The four recovered fiber procurement professionals who took the stage for the “Mill Buyers Panel” at the 2014 Paper & Plastics Recycling Conference replied to a steady stream of questions from audience members.
The panel members, coming from throughout North America, represented companies that manufacture different paper products.
Joining moderator Bill Moore of Moore & Associates, Atlanta, were these panelists:
- Andrew Kern, Smurfit Kappa (containerboard), Forney, Texas;
- Chris Villano, Wausau Paper (tissue products), Middletown, Ohio;
- Jerry Donahue, Huhtamaki Inc. (food service paper plates and trays), Watervillle, Maine; and
- Andrew Inneo, Resolute Forest Products (newsprint), Thorold, Ontario.
Their combined answers to several audience questions offer insights into the state of North American papermaking and the challenges facing recovered fiber buyers in the current business environment.
Q: Transportation costs are rising, especially for trucking services in the U.S. What is the impact on paper companies and what can be done to control costs?
Andrew Kern (AK): It’s becoming an increasing problem, the driver shortages in the Southwest and particularly in Texas. Freight carriers are losing drivers to the oil industry and construction. It’s an equipment shortage and a driver shortage problem. It ultimately has impacted us on higher rates on the longer haul cargoes that we’re bringing into the mill. We have used a variety of freight carriers to service accounts and have had to pass along drop-trailer expenses that carriers used to [offer] at no charge. We’ve had to look at freight lanes and rule out some areas that were regular backhauls into the mill for us because they aren’t cost-effective for us anymore because of the rising cost of freight.
Chris Villano (CV): We have the same situations where lanes that used to be covered relatively easily in the past now are becoming very competitive, with carriers charging what seem to be astronomical rates to get the loads. Our way of overcoming that is, unfortunately, to beef up on inventories, whether at the mill or potentially putting some in third-party warehouses, to be sure we have the fiber when we need it as we need it, whether it be for weekends or for the upcoming holidays.
Jerry Donahue (JD): I have to concur; we too keep inventories high so that if a freight [shipment] does not arrive when it is supposed to, it’s not as big of an issue as it used to be. We will keep two or three weeks of inventory in house; we’re not sitting there hand to mouth on Monday morning. We have moved our logistics to a third-party company, and that third-party company deals with the headaches. We’ve also determined that we have a yield factor as far as our materials are concerned. If we find good quality product that is a little ways off with a higher freight, we’ll buy that. For the material coming into our facility, the cost per usable ton of fiber will be low enough that we’ll pay a higher freight rate for it. We’ve learned to balance things.
Q: To what extent are mill operators exploring how to recycle the plastic, metal and other residuals screened out by drum pulpers and other machines at their mills?
Andrew Inneo (AI): I think the possibility is there to recycle that plastic. The main issue is that once it gets through that drum pulper, it’s covered with ink and it’s got a very high water content. Those various shapes and sizes retain water. That prohibitives content is about 5 percent of our daily receipts. Based on our annual consumption in 2013, we’re pushing out about 35 short tons of drum pulper rejects per day. It’s a significant amount of plastic. Right now the options [for the Thorold mill] are to burn it for the Btu value or to landfill it. But I’d invite any opportunity for someone to come and analyze that material and see if there are any alternative uses for it.
JD: There is a PE (polyethylene) coating on foodboard we take in. To make our paper plates, we’ve got to take the plastic off this paper, and sometimes it’s PET (polyethylene terephthalate) No. 1 or sometimes HDPE (high-density polyethylene) No. 2. Ten years ago we were getting a huge amount of this plastic coming out of our cleaning system; we were landfilling it at a cost of well over $1 million per year. We had folks who researched and were able to find somebody for whom it could be a raw material. We had been baling it and landfilling it, but now we are selling it to someone else and are getting a stream of money coming in, and they are using it to make composite lumber.
CV: Ours is a revenue stream going the wrong direction. We also have plastics going through a compactor. We have looked for opportunities to get rid of this material, but it’s commingled with so many other things that end users have not had a strong appetite to turn it into a finished product. There are so many other contaminants in there that it is just not of any value. We continue to explore other avenues. There is a high water content—a moisture component to the problem—even after the compactor. We generate 5,000 to 6,000 tons annually of this material that we just can’t find a home for. It goes to a landfill. There are metals, staples, tapes—it’s a commingled mess.
AK: We’ve looked at a lot of options. The challenge is that it’s such a blend of various plastics and primarily outthrow fibers that it is not easy to identify anything other than the waste-to-energy outlets, but then the moisture becomes a problem.
Q: Is the perceived decline in accompanying education for residential recycling programs a problem and how does it affect the prohibitives in the material you buy now versus 10 years ago?
AI: The residential curbside system is dual stream where I live. The stream has changed so much over the last few years. You’re seeing so many corrugated and box products now that people are putting in their bins.
The deterioration of the ONP (old newspapers) in that incoming stream has caused a huge challenge [as a] user of ONP. Relative to five years ago we had a daily newspaper in bins. Now maybe there is a Thursday night advertisement section and a weekend paper, and that’s about it, so the stream has changed.
The big challenge is on the hands of the processors to mechanically or hand sort this out. Trying to get the plant throughput to remain profitable has caused the outthrow and prohibitive content of the finished product to change dramatically.
JD: We buy a great deal of our material from the small community recycling operations [in Maine]. I think they do an excellent job of either controlling or educating the people that come in with material, so we get fewer problems.
I am a big proponent of educating the public. I think you’ll get more benefit out of an education program you can support as opposed to just saying you can recycle and put everything, including the cat and the dog, into the bin. I believe the communities need to have something in place to educate the folks in their community and support them.
We do have a single-stream operation in our area, and we did try to work with them because they have material, and we need it. What we found was that the ONP actually turned out to be a negative sort in their system. So as newspapers and other things went in, rather than being a positive sort where ONP was put into a bin, they took everything else out and what was left was called ONP. They had plastic and wood and everything we didn’t need in that mix.
One thing they could do to add quality was to add people for hand sorting. It seemed to work for a couple of weeks, but they weren’t able to continue—the cost got too high. We’ll look for that positive-negative sort difference. If there is a positive sort for the news, we’ll be more interested in taking a look at the quality.
CV: We’ve moved away from [dirty MRF] streams and in some cases we’re paying more for a cleaner material coming in. And to some extent there is a benefit to doing that, because that [prohibitives] extraction process, that disposal process and landfill cost exceed our costs to use a cleaner furnish potentially coming from a farther distance away. It has better benefits for yield and for overall operations at the mill.
AK: We tend to avoid some MRF operations that handle single stream. Their OCC may have a lot of carrier stock—Coke and beer boxes—a high amount of wet strength. Also, broken glass can end up in the paper bales.
I will also say not all single-stream MRF operations are the same. You have better operators with different system designs, so there are some MRFs that we buy from.
Each MRF that we buy from has different impacting factors. They may have more commercial OCC coming into their plant or better [sorting] systems.
CV: Years ago you used to have different [collection] containers for different streams. The single-stream feature, convenience, has created a different kind of monster. … Just out of sheer convenience, people don’t take the newspaper out of the plastic sleeve or the pizza out of the pizza box. It’s a tall order.
Every time we hear the word single stream in the offering, we tend to shy away from it.
Where we can, we’ll pursue the dual-stream [material] or maybe even over-issue to offset that monster.
Q: Recovered fiber prices have been relatively stable in 2014. What factors may be contributing to the lack of volatility?
CV: As we’ve been able to forecast our production needs a little bit better, it has provided opportunities for smarter purchasing and smarter approaches to procuring fiber. We’ve been able to avoid that last-minute “gotta have” a large slug of inventory, where suddenly you’re chasing the market to get your last-minute needs. I think our forecasting is improving, and that’s definitely a benefit.
Also, there are some consumers who have left the marketplace. That leaves an excess inventory that those of us that are here are fortunate to still have in our basket. Years ago those mills might have come back under a different name; today they’re just gone.
The wild card in Asia [offshore buying] has been fairly quiet, and that benefits us. When they come back in with both feet, that is always an unknown that impacts us in a very quick period of time.
AI: We’re in the Buffalo marketplace and we’ve seen the ONP No. 8 price have 12 to 14 months of price stability. You could attribute that to many things, including quality and capacity closures. The export markets have been pretty soft in the last four to six quarters.
JD: After 2008 we had the price of ONP go from $125 to $5 per ton. We saw a huge decline. During that time, closures started and they have continued on right up through today. Supply and demand seems to be in play. The wild card is export, absolutely, but it just doesn’t seem to be there applying pressure at the moment, as far as what we’re buying. But if the price jumps in the future, it wouldn’t surprise me. That’s the type of thing that occurs in these markets.
AK: The domestic collection rates in Mexico are now fairly high. The result has been a much less regular need [from there] for materials, particularly OCC, out of the U.S. and Texas. That, coupled with the fact we do a fair amount of contracting, means we haven’t had some of the struggles to pull paper away from the Mexican markets that we have in the past.
Q: In light of the growing scarcity of No. 8 ONP, which alternative materials can substitute for it at the mill?
JD: We’ve been dealing with this for a number of years already. We’ve seen quality go down quite a bit on [ONP]. We used to run a No. 6 News, then we went a No. 7, only because everybody called their No. 6 a No. 7. Then we went to No. 8 news, so quality is a big issue for us. Trying to find sufficient amounts of quality material that we can run in our process has been difficult, so we have reached out to other streams. We’re not using all No. 8, but we do bring in other types of materials and use those as well.
Unfortunately, one of the things we did was we moved to buying phone books. Guess where phone books are going? Now we’re looking for other types of streams that we can bring to supplement what we’re doing with No. 8. But the fact that the newspapers are getting so much smaller, even though we are recycling more we’re seeing fewer tons come through.
So we do find ourselves reaching out a little further and seeking alternatives. I expect we’ll be competing with [Resolute’s mill in Canada] at some point soon. One of the items we’re also looking at, because the quality issues have increased over the last few years, is trying new and better ways to clean up what we’re buying to use a lower grade material in our process. Unfortunately, when you buy a lower grade like that you have a waste stream that you need to get rid of, so your cost goes up quite a bit just because you’re going to throw away a lot of the weight you’re buying.
We also have looked at using [natural] pulp instead of No. 8 to see if it would benefit the process. It’s one of those things you have to investigate fully before you move forward. But the options when you’re in this type business are getting more and more limited.
AI: The biggest question I’m going to face is working with the deinking staff to find out what other types of alternative grades we can use to produce the finished product. We specifically use loose material coming into the Thorold mill. If the ONP No. 8 grade starts to get to a point where we’re finding it hard to procure within our regional footprint, we’re going to have to go out a little bit farther for more material, which will be a cost. Or we may have to switch to stockpiling baled ONP again. We had moved away from that, but we may have to revisit that in the future to get a more consistent fiber supply that’s cleaner—that meets our needs.
If the market is there for an end product and it means profitability for the mills [to use wood chips in the blend], we’re willing to look at anything to be able to produce that grade for the end consumer.
Q: What are the maximum moisture levels that can be accepted in shipments to your mills?
AK: Moisture in itself is not a problem in the production process. The problem lies with the added weight we’re paying for that is not making it out to the finished sheet. As a rule, 12 percent is what we allow. Above that we look for deductions on the cost and the freight of the material.
CV: Our particular plant does not measure moisture. Generally speaking, if it looks to be dry, it’s going to be accepted, and if it looks to be wet, it’ll be rejected. We try to stay away from those questionable loads. If it appears to be a question, it’s going to most likely get bounced.
JD: We don’t test for it or inspect for it. If we do see something, we may pull it out and look at it a little more closely. If it’s just surface moisture, we’ll probably bring it in. But if it’s contaminated right through the load, chances are we’ll reject it.
AI: I think a fair number would probably be between 5 and 7 percent. But we run such a tight inventory, and we buy so much residential curbside material, after three days of rain if we took moisture into account we wouldn’t have enough paper to run the mill, and it would shut it down.
Information on the Paper & Plastics Recycling Conference and other Recycling Today Media Group events can be found at www.RecyclingTodayEvents.com.
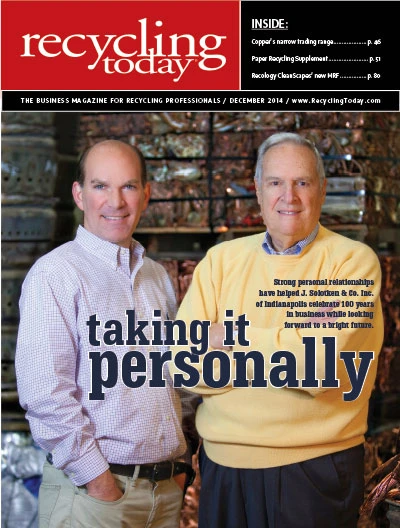
Explore the December 2014 Issue
Check out more from this issue and find your next story to read.
Latest from Recycling Today
- New recycling grant program launches in Massachusetts
- Tire Recycling Foundation names executive director
- Dock 7 named 2025 Exporter of the Year at New Jersey International Trade Awards
- Waste Connections reports ‘better than expected’ Q1 results
- Commentary: How EPR is transforming the packaging industry
- Acerinox names new North American Stainless CEO
- Greenwave closes 2024 books with red ink
- Steel Dynamics nets $217M on record shipments