Schnitzer Steel Reports Quarterly Loss
Schnitzer Steel Industries Inc., Portland, Ore., has reported a net loss of $34 million, or $1.21 per diluted share, for the first quarter of fiscal year 2009 ended Nov. 30, 2008. The company reported a pre-tax operating loss of $50 million, including non-cash inventory write-downs of $52 million.
"During the first quarter we faced difficult market conditions, including an unprecedented drop in demand for recycled metals and finished steel products," Schnitzer President and CEO Tamara Lundgren says. "The weak economic environment and the worldwide financial crisis resulted in a rapid and precipitous drop in both sales volumes and sales prices from those experienced in the previous quarter in all of our businesses."
Lundgren says Schnitzer took actions to adjust its costs and production to meet the lower demand, including reducing full-time employees by 10 percent.
She adds, "We also reacted quickly to reduce our purchase costs for raw materials, allowing us to maintain positive cash metal spreads. Our lower production output will allow us to match our inventory with levels appropriate for the current market conditions."
Revenue for the company’s metals recycling business declined 66 percent from the record revenue posted in the fourth quarter of fiscal 2008. The decline reflected the collapse in demand for recycled metals related to the worldwide economic and financial crisis that began during the quarter.
Average net ferrous sales prices fell 42 percent, and ferrous volumes fell 48 percent, quarter over quarter. Nonferrous volumes and prices also were lower. Compared to the first quarter of fiscal 2008, revenue declined 17 percent as lower ferrous sales volumes and nonferrous sales prices more than offset higher average net ferrous sales prices and higher nonferrous volumes.
Net sales prices declined throughout the first quarter, with average net ferrous prices during November approximately 40 percent less than the quarterly average. Average prices during the quarter were affected by a number of shipments scheduled for November that were cancelled by customers and resold at lower prices than originally contracted.
The lower ferrous sales volumes were driven by lower demand for raw materials used in steel production. In addition, quarterly sales volumes also were affected by deferrals and cancellations of customer contracts. The $19 million operating loss for Q4 included the impact of contract cancellations that occurred in November as well as a non-cash inventory write-down of $29 million.
Schnitzer also saw revenue for its auto parts business decline 35 percent compared to the record revenue reported in the fourth quarter of fiscal 2008, reflecting the significant decline in demand and pricing for recycled metals. Compared to the first quarter of fiscal 2008, revenue declined 7 percent, as lower prices for cores and scrapped vehicles, lower sales volumes and lower full-service parts sales offset a slight increase in self-service parts sales.
Revenue for Schnitzer’s steel manufacturing business declined 46 percent compared to the fourth quarter of 2008 in light of weakened demand. Sales volumes dropped 46 percent to 98,000 tons, and sales prices fell 10 percent to $864 per ton. Compared to the first quarter of fiscal 2008, revenue declined 10 percent, as a 44 percent drop in sales volumes more than offset a 44 percent increase in average sales prices.
Horsehead Breaks Ground on S.C. Plant
Horsehead Corp., a subsidiary of Horse-head Holding Corp., has announced that it has broken ground on its project in Barnwell County, S.C.
The facility, when complete, will recycle electric arc furnace dust, a material that contains zinc, produced by electric arc furnace. At full capacity the facility is projected to handle around 180,000 tons per year.
The plant, which will consist of two units, is expected to be completed by mid-2009. It is the first greenfield project for Horsehead.
The company, based in Monaca, Pa., operates six facilities throughout the United States.
Iowa Company Looks to Add Second Scrap Yard in State
A-Line Iron and Metal, Waterloo, Iowa, has announced plans to add a second location in the state.
Kyle Stone, owner of A-Line, has purchased land in Cedar Rapids, Iowa, where he wants to build a scrap yard from the ground up. The site is nearly 70 miles from the company’s original yard.
While the proposed site is in an area of the city zoned for industry, opposition is threatening to halt the expansion of the company. According to one local report, two area radio stations have aired a number of commentaries protesting the project. The stations, KZIA and KGYM, would border the new scrap yard and have aired public service announcements presenting the drawbacks of having such a facility adjacent to their property.
The yard has plans to include fencing and landscaping to screen the operation from the public as well as a large building and a metal storage facility.
If the city approves the plan, Stone plans to break ground this spring, with the facility opening by June of 2009.
Aluminum Association Announces Recycling Target
The Aluminum Association has announced an industry-wide effort to increase the recycling rate for used aluminum beverage containers to 75 percent by 2015. Presently the aluminum industry recovers about 54 percent of the aluminum containers produced in the United States.
Martha Finn Brooks, president and COO of Novelis Inc., describes the recycling goal as "a vital leadership initiative for the aluminum industry."
"It is time," says Brooks, "that we aggressively advance a multi-tiered approach and work with other stakeholders to achieve higher recycling rates. This metal is too valuable, from both an economic and environmental point of view, not to recover."
To achieve the recycling target, the Aluminum Association will work in partnership with other stakeholders to increase public education, grow the recycling infrastructure and explore new policy initiatives. The association will encourage and assist local and state governments to consider a range of options, including growing and strengthening voluntary recycling programs, such as curbside recycling initiatives; considering deposit legislation as an option for all beverage containers; exploring the role mandatory recycling programs and landfill bans can play as part of the solution; and recognizing the benefits of recycling in any potential climate change policies.
The U.S. aluminum industry’s recycling rate peaked at 68 percent in 1992, but declined to as low as 50 percent in subsequent years. More recently the recycling rate has gradually increased, growing by 2.2 percentage points in 2007.
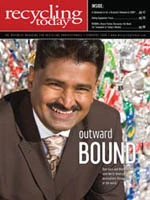
Explore the February 2009 Issue
Check out more from this issue and find your next story to read.
Latest from Recycling Today
- AF&PA report shows decrease in packaging paper shipments
- GreenMantra names new CEO
- Agilyx says Styrenyx technology reduces carbon footprint in styrene production
- SABIC’s Trucircle PE used for greenhouse roofing
- Hydro to add wire rod casthouse in Norway
- Hindalco to invest in copper, aluminum business in India
- Recycled steel price crosses $500 per ton threshold
- Smithers report looks at PCR plastic’s near-term prospects