
When SDI La Farga formed in 2011, its parent companies, Steel Dynamics Inc. (SDI), Fort Wayne, Indiana, and La
New Haven, Indiana-based SDI La Farga offers an alternate home for some of the lower grades of copper scrap that are generated within the United States.
While the companies might not have foreseen the developments that were to come, OmniSource, the scrap processing division of SDI, was interested in reducing its dependence on China for the sale of much of its copper scrap.
“When this partnership was conceived, Omni was dependent on selling much of their copper scrap to China,” says Kurt Breischaft, SDI La Farga president. “Omni desired a more consistent consumer of copper scrap, preferably in the U.S. Midwest.”
OmniSource had been supplying scrap to La Farga’s furnace outside of Barcelona, Spain. La Farga manufactures and sells semifinished copper products and their alloys to the electrical, metal packaging, railway, tubes, automotive, billets and special conductors markets.
“The location in New Haven, just east of Fort Wayne, is strategic both on the supply side as well as the demand side,” Breischaft says. “Copper scrap from the Midwest flows cost-effectively to New Haven rather than Asia. Copper rod competitors are primarily in the Southwest and Northeast U.S., but there’s a strong wire and cable presence in the Midwest.”
Better together
La
He continues, “Steel Dynamics has an extremely successful track record and culture. Getting the best technology and putting the right people in place with the right incentives to do better-than-rated performance are key pillars.” Breischaft says La
“People have been fire refining for thousands of years, and La Farga has been refining copper for over 200 years,” he says. “In the 1980s, there was a significant leap forward in the technology through developments at La Farga. This allowed fire refined high conductivity (FRHC) copper to be used in wire rod and compete with electrolytic tough pitch (ETP) rod. Today, both La Farga and SDI La Farga in North America use this technology.”
The flexible technology allows SDI La Farga to run a wide variety of copper scrap in high volumes. This, in turn, allows Michael Vose, purchasing manager at SDI La Farga, to buy scrap that offers the best economy for the company. That fits well at SDI, which provides an incentive-based culture that prioritizes production efficiencies.
Breischaft says because SDI La Farga uses a batch process, when the team finds a tweak that saves it five or 10 minutes per batch, its productivity goes up. “We continue to have meaningful year-over-year growth as our production team finds process improvements,” he says. “We run a melting-refining-casting process that is iterative, so any improvement in cycle times yields additional output. The Steel Dynamics culture with a highly incentivized workforce aligns every single person in the shop to find ways to make more quality product.”
Breischaft continues, “Part of what we get from SDI is being very incentive driven.”
The time savings and productivity increases translate into higher pay for the SDI La Farga team members.
The company’s employees are “team and
“The supervisors and engineers on the floor get to do a lot of the hiring,” he says of the SDI La Farga employees.
Company turnover tends to be low, Vose says, adding that most job openings at the company arise because of growth.
Growing pains
SDI La Farga processed less than 10 million pounds of copper scrap in 2012. In 2017, the company consumed 150 million pounds. “For 2018, we see increases that will get us to 180 million pounds,” Breischaft says. “As the scrap volume requirements have grown, so has our supplier base,” he adds.
In growing that supplier base, SDI La Farga had some challenges to overcome.
Vose says, “One challenge was changing sellers’ minds on supplying an unproven domestic home versus Chinese or European refineries that had a consumption history. Those concerns are resolved now, with mutual trust established on both sides of the supplier/consumer relationship.”
Startup also took a little longer than SDI La Farga would have liked, Breischaft says. “In North America, the grades of birch and cliff, which have been what our target feed has been, have nuances that are different than birch and cliff in Europe.”
“When this partnership was conceived, Omni was dependent on selling much of their copper scrap to China.” – Kurt Breischaft, president of SDI La Farga
He says these differences are related to the silver and nickel content in the scrap.
“Quality does vary from one dealer to the next and sometimes dictates who we purchase specified materials from,” Vose says. “A big change in the early days was to adjust to the culture of dealers’ loose adherence to ISRI’s (Institute of Scrap Recycling Industries’) birch/cliff specifications. Birch/cliff had become the ‘catch all’ for copper scrap not meeting other defined scrap specifications. The quality of the package has improved considerably into SDI La Farga in the last two years.”
SDI La Farga has performed five or six relines since it started up in 2011, with the most recent reline having seen the longest life. However, Breischaft says that the number of relines is a bit misleading.
“When they first started up, they put in cheaper brick because they knew they were going to be learning
Vose says SDI La Farga has exited the market for the month of February 2018 and the first week of March because of the scheduled downtime. However, he adds there might be spot buying opportunities during that time. “We will start buying soon for April delivery,” he says.
Scrap buying
Vose says to produce the 180 million pounds of wire rod SDI La Farga expects to in 2018, it will consume 190 million pounds of copper scrap.
“Ninety-one percent of the furnace feedstock originates from U.S. scrap dealers,” he says. “The last 9 percent comes from toll processing of scrap materials generated by our sales homes.”
While SDI owns scrap supplier Omni- Source, Vose says SDI La Farga “is not compelled to buy from them, and they are not compelled to sell to us.” Yet, he adds that OmniSource is one of the company’s largest suppliers, providing 7 percent of its infeed material in a typical month.
SDI La Farga purchased scrap from 137 scrap dealers in 2017, he adds. “Competitive pressures from other scrap consumers (including overseas refiners) mean we must have a wide base of suppliers. Also, if the copper market sours and flows into dealer yards slow down, it is good to have relationships with many suppliers.”
Vose and Breischaft say that 2018 is “a year of change” related to scrap supply because of actions out of China.
“China consumes roughly 50 percent of global copper, so the world largely follows its cue,” Vose says. “This year, a high volume of copper and copper-bearing scrap will no longer be permissible for import due to what are identified as contaminants. As a result, an opportunity exists for scrap dealers to evolve and improve their operations. One such change is the installation of insulated copper chopping lines. Today’s units are much improved over the technology of five years ago, obtaining better separation of acceptable and unacceptable materials using equipment with a smaller footprint. In-house grinding of insulated copper wire could open more global doors for scrap dealers.”
Vose adds, “Quality will largely dictate where the chopped packages can be marketed. SDI La
Growing market share
Almost all of SDI La Farga’s production is copper wire rod, which is used by copper cable manufacturers. “Additionally, some of the rod is drawn into wire at SDI La Farga, either as a service for wire producers or to support customers who make steel cans,” Breischaft says. “Interestingly, most steel cans for food and aerosol use are welded with copper wire. No copper becomes part of the can, it is only an electrode. The copper becomes contaminated with tin from the can and is returned to SDI La Farga. It’s a closed loop system with no inherent loss of material properties.”
SDI La
He adds, “We believe the North American wire rod market is about 3.7 billion pounds annually, and our share is approaching 5 percent.”
Vose says, “On the scrap side, SDI La
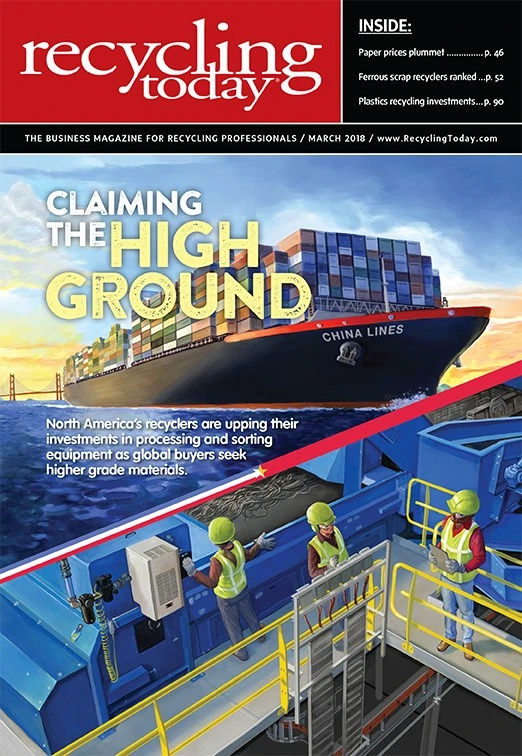
Explore the March 2018 Issue
Check out more from this issue and find your next story to read.
Latest from Recycling Today
- PCA reports profitable Q1
- British Steel mill subject of UK government intervention
- NRC seeks speakers for October event
- LME identifies Hong Kong warehouses
- Greenville, Mississippi, launches aluminum can recycling program
- Cotton Lives On kicks off 2025 recycling activities
- Georgia-Pacific names president of corrugated business
- Sev.en Global Investments completes acquisitions of Celsa Steel UK, Celsa Nordic