The 1994 implementation of the North American Free Trade Agreement (NAFTA) removed most barriers to trade and investment between the United States, Canada and Mexico. Many tariffs were eliminated immediately, with others being phased out over time. This has allowed trade to greatly increase between the United States and its two neighboring countries.
Today more than $500 billion in goods annually move between the United States and Canada. Thirteen million truck crossings move two-thirds of these goods. That equates to 35,000 truck crossings a day, or one every three seconds. Additionally, more than $230 billion in goods move between the United States and Mexico via 4.5 million truck crossings.
Yet the benefits achieved by NAFTA may be in jeopardy over disagreements on how freight moves between the three countries, specifically, how the freight is to be safely secured during transport.
AT THE DRAFTING TABLE. In 1993 the United States and Canada began a joint research project to develop an understanding of the mechanics of securing cargo onto heavy trucks. The research would provide the basis for drafting model regulations for cargo securement to ensure safe truck transport. Tests were conducted to examine securement issues such as anchor points, tie-downs, blocking and friction. Studies were also conducted on securement issues related to heavy truck cargo, intermodal containers, metal coils, large boulders, thick metal plates and lumber.
Meanwhile, a drafting group began developing the outline for the model regulations, adding detailed performance criteria as parts of the research project were completed. The drafting group was comprised of U.S. and Canadian transportation officials. While invited, Mexican transportation officials declined to participate.
The drafting group reported to a Standards Harmonization Committee comprised of any government and industry stakeholders interested in load securement issues. The committee took reports from the drafting group and attempted to build a consensus for a North American standard. This standard would serve as a model to assist the United States and Canada in adopting similar regulations.
In May of 1999 the final version of the North American Cargo Securement Standard Model Regulations was published. The standard contained general cargo securement requirements and specific requirements on four of the five commodities included in the research study. Specific requirements were added for logs, paper rolls, concrete pipe, automobiles, light trucks and vans, roll-on/roll-off containers and flattened or crushed cars. In September of 2002 the Federal Motor Carrier Safety Administration (FMCSA) published a final rule that, with few exceptions, adopted the definitions and regulations of the model regulations. Two years later, Canadian Transportation Ministers also adopted the model regulations, with even fewer exceptions. Canadian officials had decided to await the completion of the U.S. rulemaking process to ensure that carriers in both countries would be faced with the same containment regulations.
Yet the harmony did not last long. The FMCSA is currently involved in a rulemaking that would reverse their adoption of what was considered one of the most important safety requirements of the model regulations. In its written comments on this rulemaking, the Canadian Council of Motor Transport Administrators (CCMTA) expressed disappointment that some of the directions proposed by the FMCSA "ran counter to critical and fundamental points of consensus which had been built over the previous 10 years through the research and standard development phases." What are the critical points of difference that could jeopardize regulatory uniformity between the United States and Canada? Also, how might this controversy effect the securement regulations for flattened and crushed cars?
MODEL REGULATION. Cargo accelerates at the same speed as the truck on which it is loaded. When the driver applies the brakes, the truck decelerates, yet the truck’s brakes have no effect on the cargo within the vehicle, which continues to move forward. Friction between the cargo and the truck’s deck can slow down the movement of the cargo. Yet numerous potential factors, such as oil, ice and dirt, can negate the level of friction. Therefore, most cargo must have restraints against movement. When the cargo is properly loaded on a van, the walls of the vehicle can provide much of the restraint. Yet additional restraints are needed when the cargo is carried on a truck with no walls, such as a flatbed.
The cargo securement research studied the potential forces that could act on cargo carried on a flatbed-like vehicle. These forces were expressed as a proportion of the acceleration on an object in light of gravity.
The Standards Harmonization Committee agreed that any component of a cargo securement system should always be able to withstand the greatest possible force of deceleration or acceleration, short of an accident, without sustaining permanent damage. Therefore the model regulation required that the working load limit (WLL) of any component of a cargo securement system must always withstand the following forces:
• 0.8 g forward deceleration;
• 0.5 g backward deceleration; and
• 0.5 g lateral acceleration.
A simple example to explain this requirement involves securing a 1,000 pound load to a flatbed trailer using chains. The chains and anchor points securing the load from moving forward must each have a WLL of at least 800 pounds, while those preventing the load from moving to the rear or to either side must have a WLL of at least 500 pounds.
The WLL, which is determined by the manufacturer, is the maximum load that may be applied to a component of a cargo securement system during normal service. The WLL is a percentage of the Minimum Breaking Strength (MBS), which is the minimum load that would cause a new tie-down to break. The range of WLL for most metal tie-down components is 20 percent-30 percent of the MBS. Manufacturers of these components warn users to never exceed the WLL.
Sponsored Content
Redefining Wire Processing Standards
In nonferrous wire and cable processing, SWEED balances proven performance with ongoing innovation. From standard systems to tailored solutions, we focus on efficient recovery and practical design. By continually refining our equipment and introducing new technology, we quietly shape the industry—one advancement at a time.
Normal use and exposure to the elements can gradually weaken the strength of a tie-down. Exceeding the WLL will add to this weakening, and repeated stress beyond the WLL will increase the potential that the tie-down will break under pressure. This could cause uncontrolled movement of the cargo that could result in the driver losing control of the vehicle. When dealing with cargo transported on a flatbed using the WLL of tie-downs is the most reliable way to determine if the cargo is safely secured. Requiring that, short of an accident, the WLL of the tie-down would rarely be exceeded would greatly decrease the potential of unseen weakening of the tie-down.
While all the parties involved seek clarification, at least one comment recived by the FCSMA reminds those involved what is at stake.
A comment received after publication of the 2002 final rule came from Charles B. Hall of Leesburg, Ga. He wrote "My niece and her friend were killed on June 5, 2003, by freight that fell from the side of a transfer truck. The freight weighed several thousand pounds. It’s time to stop negotiating about standards and do something substantial about this issue–more people will die without constructive action. I don’t want to hear about the cost of compliance to transportation companies; we are talking about people’s lives. My niece and her friend were only 22 years of age. She graduated from college three weeks ago and was engaged to be married."
The author owns HSR (Health, Safety and Risk) Consulting and advises on safety and risk management issues. He can be contacted at mikemattia@hsrconsulting.org or at (303) 318-6974.
IN OUR MARCH ISSUE: Part II of "Securement Complex" looks at continued wrangling over clarification of cargo securement standards and flattened-car transportation specifics.
Get curated news on YOUR industry.
Enter your email to receive our newsletters.
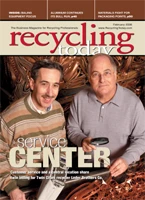
Explore the February 2006 Issue
Check out more from this issue and find your next story to read.
Latest from Recycling Today
- ReMA board to consider changes to residential dual-, single-stream MRF specifications
- Trump’s ‘liberation day’ results in retaliatory tariffs
- Commentary: Waste, CPG industries must lean into data to make sustainable packaging a reality
- DPI acquires Concept Plastics Co.
- Stadler develops second Republic Services Polymer Center
- Japanese scrap can feed its EAF sector, study finds
- IRG cancels plans for Pennsylvania PRF
- WIH Resource Group celebrates 20th anniversary