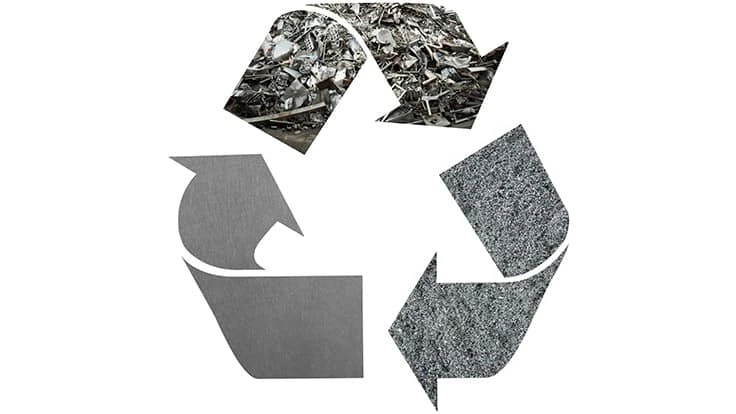
Image provided by AdobeStock.
“Scrap is a product of affluence,” veteran ferrous scrap trader Nathan Fruchter told Recycling Today in a May 2020 interview, referring to the impact of humming factories and traded-in vehicles and appliances on regional and global flows of scrap metal.
In the second quarter of 2020, that affluence was largely absent in North America and Europe, as both continents dealt with COVID-19 and subsequent workplace shutdowns. The ripple effects of the COVID-19-related decline in scrap generation are providing a case study that backs Fruchter’s observation and demonstrates the valuable role of secondary commodities in the global economy.
In the ferrous scrap market, even as steel mills scaled back output dramatically in the second quarter, scrap prices rose by $30 to $50 per ton in early May because scrap collection had dropped even faster. Longer-term, a recent analysis by Arlington, Virginia-based B. Riley FRB Inc. predicts a potential shortage of high-grade ferrous scrap in the United States as additional higher-grade electric arc furnace (EAF) steelmaking capacity comes online in the next couple of years.
Globally, steelmakers in China and their trade associations have been taking measures to make imported ferrous scrap shipments more welcome by trying to have scrap reclassified as a “resource.” One source tells Recycling Today steel firms there that are increasing their EAF capacity are particularly eager to be able to bring in imported ferrous shred. Even some policy makers there “realize that it is more effective than importing iron ore, because of economic issues as well as environmental issues,” says the source.
Recovered fiber prices ratcheted up even more quickly in the spring, as home deliveries and tissue demand caused paper mills to be a rare hot zone in the COVID-19 economy. This was happening at the same time many material recovery facilities (MRFs) were still examining how to best proceed with paper collection and sorting tasks amid a spreading virus landscape.
Nonferrous markets have reacted differently, depending in part on the end market they serve. In the third quarter of 2020, however, price momentum has been upward. This seems to have occurred in part because global copper and aluminum supply chains are now fully experiencing the impact of the hiccup in scrap supply.
Regarding copper, Reuters commodities columnist Andy Home writes in late July, “An already fragile scrap supply chain has been devastated by the coronavirus this year.” Copper producers in China, in particular, are scrambling to find material to melt.
On the aluminum side, Shanghai-based SMM Information & Technology Co. Ltd. reports in late July that, despite China’s attempt to thoroughly rev up its economy, “In June, the average operating rate of China’s secondary aluminum industry fell 0.7 percentage points to 48 percent, with a decrease of 4.3 percentage points year on year.” Adds SMM, “Operations at secondary aluminum producers [have] been beleaguered by scrap shortages.”
In China, the reason for scrap shortages extends beyond the market and into the political realm. The nation’s government has branded imported scrap as “foreign garbage” and has limited the amount that can enter with a strict quota system that is scheduled to reach zero in 2021.
The restriction in China—the world’s largest producer of finished metal and paper—has been criticized in the same terms as a high tariff: a self-imposed blockade on trade that results in self-inflicted wounds.
While China is busy keeping scrap out, governments in other nations—recognizing the value and current scarcity of scrap—have imposed or proposed banning exports of scrap materials. Neither type of barrier is welcomed by the world’s scrap recyclers and their trade associations.
Sponsored Content
Still relying on manual sorters?
Let AI do the heavy lifting. Waste Robotics delivers reliable, high-performance robots tailored for complex waste streams. They require minimal maintenance, are easy to operate, and are designed to boost your recovery rates. Smarter sorting starts with the right partner. Waste Expo Booth #1969 & REMA #2843
Click here to see our robots in action!Sponsored Content
Still relying on manual sorters?
Let AI do the heavy lifting. Waste Robotics delivers reliable, high-performance robots tailored for complex waste streams. They require minimal maintenance, are easy to operate, and are designed to boost your recovery rates. Smarter sorting starts with the right partner. Waste Expo Booth #1969 & REMA #2843
Click here to see our robots in action!Sponsored Content
Still relying on manual sorters?
Let AI do the heavy lifting. Waste Robotics delivers reliable, high-performance robots tailored for complex waste streams. They require minimal maintenance, are easy to operate, and are designed to boost your recovery rates. Smarter sorting starts with the right partner. Waste Expo Booth #1969 & REMA #2843
Click here to see our robots in action!Lest Americans think recycling regulatory woes belong only to other countries, it should be noted the United States Environmental Protection Agency (EPA) and some state agencies are creating potential pressure on the domestic scrap market by introducing increasingly tight volatile organic compounds (VOCs) emissions limits for auto shredding operations.
Millions of tons of metal are processed and prepared for melting annually via the nation’s 300 or so auto shredders. Much of the EPA shredder emissions scrutiny has been occurring within urban EPA “nonattainment” areas, where the most scrap is generated and where governments spend considerable effort creating and retaining manufacturing jobs.
Ideally, shredder operators and the EPA will agree to suitable solutions. A shredder crackdown in the U.S. may not lead to global shortages of scrap the way COVID-19 did, but it could prompt longer, fuel-intensive journeys for scrap bound for rural shredders, and a one-way migration of recycling-related jobs away from America’s largest cities.
Get curated news on YOUR industry.
Enter your email to receive our newsletters.
Latest from Recycling Today
- Enfinite forms Hazardous & Specialty Waste Management Council
- Combined DRS, EPR legislation introduced in Rhode Island
- Eureka Recycling starts up newly upgraded MRF
- Reconomy Close the Gap campaign highlights need for circularity
- Nickel carbonate added to Aqua Metals’ portfolio
- EuRIC, FEAD say End-Of-Life Vehicle Regulation presents opportunity for recyclers
- Recyclers likely to feel effects of US-China trade war
- BCMRC 2025 session preview: Navigating battery recycling legislation and regulations