![]() Left to right: Clarence White, Ramon Ortiz, Doug Scroggins, Jim Gazley, Rafael Romero (Photo: Doug Scroggins/ARC) |
Las Vegas-based Aircraft Recycling Corp.’s (ARC’s) work begins when an aircraft’s service ends. Just because the airplane itself may no longer be useful, the same cannot be said for the scrap metal, carbon fiber and salvageable spare parts it contains. Approximately 83 percent to 88 percent of a typical aircraft is recyclable, says Doug Scroggins, the company’s managing director. Aluminum makes up the bulk of the material most commonly recovered for recycling, but airplanes also contain recyclable titanium, stainless steel and copper wire.
ARC has been in the business of disassembling and demolishing old aircraft for more than six years. Recycling an airplane is generally a two-part process—dismantling and demolishing. To dismantle, ARC brings in a crew of aviation mechanics licensed by the Federal Aviation Administration (FAA) to remove, sort and tag parts for reuse. For demolition, the crew uses equipment that would look at home on any building demo site—hydraulic excavators fitted with demolition attachments such as grapples.
Not all of the aircraft that end up in ARC’s hands reach the end of their useful lives through simple age, wear and tear. Some of the planes are hurried into early retirement through accidents, including two recent jobs.
AMERICAN AIRLINES — BOEING 767
The American Airlines Boeing 767 N330AA that ARC processed during a five-week period during October and November 2008 had suffered irreparable damage years before it ended up on ARC’s project list. In June 2006, the aircraft was conducting an engine maintenance test when the high pressure turbine ruptured. Fortunately, all three maintenance personnel escaped uninjured. The 767 was not quite as fortunate. During the rupture, debris punctured the fuselage and the engine caught fire, damaging the airframe.
The 767 was written off by American’s insurance company and sold to a company that provides aftermarket aviation services to the airline industry.
While it took ARC a total of five weeks to process the American Airlines 767 at the Los Angeles International Airport, four of those weeks were spent dismantling the aircraft. The demolition itself only took about five days, says Scroggins. A variety of parts was salvaged—including the electronics, landing gear, flight controls and actuators—with most of those items going to American for use as spares for the rest of its fleet before the hulk was reduced for scrap, says Scroggins. The scrap material is currently being separated at ARC’s Victorville, Calif., location.
NORTHWEST AIRLINES — BOEING 747
Recently, ARC completed a dismantling and demolition project in Guam, where a damaged plane had sat for several years before the decision was made to demolish it for scrap.
In August 2005, a Northwest Airlines flight on a Boeing 747 N627US landed with its nose gear retracted at the Guam International Airport, leading to an emergency evacuation. While the crew and passengers all escaped, the rough landing severely damaged the plane. Once deemed beyond economical repair, the plane was bound for disassembly by ARC. Work began on Sept. 7, 2008. Prior to demolition, the Pratt & Whitney engines and auxiliary power unit were salvaged for reuse. Some 325,000 pounds of scrap was recovered for recycling from the single aircraft.
The author is associate editor of Recycling Today and can be reached at jgubeno@gie.net.
WANT MORE?
Enter your email to receive our newsletters.
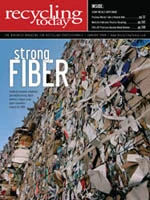
Explore the January 2009 Issue
Check out more from this issue and find your next story to read.
Latest from Recycling Today
- Recyclers likely to feel effects of US-China trade war
- BCMRC 2025 session preview: Navigating battery recycling legislation and regulations
- Yanmar Compact Equipment North America appoints new president
- LYB publishes 2024 sustainability report
- Plum Creek Environmental acquires Custom Installation LLC
- Avis introduces Harris American Co.
- International Paper in talks to divest 5 European box plants
- Recycled PP from Polykemi, Rondo Plast used in flood protection product