The Institute of Scrap Recycling Industries Inc.’s (ISRI’s) approach to safety is less about how to enforce rules and regulations and more about how promote a culture of safety. Its newly revised “Safety Manual” focuses on developing a culture of safety in a way that can be tailored to any recycling company.
“A safety culture exists when your company has made the jump from managing safety because the law requires it to living safety because it has become ingrained in all aspects of your operations,” the manual states. “You know you’re on the right track when your employees practice safety even when you aren’t looking.”
ISRI Director of Safety John Gilstrap explains, “If you have a safety program that is dedicated truly to worker safety, regulatory compliance will follow.” He says a company’s safety program has to be rooted in the notion of sending people home healthy to be successful.
“Unless and until it is unacceptable to shed blood on the job—until that is the core value—a safety program will be troubled,” he says. Gilstrap says the safety pledge ISRI members are asked to sign gives safety a place at the management table equal to productivity and profitability.
SENNEBOGEN ADDRESSES SAFETY |
Constantino Lannes, president of Sennebogen LLC, Stanley, N.C., says his company has worked closely with customers in North America to understand their safety concerns when operating material handlers. “There are basically three main concerns,” says Lannes, “Operator and maintenance access as well as personnel safety when operating equipment.” The company has addressed these concerns in its design and installation of equipment, according to Lannes. He says Sennebogen modified the door cab on its material handlers from a traditional swinging door to a sliding door, which allowed it to install a catwalk on the side of the cab and to enclose it completely with handrails. When the catwalk is installed, the operator is forced to access the cab through the central steps instead of climbing on a tire, he says. To address maintenance access, Sennebogen says it installs the engine and pumps on the side of its machines, making them accessible through a large door. According to Lannes, the industry standard is to install the engine on the back of the machine. By installing it on the side, Lannes says, most of the maintenance work can be done from the ground. For the once every 2,000 hours that a mechanic needs to climb to the top of the machine for a hydraulic oil filter change, Sennebogen says it has installed handrails around the upper carriage to eliminate the risk of falling. Lannes says personal safety during operation means “not only better operator visibility but, at the same time, providing the operator with an operator’s cab that allows him to better concentrate on his work.” |
A NEW APPROACH
The “Safety Manual” is not intended to be adopted as a company’s safety policy, according to Gilstrap, because “no one document can be all things to all people.” He says it is instead intended to be a tool. The first part of the 169-page manual is what Gilstrap describes as an interactive “cook book” approach to help companies develop effective safety programs.
The second part of the manual is devoted to operating specific pieces of equipment, such as skid steers, wheel loaders, scrap handlers, shredders, crawler cranes and mobile truck cranes. It provides information on specific equipment setup, operation and shutdown procedures.
CONTINUING TO EVOLVE
Gilstrap says the “Safety Manual” will continue to evolve in time, not only to add new chapters but to add to, modify, change and remove parts of existing chapters. He says ISRI has had a safety manual since the 1980s, but he describes the earlier version as a static manual. It wasn’t until 2004 when ISRI began redesigning its safety program to be management and worker oriented that the manual was readdressed and conceived of as a developing document. The revamping of the manual began with the ISRI Safety Council, which is now the ISRI Safety and Environmental Council (ISEC). Instead of incorporating best management practices, which Gilstrap says have a legal connotation to them, ISEC has developed and incorporated what it calls RISPs, which stand for recommended industry safety practices, into the manual.
Working groups within the ISEC will take on individual programs, procedures and pieces of equipment and develop the elements of the safety program. Once the working group finishes its job, the information is put into the format of a RISP. Then the safety council, as a body, votes on whether to approve it. If it is approved, it will then go to the Operations Committee of the ISRI board of directors, which will vote on whether to accept the recommendation from ISEC. If the Operations Committee accepts the RISP, it then goes to the board of directors to be adopted by the association.
If the process sounds complicated, that is because it is supposed to, according to Gilstrap. “We intentionally made this process complicated,” he says. “What comes through on the other end is going to affect the entire industry, so we want to make sure it is looked at by as many eyes as possible.”
ISEC meets twice yearly and the “Safety Manual,” according to Gilstrap, is always on the agenda.
Another of ISRI’s goals in developing and updating the manual is to get people who are actually working in the recycling industry to have a say in what is in it.
“It is one thing to sit in Washington at the 40,000-foot-level and say, ‘This is what you should do.’ But we also think that it is just a much healthier document if it comes from people who are going to be implementing it,” Gilstrap says.
Jerry Sjogren, safety director of E.L. Harvey & Sons, Westborough, Mass., and past safety chairman for ISRI, was part of the initial group of people that Gilstrap called together six years ago to develop the new manual. At the time, Sjogren says, “We all identified that there were a lot of small companies, mom and pop outfits, that perhaps wanted to do the right thing but weren’t sure what they needed to do. There were a lot of safety people out there that weren’t sure what they needed to have at their facilities and they weren’t sure where to find information on it.”
EVERYONE CAN BENEFIT
The manual can be accessed online at www.isrisafety.org/assets/files/ISRI_Safety_Manual_9_10.pdf. It is not exclusive to ISRI members. The safety information is available to everyone, according to Sjogren, because when someone at a scrap recycling facility gets hurt or killed, it affects the entire industry. Another reason for making the “Safety Manual” public, he adds, is so that people in the industry can recognize the value of the manual and the services that ISRI provides.
“A company that has a good safety culture is a company that has acceptable things and unacceptable things, and everybody understands that and behaves accordingly,” says Sjogren.
The “Safety Manual” has been amended as recently as September 2010, and Sjogren says it will be revised regularly as new ideas and regulations are introduced.
“There is a huge difference between compliance and just doing enough to get by versus having an actual culture where safety is a core value or a core belief,” Sjogren says. “That’s what works in safety. That’s what keeps people safe.”
The author is assistant editor of Recycling Today and can be reached at ksmith@gie.net.
THE TRAINING DIFFERENCE |
Jerry Sjogren says one of the biggest mistakes many companies make when it comes to safety is hiring a new person or reassigning a person to a different job and immediately subjecting the worker to an unfamiliar situation. The Safety Director of E.L. Harvey & Sons, Westborough, Mass., and past safety chairman of the Institute of Scrap Recycling Industries Inc. (ISRI), says he has seen some operations where there is little or no training. He says recyclers should have a training program where they show workers what to do, mentor workers and then check back with workers to ensure they understand their jobs. Sjogren admits there is a cost to having a training program but says it is money well spent. Making sure people are clear on acceptable operating distances and what is going on around the equipment are important factors to safe equipment operation, according to Sjogren. At E.L. Harvey & Sons, he says, employees are taught to communicate with one another, “making sure that the people who are on the ground are very clear with what the equipment is doing, and the equipment operator is very clear about what the person on the ground is doing.” |
Get curated news on YOUR industry.
Enter your email to receive our newsletters.
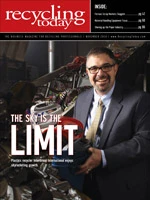
Explore the November 2010 Issue
Check out more from this issue and find your next story to read.
Latest from Recycling Today
- Radius loses money, says merger on track
- Electrostatic technology vies for role in ASR sorting
- ReMA board to consider changes to residential dual-, single-stream MRF specifications
- Trump’s ‘liberation day’ results in retaliatory tariffs
- Commentary: Waste, CPG industries must lean into data to make sustainable packaging a reality
- DPI acquires Concept Plastics Co.
- Stadler develops second Republic Services Polymer Center
- Japanese scrap can feed its EAF sector, study finds