Recyclers traditionally use internal combustion (IC) forklifts around their yards and inside their recycling facilities to move prepared and baled material. But with the price of fuel rising and new emissions regulations coming into play, recyclers are questioning whether to maintain and operate their gas-powered forklifts.
To address these issues, equipment providers suggest switching from an IC-engine-powered forklift to an electric model. Electric forklifts produce zero emissions, making it easier for recyclers to comply with emissions regulations, and they can also offer lower maintenace costs, equipment providers say.
But there’s a trade-off to going electric. While, electric-powered forklifts can help to reduce maintenance costs and emissions, they also have a higher initial cost and are not suited for outdoor applications. For outdoor applications equipment providers recommend IC-powered models.
Either way, recyclers have a long list of pros and cons to consider before making a final decision.
IT’S ELECTRIC
High gas prices and emissions regulations are causing more recyclers to turn to electric-powered forklifts for their material handling needs.
"In recycling applications, the electric truck is typically used for moving finished goods around the warehouse," says J.B. Mayes, target marketing and analysis manager for Yale Materials Handling Corp., Greenville, N.C.
The key advantage to using an electric forklift is it produces zero emissions, which makes for a cleaner and healthier indoor working environment, equipment providers say.
"Electric forklifts also reduce fuel costs by up to 80 percent," says Mark Rossler, corporate general product manager, Linde Material Handling North American Corp., Summerville, S.C. But to receive these benefits, recyclers must be willing to pay more up front.
"The initial cost of an electric forklift is higher than IC units because recyclers must also purchase batteries and chargers," Mayes says.
For instance, "A 5,000-pound electric forklift will cost about $2,000 to $4,000 more depending on the configuration users want," says Harry Garber, safety director, Grossman Iron and Steel, St. Louis. "But they are ‘green’ and can be used in indoor environments where emissions may be a concern," he adds.
Mayes says recyclers shouldn’t worry about the initial cost because in the long run electric forklifts are less costly to maintain than IC-powered models. "Electric forklifts help lower maintenance costs because they don’t have the moving parts associated with an internal combustion engine," he says. "They also have lower overall operating costs."
Garber says energy costs for electric forklifts are generally 10 percent to 15 percent of what an internal combustion unit costs. "So, if you spend $1,000 on liquid petroleum gas (LPG) fuel, electric costs to recharge would be about $100 to $150, depending where you live," Garber says.
CHARGING OPTIONS
When purchasing electric forklifts recyclers must factor in the space they will need for the battery charging and changing station.
"How much space recyclers should set aside really depends on how many trucks they have in their fleets," Mayes says. He adds that he has seen recyclers with large fleets set aside anywhere from 1,500 to 2,000 square feet of space.
For recyclers concerned about space, equipment providers suggest fast charging or opportunity charging. "With fast or opportunity charging you may only need to use one battery, which stays in the truck," Rossler says. "So, instead of bringing the truck to the charge station, users can place chargers around the plant to make charging a more flexible procedure."
The electric forklift’s battery life also depends on the recycler’s charging technique. "The traditional charge cycle follows the eight-eight-eight rule, which is eight hours of work, eight hours of charge, followed by eight hours of cool down," Rossler says.
With the fast charge, recyclers only need to charge the battery for four hours before putting the forklift to work. "One drawback to fast charging is it generates a lot of heat, which makes the cool down process critical and sometimes tricky," Rossler adds.
The most convenient charge technique is the opportunity charge. "This enables recyclers to charge the trucks when idle and it’s also a controlled charge that doesn’t overheat or gas the battery," Rossler says.
Improper charging and battery maintenance can also affect the battery’s life cycle. Rossler says recyclers need to remember to clean and water the batteries and to charge them when they reach a certain discharge level.
FILLING UP
Fork It Over |
Besides the engine, another crucial component of the forklift is its forks. Depending on the application, recyclers have their choice of long forks, short forks and even forks designed to perform specific tasks. SAS Forks has been building forks and attachments for the salvage industry for 36 years. "We started out with the 15-foot long forks for moving cars from front to rear, and our business has grown through the needs of our customers," says Adam Lindley, sales manager for the Luxemburg, Wis.-based company. Today, SAS Forks also offers a variety of short forks, crushing forks, claw forks and the company’s latest product, the Scorpion engine puller, for the automotive and scrap recycling industries. The new Scorpion engine puller mounts to any wheel loader weighing more than 28,000 pounds and is designed for versatility, Lindley says. "It can move stacks and bundles of cars, load and unload haulers and crushers and at the same time is able to perform as an engine puller when unfolded." |
Even through electric forklifts offer many advantages, equipment providers still say internal combustion forklifts are the recycling industry’s truck of choice. "This is primarily due to the environment these trucks are working in," Mayes says.
Ken Biediger, senior product manager for Cat Lift Trucks, Houston, says that IC trucks are designed to work in abusive applications such as recycling. "The truck needs to be able to handle bulldozing into loads, product being dropped on it and being hit by debris," Biediger says.
Grossman Iron and Steel operates four IC forklifts, which the company uses for nonferrous material handling, roll-off boxes, barrel handling and unloading skids, parts and supplies. The company also uses its forklifts outside on occasion.
"We have always used IC forklifts because of the demand on their performance," Garber says. "They are constantly working, and when you run low on fuel, you fill them up and keep working." He adds that with electric forklifts the operator either has to stop to charge or replace the batteries, which is time consuming.
Outside, recyclers need forklifts capable of handling a variety of tasks, including lifting and moving heavy materials. "By nature, the IC forklift has a lot more power and torque in the engine, making it more suitable for gathering material and feeding it into the process," Mayes says.
The tires for IC forklifts also add to the machines’ functionality in a recycling yard. "Pneumatic or solid super-elastic tires are the preferred tire options in recycling applications," Rossler says. Biediger suggests purchasing solid tires that are molded into the shape of pneumatic tires and can be used on the same rims.
But IC forklifts also come with their own set of drawbacks. For one thing, IC units are higher maintenance and have a higher fueling cost than electric forklifts, equipment providers say. Because of the engine’s design, IC forklifts require typical preventive maintenance, such as oil and filter changes, greasing of fittings as well as daily checks for hose leaks and wear, Biediger says.
"A general rule of thumb is scheduled maintenance costs will run about three times higher for internal combustion than electric units," Garber says. For example, "based on 2,000 operating hours per year the cost would be $500 for electric vs. $1,500 for IC," Garber adds.
Additionally, IC-engine-powered forklifts are not ideal for use indoors, unless the building has a good ventilation system, according to equipment providers.
Whether recyclers prefer electric or IC-engine-powered forklifts will often depend upon finding the one that best suits their applications.
The author is assistant editor of Recycling Today and can be contacted at kmorris@gie.net.
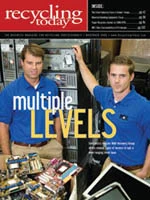
Explore the November 2008 Issue
Check out more from this issue and find your next story to read.
Latest from Recycling Today
- Electrolux commits to recycled content
- Duesenfeld system targets battery cell scrap
- Hyundai says it will make steel in the US
- APR announces Recycling Leadership Award winners
- Glass Half Full opens glass recycling facility in Louisiana
- AmpUp partners with Roundtrip EV
- Global Recycling Day event supports Pittsburgh school's recycling efforts
- President signs executive order on critical minerals