A number of market factors make materials such as DRI more significant feedstocks for steelmaking than ever before, and scrap processors are taking notice.
It’s been said that change is the only constant. This holds true for the recycling industry, which has benefitted from changes such as the advent of the electric arc furnace, and suffered through others such as increased regulatory pressures. Now the industry faces the increased demand for scrap alternatives like direct-reduced iron and pig iron which, although they have been used in steelmaking for many years, have only recently become significant contenders.
Some scrap processors view this trend as a market opportunity. Both the Australian Simsmetal Pty Ltd. — a large scrap metal processor and broker — and Minneapolis-based North Star Steel Co. — which owns its own scrap yards — are reportedly interested in some degree of involvement in DRI or iron carbide facilities. Another scrap veteran, Columbia Iron & Metal Co., Cleveland, has taken the lead in research and development of products from DRI by-products.
Whether the average scrap processor will have to get directly involved with materials such as DRI in order to remain competitive is debatable. But one East Coast market analyst speculates that scrap processors who are open to change and to the advent of new materials such as DRI are more likely to be successful in the future.
DRI EXPLOSION.
The use of DRI is "exploding" in the U.S., says Gerald Houck, iron and steel specialist for the U.S. Bureau of Mines, Washington, because of the high price of scrap and the forays the electric furnace steel producers are making into more demanding steel products requiring lower levels of residuals. There isn’t enough suitable scrap to make all of these products, he adds."You have to look in total at what scrap is available to you and use it in the best way, and what mills are finding is it’s helpful to have a supply of direct-reduced iron in one form or another to make these products."
Other factors behind the steel mills’ interest in scrap complements include changes in process technology, equipment technology and environmental technology; potential scrap shortages; freight costs and world trade tariffs, adds Jim Braselton, vice president of Columbia Trading, a division of Columbia Iron & Metal, Cleveland.
"So many things drive the mills," says Braselton. "The factors just keep building."
Integrated mills are interested in these products for some of the same reasons as electric furnace operators, adds John Jacobson, president of Jacobson & Associates, a steel industry research firm in Swarthmore, Pa. "There’s lots of reasons producers of all ilk are going to be looking at and utilizing scrap supplements," he explains. "One is the reliability of the product. I think for many grades of scrap there’s been an increased concern around potential contaminants. What we’re seeing is a classic example of customers — the buyers of steel — demanding quality and the steelmakers are responding as best they can."
Jacobson defines quality broadly as the ability to deliver the type of product the customer is looking for.
"That’s one of the biggest benefits of the iron-based products (scrap complements) — the producers have a much better handle on what the metallurgical properties of the steel will be," says Jacobson. "I see more customers looking for more pure products."
The acceleration in demand for steel is another driver in the push for higher quality products, says Jacobson, as is the globally competitive nature of the steel industry. But the customer is the biggest force in this trend.
Not all steelmakers, however, are convinced that DRI and related materials are necessary for their success.
"We’re watching it carefully, obviously, as it has an impact on our scrap business," says Bob Philips, president, Schnitzer Steel, Portland, Ore. "We brought in some pig iron, but not iron carbide or DRI, and right now we don’t have any plans to invest in DRI facilities."
Schnitzer has less need for low-residual scrap than a company that is producing flat-rolled products, Philips adds. But all the mills are watching the markets carefully and considering the use of scrap complements, he says.
"They’re all looking at it in the regard that if scrap is short they need to figure out how to keep their furnaces going," he says. "For some people it might be cost effective, for us it’s not."
EVOLUTION.
Although DRI has been produced for years, the market is changing rapidly. Until recently, DRI was produced using processes and facilities supplied by a very few companies. Now, new processes are emerging to compete with the established ones.One of these is the iron carbide process, pioneered by Nucor Corp., Charlotte, N.C. Nucor recently completed the first iron carbide plant in Trinidad, which is scheduled to be fully operational early in 1995.
There was a great deal of activity in the scrap complements field until Nucor announced their Trinidad iron carbide facility, says Houck. At that point, many people backed off and are waiting to see how this plant works.
"If that is as successful as the Nucor people think it will be, then the people that are interested in building DRI plants could very easily adopt that technology rather than one of the others," says Houck. "It’s potentially cheaper for two or three reasons. First, the material doesn’t need to be briquetted. Second, it uses a cheaper form of iron ore. And it’s claimed that it offers certain advantages in the actual melting process. The other side of the coin is it takes more energy, so it’s slightly more costly from an energy point of view."
Although the majority of the iron carbide produced by the Nucor plant will be used by the company’s own facilities, Nucor has already sold some of it to other companies, according to LeRoy Pritchard, manager of new steel technology for Nucor.
"We’re going to take a small portion of it and market it, just to whet people’s appetites for the material," he says. "And if this meets the expectations we’re placing on it, we’ll probably start the next modules next year."
An iron carbide plant such as Nucor’s requires a capital investment of $60 to $75 million, says Pritchard. He speculates that a large scrap processor could conceivably make such an investment.
"If you’ve got a large scale scrap processor that’s got an asset base and credits lines and so on, there wouldn’t be any reason why he couldn’t," he says. "I haven’t seen many scrap processors investing in these technologies yet, but they keep flirting around out there. It wouldn’t surprise me if it happened one of these days. Especially with iron carbide, as the cost of getting into an iron carbide facility is less than any of the other alternatives. So if it proves to be as attractive as we think it is, you may find other people showing interest in it."
But the need for scrap is constant and will remain so, Pritchard adds, as is the need for DRI. "Scrap is not going to go away. As a consuming society, we’re going to continue to generate scrap, and there is also going to continually be a sweetener requirement if you are a scrap-based producer. I think iron carbide is going to have a place for people who want to get into the high-quality steel."
PIG IRON. Along with various forms of DRI, there has been a recent resurgence in the use of pig iron as a complement to the scrap charge in electric furnaces, according to Houck.
"It’s more pure than scrap. It has the same beneficial characteristics that the DRI has. Pig iron has traditionally been more expensive than scrap, but when scrap gets to a certain level, pig iron tends to come out and prevent scrap prices from getting too high," he says.
The quantities of pig iron being used now are actually greater than those of DRI, Houck points out. "Imports for pig iron were 1.957 million metric tons for the first nine months of 1994, whereas imports of DRI were 727,000 metric tons during the same period."
For comparison, he adds, imports of pig iron for 1993 were 828,000 tons for 1993 and 427,000 tons for 1992. DRI imports have also increased significantly over the same period. In 1991, imports of DRI totalled 365,000 metric tons. In 1992 that number increased to 542,000 tons and leaped even further to 900,000 metric tons in 1993.
"I think in terms of the substitution or complementing to scrap in electric furnace melting, pig iron is a much bigger story than DRI this year, " says Houck. "And we will see more of this if the market stays as it is. Electric furnace melters would probably prefer DRI to pig iron, as it may be a little easier to handle. But they’ll use either. There’s an availability problem with DRI — there just isn’t that much out there."
INNOVATION. One forward-looking scrap processor, Columbia Iron & Metal, Cleveland, is involved in the briquetting and marketing DRI fines, a by-product of DRI. Although the company is investigating products for all types of steelmaking applications, the existing product is mainly used by blast furnaces, according to Columbia’s Mark Heuschkel.
"This is due to the chemical properties of the product," explains Heuschkel.
Columbia’s product is relatively new to the U.S. market, but it is rapidly gaining in popularity.
"There’s a definite wave of awareness of this product," says Ronald Bone, president of Columbia Iron & Metal. "In the last six months we’ve seen a lot more interest. It hasn’t been just a result of marketing on our part, it’s also been a result of mills talking to each other about the benefits of using alternative products."
In order to meet the changing needs of the steel industry, scrap processors may increasingly want to diversify into other iron-based products, says Bone.
"I think that there are going to be a lot of motivators to people who want to be as successful in the future as they’ve been in the past," he says. "People who start to modify will have more of an edge in the future."
This holds true for the steel industry as well as the scrap industry, as there are steel producers that are not yet interested in using scrap complements.
"We’ve talked to some people that are very enthusiastic about these products, other people are less receptive about using them in their furnace," says Bone. "Do they change as time goes on? I think so. I think the steel industry is like ourselves. They realize that to be successful in the future they have to look at quality, technical applications, what’s going to happen with the scrap market. It’s a commodity market — supply and demand dictate what takes place. All we’re trying to do is to fit in in a different way to these needs that are ever changing from the steel side."
The product offered by Columbia has benefitted from the increased use of scrap complements such as DRI, says Bone.
"As that became a more accepted product, there were shortages," he explains. "That was an opportunity for this product to come in. Though it’s not the same, it’s similar. It’s more easily available, and so it takes the pressure off the HBI and DRI."
In fact, HBI production for 1995 is sold out for the whole year, according to Heuschkel.
GROWTH.
The outlook for scrap complements is likely to be one of significant growth, says Jacobson. "Of the two major factors affecting the use of DRI, the drive for quality is never ending. The price consideration will be very volatile — it will be up and down. At this point in time, both factors are at full throttle — quality demands are up and price is way up. It will ebb and flow a little bit depending on the price of scrap, but the trend is for tremendous growth."Although he admits that iron-based products do compete with scrap to some extent, Jacobson says they need not be viewed as a threat to the scrap industry.
"There is a tremendous reservoir of scrap, and the country and most parts of the world are committed to a recycling philosophy," says Jacobson. "What we’re really going to see — and have been seeing — is a reduction of the reliance on coke ovens and blast furnaces."
SCRAP COMPLEMENTS: A PRIMER
I
n recent years, there has been increased discussion of materials such as direct-reduced iron, hot briquetted iron and iron carbide. It’s useful to note that all these products fall under the general category of direct-reduced iron, according to Gerald Houck, iron and steel specialist for the U.S. Bureau of Mines, Washington."There are a variety of manufacturing processes for producing direct-reduced iron and handling it," Houck explains. For example, in response to concerns that DRI was somewhat prone to reoxidation, the material is often compacted and called hot briquetted iron. Other forms of DRI are produced differently.
"Iron carbide is a form of DRI and it’s a new technology for which there’s one plant that has just been built," says Houck. "Quite frankly, the whole world is watching because it is a technology that a lot of people consider promising. If this plant starts up and produces good product at the cost and quality that the owner of the plant thinks it’s going to, there may be some more plants built in the next couple of years."
Iron carbide is iron ore that has been reduced, like other forms of DRI, but at a lower temperature and for a longer period of time. Possible benefits of the material include its resistance to re-oxidation and the avoided cost of briquetting.
However, all the different forms of DRI are basically the same "from the standpoint of substitution for scrap," says Houck. "They enhance quality and provide iron units that are free of unwanted elements that are normally present in scrap."
DRI plants are generally sited in places such as South America and Trinidad because the price of gas to fuel the process is cheaper there, says Houck. "The big costs to produce this material are the ore, the fuel and the capital."
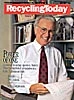
Explore the January 1995 Issue
Check out more from this issue and find your next story to read.
Latest from Recycling Today
- Haber raises $44M to expand to North America
- Canada Plastics Pact releases 2023-24 Impact Report
- Reconomy brands receive platinum ratings from EcoVadis
- Sortera Technologies ‘owning and operating’ aluminum sorting solutions
- IDTechEx sees electric-powered construction equipment growth
- Global steel output recedes in November
- Fitch Ratings sees reasons for steel optimism in 2025
- P+PB adds new board members