Formerly Dodge-Regupol Inc., Ecore International, Lancaster, Pa., has been using recycled rubber tires in its production process since the company was founded in 1989.
Prior to this, Ecore was manufacturing cork products under the name Dodge Cork Co. But when demand for these products declined, the company’s founders, the Dodge family, started looking for alternative, low-cost raw materials to complement the company’s existing technology and market knowledge. "Recycled rubber was a logical fit," says Ecore President Art Dodge.
Since then, Ecore has grown into a significant consumer of scrap tires, using approximately 40,000 tons of scrap tire shreds and crumb rubber per year, according to Ecore’s Web site. Dodge says he attributes Ecore’s success to the organization’s commitment to innovation and growth.
This commitment was demonstrated in 2008 when the decision was made to part ways with a German affiliate and to rename the company Ecore International. "We choose the name Ecore International because we wanted to broaden our scope and really become an internationally focused company," says Kate Lowry, product manager for Ecore. Lowry notes that even though the company’s name has changed, the types of products, materials and quality Ecore produces have not.
Today, Ecore International continues its efforts to produce high-quality recycled rubber, cork and cork/rubber products for the industrial, commercial and consumer markets.
KEY INNOVATIONS
Ecore produces a number of recycled rubber products, but its most profitable product lines include ECOsurfaces commercial flooring, Everlast sports surfacing and QT sound control insulation.
ECOsurfaces commercial flooring is one of Ecore’s largest business units, and, according to Dodge, Ecore actually pioneered this recycled rubber flooring category 20 years ago. "Art Dodge saw a need for this category, so he decided to create a flooring category using recycled rubber tires," Lowry says. "We like to say that we were green way before the term was even popular in the marketplace."
Gerbert Ltd., Lancaster, Pa., which is run by Dodge’s brother, Andrew Dodge, is the sole distributor of ECOsurfaces in the U.S. The floors are marketed to businesses in the retail, hospitality and health care industries.
A LEG UP |
Lancaster, Pa.,-based Ecore International’s Everlast sports surfacing line has entered a new sustainability partnership with Nike Inc., Beaverton, Ore., for 2009. Through this partnership, Nike Grind rubber is being incorporated into Everlast’s fitness flooring products, now called Everlast with Nike Grind. Everlast with Nike Grind combines raw materials from Nike’s recycled athletic shoes, including out-sole rubber, mid-sole foam and various other shoe components, with premium, recycled tire rubber, according to a company press release. "This partnership gives our customers the best of all worlds," says Kathryn Ross, director of marketing for Ecore. "The opportunity to combine Everlast’s products, already the top brand in fitness flooring known for its durability and large color assortment, with Nike Grind rubber creates a surface capable of meeting the increasingly higher sustainability standards of facility managers, designers and architects." Everlast flooring is made in the United States from recycled tire rubber and colorful ethylene propylene diene monomer (EPDM) flecks that contain approximately 20 percent pre-consumer scrap. |
These floors are made from recycled rubber and ColorMill ethylene propylene diene monomer (EPDM) flecks and are available in rolls and tiles. Everlast sports surfacing can be found in gyms, fitness centers and athletic facilities. In addition to a high recycled content, Everlast products also meet stringent indoor air-quality testing requirements for low-emitting building materials, qualifying them for use in schools and other high-performance buildings, according to Ecore International.
Ecore’s third most popular product is QT sound control insulation. QT is made from tire regrind and leftover tire scrap and is designed to serve the hospitality and multi-family housing markets.
In addition to these products, Ecore also manufactures materials for the automotive, aerospace and industrial markets. Ecore manufactures and sells dynaflex masticated rubber sheets and rolls to auto makers, who then use the material to manufacture fuel tank pads, air dams, mud flaps and splash shields. Ecore also manufactures cork gaskets and duraprene gasketing material for the aerospace market and industrial original equipment manufacturers.
PROCESSING POINTS
Ecore typically receives four truck loads of pre-shredded tires per day from its subsidiary, Recycling Technology International, Hanover, Pa. "They clean and grind the tires at their facility and then send us the tires in chips, pellets or bit-sized form," Lowry says.
Ecore focuses on its manufacturing processes, relying on its subsidiary and outside suppliers for raw material, she says. Even if the company wanted to produce the raw material on site, it doesn’t have enough space, Lowry says.
Dodge says Ecore is not a tire recycling business. "We depend on tire recyclers for our raw materials, but we are not out picking up scrap tires," he says. "So, as long as we have quality suppliers who meet our requirements, there is little business logic in our investing capital to compete for tires."
Once the tires arrive at Ecore, they go through a sophisticated, state-of-the-art production process, according to Dodge. Dodge and Lowry avoid providing details of the company’s process for competitive reasons. What Lowry does say is that Ecore’s process uses minimal heat. The company uses recycled water and its internal scrap to produce some of its products. "So, when material is cut off or rolls have defects in them, we regrind," she says.
Most of Ecore’s products are sold in rolls or tiles. The standard thickness for rolls of ECOsurfaces is 3.2, 6 and 8 millimeters. The standard thickness for rolls of Everlast is 8 millimeters. Lowry says one, 36-inch car tire equals 20 square feet of rubber flooring.
FORWARD THINKERS
Even in today’s tough economy, Ecore has found ways to grow.
Market conditions for the automotive industry have been slowing down, but according to Lowry, the commercial flooring industry is still booming. "I think some of that has to do with the fact that we spec our projects two years out, so we are still feeling the effects of these orders," Lowry says.
As its business has grown, so has Ecore International’s need for more space. Presently, Ecore operates facilities in Lancaster and York, Pa. The Lancaster facility includes a number of buildings spread out across a couple of acres, while the York facility is a new purchase. The acquisition of the York facility brings the company’s total square footage to 800,000.
"In the space we’re in right now, we just can’t expand anymore, so we’re going to move some production to the York facility," Lowry says. She describes the York facility as "more of a holding facility as we continue to grow and emerge within the recycled rubber category."
Ecore also is moving forward with its products. "Our relationship with Nike and the introduction of Nike Training Ground have been really exciting for us," Lowry says. "Nike Training Ground is actually our first retail-to-direct-consumer product." Ecore also has some new products in the works. "Because we have the technology right here in the building, we are able to experiment more with our products," Lowry says.
Currently, Ecore has four new products in research and development.
In terms of where Ecore goes from here, Lowry says, "We all know how the economy is at this time, but because we’re forward thinkers here, we are able to look forward and really see the opportunities that are out there."
Dodge adds, "As an organization, we are committed to innovation and growth. We plan to weather the current economic downturn by introducing new generations of Ecore products and materials here and around the world."
The author is assistant editor of Recycling Today and can be contacted at kmorris@gie.net.
Get curated news on YOUR industry.
Enter your email to receive our newsletters.
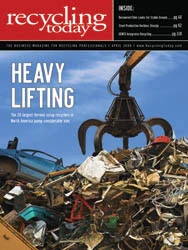
Explore the April 2009 Issue
Check out more from this issue and find your next story to read.
Latest from Recycling Today
- Returpack reports increased DRS activity in Sweden
- Trade groups align against European export restrictions
- Construction, auto sectors show mixed signals
- Politics in Turkey threaten recycled steel outlet
- Toppoint Holdings expands chassis fleet
- Lego creates miniature tire recycling market
- Lux Research webinar examines chemical recycling timetables
- Plastics producer tracks pulse of wire recycling market