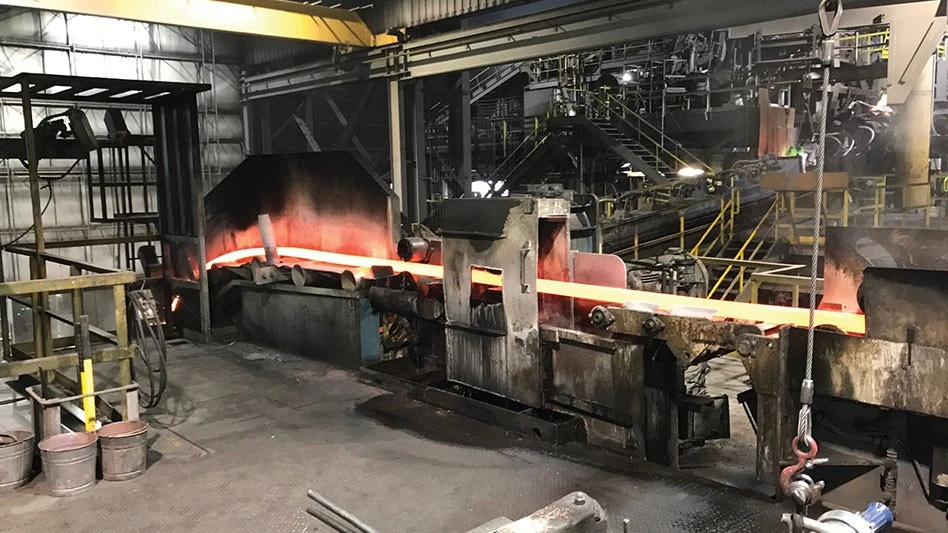
Photo courtesy of SDI LaFarga Copperworks

In late 2019, copper wire and rod producer SDI LaFarga Copperworks announced plans to invest $16 million to expand its New Haven, Indiana, plant. The company, a joint venture between Steel Dynamics Inc. (SDI), Fort Wayne, Indiana, and Barcelona, Spain-based La Farga Group, was established in 2011 and opened its New Haven plant in mid-2012, which features a 250-metric-ton scrap-fed furnace. That furnace, which uses a batch process, was joined by a second furnace in late 2020 that allows continuous melting of copper cathode and bare bright copper scrap to produce rod and wire.
The addition of the shaft furnace took SDI LaFarga Copperworks’ finished copper production from 180 million pounds annually to 430 million pounds and allowed the company to operate more efficiently, SDI LaFarga Copperworks President Kurt Breischaft says.
Added efficiency

The company’s scrap-fed refining furnace operates continuously but produces output in batches or heats. “It takes about 24 hours to make a heat—that’s divided into melting, refining and casting—and when we are melting and refining, the caster part of the plant is idle,” Breischaft explains.
“By design, even when that refining furnace was running, the caster and the rolling mill were only running about a third of the time” prior to installing the shaft furnace, he says. “So, adding a second furnace that continuously melts lets us fill in the other two-thirds of the time.”
The new furnace melts primarily cathode rather than scrap, making SDI LaFarga’s product mix a little wider than it was previously and than its competitors’ product mix.
Its fire-refined, high-conductivity copper rod and wire, sold under the Infinity trademark, is made from scrap using its original furnace, while its electrolytic tough pitch copper rod, sold under the Elemental trademark, is made using primarily cathode and the new furnace. Infinity copper rod is used to make power cables, building wiring and many other electrical wire products, while Elemental copper widely is used in electrical applications. SDI LaFarga Copperworks also produces drawn wire and can wire.
As of mid-September, SDI LaFarga Copperworks was making nearly 15 million pounds each month of Infinity products and about 21 million pounds per month of Elemental products, though Breischaft says he expects the Elemental number to grow somewhat as the company continues to perfect that process. Conceptually, the company should be producing 33 percent Infinity products and 66 percent Elemental products. “We’ve got to maximize everything to get there,” he says. “So that’s what we’re working to do.”

A distinct identity
Breischaft says it was important for the cathode-produced products to be distinct from the scrap-produced products. “We didn’t want one product to eclipse the other one,” he says. This led to the development of the Infinity and Elemental trademarks as well as to the rebranding of the company from SDI La Farga to SDI LaFarga Copperworks.
“We surveyed suppliers, customers, employees, and that’s where the Copperworks brand came from,” he says. “LaFarga is a strong brand in copper in Europe. And Steel Dynamics is a strong brand in steel in North America. We needed an equally strong brand for the American copper space.”
While Breischaft says SDI LaFarga Copperworks is “proud of both of our parents,” he adds, “we’re also proud of the culture and the folks that we’ve got on our team here.”
Still focused on sustainability
Despite the growing role that copper cathode is playing in the company’s production, SDI LaFarga Copperworks says sustainability remains a focus. It’s an ethos that has been handed down by both its parent companies.
“Both our parent companies of La Farga in Spain and Steel Dynamics in America are very interested in the recycling space,” Breischaft says.
However, being able to use scrap as well as cathode gives SDI LaFarga Copperworks “more options than if we were just doing one or just doing the other,” he says. But cutting its teeth on scrap-based production has helped to make the company what it is.
“Doing the scrap is a lot harder than not doing the scrap,” Breischaft says. “If we had done it the other way around, we would have really struggled to figure out the scrap stuff. We figured out all the scrap stuff and all the refining because we had no choice—figure this out or your company goes away. And, so, we figured it out.”
SDI LaFarga Copperworks offers a domestic home for some lower grades of copper scrap that are generated within the U.S., such as birch and cliff, but the company also consumes No. 1 copper.
“One of the big things that made us successful … was adjusting our processes to be able to run whatever scrap is available rather than have a specific recipe,” Breischaft says. “Being flexible put the power back into our buyers’ hands. Certainly, we know the different processing costs for the different things, but we’ve got the operations structure to be flexible and be trying to move back and forth as the market conditions change.”
In addition to its use of scrap, SDI LaFarga Copperworks says it constantly works to reduce its environmental impact and manufacture its products sustainably. The company has recycled more than 1 billion pounds of copper scrap since it began operating in 2012, reducing its CO2 generation by more than 1.8 billion pounds. SDI LaFarga Copperworks also recycles the slag pulled off the melted copper in its refining furnace, the copper dust emitted during the production process and the water used in its rolling mill.

Culture of commitment
In addition to its flexibility in terms of production, Breischaft says SDI LaFarga Copperworks’ culture is a distinct advantage for the company. It is borrowed from SDI’s culture. “It’s very incentive-based, or team-based, and very driven,” he adds.
Since the installation of the shaft furnace, he says, “It’s been sales versus production” as far as which team can get to the highest number first. “We want to sell as much of it as we can. We want to produce as much as we can. And that’s what we’ve been doing.”
Demand for its products increased following the late August announcement by ASARCO that it was indefinitely shutting down operations in Amarillo, Texas, because of challenging economics and production interruptions related to maintenance and manpower issues and the September strike at Nexans Montreal plant.
As of mid-September, Breischaft says the company was selling October production. “And our spot sales, we have about 21 million pounds of demand chasing about 7 million pounds of our capacity,” he says.
“We’re trying to keep turning the knob up to get more out” of its operations, Breischaft adds. “We’ve got a great team that’s working on that and has made substantial progress, especially in the last couple of weeks. So, it’s exciting times for us.”
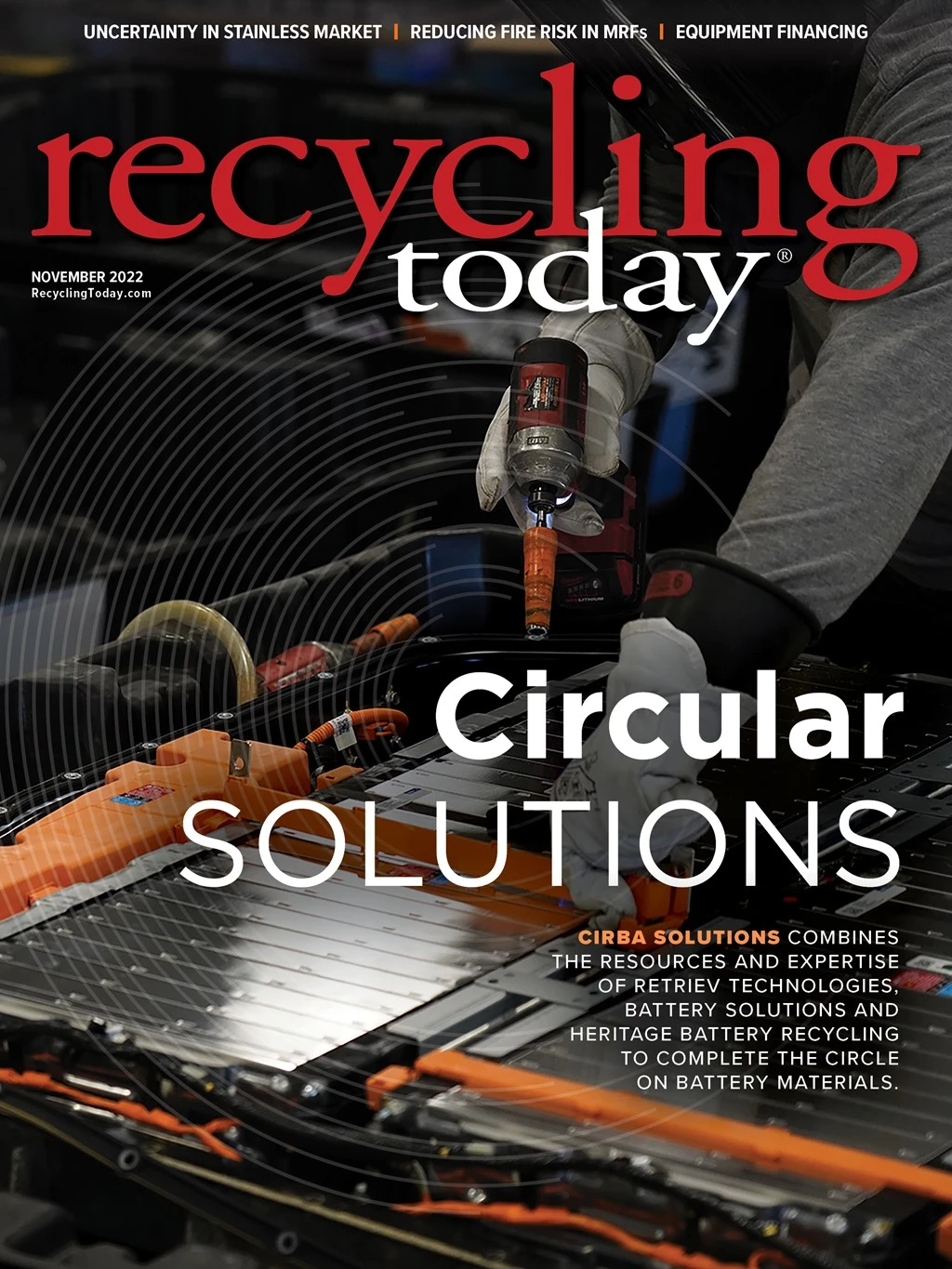
Explore the November 2022 Issue
Check out more from this issue and find your next story to read.
Latest from Recycling Today
- European project yields recycled-content ABS
- ICM to host co-located events in Shanghai
- Astera runs into NIMBY concerns in Colorado
- ReMA opposes European efforts seeking export restrictions for recyclables
- Fresh Perspective: Raj Bagaria
- Saica announces plans for second US site
- Update: Novelis produces first aluminum coil made fully from recycled end-of-life automotive scrap
- Aimplas doubles online course offerings