2012 Global Forecast The opening session of the 2011 Paper Recycling Conference – Europe provided an overview of the world economy as well as the implications for the paper and board industry in the near term. Clive Suckling of U.K.-based PricewaterhouseCoopers (PWC) LLC said that following a strong recovery from the global recession, GDP once again was trending downward, especially for the advanced economies of the world. “The actions of the political leaders will determine how long we stay in an economic trough.” While PWC had originally predicted an uptick in GDP for the advanced economies in 2012, the company revised its projections to flat once the IMF (International Monetary Fund) released updated figures, Suckling said. In contrast, the BRIC (Brazil, Russia, India, China) countries’ economies were forecast to provide 40 percent of the global GDP growth seen in 2011 to 2012, he noted. The debt crisis continued to plague the economies of advanced countries, fueled by problems with sovereign debt in the eurozone periphery, medium-term debt burdens in the major advanced economies and challenges in achieving political consensus on fiscal consolidation, Suckling said. Key threats as a result of the eurozone crisis include a credit squeeze in light of bank recapitalization, lack of competitiveness in some periphery countries and dampened business and consumer sentiment, he said. The picture is similar in the United States, where low consumer sentiment is combined with aggressive fiscal consolidation and the impact of long-term unemployment. The BRIC countries face different threats, which include inflationary pressures, particularly in China, monetary tightening, reliance on export-led growth and government red tape, Suckling said. David Powlson of Poyry Management Consulting, London, said demand for paper and board was expected to increase by 1.6 percent per year globally, though the dynamics affecting this growth are regional. China and other emerging economies should see 3.2 percent growth per year. A decline in graphic packaging demand is expected through 2025, Powlson said, while tissue and packaging board consumption are expected to grow during that same time. Demand for recovered fiber has increased, as has demand for virgin fiber, he said. However, recovered fiber growth is outpacing virgin growth at 4.7 percent per year versus 0.3 percent per year. Powlson said he saw no reason for this trend to reverse in the near future. Recovered fiber demand has led to market imbalances and supply chain pressure, he said. China continues to drive recovered paper demand, importing 24 million metric tons of the material annually. Recovered fiber demand also has led to increasingly volatile prices for the material, which are forecast to continue, according to Poyry. “The market dynamics and environment are changing,” Powlson said. “Businesses will need to adapt their business models to survive and ever tightening supply-demand imbalance.” The Paper Recycling Conference – Europe was Nov. 8-9 at the Barcelo Sants Hotel in Barcelona. – DeAnne Toto |
Throughout the last 20 years, what passes for sorted office paper (SOP) has changed, and these changes present significant challenges for recovered fiber processors and paper mills. In light of changes in generation patterns, SOP has evolved from mostly white paper with long fibers to material that includes a mixture of paper types and higher sticky-label content. As a result, processors face higher labor rates, and paper mills face production slowdowns and higher levels of fiber loss.
Deteriorating Quality, Volume
Rick Ramsay of Atlantic Coast Fibers of Passaic, N.J., has seen the evolution firsthand. As someone who has collected and processed SOP for more than 20 years, Ramsay says he has seen the quality and volume of the material deteriorate.
“Office paper 20 years back was not mixed sheet,” Ramsay says. “There was no groundwood content; it was all long fiber.”
Office collection bins have gone from mostly white paper to a mix also containing catalogues, magazines and newspapers and even the occasional half-eaten sandwich. Mixed office paper is transported to a processing facility where the groundwood grades are removed, and the cleaned pack becomes SOP. As a result of the trend toward mixed collection, the volume of SOP available to paper mills is shrinking.
“While traditional sheet goods from the office environment still exist, volumes have decreased substantially,” Ramsay says.
The advent of regulations like the Health Insurance Portability and Accountability Act (HIPAA), the Fair and Accurate Credit Transaction Act of 2003 (FACTA) and the Gramm-Leach-Bliley Act (GLB, also known as the Financial Services Modernization Act of 1999) also have reduced the available volume of SOP during the last 20 years. These three federal laws require safeguards in the handling of confidential or private information. As a result, document destruction services have grown in demand.
Before the introduction of HIPAA, for instance, hospitals and medical facilities were not focal points of collection. These files were stored and then destroyed by methods other than shredding. Now, paper recovered from medical facilities, financial institutions, governments and law offices all require shredding in light of privacy issues related to the content of these documents.
“Shredding has severely limited full-sheet SOP availability,” Ramsay says. “In addition to those companies that are required by law to shred their documentation, many companies shred to prevent their private business from becoming public.”
This increase in shredding has led to a glut of shredded fiber. According to Jon Chase, vice president of National Paper Recycling, Camden, N.J., “The market has been saturated with shredded material from mobile shred trucks and stationary shred operations located within traditional recycling or packing plants.”
Challenging the Mills
In addition to presenting challenges for processors, shredding also can negatively affect paper mills. One repercussion has to do with the size of the shredded fiber. “Contemporary shredding systems are equipped with screen systems that enable the size of the residual product to be adjusted from less than 2 inches down to a fine powder,” Chase says.
The finer the shred, the harder the material is for paper mills to work with; this increases the percentage of shrink.
Additional handling is often needed, as well, as bales consisting of finely shredded material have a tendency to “bleed” or break apart when they are handled.
When the shredded material is fed into the mill pulping system, the yield is reduced, as fiber continues to be lost from each cut as the shredded material goes through the mill’s screening process.
Another issue paper mills have with shredded material is the inclusion of nonpaper material. For instance, HIPAA regulations mandate that any papers containing personal identifying information be rendered unrecognizable. While most medical files start out as standardized forms, patient information and clinical results are typically retrieved electronically and printed out on pressure sensitive labels, which are then attached to the standardized forms. This is also true for many academic institutions and direct mail operations. These organizations use bar-coded labels affixed to documents to track pertinent information and information flow. As a result of the increased use of adhesive labels, more pressure sensitive adhesives are flowing into the SOP stream.
Also, papers originating from hospitals and medical facilities often include X-rays, plastic and plastic-lined envelopes or bags as well as office paper. Because paper commingled with labels and plastics often are not separated prior to shredding, paper mills must deal with glue and plastic contamination and with lower yields.
Making Adaptations
Changes in SOP generation have led processers and mills to make adjustments to the way they treat SOP. Because different mills have differing tolerance levels for prohibitive and out-throw materials in the pack, Chase says, it is important for the packer to know where the material is being sold and the nature of the mill’s specific cleaning system. Based on this knowledge, processing facilities can then create sub-grades of office pack (such as A, B and C) based on these tolerance levels. Developing a customer base for each sub-grade will improve processor efficiency.
Mixed paper collection and document shredding are here to stay, and they will continue to put pressure on the SOP supply chain. At the same time, generation levels for office paper will not relieve this pressure. Why? First, as long as economies across the globe continue to struggle, demand for paper will hold steady. While the direct correlation between GDP growth and paper demand has weakened somewhat, the relationship persists. Second, as more and more offices move toward greener, paperless operations, generation will not grow on that front, either.
Because SOP is likely to remain a mix of assorted paper grades, contaminated with glue and plastics, and often shredded into fine particles, the industry—both processors and mills—will need to pursue continuous adjustments to their processes and pulping systems to maximize yield. These trends will pose greater challenges for processors and mills in the future.
The author is manager of Forest2Market’s Recovered Fiber Practice. Forest2Market soon will begin publishing prices for SOP in Market2Mill, its monthly recovered fiber price report and quarterly benchmark. She can be reached at 704-540-1440, ext. 35, or at barbara.hudson@forest2market.com.
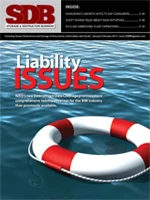
Explore the February 2012 Issue
Check out more from this issue and find your next story to read.
Latest from Recycling Today
- Magnomer joins Canada Plastics Pact
- Electra names new CFO
- WM of Pennsylvania awarded RNG vehicle funding
- Nucor receives West Virginia funding assist
- Ferrous market ends 2024 in familiar rut
- Aqua Metals secures $1.5M loan, reports operational strides
- AF&PA urges veto of NY bill
- Aluminum Association includes recycling among 2025 policy priorities