
Tire recycling has come a long way, according to tire processing veteran and current consultant Terry Gray of Houston-based T.A.G. Resource Recovery. However, Gray also remarked while speaking at the Spotlight on Tires session at the 2017 convention of the Institute of Scrap Recycling Industries (ISRI2017) that some of the end markets for scrap tires currently are facing difficulties, causing a sense of disruption in the overall market.
Gray said he started in the North American scrap tire processing sector in
The bad news for scrap tire processors is government-related obstacles they are facing in several key end markets, including athletic turf and tire-derived fuel (TDF)—the single largest end market for tire processors in the U.S.
SOS for TDF
Gray said a tax credit that had been available to users of TDF had expired in some states, “so [energy] plants are failing that had converted to TDF.”
He said officials in one such state, Michigan, are acknowledging they will need to find and boost alternative end markets for scrap tires, but Gray said in many New England states, “It’s a real issue and they’ve got their heads in the sand.”
Not all the news is bad in the TDF market. In late May 2017, Chicago-based cement maker LafargeHolcim unveiled a new plant at its Ada, Oklahoma, cement facility after a three-year modernization project.
Through Geocycle, LafargeHolcim’s waste management company based in Dundee, Michigan, the Ada cement plant uses more than 3 million scrap tires per year as supplemental fuel to replace at least 20 percent of the fossil fuel, which includes coal and natural gas, used to power its facility.
According to LafargeHolcim, the modernization focused on
“Investing in the environment is critical for the health and long-term viability of the communities where we work, which is why we reuse materials that would normally be sent to landfills,” says Mike Langan, Ada plant manager. “We appreciate the support of the Oklahoma Department of Environmental Quality in
In March 2017, Colorado-based Vista International Technologies Inc. provided an update on progress in its scrap-tire-based waste-to-energy (WTE) operations.
Vista’s commercial scale pilot gasification unit (MFG-8 Thermal Gasifier) has completed its independent testing phase. The company says it plans to present the results to the states where it has projects in development, with the goal of securing permits for these projects.
The company also conducted its own tests concurrent with those managed by the third party and found that the unit met or beat Vista’s internal targets for efficiency, emissions, feedstock variability and moisture content, among other measures.
Vista says its tire operations have continued to see strong revenue in the first quarter in light of increased disposal (tipping) fees as compared with prior quarters. However, margins are currently lower as the company has increased its hauling of scrap material to the landfill so it can clear certain areas of the facility as it works toward obtaining its permit for scrap tire processing and storage with the TCEQ (Texas Commission on Environmental Quality). That permit would allow the facility to continue operating for the next five years.
Vista’s main stumbling block in its permit application process has been its pursuit of a variance from the Dallas County Fire Marshal that would allow it to keep its storage piles at their current sizes rather than at a significant reduction.
Vista has been producing WTE gasification systems for more than 20 years, with installations on three continents. The company says its technology has low costs of installation and operation and allows for the processing of virtually any hydrocarbon-based materials, including scrap tires.

Retreating from the field?
In the ground or crumb rubber markets, the sports field additive sector had been emerging as a strong consumer, but that end market is taking a hit from (as yet unsubstantiated) claims that athletes coming into contact with crumb rubber on fields are experiencing health issues, including cancer.
By Gray’s estimate, some 30 percent of sports fields are in regions such as New England and California, where regulators are advising turf managers to be wary of using crumb rubber. In 2015, 25 percent of crumb rubber was used on sports fields and another 23 percent as playground surfacing or as mulch, so shrinkage in any of those markets will cause considerable disruption, he said.
The concern about crumb rubber as a health issue has been raised in media reports throughout the middle of this decade. (It was the subject of the 2016 Recycling Today Commodity Focus on scrap tires, “Penalty flag,” found in the July 2016 issue, starting on page 34.)
Not all of the media coverage has been alarmist in nature. In mid-May 2017, the Everett, Washington-based HeraldNet, www.heraldnet.com, ran a story on the topic headlined, “Study: Crumb rubber cancer risk ‘at or below 1 in a million.’”
The article reports on tests of crumb rubber sports fields conducted in five U.S. cities, including one in Everett, which “found that the cancer risk for children playing on the fields was at or below 1 in a million.”
The $200,000 study was conducted by Maryland-based Jenkins Environmental Inc. and was undertaken at the request of the Cal Ripken Sr. Foundation in Baltimore, according to HeraldNet.
The article quotes the foundation’s CEO Steve Salem as saying, “We are very confident in the results. Our role in this was to bring the right people together, to come up with the funding to get this done and make sure the kids were safe.”
The foundation sponsored the construction of the five fields tested for the study, with the others being in Maryland, Virginia,
HeraldNet writes that the foundation’s decision to test the fields “came as concern has grown over the safety of playing on the artificial turf fields” because “the tiny crumb rubber particles used for fill [can] come in contact with the skin of players.”
Sponsored Content
Labor that Works
With 25 years of experience, Leadpoint delivers cost-effective workforce solutions tailored to your needs. We handle the recruiting, hiring, training, and onboarding to deliver stable, productive, and safety-focused teams. Our commitment to safety and quality ensures peace of mind with a reliable workforce that helps you achieve your goals.
Sponsored Content
Labor that Works
With 25 years of experience, Leadpoint delivers cost-effective workforce solutions tailored to your needs. We handle the recruiting, hiring, training, and onboarding to deliver stable, productive, and safety-focused teams. Our commitment to safety and quality ensures peace of mind with a reliable workforce that helps you achieve your goals.
Sponsored Content
Labor that Works
With 25 years of experience, Leadpoint delivers cost-effective workforce solutions tailored to your needs. We handle the recruiting, hiring, training, and onboarding to deliver stable, productive, and safety-focused teams. Our commitment to safety and quality ensures peace of mind with a reliable workforce that helps you achieve your goals.
Sponsored Content
Labor that Works
With 25 years of experience, Leadpoint delivers cost-effective workforce solutions tailored to your needs. We handle the recruiting, hiring, training, and onboarding to deliver stable, productive, and safety-focused teams. Our commitment to safety and quality ensures peace of mind with a reliable workforce that helps you achieve your goals.
Sponsored Content
Labor that Works
With 25 years of experience, Leadpoint delivers cost-effective workforce solutions tailored to your needs. We handle the recruiting, hiring, training, and onboarding to deliver stable, productive, and safety-focused teams. Our commitment to safety and quality ensures peace of mind with a reliable workforce that helps you achieve your goals.
Sponsored Content
Labor that Works
With 25 years of experience, Leadpoint delivers cost-effective workforce solutions tailored to your needs. We handle the recruiting, hiring, training, and onboarding to deliver stable, productive, and safety-focused teams. Our commitment to safety and quality ensures peace of mind with a reliable workforce that helps you achieve your goals.
Foremost among the people expressing those concerns
However, the Ripken Foundation-sponsored study is the second one in 2017 that has concluded that crumb rubber sports fields are safe, according to HeraldNet. The news organization says in January 2017 “a review by the [Washington] Department of Health found no evidence that playing on crumb rubber sports fields caused soccer players to get cancer.”
Reactions and strategies
With TDF markets troubled in some regions and sports turf markets in retreat in others, Gray and other speakers at ISRI2017, which was held in late April in New Orleans, provided updates on other markets.
Gray characterized the rubberized asphalt market for ground tires as often subject to “wait and see” attitudes, but he said the manufactured products sector for molded rubber has been one brighter spot.
J.D. Wang, CEO of California-based ReRubber LLC, after acknowledging that the firm “has gone through eight years of disruption” itself, said his company’s investors have been putting most of their R&D resources into the crumb rubber and powder categories. “In our first five years, we processed a lot and failed a lot,” he said.
ReRubber is focusing on making rubber powder, researching and opening up end markets for the tire-derived powder to be used in protective and architectural coatings applications. The company is exploring a supply loop that Wang said allows it to “innovate” and conduct research in California, then more rapidly implement the ideas in Asia or “work out the kinks” there before bringing successful ideas back to the United States.
Offering a point of view from state government, Elizabeth Hoover of the Arkansas Department of Environmental Quality (DEQ) said TDF used at cement plants represented “about the only markets” for scrap tires in that state in the 1990s.
She remarked that emissions concerns about zinc levels had harmed that market, and now the health questions surrounding the field turf market are presenting a new disruption. Unless scrap tire processors have diversified markets, “you have problems on your hands,” Hoover warned.
Her message to scrap tire processors was that states can provide help in the form of loans for equipment, workshops and conferences and assistance in identifying and developing end markets. She also remarked, however, that because of tight state budgets, “a lot of that [potential assistance] is beginning to dry up.”
Get curated news on YOUR industry.
Enter your email to receive our newsletters.
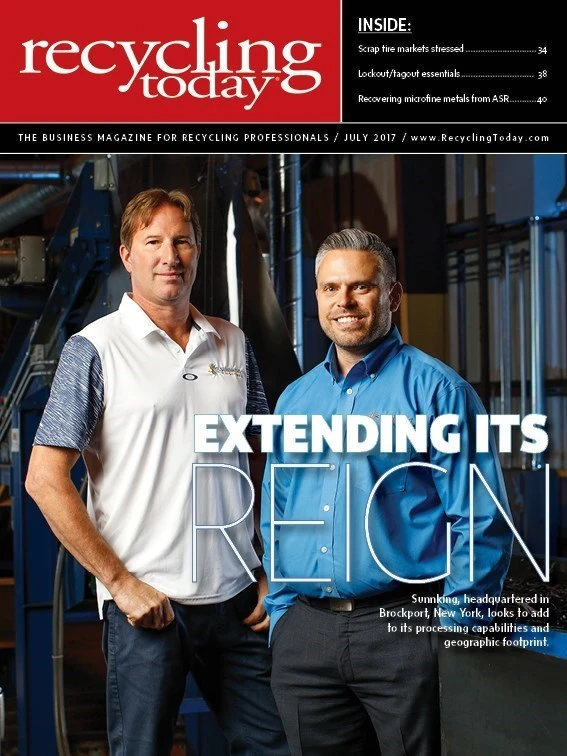
Explore the July 2017 Issue
Check out more from this issue and find your next story to read.
Latest from Recycling Today
- Green Cubes unveils forklift battery line
- Rebar association points to trade turmoil
- LumiCup offers single-use plastic alternative
- European project yields recycled-content ABS
- ICM to host colocated events in Shanghai
- Astera runs into NIMBY concerns in Colorado
- ReMA opposes European efforts seeking export restrictions for recyclables
- Fresh Perspective: Raj Bagaria