)—Melton says ACI has solutions to recover these materials.
All three of ACI’s facilities process postindustrial medical scrap, and Melton says all three facilities will process postconsumer medical scrap within the next 12 months. The company’s wash lines help to clean the material, allowing the company to efficiently process it.
“There is a large volume of medical waste that is being treated [via sterilization] and sent to landfills,” he says. “We believe this is good material that can be cleaned up, separated, washed and reused. … We are working with some of the generators of the scrap to take it back and put it in some application. We are also working with a virgin [plastics] company who is interested in taking the scrap back and blending it with their virgin and selling it back to the same manufacturer—a true closed-loop PCR program.”
“Recycling is a business of pennies and pounds. We need to have high throughput rates and high volumes to process through our machines because our selling price is lower than virgin, and our costs have to be low.” – Scott Melton
Sorting technologies
Throughout the past 12 years, Melton says sorting and separating technologies have improved to be able to handle a wider variety of material.
“I believe technology is strong enough today to purify most material streams,” he says, adding that optical sorters are doing a better job at sorting black PP from PE, for example, but the technology has a long way to go before its perfected.
Sponsored Content
Labor that Works
With 25 years of experience, Leadpoint delivers cost-effective workforce solutions tailored to your needs. We handle the recruiting, hiring, training, and onboarding to deliver stable, productive, and safety-focused teams. Our commitment to safety and quality ensures peace of mind with a reliable workforce that helps you achieve your goals.
“We don’t currently use optical sorters to separate PP and PE,” Melton adds. “We know the manufacturers are getting better at the process, and these optical sorters are used at many postconsumer recycling locations.
“The European community is leading the charge [with sorting technologies], and the U.S.-based equipment manufacturers are joining the process, making equipment to purify scrap plastic. The need is tremendous to recover this scrap and clean it to the point that it can be used in many high-value applications.”
Although sorting technologies have improved and the need for recycled resin has only increased, the high cost of applying these technologies remains a challenge.
“The biggest challenge is supporting the cost of separating with the sale of the final product,” Melton says. “The low price of virgin PP and PE make it difficult to sell the recovered recycled resin to buyers when they can buy virgin so inexpensively.”
Working with scrap generators to find ways to incorporate plastic scrap into their products is one way to try to ensure recycled resins are purchased on a long-term basis to make up for the cost of sorting, Melton says. ACI also is focused on finding ways to improve the properties and consistency of its recycled plastics.
“I believe the recycling equipment vendors are working on better technology to separate smaller flake size and separate the materials at a higher rate,” he says. “Recycling is a business of pennies and pounds. We need to have high throughput rates and high volumes to process through our machines because our selling price is lower than virgin, and our costs have to be low.”
Get curated news on YOUR industry.
Enter your email to receive our newsletters.
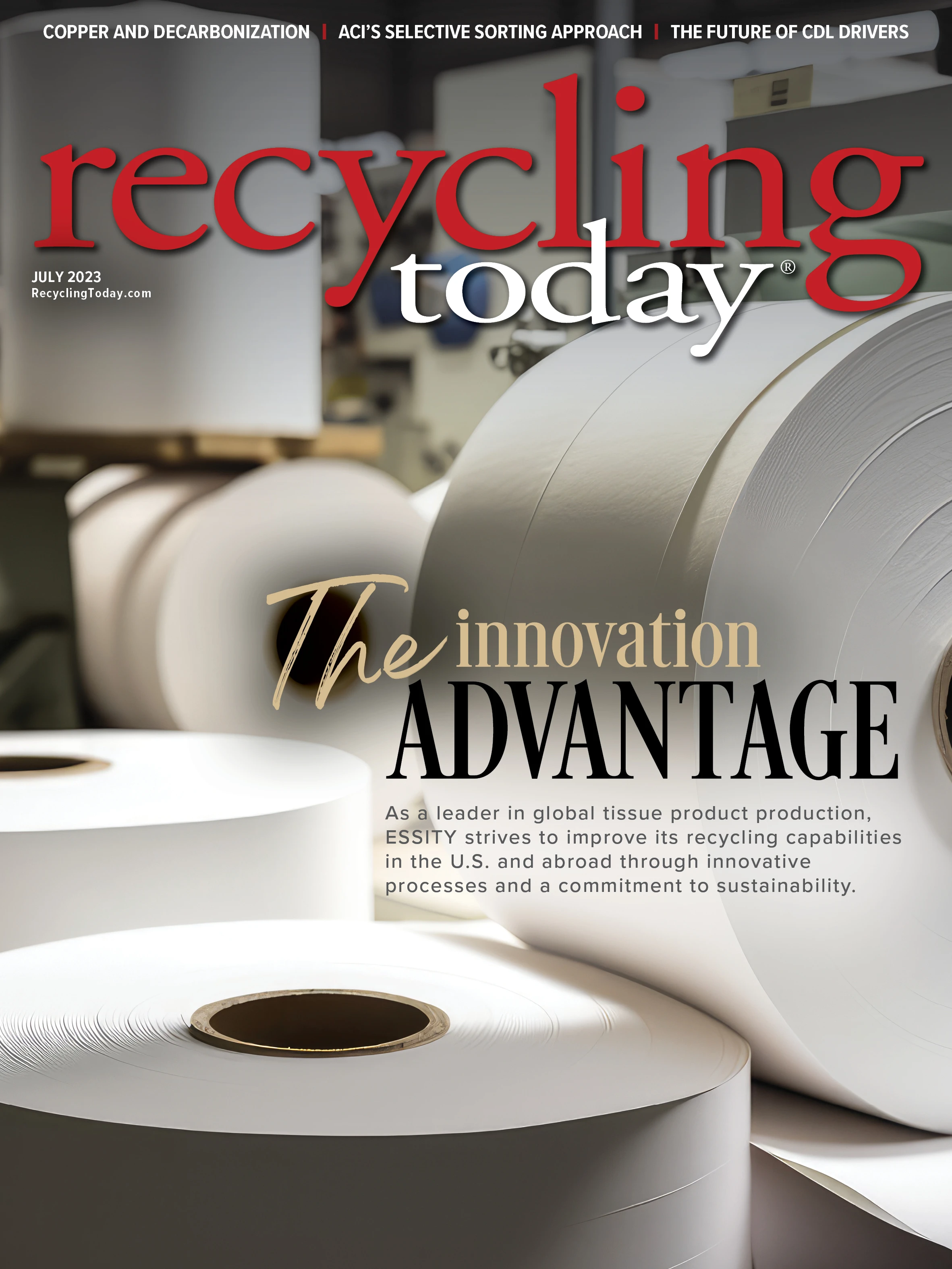
Explore the July 2023 Issue
Check out more from this issue and find your next story to read.
Latest from Recycling Today
- LumiCup offers single-use plastic alternative
- European project yields recycled-content ABS
- ICM to host colocated events in Shanghai
- Astera runs into NIMBY concerns in Colorado
- ReMA opposes European efforts seeking export restrictions for recyclables
- Fresh Perspective: Raj Bagaria
- Saica announces plans for second US site
- Update: Novelis produces first aluminum coil made fully from recycled end-of-life automotive scrap