
Nearly any scrap metal facility that handles a steady volume of loose material will find itself in the market for one or more hydraulic scrap handlers.
In the previous three decades, machines designed and custom-made for scrap recyclers have overtaken the market in an industry that had formerly used converted hydraulic excavators or, prior to that, cable cranes to move or load large volumes of material.
Manufacturers, including the German trio of Liebherr, Sennebogen and the Fuchs division of Terex, offer recyclers a choice of brands and, combined, a wider choice of model sizes and configurations from which to choose.
With choice also comes the opportunity to make the wrong decision, however, which is why recyclers may be best off starting the shopping process by asking themselves several questions before sharing those answers with potential machinery suppliers.
The known and the unknown

Scrap recyclers may not know exactly how many tons of material their new hydraulic handlers will be tasked to lift and move each day or week after they acquire them, but certain production and shipping figures usually can provide an estimate.
“Some yards know to the ton how much scrap each material handler moves in a single shift, and most operations know how much material is moved by a fleet in a single shift,” says John van Ruitenbeek, sales manager for Louisville, Kentucky-based Fuchs North America.
He continues, “Tracking volume also depends on the application.” It is more likely that a volume figure exists for “feeding a shredder as opposed to moving or stacking material from point A to point B, where it is a little more difficult to measure,” van Ruitenbeek says.
In terms of a formula that can match a machine to the task expected, he says, “I take into account the amount of reach the application requires and the weight of the material in each cycle. Then, one can estimate the cycles per hour using a 50-minute hour to calculate production.”
An estimated volume figure can help a buyer determine the lift capacity or cycle time desired from a new machine, but it is far from the only factor to consider, scrap handler suppliers say.
Andreas Ernst, strategic account and marketing manager for Stanley, North Carolina-based Sennebogen LLC, says the reach a machine needs factors greatly into which model is the best fit, and reach may have to be measured in a many ways.
Yard space and configuration can determine, for instance, exactly how a truck is loaded or unloaded. “Assume you unload a truck—it is one thing to load or unload from behind and another from the side. A machine with longer reach is not as critical when just reaching over the sidewall,” Ernst says.
Small yards also may need a machine with greater reach because their stockpiles can be higher, he says. “A small mom-and-pop yard might need a machine with [a] 45-foot reach.”
“There are several variables that can change based on the position of the machine to the pile, the height of the material pile and the experience of the operator,” van Ruitenbeek says.
For operators of auto shredders, how a shredder is fed likewise affects the amount of reach needed on a handler. “How high is the infeed and how far do you want to reach in there comes into play,” Ernst says.
The distance of stockpiled material from the shredder provides one more factor in solving the reach equation. He says, “With shredders, the discussion might be about determining how far away is the materials, and are you handling cars and, if so, how high are they piled?”
In terms of lift capacity when feeding a shredder, a question to ask, according to Ernst, is “Are you feeding the shredder with one handler or with two?”
Volume, reach and expected tasks factor in not only to the size of material handler needed but also into what platform is desired and what type of attachment or attachments make the most sense.
Suitable in all conditions
Makers of scrap handling attachments have provided even more choices to scrap yard operators; therefore, even more decisions must be made.
A larger grapple often may seem like the higher productivity choice, but Ernst says there are task-related considerations. “Choosing a grapple has to do with reach and how quickly do you want to unload,” he says. “A 2-yard grapple is the maximum to reach into a gondola car or truck.” But, he adds, “A smaller grapple can make it easier to reach in there.”
Van Ruitenbeek says during his career he has observed great differences in attachment preferences among yard managers and machine operators. “Different regions in North America as well as different countries around the world all seem to do it a little differently,” he says of the use of magnets and grapples to move ferrous scrap.
His approach, he says, is to “look at what the customer is using now and ask the operator what he likes and dislikes about the current operation.”
Van Ruitenbeek says he commonly finds that “most yard owners know what they want and why they want it” when it comes to purchasing attachments for their scrap handlers.

In terms of platform, Ernst estimates, “The market today is for sure rubber tired foremost. These machines can make it through most severe applications. I think the ratio today really is almost 98 percent rubber tired.
“In parts of the South, where it’s sandy, you could run into terrain where tires struggle a little bit,” he adds.
When an operation gets large enough, it is unlikely to settle on a uniform fleet of model sizes because of the variety of tasks required and the numerous types of material encountered at large-volume scrap processing facilities.
Ernst says, “The larger the yard, the bigger variety of machines you need. A big shredder yard may still have some smaller machines dedicated to unloading trucks. Plus, they can do some sorting—for tasks that you don’t need big machines [for] but need something small and quick.”
He continues, “Feeding the shredder is the opposite; you need to continuously swing that machine to feed the shredder.
“Thus, big yards have a mix of model sizes,” Ernst says. “Some are multiuse, while others are dedicated to feeding a shear or a shredder or loading barges.”
Both material handler suppliers say their customers most often have done their homework before getting serious about purchasing a machine, though Ernst remarks, “I think customers still can be surprised about our recommendations, especially with electric machines,” which Sennebogen might recommend for stationary applications.
In all cases, finding a machine that performs safely, effectively and reliably is the goal. “The name of the game today is safety and uptime,” Ernst says. A machine that is the right match is a critical first step in meeting those goals.
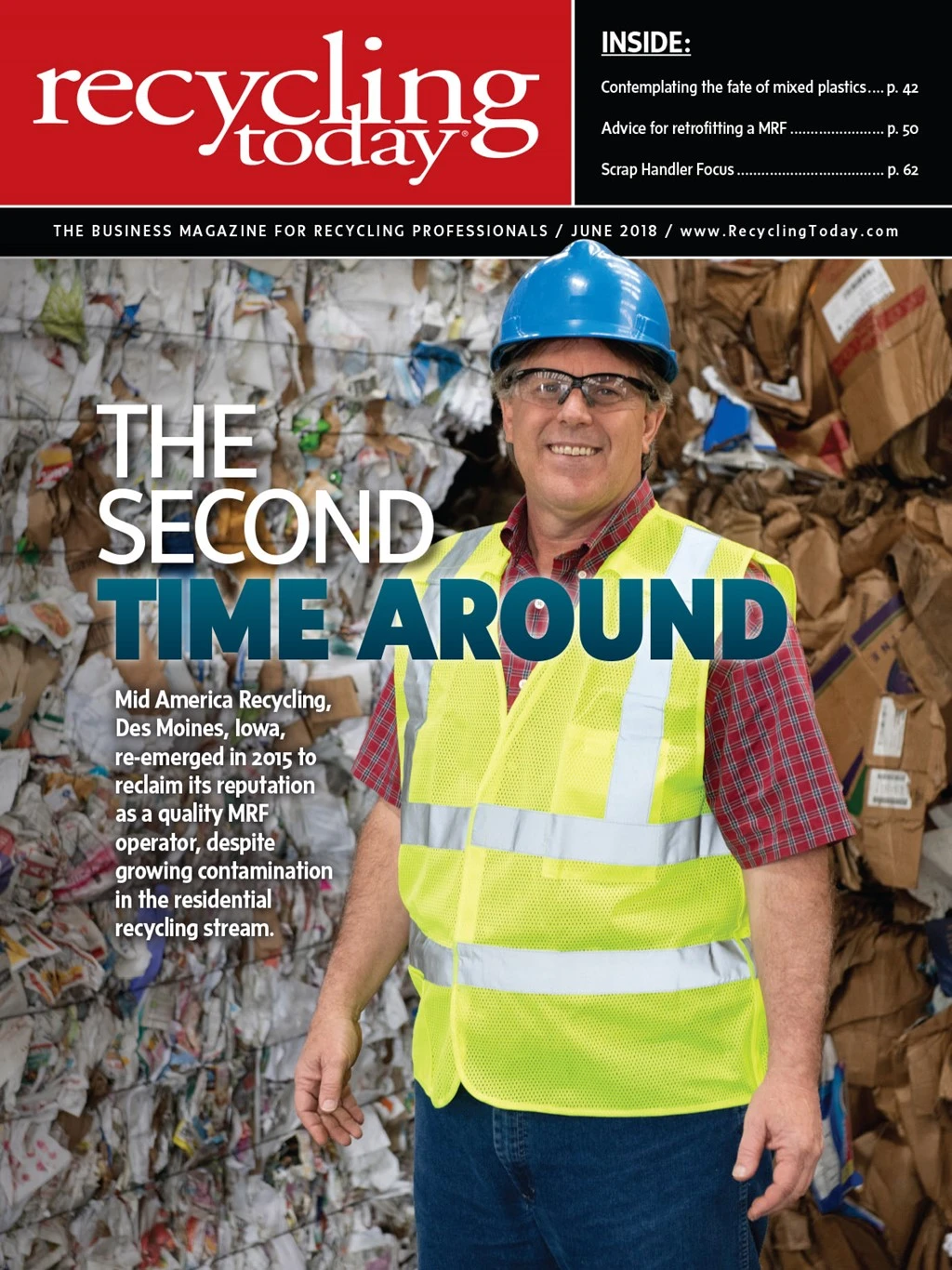
Explore the June 2018 Issue
Check out more from this issue and find your next story to read.
Latest from Recycling Today
- Nucor receives West Virginia funding assist
- Ferrous market ends 2024 in familiar rut
- Aqua Metals secures $1.5M loan, reports operational strides
- AF&PA urges veto of NY bill
- Aluminum Association includes recycling among 2025 policy priorities
- AISI applauds waterways spending bill
- Lux Research questions hydrogen’s transportation role
- Sonoco selling thermoformed, flexible packaging business to Toppan for $1.8B