Belgium-based Group Galloo has installed a new 2000 Series equilibrium crane from E-Crane, also of Belgium, at its Van Heyghen Recycling yard in Ghent, Belgium. This marks the third E-Crane installation at this location and the seventh at company’s overall scrap handling operations, with sites in Belgium and France and at the Çolakoglu Metalurji steel mill in Turkey.
Group Galloo reports that its new 2000 Series E-Crane has greatly reduced operating time and costs associated with loading scrap metals into Handymax vessels at its Van Heyghen location as well as those costs related to receiving, handling and stocking scrap in the yard.
The 2000 Series E-Crane has a lifting capacity of 30 metric tons in grab mode (and of 40 metric tons in hook mode) and a reach of 38.2 meters, or roughly 125 feet. The parallelogram design of the E-Crane is engineered to provide balance throughout its full working range and to provide significant energy savings and lower operating costs, the equipment manufacturer says. Group Galloo’s newest E-Crane is mounted on a high gantry and is designed for curved rails.
Other specially designed features include a moveable cab for increased operator visibility, a camera system for the 12-cubic-meter grab and a matching quick-change system.
On-site testing and tuning were completed in October 2009, followed by comprehensive training for operators and maintenance staff.
The E-Crane can stockpile scrap to a height of more than 25 meters, or 82 feet, according to E-Crane. This allows the operator to ensure that Handymax ships accommodating 30,000 to 40,000 DWT (dead-weight tonnage) can be loaded easily without bringing up extra scrap during the loading process.
Additionally, the E-Crane handles scrap brought in and dumped by trucks as well as larger quantities brought in by barges and other vessels. During the unloading of the first barges to arrive at the yard after the E-Crane was installed, it was clear that the process took only half the time of the previous equipment, according to Group Galloo.
The company says it also has seen improved efficiency when loading outgoing vessels with processed scrap. For example, the new E-Crane has been loading intercoastal vessels at 1,000 tons per hour.
COMING IN HANDY
But the ultimate test of Group Galloo’s new material handler would be loading the first Handymax vessel. These ships have five holds, four deck cranes and a typical length of 180 to 200 meters, or 590 to 656 feet. Handymax and smaller Handysize ships are commonly used for dry bulk ocean transport. Although a Handymax bulk carrier is smaller than a Panamax (50,000 to 80,000 DWT), loading and unloading these ships presents challenges that require crane versatility.
The first Handymax the new E-Crane loaded was the “Monica P.,” a ship that is 31 meters (102 feet) wide, 190 meters (623 feet) long and has a load capacity of 46,000 tons. Once the ship was moored, at about 7 a.m. on a Thursday, the loading began. Two mobile harbor cranes also were used to assure maximum efficiency. The E-Crane loaded the smallest and most difficult first hold at what was called a record pace and then was employed to load the second hold by approximately 11 a.m., according to Group Galloo. The overall performance of the E-Crane was so quick and efficient that only one harbor crane was used on Friday, according to the company. At about 6 a.m. Saturday, the “Monica P.” set sail with 35,000 tons of scrap that had been loaded in 48 hours.
A COMPLEMENTARY SET
The installation of the new 2000 series E-Crane at Ghent complements Group Galloo’s seven E-Cranes employed at four different locations:
- • At Galloo’s Halliun, France, and Brugge, Belgium, yards, scrap is off- loaded from trucks and fed into a shear. The cut scrap is then loaded into small ships using a 700 Series E-Crane model 6317 on crawlers (operational since 2000) at the Hallium yard or a 1000 Series E-Crane model 7317 high gantry on rails (operational since 2005) at Galloo’s Denolf Recycling in Brugge.
- On the quay at Van Heyghen in Ghent, the new 2000 Series E-Crane unloads the ships from Brugge and Halliun. The scrap is then stockpiled by a 1000 Series E-Crane model 7317-GAE as well as a 2000 Series E-Crane model 21382-GAE.
- Subsequently, in Ghent the scrap is loaded into Handymax ships by the new 2000 Series E-Crane.
- The “Monica P.” sailed to her final destination at the Çolakoglu Metalurji steel mill in Turkey, where a 1500 Series E-Crane type 9317-GAE, in operation at the site since 2005, unloaded the scrap into scrap baskets for transport to the mill.
The number and diversity of E-Cranes used throughout the scrap recycling process at Group Galloo demonstrate the versatility and flexibility these machines can provide to clients worldwide, according to E-Crane. The company’s modular design allows E-Crane’s engineers to tailor custom solutions to meet customer needs based on proven core components, the company adds.
Five different machine series are available based on capacity requirements: 700, 1000, 1500, 2000 and 3000. Within each series are models with different boom and stick configurations to suit various reach requirements. E-Cranes’ hydraulically pivoting, mechanically linked boom design is engineering to keep the machine in near perfect balance throughout its working range. Having gravity work for you instead of against you reduces horsepower requirements and power consumption up to 50 percent, according to the company.
KEEPING THE DUST DOWN |
Dust Control Technology, Peoria, Ill., has announced a strategic collaboration with SMI Evaporative Solutions, Midland, Mich., to apply computer-controlled automation to monitor and manage dust suppression equipment. Users of DustBoss equipment featuring this technology can automatically adjust elevation, oscillation range and other features to improve suppression performance and free up manpower for other tasks, say the companies. “Our dust suppression team has a unique understanding of material flow and fugitive particle control issues,” says Dust Control Technology CEO Edwin Peterson. “With SMI’s engineering and manufacturing expertise, we’ve created a perfect strategic partnership to further advance the science of dust suppression.” SMI President Joe VanderKelen says the new technology can help customers improve suppression efficiency and control labor costs. Designed to deliver greater control and efficiency to dust management systems in bulk material handling operations, the systems give users the capability to track wind direction, speed, temperature, humidity and visible emissions data. The automated networks can be programmed to factor any or all of those elements and determine which combination of conditions will trigger specific system responses, according to Dust Control Technology and SMI. More information is available at www.dustboss.com. |
This text was submitted on behalf of E-Crane International USA Inc. (www.ecrane-usa.com), Galion, Ohio. More information is available from Mark Osborne at mark.osborne@ecrane-usa.com.
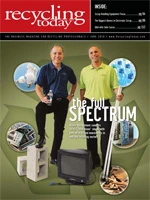
Explore the June 2010 Issue
Check out more from this issue and find your next story to read.
Latest from Recycling Today
- IDTechEx sees electric-powered construction equipment growth
- Global steel output recedes in November
- Fitch Ratings sees reasons for steel optimism in 2025
- P+PB adds new board members
- BlueScope, BHP & Rio Tinto select site for electric smelting furnace pilot plant
- Magnomer joins Canada Plastics Pact
- Out of touch with reality
- Electra names new CFO