
Photography
For nearly 75 years, the Goldstein family has owned Alter Trading Corp. Michael Goldstein, executive vice president of operations at St. Louis-based Alter and a third-generation company owner, grew up in and around his family’s business.
“I remember going to my grandparents’ house on Sundays for lunch. My grandfather, dad and uncles would always talk business in the living room,” Goldstein says. “While in the back of my mind I thought maybe one day I might come into the scrap business in some capacity, I didn’t join the business right out of college.”
Instead, casino construction and development was his first stop after college. However, after the Great Recession hit in 2008, casino projects dried up, and Goldstein needed a job. He decided to work his way up at Alter, starting in operations at a yard in Des Moines, Iowa.
“I came into scrap with an open mind and eager to learn,” Goldstein says. “I started at the bottom as a broom and shovel operator, which is the only way to learn this business.”
Since joining Alter in 2009, he says there isn’t much he hasn’t done, “except drive a semi.” As executive vice president of operations, he oversees all of Alter’s yards and the company’s safety, quality and project management departments.
Goldstein shares more about how Alter has grown in the past decade as well as his take on issues affecting the scrap industry.
Q: You joined the family business in 2009. How has the company grown and changed since then?
A: Through acquisition, we are probably double the size. A lot comes with this, for example, more volume. The more we buy, the more we produce, the more we sell and the more homes we need for our products. This has really allowed us to become a major supplier to mills and foundries around the world.
More equipment means we have more stuff that breaks.
[We also have] more people.
Additionally, the vertical integration has been impressive. The nonferrous recovery systems continue to evolve, allowing us to extract more and more metals from the waste streams. With the number of shredders we have, we’re able to consolidate the [auto shredder residue] at large nonferrous recovery plants, which helps us extract these different nonferrous commodities.
In recent years, we’ve integrated vertically further by building two media plants, which use zorba to make twitch, for use in the automotive industry.
It’s really the size and scale that we’ve grown to that has allowed us to have this vertical integration.
Q: Alter oversees dozens of facilities in the U.S. plus a trading office in Singapore. How does it ensure consistency across its sites and offices?
A: You are only as strong as your weakest link. In order to be as strong as we can, we need to communicate across the regions, departments and teams. While it’s not always easy, communication is key to consistency.
Q: How could the scrap industry do a better job of attracting and retaining talent?
A: Hiring is a challenge in every industry right now.
Part of the challenge with our industry, specifically, is the perception people have of us. Most people don’t understand what it is we actually do. They drive by and see piles of junk. They read about scrap theft and think we’re a bunch of thieves.
What people don’t understand is that there are recycling centers in every community. We are a place people come to bring recyclable materials that are eventually used to make new goods that are used every day. We are job creators. We are an essential part of the supply chain, and the products we make are produced in the most environmentally friendly way possible. So, I think one way hiring could be improved is if the perception of our industry changed.
Q: What are some other issues affecting the scrap industry presently?
A: In addition to environmental factors and hiring issues, the transportation issues impacting the supply chain have had a major impact on our industry. It’s very difficult to ship material.
The equipment vendors are having the same problem, so when we order new equipment, it takes much longer than it used to … to arrive.
The war [in Ukraine] has had an impact on the industry as it relates to commodity supply and demand.
COVID continues to impact everyone’s lives.
The list goes on and on.
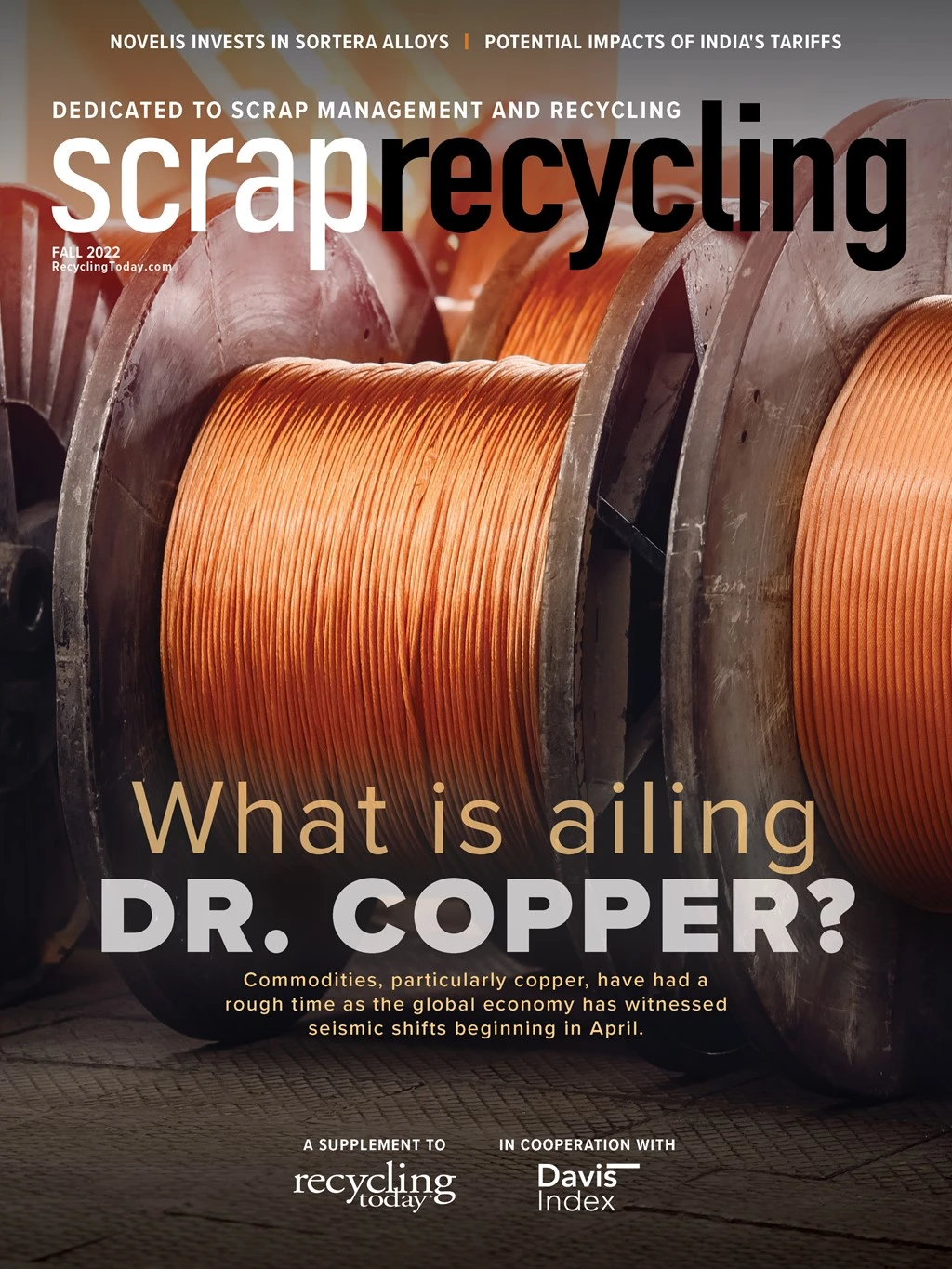
Explore the Fall 2022 Scrap Recycling Issue
Check out more from this issue and find your next story to read.
Latest from Recycling Today
- USTR announces phased measures designed to address China’s shipbuilding dominance
- APR, RecyClass release partnership progress report
- Clearpoint Recycling, Enviroo sign PET supply contract
- Invista expanding ISCC Plus certification program
- Redwood partnership targets recycling of medium-format batteries
- Enfinite forms Hazardous & Specialty Waste Management Council
- Combined DRS, EPR legislation introduced in Rhode Island
- Eureka Recycling starts up newly upgraded MRF