
Scott Newell says he has been given the nickname “Professor Newell” by those working for his El Paso, Texas-based company, Newell Recycling Equipment LLC (NRE), because of his willingness to share information on shredding technology with customers, colleagues and competitors alike.
The nickname is meant as a lighthearted joke, but Newell’s shredder expertise is anything but. Having spent a lifetime in the scrap industry, his last name is synonymous with the equipment itself.
Scott and his father, Alton Newell, are responsible for the design of the modern automobile shredder. The original Newell shredder, developed by Alton, was named a National Historic Mechanical Engineering Landmark by the American Society of Mechanical Engineers in 1994.
Before he started manufacturing shredders, Scott spent the first seven years of his career running a scrap yard in Phoenix.
He estimates shredders bearing the Newell name, which have been installed all over the world, have been in operation for decades.
Throughout his manufacturing career, he’s continued to seek new and better ways to create machines that are increasingly productive and deliver a lower cost per ton processed.
Through NRE, Scott has overseen a continued global expansion of the family business, including into China, where nearly 70 of his shredders are operating. Twenty of those machines have more than 10,000 horsepower and can process more than 1 million tons per year.
“Fortunately, for me, we’ve been able to be very successful,” he says of the company’s global reach. “We’ve had our ups and downs, but we’ve always tried to handle ourselves transparently, and I think that’s allowed us to maintain relationships with people all over the world.”
In the following interview, Newell discusses the evolution of his shredder business and innovations that have pushed the technology forward.
Q: When did you develop the philosophy of “What’s good for the shredding industry is good for us,” and why is that your mentality?
A: I tell my engineers and my salespeople that anything that’s good for the shredding industry is good for us because if we’re seen as the innovators and the ones leading, then we get some prestige out of that. We get some credibility from that.
Sometimes people will come to me and say, “I can buy your machine and I can buy it cheaper from someone else,” and, I say, ‘Sure, if you want to buy last year’s machine, you can buy it from anybody.’ If you want to buy next year’s machine, you had better buy it from us, because we operate these machines and we’re constantly looking for improvements, and the evolutionary changes are fantastic. [Sharing information] is good for us.
Q: What makes for an efficient shredding operation?
A: Let’s say I know it takes 14 kilowatts an hour to shred 1 ton of material to a density of 1.1 in a certain-sized machine, and then I know what the horsepower is, I can [determine] a theoretical capacity. If I use this machine at 100 percent capacity all day long, well, of course, nobody does that—we typically rate our machines at 50 percent or 60 percent of the theoretical capacity—that poses the question, why don’t we run at theoretical capacity?
The short answer is the shredder’s not being fed. If you could put the material in the shredder on a consistent basis, minute by minute, hour by hour, you would come closer to that theoretical capacity. That’s when we started looking at computer controls for the shredder.
Now, in the most modern machines, we have a computer controlling the speed of the feed rollers, the speed of the infeed conveyor, and we’re actually trying to drive the shredder motor closer to the real capacity.
Q: What are some innovations coming into the shredder space? What might be the next wave in shredding?
A: When I’m looking at the future, it’s more automated separation but also more in the plastic and waste streams. In some of the experiments I’ve been running on ASR [auto shredder residue], by using some very aggressive air separation, we can create an aggregate product … that can be used to make concrete. … There are a lot more things to recycle than just the metal, and if we can figure out how to do some of that, we can create some more products.
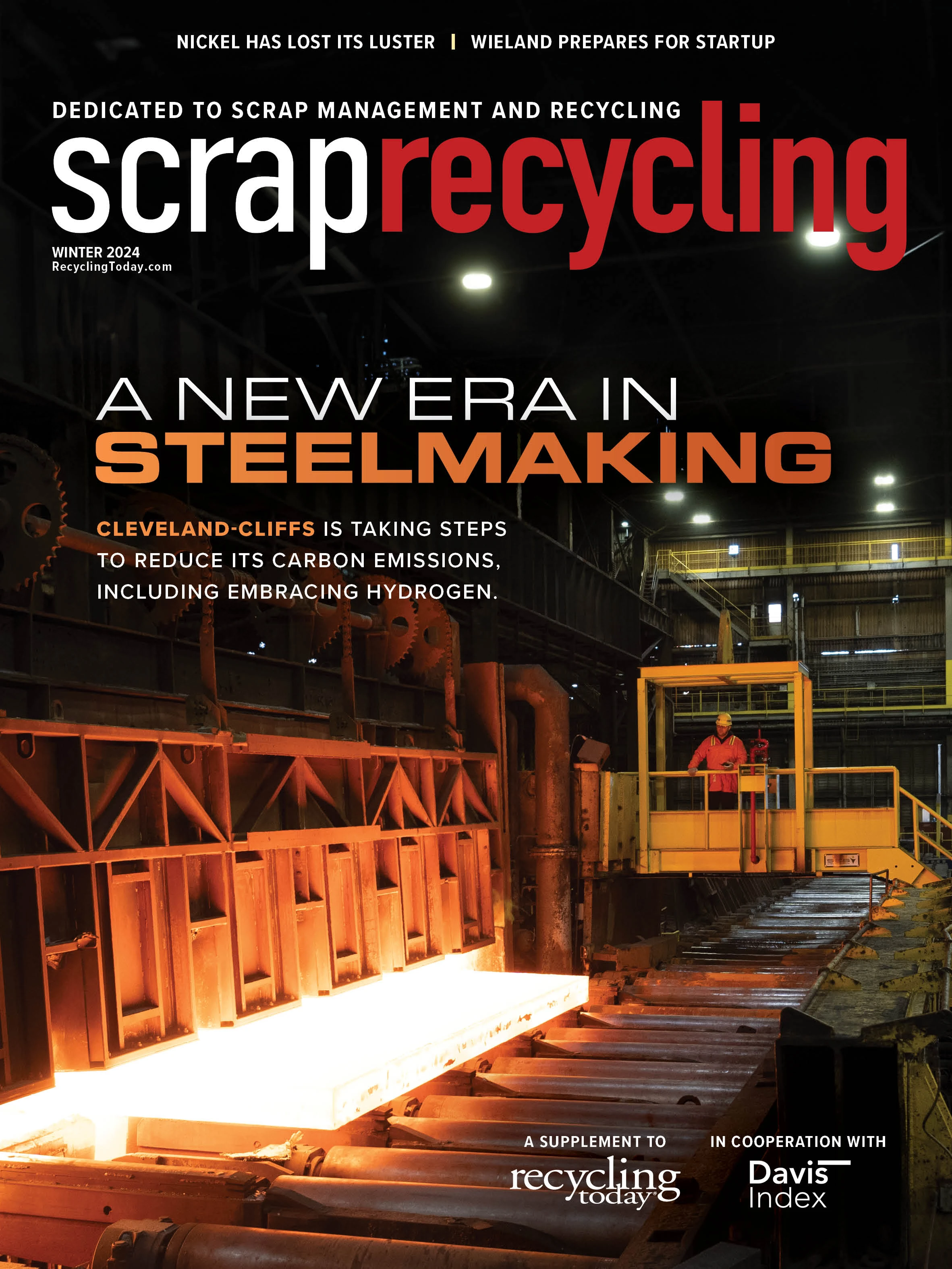
Explore the Winter 2024 Scrap Recycling Issue
Check out more from this issue and find your next story to read.
Latest from Recycling Today
- Toppoint Holdings expands chassis fleet
- Lego creates miniature tire recycling market
- Lux Research webinar examines chemical recycling timetables
- Plastics producer tracks pulse of wire recycling market
- Republic Services, Blue Polymers open Indianapolis recycling complex
- Altilium produces EV battery cells using recycled materials
- Brightmark enters subsidiaries of Indiana recycling facility into Chapter 11
- Freepoint Eco-Systems receives $50M loan for plastics recycling facility