
When the Plastics Industry Association (PLASTICS), Washington, brought a group of government and packaging industry leaders together for the Pacific Northwest Secondary Sorting Demonstration Project (or PNW Sort, for short), the ultimate goal was to show how secondary sorting is one of many great options that can be used to improve recycling infrastructure in the United States. The 60-day demonstration project was conducted in Portland, Oregon, and began in the summer of 2019.
The PNW Sort involved installing a portable, secondary sorting system provided by Danville, California- headquartered Titus MRF Services. The secondary material recovery facility (MRF) received, sorted and measured the recovery of recyclables from two types of material streams from four MRFs in Oregon and Washington.
For more background on the pilot project, see the article “Taking an evolutionary leap” in the Fall 2019 issue of Plastics Recycling, available at www.RecyclingToday.com/article/taking-an-evolutionary-leap.
Secondary MRFs aggregate low-volume and difficult- to-manually sort materials, along with machine yield losses, from a network of existing primary MRFs to reach the critical mass needed to justify investments in automated technologies for sorting by material type. Secondary MRFs offer a more efficient and cost-effective solution to upgrade our material recovery infrastructure than MRF retrofits can. They help move the needle in improving our recycling systems. By focusing the effort on a regional approach, they also provide a solution that can be implemented within a time scale more likely to meet marketplace demand.
“Projects like this are important as we work towards a more sustainable system nationwide,” says Scott Farling of Titus MRF Services. “While top-producing primary MRFs can recover close to 90 percent of the recycled materials from the waste stream, we’d like to see that number increase in the coming years. This project allowed us to dig deeper to recover what remains: the low-volume and difficult-to-manually sort materials along with machine yield losses.”
This study recovered polyethylene, mixed paper, gable-top cartons, polypropylene, polystyrene and polyethylene terephthalate bottles and thermoformed containers.
The concept of a secondary MRF is less about advanced sorting technologies and more about a business model that can achieve the economies of scale for sorting all materials by type within a regional wasteshed, such as Oregon and Washington in the Pacific Northwest.
Being a pilot project, PNW Sort has ended, and the results are encouraging. They provide a loose blueprint for how other municipalities can take similar strides to improve their recycling and waste management infrastructure by adding a secondary MRF.
The results are in
The PNW Sort shows that adding a regional secondary MRF sized to serve the populations of both Oregon and Washington (more than 11 million people) would:
- increase material recovery or landfill diversion by more than 50,000 tons (100 million pounds) per year, the equivalent of 2,500 semitrailer truckloads of recyclables;
- increase the recovery rate by 3 percent to 6 percent without significant program changes or investments based on a regional model where MRFs recover 88 percent of recyclables;
- generate 46 green jobs per secondary MRF;
- reduce the generation of greenhouse gases by more than 130,000 tons per year, which is equivalent to taking more than 27,600 cars off the road, according to the Environmental Protection Agency’s Greenhouse Gases Equivalencies Calculator;
- enable future expansion of the accepted materials without retrofitting primary MRFs to sort these materials; and
- provide accountability for all collected recyclables and eliminate the risk of potential mismanagement and pollution.
We think that’s a pretty good start.

A new solution
The brilliance of the PNW Sort has been the public and private sector collaboration, which was instrumental in the pilot’s execution. This collaboration gave the partners space to test new technologies to help modernize our domestic recycling systems. While PLASTICS managed the project, it included the collaboration and commitment of the American Chemistry Council, AmSty, Berry Global, the Carton Council, LyondellBasell Industries, Oregon Metro government, Milliken & Co. and Titus MRF Services.
So instead of sorting once, why not do it twice? PNW Sort shows just how important the latter can be.
“Our biggest takeaway following this pilot program is that a secondary sorting facility model is a viable option to help meet the ever-increasing demand for recycled materials,” says Tony Radoszewski, president and CEO of PLASTICS. “The project data shows the value that can be extracted from landfill-bound or mixed materials. It is our hope that the data from this report can help inform state and local decision-makers on how to improve our recovery systems.”
Expanding this approach
PLASTICS stands firmly behind this project and its replicability in other areas and other waste management systems outside of the Pacific Northwest. The recently introduced Realizing the Economic Opportunities and Value of Expanding Recycling (RECOVER) Act is a bipartisan, federal bill that would make it easier to expand this approach—and the results it clearly delivers—to more towns, cities and states across the United States.
If you haven’t yet, we hope you’ll visit our newly redesigned This Is Plastics website, www.thisisplastics.com, and take action for plastics recycling by voicing your support of the RECOVER Act.
We encourage people to use the findings from the PNW Sort to further those conversations and in updating our recycling systems one region at a time.
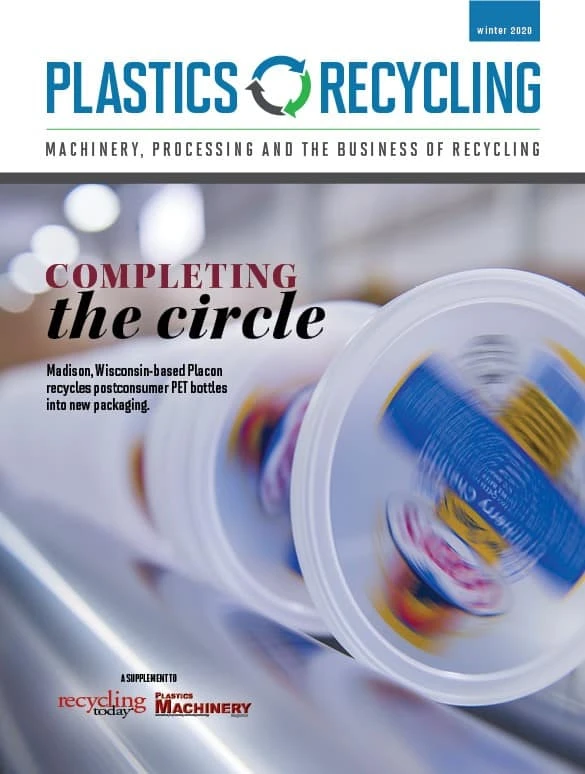
Explore the Winter 2020 Plastics Recycling Issue
Check out more from this issue and find your next story to read.
Latest from Recycling Today
- Aqua Metals secures $1.5M loan, reports operational strides
- AF&PA urges veto of NY bill
- Aluminum Association includes recycling among 2025 policy priorities
- AISI applauds waterways spending bill
- Lux Research questions hydrogen’s transportation role
- Sonoco selling thermoformed, flexible packaging business to Toppan for $1.8B
- ReMA offers Superfund informational reports
- Hyster-Yale commits to US production