An efficient screening system helps C&D recyclers separate unwanted materials from wanted materials. What recyclers want to keep or toss depends largely on their end markets and the types of materials that come through their facilities.
Purchasing the wrong type of system could affect a recycler’s overall profitability, which is why it’s important for a recycler to know the volume his operation can handle and the various types of screens available before investing in a system.
SCREENING NEEDS"The end product is definitely a prerequisite to what style screen is required, as we all know that one style screen does not meet all the different screening needs in the C&D market," says Tim Griffing, systems engineer for Continental Biomass Industries Inc. (CBI), Newton, N.H.
To find out what works best for each recycler, there are a couple of factors that should be taken into consideration. The biggest thing is knowing what kind of material will be processed, the volume of material to be run per hour and what the desired end product is going to be, says recycler Robert Lenzini, owner of MBL Recycling in Palatine, Ill.
When it comes to screen sizes, manufacturers recommend looking at the volume of incoming material and matching it to the separation for which the machine is designed. "The cost of a screen, especially at the front end of the system, is very high, and you must have a big enough machine to give you separation that equals your incoming throughput," says Bill Garr, sales engineer for Krause Manufacturing, Bellingham, Wash.
Lenzini purchased a dual-line system to match his infeed material. His primary finger screen cuts the incoming material into an 8-inch minus, which goes down one line, and anything 8 inches or larger is sent down another line.
The biggest mistake recyclers make is not taking into consideration their end products when purchasing a screening system. The size of the fines determines the size and type of screen that a recycler uses, and options can include trommels, vibratory screens or a variety of other styles, Griffing says. "It is very important that the customer knows the market which their material will be used for," Griffing says. It’s also imperative that a recycler’s screening system matches the volume of incoming material. When planning their sorting systems, recyclers need to have their maximum throughput in mind, Garr says.
SCREEN TYPESThe type of screens a C&D recycling company uses once again depends on what its incoming material stream is made up of and what the company’s end markets are. "Disc screens are best suited for fines or ADC and work
Screening Shortcuts |
It’s imperative for C&D recyclers to purchase a screen system that meets their end product needs. With so many different types of screens to choose from, it is easy for recyclers to lose sight of their ultimate goals. Here are some short-cuts to help you stay on track when it comes to purchasing a screening system: 1. Two major factors recyclers should take into consideration before purchasing a screening system are their incoming materials and desired end products. 2. Recyclers need to remember that one size does not fit all applications, says Tim Griffing, Continental Biomass Industries Inc. (CBI), Newton, N.H. 3. Recyclers should know that a large screen at the front can split incoming material into two different lines, doubling input flow, says Bill Garr, sales engineer for Krause Manufacturing, Bellingham, Wash. 4. Before purchasing a screening system, recyclers should visit other facilities to look at systems and see how they handle the plants’ material. 5. If a recycler’s budget is tight, Garr recommends putting a smaller, less expensive machine at the end of the system. "You will be able to sort 50 percent or better of the flow before the screen, allowing a smaller machine, which means less cost," he adds. |
"In my experience, anything under 1-inch minus, you need to go with a star screen or trommel screen," Lenzini says. "A finger deck doesn’t do any good till you get over 1.5 to 2 inches."
Wilfred J. Poiesz, western region vice president for Stamford, Conn.-based Lubo USA, adds that the smaller stars on star screens are typically used to screen fines and dirt down to a 3/8-inch size. For material smaller than 3/8 inches, he suggests using a flexible deck screen. Poiesz also recommends using the largest stars to separate the 12-inch and larger fractions.
It is also common for recyclers to use screens in tandem. For instance, Griffing recommends using the trommel as a primary screen to size material to 1 inch or less and a vibratory screen as a secondary screen to remove the fines from the 8-inch-minus fraction. "The trommel has an octagonal shape for durability and ease of changing out screen panels, and the Vibra Snap screen is very efficient and makes a tight spec-size product," he adds.
Garr also suggests putting a large trommel at the front of the line or a smaller unit at the end to split the flow and/or to take out fines. He cautions recyclers that units with a 5/8-inch screen will need brushes and can cause problems in high-moisture areas, but can be handled with no problem.
Griffing says he has qualms about using star screens or disc screens for C&D because of material wrapping around the rotating shafts and the higher maintenance costs that an operation can realize over time.
The high maintenance costs is why Lenzini, a strictly C&D recycler, recently changed out his star screen for another finger screen in his dual-line system. "The star screen has rubber discs which incur more wear," he says. "For C&D recycling, I found that the finger screen is really the most durable."
Poiesz, on the other hand, points out the positive features of the star screen in C&D applications. "The rubber stars are the reason why C&D materials don’t get stuck in the screen," he says. "Since the stars are made of rubber, heavy material, such as rock and concrete, that falls onto the screen is cushioned and therefore don’t break screen components on impact," he says.
As for maintenance, Poiesz says it’s limited to lubrication of bearings and drive chains, regular cleaning of trapped items, such as steel wires, and replacement of stars in the impact zone. "Dependent on material and tons throughout, we recommend replacing stars in the impact zone every three to six months," Poiesz says.
SCREENING VALUEMaterials that yield the highest value for recyclers include concrete, asphalt, OCC and metals. "Plastics, sheetrock, inerts and carpet can also have good markets, but they can vary from city to city," Garr says.
Even though these materials have the highest return, wood still makes up the highest percentage of the incoming stream. "Sorting out the wood to feed a cogeneration plant is the No. 1 best market for the wood and pays the most, but some wood cogeneration plants are more stringent on contaminated wood and can be a little more work," Garr says.
Griffing adds that the wood market has become spotty in light of different state regulations, such as New Hampshire’s ban on the burning of C&D wood.
The materials Lenzini’s system sorts out include wood, ferrous and nonferrous metals, cardboard, brick and concrete. Even with his dual-line system separating the material, he still has his employees perform a pre-sort. "Pre-sorting makes it a lot easier on the plant and on the guy picking," Lenzini says.
Griffing agrees pre-sorting is normally required, especially if star screens are being used. If a shredder is used, then he says much less pre-sorting is required. The items that typically cause jamming include large metal items, mattresses, concrete chunks and rugs.
Pre-sorting is just one way recyclers can help keep their systems running at optimum levels. Recyclers should also perform housekeeping along with preventive maintenance. This includes instructing workers to look at the openings of the screen on a daily basis to make sure they are clean, Garr says.
"Long vibrating finger decks have the problem with longer pieces spearing through the deck and causing material to hang up," Griffing says. This then requires the system to be shut down and cleared."
Recyclers should also check the screen mesh as well as grease the bearings routinely. Conducting these daily checks can help ensure the type of lasting productivity that can be seen in Lenzini’s screening system. "I have been running my finger screen for more than two years, and the only maintenance it requires is six screen fittings done once a week," he says.
The author is assistant editor of Recycling Today and can be contacted at kmorris@gie.net.
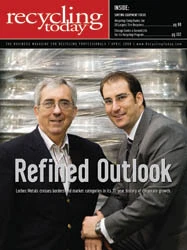
Explore the April 2008 Issue
Check out more from this issue and find your next story to read.
Latest from Recycling Today
- Athens Services terminates contract with San Marino, California
- Partners develop specialty response vehicles for LIB fires
- Sonoco cites OCC shortage for price hike in Europe
- British Steel mill’s future up in the air
- Tomra applies GAINnext AI technology to upgrade wrought aluminum scrap
- Redwood Materials partners with Isuzu Commercial Truck
- The push for more supply
- ReMA PSI Chapter adds 7 members