Shredder Fluff Facility Nears Groundbreaking
A group of companies that seeks to extract additional value from auto shredder fluff has decided to build a processing site in Fond Du Lac, Wis.
The companies involved in the project include Green EnviroTech Corp. (GET) of Fond Du Lac; the German company SiCon GmbH, which will use its system to process the material; Sadoff Iron & Metal Co. of Fond Du Lac, a scrap recycler who will supply shredder fluff to the facility; and Plas2fuel of Tigard, Ore., a plastics-into-fuel technology provider.
The GET recycling process begins with ASR (auto shredder residue). The residue is separated into four material streams: mixed plastics, rubber, metals and all other remaining non-specific materials. The automated separation of shredder residue is a mechanical process developed by GET’s strategic partner, SiCon Gmbh.
Plans call for the project to handle up to 100,000 tons of ASR per year.
In an article in Recycling Today published in August 2009, Heiner Guschall, SiCon’s managing director, says the company has three VW-SiCon systems operating in Europe with a total annual capacity of 200,000 tons. “A fourth plant is currently under construction in Slovakia, and a fifth plant will be started up in the second quarter of 2010,” Guschall says, adding that three more plants are in the engineering phase.
SiCon’s VW-SiCon system can recover 80 percent of the ASR, Guschall says. “It is a key feature of our process that we produce products which are marketable and which have a positive value.”
The process involves multiple steps, including extracting ferrous and nonferrous metals from the ASR. From there, the fluff will be separated into three piles: plastics, fiber and sand. The plastics will be processed, with some material going back into the manufacturing of other plastic products, while another portion will go toward the production of synthetic fuels. The fiber and sand will be sent to a landfill.
GET processes the plastic/rubber stream using a technology it calls Plasti-Stract, removing any contaminants from the plastics using a single-step process, including a combination of two liquefied gases under pressure.
Once cleaned of contaminants, the plastic separation process begins. The mix of plastic and rubber is separated into three streams—polypropylene/polyethylene, ABS/high-impact polystyrene and mixed plastics and rubber—using “sink/float” technology developed by SiCon. During this step, each plastic type to be recovered and recycled is separated into its own “family” of plastic, according to the company. The separated streams are then sent through a metal detector and into a rail car or bulk truck ready for market.
The remaining mix of resins and rubber will then be sent to Plas2Fuel, which will use a process to convert the mix to synthetic oil. The process converts eight pounds of the mix into one gallon of synthetic oil, the company says.
GET’s process does not use any water, so the plant will not generate any effluent, according to the company.
Norb Geiss, the U.S. representative for SiCon, says that while the ASR sorting system has been used throughout Europe, this is the first installation of its kind in the United States.
Newell Recycling Opens New Facility in Columbus, Ga.
Newell Recycling LLC, based in Atlanta, has opened a metal recycling transfer facility in Columbus, Ga. The newest facility is situated on seven acres and features a 1,000-foot rail spur connecting the yard to Norfolk Southern.
The company cites the challenges facing the metal recycling business in the Columbus area as the key reason for opening the plant.
Newell Recycling designed the new facility to provide its suppliers in the Columbus area with a cost-effective transportation option. The company’s customers will now have the ability to send their scrap metal by rail to Newell’s large processing facilities in Atlanta and Savannah, Ga.
“In addition to leveraging our existing customer base in Columbus, we chose to locate a facility in Columbus because of the strategic geographical location and the strong work ethic of the Columbus residents,” says Bobby Triesch, vice president of ferrous operations at Newell Recycling. “We are grateful for the support we have received from the economic development department at the Greater Columbus Georgia Chamber of Commerce and the Columbus Consolidated Government.
Newell Recycling is investing $2 million in the new facility.
“Economic development growth comes from existing companies and new businesses like this announcement from Newell Recycling,” Mike Gaymon, president and CEO of the Greater Columbus Georgia Chamber of Commerce, says. “It also puts a new business into Columbus’ Enterprise Zone, which was designed to help stimulate economic growth. It is great to start the new year with this announcement. All new jobs are important to keep our region growing. Small business is big business to our Chamber.”
Two Colleges Establish Metals Recycling Research Center
The Worcester Polytechnic Institute (WPI), Worcester, Mass., and the Colorado School of Mines, Golden, Colo., have jointly received a $400,000 award from the National Science Foundation to establish a research center for metals recycling.
The two colleges will create the Center for Resource Recovery and Recycling (CR3), which, they say, is the first research center dedicated to developing new technologies for maximizing the recovery and recycling of metals used in manufactured products and structures.
The award will help fund the cost of establishing the center and recruiting corporate members. The possible members could include scrap yards, municipal waste centers, shredding companies, smelters, foundries and manufacturers.
According to Diran Apelian, Howmet professor of mechanical engineering at WPI and director of its Metal Processing Institute, the center will seek 30 to 40 members, each initially paying $30,000 per year, bringing the potential funding for the center to more than $6 million during the course of the grant. Apelian will serve as the center’s director, and WPI will be the lead institution.
Brajendra Mishra, professor and associate director of the Advanced Coatings and Surface Engineering Laboratory and the Kroll Institute for Extractive Metallurgy at Colorado School of Mines, will serve as associate director.
“Despite growing efforts to recycle metals, we still fail to recover half of the post-consumer metal scrap generated in this country; we rely on primary metals—those derived directly from ores—to fulfill two-thirds of our manufacturing needs,” Apelian says. “The environmental benefits of reusing scrap instead of smelting primary metal are tremendous.”
Faculty and students associated with CR3 will collaborate with industry partners to conduct research leading to advances in recycling and recovery technology that maximize the capture and reuse of post-consumer scrap and minimize the production of manufacturing scrap. These include sensors, controls and sorting technologies that can identify valuable metals and separate them from the waste stream, as well as new alloys that are easier to recycle.
WPI will focus its research on metals used in structural applications, such as steel used in buildings and aluminum forged for automotive components. The Colorado School of Mines will focus its energies on metals used in what it calls functional applications, including high-value and rare-earth metals used in computers, electronics and photovoltaics.
“Our nation’s economic health is intimately intertwined with our ability to conserve natural resources, including inorganic materials, which are not renewable,” says Apelian. “The issue of sustainability should be paramount in how we design, manufacture, use and retire the many products we use. That is the motivation for this new center’s research and its partnership with industry.”
Members of CR3 will help determine the direction of and benefit from the center’s research and will have royalty-free rights to intellectual property resulting from that research. Board members also will have the option of sponsoring supplementary research projects for additional fees. Members will have representation on the center’s Industrial Advisory Board, which will meet twice per year.
River Metals Recycling Opens New Facility in Cincinnati
River Metals Recycling (RMR), based in Crescent Springs, Ky., has officially opened its newest feeder yard in Cincinnati. The company says the yard sits on approximately eight acres.
The facility will accept ferrous and nonferrous metals. Metals purchased will be sorted on site and then transferred to RMR’s Newport, Ky., facility.
RMR, a wholly owned subsidiary of David J. Joseph Co., says the new yard adheres to all city, county, state and federal environmental laws and rules. Existing buildings at the site were renovated, a truck scale was installed and an unmanned payment station was erected.
This new yard brings RMR’s total number of processing and feeder yards to 10. The company now operates yards in Henderson, Louisville, Newport, Owensboro, Paducah, and Somerset, Ky.; Metropolis, Ill.; Greensburg, Ind.; and Xenia and Cincinnati, Ohio.
ISRI Sets Up Police, Scrap Industry Cooperation
The Institute of Scrap Recycling Industries Inc. (ISRI), Washington, D.C., has been taking measures to convince law enforcement agencies that it takes the problem of metals theft seriously.
At a joint meeting of two of its regional chapters in January, ISRI Director of Metal Theft Prevention Gary Bush provided an overview of programs created by the organization.
Bush, who is also ISRI’s national law enforcement liaison, served as a detective and patrol officer in Florida, where he still lives. He addressed a group of more than 50 people that consisted of scrap company owners and managers as well as law enforcement officers from Ohio and Pennsylvania.
The Metal Theft Symposium at which Bush spoke took place before a joint meeting of the Northern Ohio and Pittsburgh Chapters of ISRI near Sharon, Pa.
Part of Bush’s presentation focused on the www.ScrapTheftAlert.com Web site and the notices and bulletins stemming from that site.
According to Bush, the Web site started in December of 2008 and in January of 2009 had an initial group of 47 law officers registered. As of late January 2010, Bush said, there were 1,100 law officers among the site’s 6,000 total registered users.
One of the system’s functions is to allow law officers and scrap dealers to create “alerts” for stolen material that can be broadcast e-mailed to ISRI members and other registered scrap dealers within a 100-mile radius. Bush said nearly 650 such alerts were broadcast in 2009.
Bush urged those in attendance to continue to build good relationships and open lines of communication between the scrap industry and local law enforcement agencies.
Aleris Files Plan of Reorganization
Aleris International, based in Beachwood, Ohio, has announced that it has filed a proposed Plan of Reorganization and a related draft disclosure statement in U.S. Bankruptcy Court in Delaware. With the filing, Aleris and its wholly owned U.S. subsidiaries co-debtors are positioned to emerge from Chapter 11 protection by the middle of this year, according to a press release issued by the company.
“The filing of the Plan of Reorganization with this level of creditor support represents a major milestone in our ongoing efforts to position Aleris to emerge from Chapter 11 with financial stability and an operationally sound and competitive foundation for the long term,” says Steven Demetriou, Aleris chairman and CEO. “Since our filing last February, we have made significant improvements to our operations worldwide, reducing overhead, manufacturing costs and global head count as well as achieving significant productivity and customer service improvements.
“When Aleris emerges from Chapter 11, we will have eliminated all of our term loan and unsecured debt and will have a strong balance sheet, significantly reduced operating costs and greater financial flexibility,” Demetriou continues. “The strong financial support and equity ownership commitment from the Backstop Parties demonstrate confidence in Aleris’s future.”
The U.S. Bankruptcy Court in Delaware has set the hearing to consider approval of the Disclosure Statement for March 12.
To facilitate the global restructuring of all of the debt on the company’s balance sheet, Aleris also says it has filed a voluntary petition for relief under Chapter 11 as well as a Plan of Reorganization for its German holding company subsidiary, Aleris Deutschland Holding GmbH.
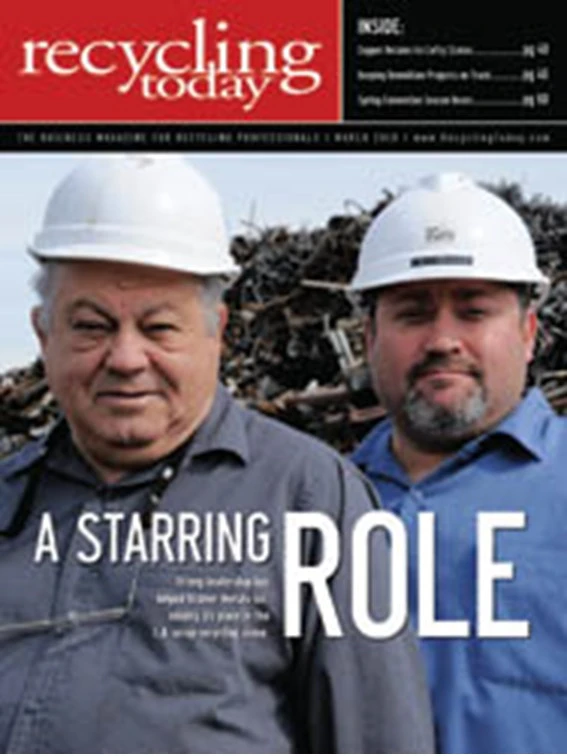
Explore the March 2010 Issue
Check out more from this issue and find your next story to read.
Latest from Recycling Today
- WM of Pennsylvania awarded RNG vehicle funding
- Nucor receives West Virginia funding assist
- Ferrous market ends 2024 in familiar rut
- Aqua Metals secures $1.5M loan, reports operational strides
- AF&PA urges veto of NY bill
- Aluminum Association includes recycling among 2025 policy priorities
- AISI applauds waterways spending bill
- Lux Research questions hydrogen’s transportation role