
Mobile shears quickly became workhorses on demolition sites and at scrap yards after they were introduced to these markets in the late 1970s.
In several scrap applications, the hydraulic shear has replaced torch cutting, primarily for perceived productivity and labor-saving purposes but also for worker safety reasons.
Using a mobile shear to cut scrap steel and other recyclables, nonetheless, involves the exertion of powerful force to cut through metals designed to be strong and resistant to damage. For all shearing operations, safety should be a consideration, Terry Sturgell of Wisconsin-based ShearCore says.
Trained to maintain
At active job sites, such as scrap yards and demolition sites, undertaking maintenance tasks on mobile material handling machines and their attachments can leave a mechanic performing the work exposed to the other moving machines and trucks nearby.
For that reason, Sturgell says, ShearCore and other companies design shears to be easy to maintain and to be sturdy enough to minimize the need to perform repairs. ShearCore, part of Exodus Global, designs and makes the Fortress line of hydraulic mobile shears.
Sturgell says preventive maintenance inherently is safer than emergency repairs, in part because it can be performed in a designated area the yard or work site.
“By addressing and minimizing many of the things that can go wrong in the field, we allow for a tool to stay working longer and then have its maintenance done in a designated area,” he says. “We also make it so that when a technician does have to do maintenance in the field, it can be done in a more efficient and safe manner and be completed in a timelier manner.”
However, scrap recycling is not always a process where things go exactly to plan, Sturgell adds. “We all recognize that doing maintenance in a controlled environment is not always possible and often needs to be done in the field on a job site or in the yard.”
Wherever the work is done, a key to performing maintenance tasks quickly and effectively is training, he says. “Every job site is a bit different, so we offer on-site training for all of our customers,” Sturgell says.
“That said, there are basic things that apply to all applications, especially when it comes to maintenance, and that is why we also offer training at our factory, maintenance documentation and toolkits so that maintenance can be provided safely and effectively.”
Designing for endurance
Training operators and mechanics thoroughly is one way to increase the safety quotient at a scrap yard or a work site. Another is to design and build a shear that is less likely to experience a catastrophic failure and all the risks such an incident can entail.
Manufacturers of mobile shears compete with each other to offer products that can withstand harsh conditions and earn a reputation for avoiding downtime. Sturgell says ShearCore was well-aware of those demands when it introduced the Fortress FS145.
“We designed the FS145 with certain criteria in mind. We focused on high cutting capacity packed into a lower weight and shorter center of gravity tool,” he says of the Fortress FS145, which was introduced in 2019.
ShearCore has been marketing the FS145 to demolition contractors for high-reach applications, Sturgell says, though the model is “designed to process all types and sizes of scrap, meeting the needs of our customers, including scrap metal recycling facilities, large demolition projects, ship dismantling or even [underwater] projects and just about anything in between.”
Sponsored Content
Labor that Works
With 25 years of experience, Leadpoint delivers cost-effective workforce solutions tailored to your needs. We handle the recruiting, hiring, training, and onboarding to deliver stable, productive, and safety-focused teams. Our commitment to safety and quality ensures peace of mind with a reliable workforce that helps you achieve your goals.

Specifically, the shear contains fewer pieces and fewer welds, offering what Sturgell calls “a bit more structural stiffness, which cuts cleaner and more efficiently.” He says that is where a well-designed shear can make a difference in terms of safety: “Fewer pieces and fewer welds also means fewer things to go wrong or fail, leading to a longer lasting tool.”
Another design feature of the FS145 involves the use of bolt-on wear parts and what Sturgell calls “superior coverage and replacement wear plates with extra thickness in the chin area.
“Those things reduce a company’s time spent building up high wear areas and changing wear parts like blades and tips,” he says. Or, put another way, they reduce time spent on tasks that take operators out of their cabs and into a situation where they are performing maintenance tasks in an active area.
When maintenance is necessary (and some amount always is), manufacturers still can make decisions that affect safety. “We kept maintenance personnel in mind when designing our access panels and hydraulic components, allowing for easier access,” Sturgell says of his company’s shears.
Safe journey home
Providing workers the best opportunity to operate a mobile hydraulic shear safely can start with the research and shopping process as the best shear for the job can mean scheduled maintenance work predominates rather than emergency repairs.
Shear buyers who make the right choice and follow up appropriately will benefit on several fronts, Sturgell says. “A good maintenance process with the emphasis on safety will extend the life of the shear, reduce downtime, prevent jamming and increase productivity.”
As has been increasingly emphasized by trade associations serving scrap recyclers and demolition contractors, attention to equipment maintenance and workplace safety goes beyond the financial and operating cost considerations.
“We all have families at home that love us and, at the end of the day, we recognize the importance of getting home safely to our families,” Sturgell says. “That is why doing things safely is of the utmost importance.”
Get curated news on YOUR industry.
Enter your email to receive our newsletters.
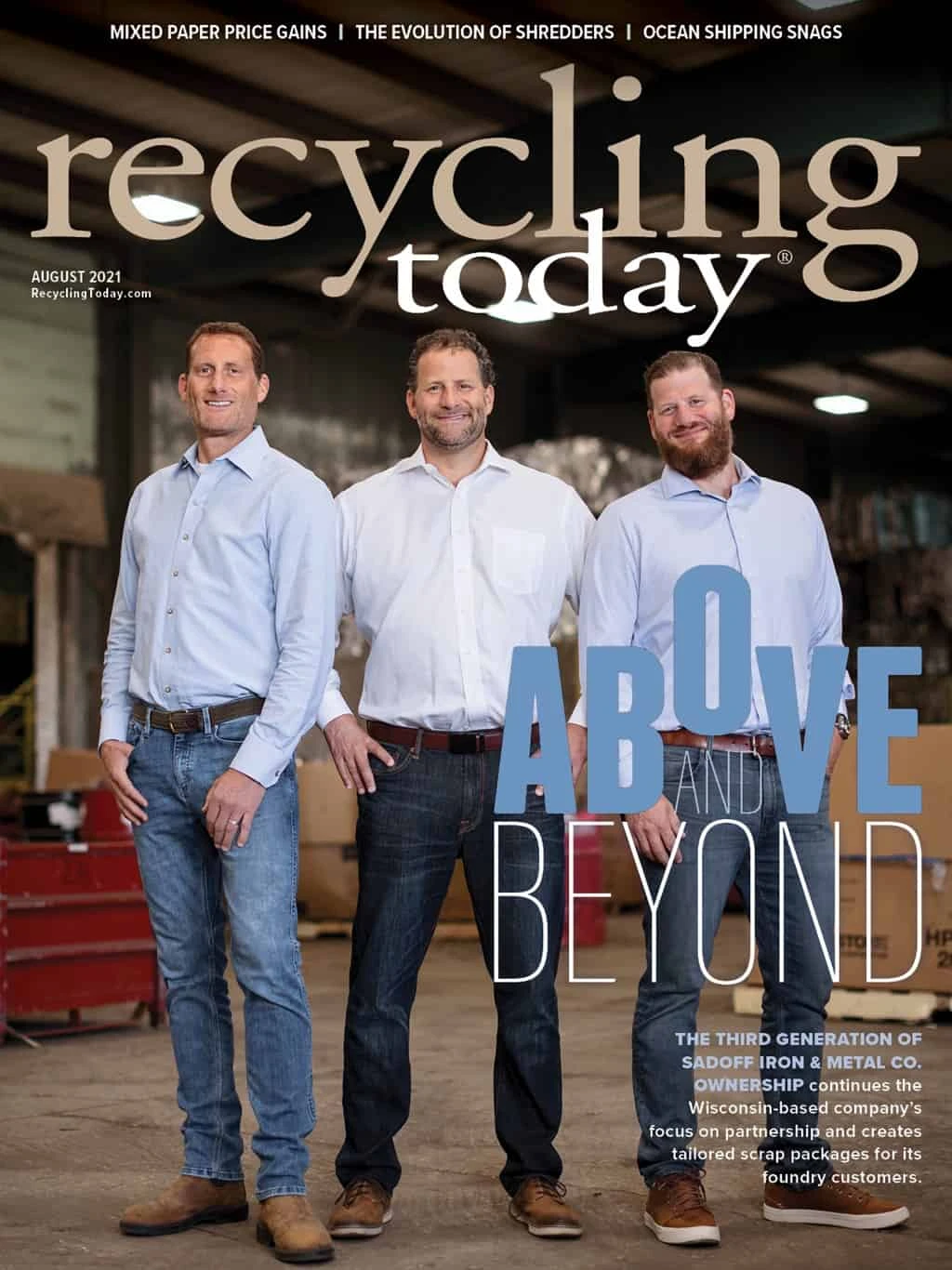
Explore the August 2021 Issue
Check out more from this issue and find your next story to read.
Latest from Recycling Today
- CATL, Ellen MacArthur Foundation establish battery partnership
- Greif announces price hike for all grades of URB products
- Ascend Elements appoints new president, CEO
- Culligan International to provide aluminum water bottles at Chicago running events
- Returpack reports increased DRS activity in Sweden
- Trade groups align against European export restrictions
- Construction, auto sectors show mixed signals
- Politics in Turkey threaten recycled steel outlet