Editors’ Note: The following safety tips are an edited version of “A Safe Operation: Safety Tips for Scrap & Recycle Operations,” which was produced by Caterpillar Inc., based in Peoria, Ill. The full publication can be accessed from Caterpillar’s safety Web site.
The scrap and recycling industry processes millions of tons of materials on a yearly basis. This includes copper, iron, steel, aluminum, lead, zinc, stainless steel and other metals and materials. Anyone who works in the scrap and recycling industry needs to be mindful of the hazards and how to protect themselves against these risks to ensure “Safely home. Everyone. Every day.™”
1. Buckle up. Seat belts, when used properly, hold the operator in the seat and help contain him or her inside the rollover protection structure (ROPS) in the event of a collision or tip-over. The seat assembly, which includes the seat belt and mounting hardware, should be inspected regularly. Inspection is recommended during the pre-shift walk around and as instructed in the manufacturer’s operation and maintenance manual. The following are areas of concern:
- Inspect the seat-belt mounting hardware for wear or for damage, replacing any mounting hardware that is worn or damaged. Make sure the mounting bolts are tight.
- Inspect the buckle for wear or for damage. If the buckle is worn or damaged, replace the seat belt.
- Inspect the seat belt for webbing that is worn or frayed, replacing the belt if it is.
- Inspect the label for the date of installation and replace after three years of service life.
- Consult your [equipment] dealer for the replacement of the seat belt and the mounting hardware.
2. Reduce incidents from material movement. Materials can be transported in a scrap and recycling operation in many ways. Job sites use a variety of mobile equipment, such as trucks, excavators, wheel loaders and material handlers. Operators need to be fully aware of potential dangers while loading and unloading. All loads should be properly secured before moving. Never overload a piece of equipment or work tool. An unsecured or overloaded machine can tip or come apart, causing spillage or material debris on the job. If possible, use regular transportation routes, where employee movement is minimal and roads are smooth for operating equipment. Keep the equipment well-maintained and serviced to help reduce the possibility of injuries and to increase productivity.
3. Personal protective equipment is a must. Personal protective equipment (PPE) is designed to protect employees from workplace hazards that could cause serious injuries or illnesses. Consult your job-site safety coordinator or supervisor for the required PPE needed for your job. Common PPE for scrap and recycling operations includes hard hats, eye protection, high-visibility vests, steel-toed safety boots, gloves and hearing protection.
4. Guard holes and openings. Slips, trips and falls are an easy way to get injured. Unguarded holes can have serious consequences. Large holes, as well as openings in the ground, machinery or support equipment, are dangerous. Ensure that all holes and openings are covered (when not being worked in). Clearly identify and mark off holes so employees and visitors are aware of these dangerous areas and know to stay away. Notify employees and visitors during training and regular safety meetings where these openings exist. It should also be noted during these meetings when they will be open for work so employees are aware and can be prepared.
5. Watch out for tripping hazards. Poor footing may cause slips and falls from equipment. Use extreme caution when maneuvering on or near loose material. Organizing the work area is the best way to avoid slips and falls and make it clear that others are expected to do the same. For secure footing, slip resistant shoes or boots should be worn. Consider conditions that often lead to slips, such as rain, mud, steep terrain and debris. Use three points of contact when mounting and dismounting. Make sure the platform is free of debris, tools, gloves and loose objects. Position your equipment when parking to safely dismount per manufacturer-designed mounting and dismounting points.
6. Minimize contact with objects or equipment with moving parts. Performing maintenance and repairs on a job site can be dangerous. Employees run the risk of being struck by flying objects or material, being crushed by moving parts or subjected to large falling or rolling objects. During maintenance on balers and crushers, make sure the machines are locked and tagged out and others know work is being performed. Be attentive to your surroundings. Always wear the proper PPE (gloves, safety glasses, etc.), remove all jewelry and do not wear loose or baggy clothing. Hand and forearm lacerations easily can happen when performing these tasks, so take all precautions and eliminate as much risk for injury as possible.
7. Properly enter and exit machines. Considering the machine location and high-rise cab setting in equipment for the scrap and recycling industry is important when entering and exiting machines. Start with the proper approach: Always face the equipment and use the access system provided by the manufacturer. Make sure contact areas are clear of mud, debris and defects. Ensure the steps and handrails are properly secured and the landing areas are adequately lit. Check the machine’s surroundings for obstacles, other equipment or activities that may present a hazard. Maintain three points of contact—this means one hand and two feet or two hands and one foot—when mounting or dismounting a machine. Keep hands free of tools and other objects when maintaining three points of contact. Keep footwear free of potential hazards, such as mud, dirt, oil and grease.
8. Perform walk-around inspections. Inspections only take a few minutes to complete and are one of the best ways to prevent mechanical and safety hazards on your equipment. Operators need to understand the importance of completing the checks. Supervisors must encourage walk-around inspections and allow time for the operator to inspect machinery before each shift. Along with looking for cracks, leaks, damage or wear, use your other senses: smell, hearing and touch. Scrap and recycling machines are subject to materials that can puncture hoses and tires, wear out bearings on excavators and cause other types of damage. Taking these few extra minutes in the beginning could help save you a lot in the end.
9. Follow lockout/tagout procedures. Charged electrical equipment can be very dangerous during maintenance or service. Perform proper lockout/tagout procedures according to your company’s policy. Never remove a lock or tag that is not yours. Do not start or operate a piece of equipment that has a lock or tag on it. Place a lock and tag on a machine when continued operation could lead to a safety concern or serious injury when being serviced or maintained. Crushers and balers are extremely dangerous pieces of equipment. When servicing these items, ensure you clearly identify the machine that is being worked on, and always lockout/tagout the equipment source of electricity while work is being performed. Test the system before beginning any maintenance work.
10. Make training a necessity. Practice makes perfect. New operators should be properly trained before starting work on a job site. An operator who is not properly trained is a hazard to everyone on the site. Operators must review the manufacturer’s operation and maintenance manual to make sure they understand the basics before putting machines to work. To create a safe work zone, it is important all employees understand the common communication practices used on the job site. Train employees on job-site communication, including:
- Keeping track of others in the work zone and letting them know where you are at all times;
- Establishing eye contact before entering a work zone;
- Creating two-way communication before entering a work zone; and
- Informing coworkers when leaving a work zone.
Primary contributors to job-site safety are awareness, proper training and attention to detail on the part of business owners and employees. Safety must be a priority and part of a company’s culture. We hope this information is helpful as you strive to safely operate your business.
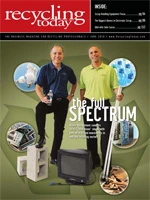
Explore the June 2010 Issue
Check out more from this issue and find your next story to read.
Latest from Recycling Today
- IDTechEx sees electric-powered construction equipment growth
- Global steel output recedes in November
- Fitch Ratings sees reasons for steel optimism in 2025
- P+PB adds new board members
- BlueScope, BHP & Rio Tinto select site for electric smelting furnace pilot plant
- Magnomer joins Canada Plastics Pact
- Out of touch with reality
- Electra names new CFO