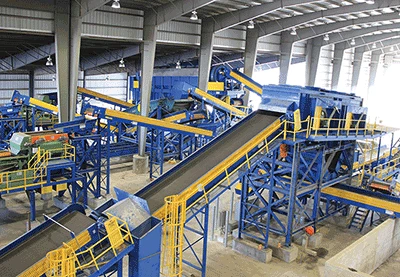
Editor’s Note: This is the first of a two-part series focusing on auto shredder downstream metal recovery and sorting practices and trends. The second story in this series, focusing on trends in nonferrous recovery, will appear in a future issue of Recycling Today magazine.
Recyclers who attended the Institute of Scrap Recycling Industries Inc. (ISRI) Operations Forum, held in Long Beach, Calif., in early October, learned that in today’s business environment, recovering and grading ferrous and nonferrous metals continue to drive process flow and equipment setup when it comes to shredder downstream systems.
At a session focusing on downstream ferrous recovery, a room full of attendees heard from Philip Walls, senior design engineer with Harris Equipment, Cordele, Ga., and Tim Shuttleworth, president of Eriez, based in Erie, Pa., who discussed specific trends they have been seeing when it comes to downstream design and techniques.
In most cases, the speakers said, the trends are spurred by the need for increased ferrous recovery and improved grading. A side benefit of these trends: reduced but more effective handpicking.
“You have to produce the minimum grade to satisfy the market,” Shuttleworth observed, “and you have to produce enough recovery that you stay in business.”
Proper Presentation
Ideal ferrous separation starts with proper presentation of the shred at all sorting processes, said Walls, who has engineered shredding systems since Harris introduced its line of shredders in 2000.
For sorting and cleaning systems to be effective, Walls said, materials need to be well-distributed over conveyor belts. This is accomplished initially by proper chute design, which ensures shredded material is well-scattered but also prevents spillage.
“Your main goal with the chute is to convey material from one conveyor belt to another,” Walls said. “You want to maximize the full width of the belt you’re dumping that material on, so the design of the chute needs to spread it out over the full width [of the conveyor].” Preventing material surges is another downstream goal, Walls noted. “Surges are the bane of effective cleaning,” he said. The shredder’s under-mill oscillator is responsible for proper metering of material, so it should be wide, and it should be monitored, Walls explained. The stroke of the machine also must be monitored for any evidence of a jam. “You never want it to clog because that shuts you down for hours,” he noted.
Another important design recommendation, Walls said, is sizing the width of downstream equipment and conveyors to keep up with the shredder. “The wider you can make things, the better off you’re going to be in picking,” he said. He referred to the tendency of some customers to try to save on equipment costs by narrowing the downstream conveyors. However, Walls said this can lead to burden depths too great for downstream equipment. “You don’t want the burden depth so deep that your magnet is missing things,” he said.
Picking out Pokers
Pokers in the ferrous stream are a source of concern as well as improvements in recent years. These long bars of metal, such as leaf springs, pipes and rebar, can cause stoppages as well as equipment damage, and they also affect the density of the finished product, Walls said.
Thankfully, equipment companies and shredder designers offer a variety of options to deal with pokers. A more inexpensive solution, said Walls, is the use of one or two solid grates below the shredder to help redirect pokers back up into the mill.
“Running solid grates is probably the simplest thing you can do to reduce the amount of pokers you have,” he said.
Another option, Walls noted, is adding a grate with a center rib or bar design perpendicular to the grate circle to help redirect pokers back into the hammer swing.
Several equipment manufacturers also offer solutions that are installed before the primary ferrous magnets that are designed to catch and pull off pokers using specially designed magnets or splitters.
“This will reduce the amount of effort you have to put in to manually remove pokers,” Walls said.
Similarly, Shuttleworth said, with today’s methods of poker removal, it’s possible to remove as much as 80 percent of pokers before they reach the primary scrap drum(s). In this way, he notes, the troubles they cause can be avoided and handpicking efforts may be more productive.
Cyclones and Magnets
Cyclone system use and positioning also has changed in recent years. Walls said, these days, cyclone systems are placed after the primary magnets. In prior years, he explained, cyclones were used before the magnets, in an attempt to clean both nonferrous and ferrous metals. But this, Walls reflected, “was not very effective for either.” The advent of better magnets and eddy current systems changed all that.
Pokers: To ReShred or Not to ReShred?Attendees of the Institute of Scrap Recycling Industries Inc. (ISRI) Operations Forum appeared to disagree on the topic of whether pokers that had been removed from the downstream flow should be sent back to the shredder. Tim Shuttleworth of Eriez told attendees it was probably best not to try to rerun them. “Put them in the heavy melt,” he said, “and make sure they never come back.” In support of this practice, a conference attendee commented that most charging buckets today are 10 feet in diameter, so an occasional leaf spring may not necessarily cause a problem. Another attendee said it could depend on the end customer as to whether it’s acceptable to put pokers in with the heavy melt. If the customer is a large integrated mill, he said, it may allow a poker here and there in the mix. A foundry, on the other hand, “wants a nice dense product of shred,” he said. Meanwhile, Scott Newell, president of The Shredder Co., Canutillo, Texas, said those shredder operators that do attempt to rerun pokers also may have prepared for this by adjusting their shredder grates in some way. “There’s nothing wrong with putting them in the No. 1 (heavy melt ferrous grade),” he said, adding, “Shredded scrap is worth $20 more and it doesn’t cost you any more to rerun them during the day.” |
“We started allowing the magnet to separate the ferrous from the nonferrous first, and then we put the cyclone straight on the ferrous scrap," said Walls. Moving the cyclone also helped eliminate nonferrous metal loss that occurred when both metals were processed together.
Another recent update, Walls said, is the use of zero-emission Z-boxes or ripple boxes. “At the end of the day you want a cascade effect,” he said. In the process, dust and foam are removed from the ferrous in a closed system, with air being vented through the top and bottom.
Conference attendee Chris Melenick, a systems project manager with U.S. Shredder and Castings Group, headquartered in Trussville, Ala., said Z-boxes may not be part of the newest shredder installations, unless specifically requested by the customer or when customers upgrade facilities with existing cyclone systems.
“It depends on the mills they go to,” Melenick pointed out. “Some have more stringent standards to abide by.”
Likewise, Walls said while cyclones and Z-boxes are still used in many auto shredding facilities, their popularity has waned a bit.
“Those cyclones and fans are expensive to run,” Walls said, referring to the need for 200- or 300-horsepower motors, complex ductwork and significant maintenance.
Meanwhile, Shuttleworth said many recyclers are avoiding air systems because of air quality permitting issues.
“The trend now is to go with strictly magnets and not do any sort of cyclone,” said Walls, though he concedes this trend hasn’t fully caught on among recyclers.
Along with this trend is the development and use of larger magnets that tend to offer greater magnetic force. “Width was still important, but we found out the larger diameter was better,” observeed Walls.
The larger magnets also led to the use of fewer magnets, he explained. “Now we’re seeing more single super or mega magnets. These are upwards of 72 inches in diameter and really pick up a lot of material,” Walls said. They can be run with or without cyclone systems, he added.
Sponsored Content
Labor that Works
With 25 years of experience, Leadpoint delivers cost-effective workforce solutions tailored to your needs. We handle the recruiting, hiring, training, and onboarding to deliver stable, productive, and safety-focused teams. Our commitment to safety and quality ensures peace of mind with a reliable workforce that helps you achieve your goals.
Sponsored Content
Labor that Works
With 25 years of experience, Leadpoint delivers cost-effective workforce solutions tailored to your needs. We handle the recruiting, hiring, training, and onboarding to deliver stable, productive, and safety-focused teams. Our commitment to safety and quality ensures peace of mind with a reliable workforce that helps you achieve your goals.
Shuttleworth pointed out that along with these new options, numerous decisions must be made concerning the selection of the right unit, such as drum size, number of units, magnet type and how the magnetic circuits are arranged. “You’re going to trade off grade and recovery and money, because the features come at a cost,” he said.
Finishing Touches
Removing copper from the ferrous stream is another job that used to be performed entirely by hand. In his presentation, Shuttleworth pointed out today’s ferrous lines optionally feature some sort of copper separation equipment, which can be one or more of three various types: polishing magnetic drums, ballistic separation and X-ray transmission (XRT) technology.
“Copper separation is optional,” Shuttleworth noted. “Not every producer goes to pains to get the copper out, but it’s one of the newest efforts in recent years.”
The goal of all three techniques is the same, Shuttleworth said: the separation of clean and low-copper ferrous from ferrous that’s contaminated with copper. To do this, ballistic separation and polishing drums may be able to create two ferrous streams: a larger, very-low-copper-content ferrous product and a smaller, ferrous stream that is easier to handpick for the concentrated copper. The larger, very-low-copper content stream, Shuttleworth said, also may be able to command a premium price in the marketplace.
“With today’s equipment, it is possible to generate a clean, low-copper shred (0.17 percent copper) which is 75 percent of the total shred volume, and therefore only need to pick 25 percent of the residual,” Shuttleworth said.
Meanwhile, XRT technology uses X-rays to sort for copper-containing pieces, such as meatballs, and eject them from the stream with an air nozzle or paddle. The downside of this method: It may not identify pieces in which the copper is concealed.
Shuttleworth referred to one recycler who is currently studying the combined use of ballistic separation and XRT.
The picking station, traditionally the last stop in the ferrous line, said Walls, has seen design changes in recent years too. Poker removal, more advanced magnets and better copper removal systems have all helped to decrease the amount of manual handpicking required.
“In the older days, and sometimes today, because of all the pokers, tires, wire and meatballs, you ended up going with a longer conveyor,” he said. The material burden couldn’t be very thick, Walls explained, “so you went wider to spread it out.”
Nowadays, though, as more is being removed on the front end, he said, conveyor belt widths and lengths are more reasonable. “You don’t have to go ridiculously overboard if you can remove some of that stuff before it gets there,” said Walls.
In the end, today’s more sophisticated processes are designed to improve the recovery and the grading of the ferrous product well before it gets to picking stations. While most of these options do come with increased costs, recyclers who are doing the math may find an option that makes financial sense for them.
The author is an editor with Recycling Today and can be reached at lmckenna@gie.net.
Get curated news on YOUR industry.
Enter your email to receive our newsletters.

Explore the December 2013 Issue
Check out more from this issue and find your next story to read.
Latest from Recycling Today
- AF&PA report shows decrease in packaging paper shipments
- GreenMantra names new CEO
- Agilyx says Styrenyx technology reduces carbon footprint in styrene production
- SABIC’s Trucircle PE used for greenhouse roofing
- Hydro to add wire rod casthouse in Norway
- Hindalco to invest in copper, aluminum business in India
- Recycled steel price crosses $500 per ton threshold
- Smithers report looks at PCR plastic’s near-term prospects