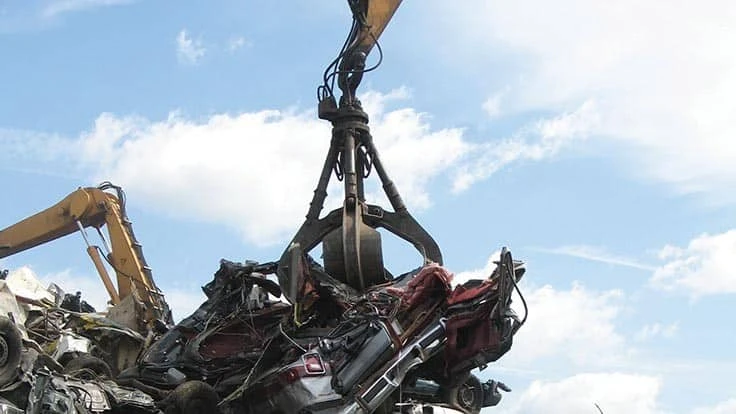

For five decades, Glen “Skip” Anthony has helped build, design, install and modify auto shredding plants in the United States and around the world. Anthony, who is currently vice president of recycling services with Illinois-based Sargent’s Equipment & Repair Service Inc., spent much of his career with St. Louis-based shredder manufacturer American Pulverizer.
In an episode of Recycling Today’s “The Scrap Show” podcast, Senior Editor Brian Taylor interviews Anthony about his career and the wider trends and changes he has witnessed (and taken part in) during his 50 years in the business. An edited excerpt from the conversation with Anthony follows.
Recycling Today (RT): In looking at the nature of how shredding plants have changed, what were some of the limitations to investing in and operating a shredding plant when you first came into the industry? How did that change over the years?
Skip Anthony (SA): Well, originally, it was mainly the larger operations that could justify putting in a shredder. And, the quantity of scrap available back then wasn’t like it is today. So, they had to have a bigger market to draw scrap from. Also, their primary concern then was to get clean ferrous scrap. The byproducts that are popular today weren’t as critical back then. So, volume meant a lot in order to produce enough material to make a profit.
There were only maybe three real manufacturers of automobile shredders then, and they were pretty dominant in that market. But, as the progression into shredding increased, some other companies started to pursue it, and, with that, it became [feasible] to be profitable without running that high volume of material.RT: So, did that change the design or the size of shredder installations later in your career?
SA: It did. One of the things that was repeated in conversations all over the country was smaller to midsize operations wanting to be able to shred. As well, they could see an increase in their profit based on the recovery of other materials, and the best way to separate and recover materials is definitely to shred. Many operators had always baled and sheared, or maybe had a niche or brought material in, processed it minimally and passed it on to the larger operations with the big shredder. The push was: Can somebody come up with a smaller shredder that we can afford to put in and run at a much lower volume and still be profitable? And I think that’s what pushed the growth of other companies into shredder manufacturing, thus also allowing other [scrap processing] companies to get into shredding.
RT: Recycling Today tries to track the shredders that are out there in the U.S., and the shredder population has certainly increased.
SA: Well, that is one thing about this industry, it never sits still. There are a lot of entrepreneurial people in it that are willing to take risks to get to a different level to find a better way to do things. So, they constantly push the manufacturers to meet those needs, and they help to make their markets grow. With the advent of several different sized shredders and different types of shredders for different materials, some more specialized shredding came about because the midsize and smaller operations were wanting to grow and be able to enjoy some of the profits that they were not receiving before.
RT: Regarding shredder maintenance, I suspect now there is a much better body of knowledge of how to maintain a shredder and how to operate it. What are your observations on that?
SA: I think that everyone has realized these are truly manufacturing systems; they’re not just a shredder or a baler. When it breaks, you fix it: The cost of being down and not producing is so great that you have to be proactive in your maintenance, in your housekeeping and in your training.What I’ve seen is a huge input into the training, the facilities, the tooling and the operations attitude to where [maintenance] is a constant part of the operation. If they maintain their equipment and do the things you do in any manufacturing process, it’s going to produce that [steel] scrap at the end of the line and the nonferrous on the other side.
RT: How has the downstream nonferrous part of the shredding process changed during your career?
SA: Well, it’s changed tremendously, and it continues to change. ... Originally, as I said, the primary goal was to clean ferrous material. Then, as eddy currents evolved, they now were able to get zorba products out of the mix. Initially, operators were happy with that, and then the commingled materials they would pick somewhat, with the rest of the material then ending up either going to another processor or to the landfill. At first, everybody went after the low-hanging fruit, but only a few dedicated companies went after hard-to-get materials.
Sponsored Content
Labor that Works
With 25 years of experience, Leadpoint delivers cost-effective workforce solutions tailored to your needs. We handle the recruiting, hiring, training, and onboarding to deliver stable, productive, and safety-focused teams. Our commitment to safety and quality ensures peace of mind with a reliable workforce that helps you achieve your goals.
Sponsored Content
Labor that Works
With 25 years of experience, Leadpoint delivers cost-effective workforce solutions tailored to your needs. We handle the recruiting, hiring, training, and onboarding to deliver stable, productive, and safety-focused teams. Our commitment to safety and quality ensures peace of mind with a reliable workforce that helps you achieve your goals.
Sponsored Content
Labor that Works
With 25 years of experience, Leadpoint delivers cost-effective workforce solutions tailored to your needs. We handle the recruiting, hiring, training, and onboarding to deliver stable, productive, and safety-focused teams. Our commitment to safety and quality ensures peace of mind with a reliable workforce that helps you achieve your goals.
Sponsored Content
Labor that Works
With 25 years of experience, Leadpoint delivers cost-effective workforce solutions tailored to your needs. We handle the recruiting, hiring, training, and onboarding to deliver stable, productive, and safety-focused teams. Our commitment to safety and quality ensures peace of mind with a reliable workforce that helps you achieve your goals.
Sponsored Content
Labor that Works
With 25 years of experience, Leadpoint delivers cost-effective workforce solutions tailored to your needs. We handle the recruiting, hiring, training, and onboarding to deliver stable, productive, and safety-focused teams. Our commitment to safety and quality ensures peace of mind with a reliable workforce that helps you achieve your goals.
Sponsored Content
Labor that Works
With 25 years of experience, Leadpoint delivers cost-effective workforce solutions tailored to your needs. We handle the recruiting, hiring, training, and onboarding to deliver stable, productive, and safety-focused teams. Our commitment to safety and quality ensures peace of mind with a reliable workforce that helps you achieve your goals.
Now, even small shredding operations in the 2,000 to 3,000 tons per month or so range are putting in equipment to try to recover every bit of material they possibly can. The return on investment on a system has increased markedly by having the ability to get these other products, and it has allowed smaller operators to be able to shred and recover material and be successful without having to have a major over-the-top investment to get there.
RT: It sounds like chasing that nonferrous and trying to wring every last bit out of it seems to usually pay off.
SA: It is amazing, because you have seen the size of the recovery plants that are being installed and the type of equipment. I mean, think back to eddy currents and the original sensor. Now you have machines that can do multiple separations. You can batch run and [undertake] multiple separations out of different materials.
RT: Downstream sorting just keeps evolving, not losing its importance.
SA: We’ve seen such a push in the automotive aluminum portion and the separation of materials using X-ray technology and optical color sorting. The materials now can be qualified for certain grades that allow it to be put into processes to make the higher quality alloys. It’s a constantly changing environment for recovering, and they keep bringing equipment in from different industries that we would have never thought of 25 years ago, from, say, the medical sector or the food industry.
Get curated news on YOUR industry.
Enter your email to receive our newsletters.
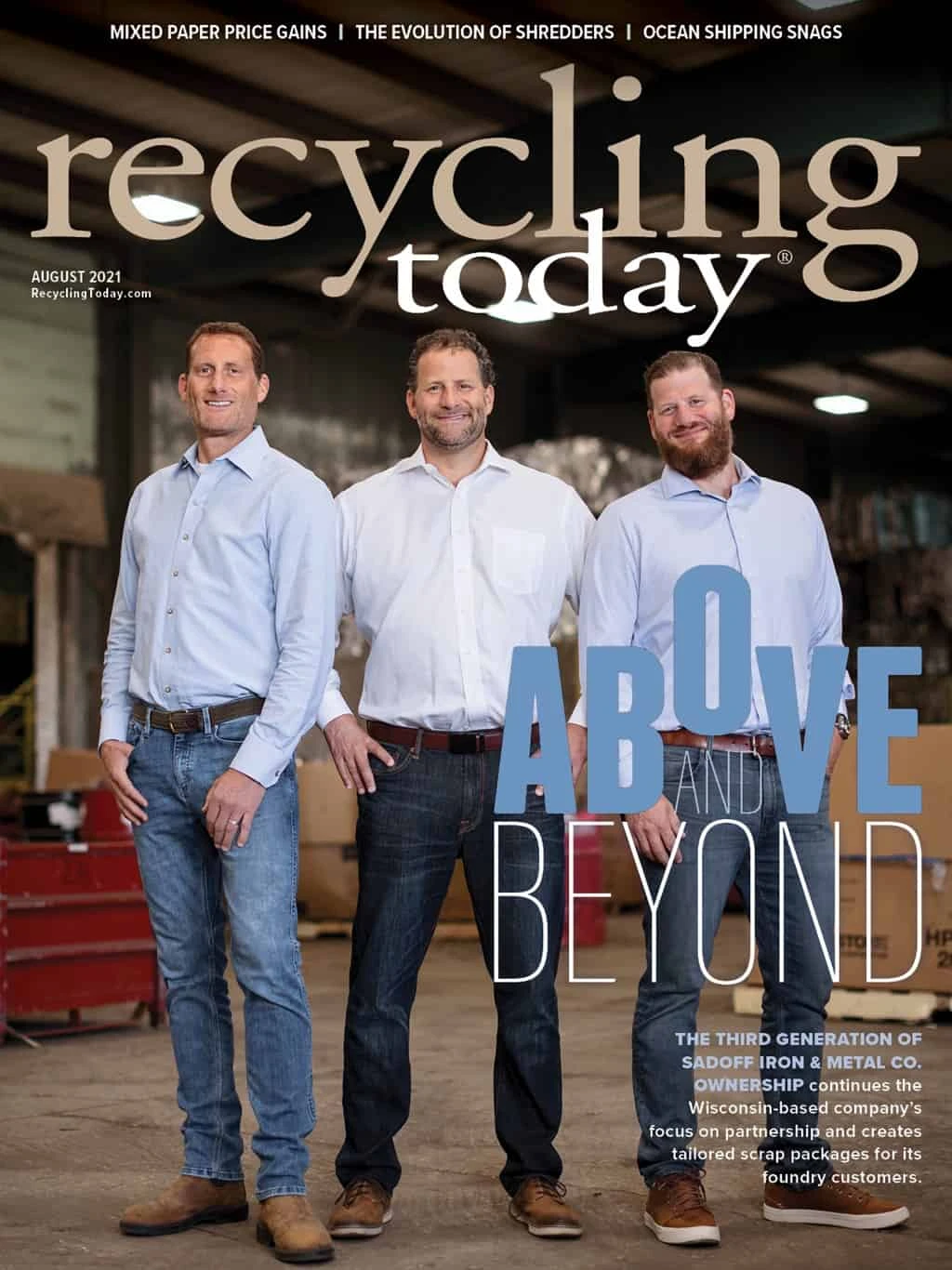
Explore the August 2021 Issue
Check out more from this issue and find your next story to read.
Latest from Recycling Today
- Green Cubes unveils forklift battery line
- Rebar association points to trade turmoil
- LumiCup offers single-use plastic alternative
- European project yields recycled-content ABS
- ICM to host colocated events in Shanghai
- Astera runs into NIMBY concerns in Colorado
- ReMA opposes European efforts seeking export restrictions for recyclables
- Fresh Perspective: Raj Bagaria