
© Liudmila / stock.adobe.com

Sealed Air Corp. has seen demand for its packaging solutions grow, fueled in part by the rise in e-commerce during the pandemic. Its 2020 net sales increased by 2 percent to $4.9 billion, while its 2020 net earnings of $484 million increased by 64 percent year over year. The company has continued to see gains in 2021 and increased its full-year sales outlook to a range of $5.4 billion to $5.5 billion as of the end of its second quarter.
In addition to growing its sales, Sealed Air is looking to grow its sustainability credentials. Ron Cotterman, vice president of innovation and sustainability for the Charlotte, North Carolina-based company that provides packaging technology, solutions and systems, says Sealed Air has been investing to produce environmentally friendlier packaging.
The company has been considering the size of its packaging formats as well as being mindful that, when it comes to e-commerce, products often are shipped in their original packaging without overwrap, which requires Sealed Air to ensure that its industrial customers are using the right internal packaging for their primary packaging. Cotterman says Sealed Air also is working to ensure the materials it uses are more sustainable.
A multifold strategy
Sealed Air has pledged that its packaging solutions will be 100 percent recyclable or reusable by 2025 and will contain 50 percent recycled content on average, 60 percent of which is postconsumer recycled content. Cotterman says Sealed Air is not tied to a specific material format. Instead, he says, “We try to use the right material for the right application.”
While the company is transitioning to paper-based solutions where it can, it is in business to protect products and people, which sometimes requires the properties that plastic packaging provides. “So, our strategy there is multifold,” he says.
“One is we’re trying to design those plastic solutions so that they can be recycled. The second thing we’re trying to do is to incorporate recycled content in that plastic, and that’s really to help drive the demand side. The third thing that is quite unique to Sealed Air, I find, is that it’s not good enough to make your materials recyclable and to use recycled content; there has to be a way for the customer to participate in that process. And that’s where there’s a lot of discussions and negotiations and trials and things underway right now. We’re very active in that space.”
Sealed Air also has committed to becoming net zero in terms of greenhouse gas emissions by 2040, Cotterman says. “We are watching the carbon footprint of everything we do, whether it’s our manufacturing facilities or our products, to drive greenhouse gas emissions out of the value chain.”
He says Sealed Air’s plastic mailers can offer an advantage over boxes in this area, citing a 2004 study by the Oregon Department of Environmental Quality that compared plastic mailers, paper envelopes and traditional boxes. The study found that plastic shipping bags were responsible for less than half the greenhouse gas emissions attributable to a paper envelope and one-fourteenth the emissions of a cardboard box.
“So, we do think we’re on the right track, both with design for recyclability and use of recycled content, but we also think these kinds of solutions are going to be very strong in terms of helping reduce the overall greenhouse gas emissions of the whole supply chain,” Cotterman says.
Embracing chemical recycling

When it comes to increasing the circularity of its plastic packaging, Cotterman says various areas must be addressed from an infrastructure standpoint, including collecting, sorting and ensuring that recovered material can go back into the same application rather than being downcycled to make a different product.
He says Sealed Air has embraced the role that advanced or chemical recycling can play in increasing the circularity of its plastic packaging by investing in London-based Plastic Energy. That company uses its patented thermal anaerobic conversion (TAC) technology to convert end-of-life plastics of different types into recycled-content oil that can be used to create packaging solutions. “We wanted to demonstrate that we could create a whole circular loop,” Cotterman says.
To do so, the company worked with U.K.-based retailer Tesco, which invited its customers to bring back flexible plastic packaging to its stores for recycling. Tesco then baled the collected plastic packaging and transported the bales to Plastic Energy, where they were converted into TACOIL. Saudi Arabia-based multinational plastic and chemical company SABIC, or Saudi Basic Industries Corp., took the TACOIL feedstock from Plastic Energy and produced a plastic pellet that it supplied to Sealed Air. The company used the pellet to produce packaging for cheese made by a U.K. company for distribution at Tesco.
“People didn’t think it was possible. And we proved that it was,” he says. “It really gives us confidence that we can do that sort of thing. And we have to do that in a very significant way. So, that’s where Closed Loop comes in,” Cotterman says, referencing New York City-based Closed Loop Partners.
In August, Sealed Air invested $5 million in the Closed Loop Circular Plastics Fund to advance the recovery and recycling of plastics in the United States and Canada.
Partners in change
The Closed Loop Circular Plastics Fund, which was established by Dow, LyondellBasell and Nova Chemicals and is managed by Closed Loop Partners, will invest in scalable recycling technologies, equipment upgrades and infrastructure solutions. The fund is seeking additional investments, with the goal of growing to $100 million. It will invest in three strategic areas to increase the amount of recycled plastic available to meet the growing demand for recycled content in products and packaging: access, optimization and manufacturing.
The fund’s investments seek to increase the collection of polyethylene and polypropylene by advancing material collection systems, including transportation, logistics and sorting technologies. The fund seeks to upgrade recycling systems in the U.S. and Canada to more efficiently aggregate, classify and sort the targeted plastics to increase the total amount of material sent for remanufacturing. The fund will invest in facilities and equipment that manufacture finished products, packaging or related goods using recycled content.
Cotterman says Sealed Air invested in the Closed Loop Circular Plastics Fund with the goal of helping catalyze investments in the advanced recycling sector. “We don’t have a lot of time,” Cotterman says of meeting Sealed Air’s 2025 goals. “We’ve got to move fast to build out this infrastructure. But we think it’s the right thing to do to really enable that circular economy.”
Because much of Sealed Air’s packaging remains in the business-to-business sector, he says the company also is working to collect that packaging to create “circular material loops” that are similar to what Sealed Air did with Tesco but on a business-to-business scale. “And once we’ve proven the viability of that and built out the infrastructure, we want to leverage that to show that this can be expanded to even postconsumer-type materials. And that’s where we’re starting. We’re not necessarily trying to take the hardest problem first,” he says, referencing postconsumer material.
As a company that not only provides the packaging materials but also the equipment and technology that allow its customers to efficiently use those materials, Cotterman says, “We’re trying to sell you material that you can use efficiently and to make that whole value chain as sustainable as possible.”
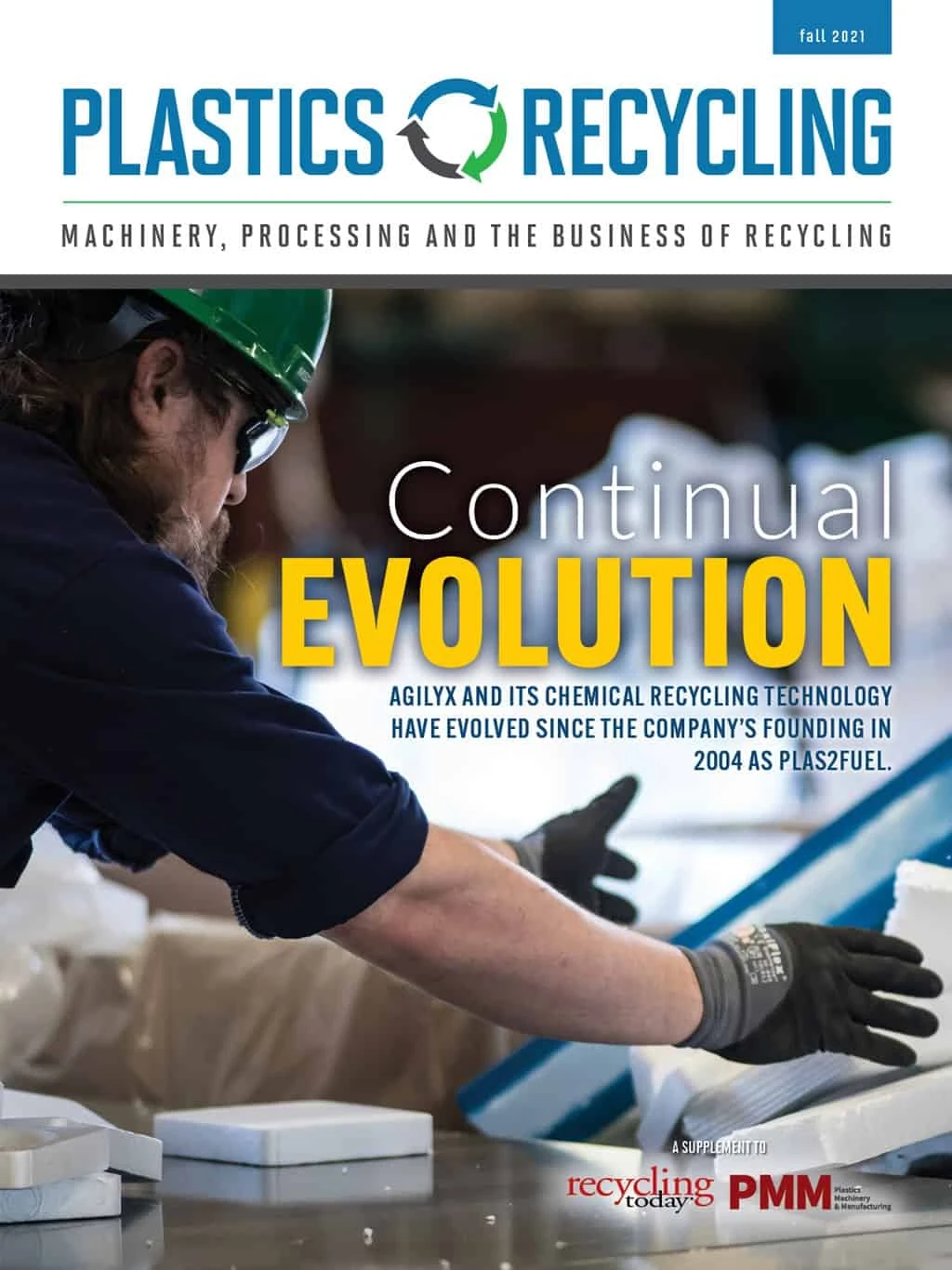
Explore the Fall 2021 Plastics Recycling Issue
Check out more from this issue and find your next story to read.
Latest from Recycling Today
- MTM Critical Metals secures supply agreement with Dynamic Lifecycle Innovations
- McClung-Logan Equipment Company joins Tana’s authorized dealer network
- Grede to close Alabama foundry
- Plastics Recycling Conference 2025: Working toward their targets
- SWACO rolls out new commercial recycling and food waste programming
- Updated: Matalco to close Canton, Ohio, plant
- Metso launches electric Anode Weighing and Casting Machine
- Circular by Shapiro releases '5 for Five' sustainability series