A visit to the U.S. Occupational Safety and Health Administration (OSHA) Web site
(www.osha.org) can be an alarming experience filled with many cautionary tales for employees and supervisors of material recovery facilities (MRFs). The tales come courtesy of OSHA’s accident detail reports, which outline incidents resulting in the injury or death of those employed within the scrap and waste management industry.
With incidents including an employee killed by a falling bale of cardboard, an employee who lost his thumb to a conveyor belt, an employ who died after being struck by a front-end loader and an employee who was crushed by the ram of a baler, the details can be downright grizzly. One thought prevails, however, when scanning though these accident detail reports: This accident could have been avoided.
How can MRFs emphasize safety and decrease the incidence of citations and penalties, protecting their employees and the companies’ bottom lines? One answer is regular safety training, which often begins with the facility managers and supervisors.
CONSISTENT MESSAGE. Susan Eppes and Shari Mattern are the principals behind E&M Consulting Inc., Houston. They provide safety consulting services to the recycling and solid waste industries.
Eppes says many MRF supervisors are unaware of the details behind OSHA standards. To educate both the supervisors and the employees, E&M recommends a weekly safety communications program, which consists of a 10- to 15-minute weekly safety brief that spells out OSHA’s requirements for a specific standard, the equipment that falls under that standard and suggestions for interacting with employees on the topic in question. The frequency of a safety communications program is the key to its success.
"A weekly communications program of this type has a proven track record of reducing injuries by an average of 20 percent," Mattern says. "With respect to OSHA compliance, this type of program has been well received by compliance officers from OSHA, as the program encourages weekly interaction with employees and supervisors," she says. "The weekly meetings are especially helpful as they continually put safety before your employees and most especially your temporary laborers."
CRITICAL EQUIPMENT |
Balers and conveyor belts represent two considerable hazards at material recovery facilities (MRFs). With this in mind, baler and MRF system manufacturers strive to reduce potential risks through engineering innovations and training programs. Providing users with a list of procedures for maintaining the baler is critical, says Joe Szany of Marathon Equipment Co., Vernon, Ala. "Some of those procedures are lockout/tagout provisions where you’re making sure you’re locking out the electricity that goes to the unit so that nobody accidentally turns the unit on." Guarding of moving parts is another area of concern for MRF equipment manufacturers. Erik Eenkema van Dijk of Van Dyk Baler Co., Stamford, Conn., says a steel door protects every moving part on the company’s balers. "That door is controlled by a double safety circuit," he notes. Some baler makers are offering a belt-style sensor that can be worn by a baler operator. The Safetech Bodyguard System from Sierra International Machinery Inc., Bakersfield, Calif., is billed as a "tag belt" that will trip sensors surrounding a baler if the wearer of the belt crosses the path of the sensors. If the sensors are tripped, an alarm will be triggered to activate the emergency stop procedure. Van Dyk has recently added a similar safety feature known as the BOSS (Bollegraaf Operating Safety System). The system consists of a transmitter that is mounted to the employee’s belt or sewn into his clothing. If an unconscious employee falls onto the baler’s conveyor belt, a sensor mounted above the conveyor belt would read the signal from the transmitter and automatically shut the system down. Manufacturers also conduct training sessions when installing new units. . |
Eppes and Mattern recommend establishing a weekly employee observation program, where the MRF supervisor tours the facility observing and noting employees’ behavior. "Sometimes you will catch people doing stuff that they think is right," Eppes says. "They are trying to help out because they see a piece of paper in [an inappropriate place] and they want to get the contaminant out. So, they reach over and grab it or they do something that puts them in harm’s way, meaning to clean the material. The intention was good, but it was a bad action," she says.
Eppes and Mattern also point out the importance of training every employee of a MRF about the facility’s potential dangers. "If you are a sorter, you still need to know about the tipping floor because it’s dangerous," Eppes says. "We try to get the employee familiar with the entire facility and what the other jobs are."
Eppes suggests informing material suppliers and vendors in writing of a facility’s safety policies and obtaining a signature verifying that they have received the information in question.
These steps help establish the safety culture of a MRF, and company-wide participation determines the success of a program, agrees Jimmy Lawrence of RecycleGuard, an insurance program for recyclers from Willis of Rochester, N.H.
CULTURAL FACTORS. RecycleGuard advocates a behavior-based approach to safety, which Lawrence defines as "a non-threatening, culture-based program."
Lawrence says the traditional approach to safety is to impart "heavy-handed" discipline whenever an employee violates safety protocol. "I think we realized that our workforce today doesn’t respond to that kind of threatening environment," he says, advocating instead a "peer intervention" model program.
However, the peer intervention model will not work if a company stigmatizes either the employee who corrects a fellow worker or the one being corrected. "When you have that culture where peers feel comfortable to intervene, then what you really have is their buy-in," he says. This buy-in is critical, Lawrence says, because it helps to hold employees accountable.
Eppes also finds employees are more willing to discuss the safety concerns if there is a method to do so, which is why E&M recommends the weekly safety brief. "That encourages people to ask questions and bring things to people’s attention."
Just as Mattern and Eppes do, Lawrence recommends walking though the facility making observations about behavior. "I think one of the really helpful tools, and the one that is the most telling, is to go through your workplace and make observations about behavior," he says. "I do this pictorially." Lawrence says he gathers photographs illustrating both good and bad safety behavior for use in training sessions.
Positive reinforcement is helpful in reinforcing safety training and procedures.
Lawrence says that positive reinforcement is crucial because it reinforces the employee’s buy-in. "It boils down to rudimentary human nature," he says. "If people are saying positive things to you…you respond to that. Obviously, we respond much more to that than to negativity."
A company must step back and look at its overall safety culture, says Lawrence. "If it doesn’t contain a strong behavioral approach, I don’t think [it will] win the battle against constant employee injury."
The author is associate editor of Recycling Today and can be contacted via e-mail at dtoto@RecyclingToday.com.
Get curated news on YOUR industry.
Enter your email to receive our newsletters.
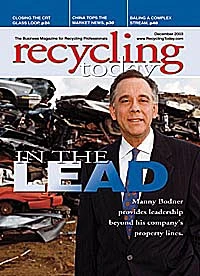
Explore the December 2003 Issue
Check out more from this issue and find your next story to read.
Latest from Recycling Today
- LumiCup offers single-use plastic alternative
- European project yields recycled-content ABS
- ICM to host colocated events in Shanghai
- Astera runs into NIMBY concerns in Colorado
- ReMA opposes European efforts seeking export restrictions for recyclables
- Fresh Perspective: Raj Bagaria
- Saica announces plans for second US site
- Update: Novelis produces first aluminum coil made fully from recycled end-of-life automotive scrap