Throughout 2008, scrap prices lived up to their reputation for volatility. In particular, many steelmakers and scrap recyclers were caught by surprise in October 2008 when scrap prices for No. 2 shredded scrap dropped from $540 per ton in August to $230 per ton.
The volatility is of particular concern to electric arc furnace (EAF) steelmakers. EAF steelmaking has been steadily increasing throughout the past 20 years. According to data provided by Canaccord Adams, Vancouver, Canada, it is estimated that 58 percent of U.S. steel production will be done using EAFs in 2008, compared to 38.4 percent in 1991. The data also shows an estimated 20 percent increase in U.S. steel production from 80 million metric tons in 1991 to an expected 100 million metric tons in 2008.
Analysts and steelmakers attribute last year’s increase in U.S. steel production and EAF steelmaking to many factors, including higher domestic demand and a stronger U.S. dollar relative to foreign currencies. Despite a different economic landscape in 2009, some analysts and steelmakers say the trend in the U.S. toward EAFs will continue to grow in the coming years.
BALANCING COSTS
In 2008, the U.S. steel industry experienced its lowest level of production in the past 24 years, according to Eric Glover, a scrap analyst with Canaccord Adams. He says scrap prices also have declined dramatically this year because demand has dropped so rapidly (as evidenced by domestic steel production data). But before the scrap market pricing floor dropped out, these industries were experiencing record high prices for steel and scrap.
And it was these unprecedented high prices that led many EAF steelmakers to look into new ways to control costs while also maintaining operational efficiency.
"Unfortunately, there are limited options available to most EAFs, particularly flat-roll shops, when scrap costs move up sharply in a brief timeframe," says Rich Brady, vice president of ferrous sourcing and marketing, Steel Dynamics Inc. (SDI), Fort Wayne, Ind. "Given most mills source their requirements from month to month, scrap consumers have little choice but to react to these fluctuations and, as evidenced in recent months, can be exposed to significant market risk."
SDI’s method for controlling costs in an escalated price market includes continually reviewing its melt mixes to optimize raw material costs and balancing quality requirements with scrap market conditions to ensure the company achieves the most competitive cost structure.
Matthew Yeatman, vice president of raw materials at Gerdau Ameristeel, Tampa, Fla., adds that a more variable cost structure is the one advantage EAF steelmakers have over blast furnace operations. "We can adjust shifts to times of the day when power is cheaper and we also attempt to optimize our scrap mix to match the grade of the scrap used with the steel being produced," he says.
EAF, or mini-mill, steelmakers also have tried to control their raw materials costs through acquisitions. "Over the past few years, many steelmakers, including Nucor Corp., Charlotte, N.C., and Steel Dynamics, have aggressively acquired scrap metal processors to supply their own feedstock to their steel operations," Canaccord Adams’ Glover says. "So the margins the steelmaker would originally pay to the scrap supplier, they now get to keep for themselves."
He says steel mills also have attempted to control their gross margins by adding scrap surcharges on to their finished steel products.
SCRAP ALTERNATIVES
Another way steel mills manage their costs when scrap prices are high is by using scrap alternatives, such as direct-reduced iron (DRI) and hot-briquetted iron (HBI) in their steel mixes in place of scrap.
"Whether scrap alternatives are a cost-effective way for EAF steelmakers to obtain raw materials really depends on the price of scrap and the scrap alternatives," Glover says. For example, Glover says when scrap prices rose sharply, SDI used the opportunity to invest in its own nugget production plant, which seemed to make a lot of strategic sense. But now that scrap prices are less than $300 per ton, Glover says this project may not be as cost effective as once thought. The nugget plant, in Hoyt Lakes City, Minn., is a joint-venture between SDI and Kobe Steel.
In response, Brady says that while the present economic environment may delay some projects, the company is pushing forward with its iron-making projects, including the nugget plant, as this still represents a key part of SDI’s longer term raw materials strategy.
"Our Iron Dynamics facility currently supports the Butler, Ind., steel operations with hot metal and HBI approaching a rate of 25,000 gross metric tons per month, supplementing consumption of prompt industrial scrap," Brady says. Regarding the joint-venture project, Brady says Mesabi Nugget LLC is still scheduled to be operational in 2009, with the first module having a capacity of 400,000 metric tons per year of what he calls ultra-high purity iron pellets.
On the other hand, while scrap alternatives can be cost effective for flat-rolled EAF producers who need high quality and low residual substitutes, Yeatman says they are not cost effective for long-product EAF producers who do not need low residual scrap to produce long steel.
But one thing steelmakers and analysts do agree on is that scrap alternative technologies will continue to evolve as EAF steelmaking grows domestically and globally. According to Midrex Technologies’ Web site, world EAF steel production continues to grow because of its economics, scale considerations, flexibility and environmental effects. The company adds that the availability of scrap and alternate iron sources, such as DRI and pig iron, and access to reasonably priced electricity, have made this growth possible.
So to keep up with its customers’ growing needs, in addition to developing technologies for hot discharge, transport and charging of DRI to the EAF, Midrex is also developing hot transport by conveyor or vessel and new melting technologies.
A BRIGHT FUTURE
Even in a down market, many mini-mill steelmakers say they are optimistic about the future.
According to an SDI press release, even though the company’s combined steel operations are expected to operate at an approximate 50 percent utilization rate during the fourth quarter of 2008, the company forecasts that 2009 financial results could approach and possibly surpass full-year 2008 record earnings.
"We believe that the precipitous decline in ferrous scrap prices has run its course, as prices rose slightly from November to December," Keith Busse, chairman and CEO of SDI says in a company press release issued in mid-December of 2008. "A more stable recycled metallic market, combined with lower-cost ferrous scrap inventories at our flat and long-product steel operations, positions the company to achieve improved operating margins in the first quarter of 2009."
Many steelmakers and analysts also see EAF steelmaking gaining more momentum in the U.S. going into 2009. "The North American EAF producers will continue to grow market share as technology is advanced and manufacturing capabilities are expanding," Brady says.
He adds that EAF steelmaking also remains one of the "greenest" manufacturing segments in the world.
Elaborating on this, Glover says, "EAFs have been steadily increasing for years because they’re more efficient and economical than basic oxygen furnaces, the reasoning being that EAFs can produce steel faster and with fewer harmful emissions."
Yeatman adds that he doesn’t see any radical changes to EAF steelmaking technology heading into 2009. "We will still use electrodes and electric arc furnaces to make steel," he says. "However, the industry will continue to seek and develop productivity through energy efficiency and other operational gains."
The author is assistant editor of Recycling Today and can be contacted at kmorris@gie.net.
Get curated news on YOUR industry.
Enter your email to receive our newsletters.
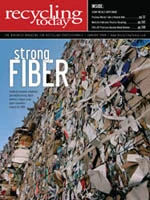
Explore the January 2009 Issue
Check out more from this issue and find your next story to read.
Latest from Recycling Today
- Toppoint Holdings expands chassis fleet
- Lego creates miniature tire recycling market
- Lux Research webinar examines chemical recycling timetables
- Plastics producer tracks pulse of wire recycling market
- Republic Services, Blue Polymers open Indianapolis recycling complex
- Altilium produces EV battery cells using recycled materials
- Brightmark enters subsidiaries of Indiana recycling facility into Chapter 11
- Freepoint Eco-Systems receives $50M loan for plastics recycling facility