Recycling and waste facilities all face the same daily pressures: thin margins, the desire to increase daily production and the fear of the unknown, such as unplanned downtime.
It’s never easy. But when it comes to balers and wire tie equipment, following 10 simple steps can help to ease the pain and put you on the path to profitability.
1. Rely on your operator. You may have the latest equipment, but does your operator understand it? The knowledgeable operator is the person who can tell when something is amiss just by listening to the machine or by its feel. Make sure that all of your operators are factory trained. This can take place at your facility. New wire-tie offerings include sequential gearing to minimize wear through variable speed operation—take advantage of this feature through training and reap the rewards.
2. Keep up and running through basic “pit-stop” maintenance. It’s more than just knowing how to operate the machine and diagnose problems. It’s about taking care of those problems once they occur. A basic preventive maintenance program should include cleaning and checking vital components. New features, such as convenient access to the tying head from the front of the machine, means your operator no longer needs to climb on top of the machine for maintenance. It also means less time to get into and out of the machine, reducing downtime from perhaps an hour to 20 minutes. With the interconnection located outside the machine with color-coded cables, accurate maintenance and revisions are simplified. Parts replacement, scheduled lubrication and keeping the system clean should be part of a checklist that’s adhered to and signed off on at least once, ideally twice, per day. A baling system should be running smoothly and its operating conditions verified at every shift change.
3. Schedule regular preventive maintenance service technician calls. A second set of eyes from outside the organization can be a lifesaver. As machine operation changes over time, an operator using the equipment daily may become used to conditions that are changing gradually. Those changes may be a red flag, however, to a service technician who visits perhaps once a month. Accelerated production or a new processing mix may have altered the machine’s operation, and that may mean that more frequent preventive maintenance is required. The technician also can test your operators by arranging a mock “failure”—doing something to prevent the machine from operating until the operators can determine what is wrong. Such simulations can help your employees learn quickly so they can prevent downtime.
4. Know when to call in a specialist. “The baler’s down.” These are words that no recycler wants to hear, ever. But reality tells us that at some point, it will happen. And what you do next is what makes the difference in getting the operation going again. Be ready with “Plan B”—If your operator and technician can’t fix the problem within a prescribed time, you can call on a factory technician who is trained to quickly diagnose problems and has access to necessary spare parts (if you don’t have them in your inventory) to make the repair and get you back up and running.
5. Quick-change artistry. Wire tying modules—those that include up to 80 percent of a system’s moving parts—mean that key wear parts can be changed quickly to accommodate basic maintenance issues. This should be the operator’s job, not the job of a facility’s service technician. Most module swaps can be accomplished in just a few minutes. Do you really want to have to shut down the baler for an extended time—and lose profitability—just to find a service technician who can make the switch? No question, the operator should own this job in your facility.
6. Drop down, save up. If a line’s baling materials change, a facility also can down-gauge its wire and cut costs with no reduction in wire strength or resilience. That’s literally money in the bank. Keep a spare module that is matched to a different gauge. It goes right to the bottom line.
7. Know your wire. If you think that all wire is created equal, think again. New 100-percent-annealed wire formulations composed of specialized steel offer higher ductility and durability along with a higher yield point. Operators can use less wire with the same or fewer straps per bale with the same strength and dependability, delivering a 25 percent yield increase. In an era where low interest rates are the norm, a 25 percent savings on anything should be incentive enough to learn more and take advantage of technology. High quality wire is an investment that will pay off in improved efficiency, reduced downtime and better quality end product.
8. Know your wire supplier. Don’t get caught short. Wire shortages may occur on occasion, but manufacturers that specialize in and invest in wire technology typically won’t get caught short. Some produce both wire and wire tying machines and have specialists on hand, such as metallurgists and packing engineers, who are there when you have questions and can prescribe the best solution to meet your needs.
9. Play it safe. Thanks to modern safety measures, accidents and injuries have almost become a thing of the past. Almost. Operators should be aware of the areas they need to watch to avoid an injury. Safety covers make it easier to ensure safe operation, because the machine is disabled if they are removed. The equipment is designed that way for a good reason, of course, but safety devices such as these have been tampered with in many instances. That’s never a good idea. Forgoing safety for production is a recipe for disaster and lawsuits. It’s not worth it, ever.
10. Take the train. Most of what is covered in the first nine points comes down to one word: training. Providing employee training for everything—operation, maintenance, safety—should be a part of your plan, and that includes, to the degree necessary, training for your operations personnel, service technicians and management. Training ensures that everyone knows what to do and when to do it. It’s also knowing when to admit you’re in too deep and you need outside help. It’s knowing the right suppliers and manufacturers. Training should never stop. Refresher courses for existing employees and introductory courses for new employees should be scheduled annually.
These 10 steps aren’t foolproof. There will always be something you didn’t plan for. But, by following these steps, you’re off to a good start.
Sponsored Content
Labor that Works
With 25 years of experience, Leadpoint delivers cost-effective workforce solutions tailored to your needs. We handle the recruiting, hiring, training, and onboarding to deliver stable, productive, and safety-focused teams. Our commitment to safety and quality ensures peace of mind with a reliable workforce that helps you achieve your goals.
Sponsored Content
Labor that Works
With 25 years of experience, Leadpoint delivers cost-effective workforce solutions tailored to your needs. We handle the recruiting, hiring, training, and onboarding to deliver stable, productive, and safety-focused teams. Our commitment to safety and quality ensures peace of mind with a reliable workforce that helps you achieve your goals.
Sponsored Content
Labor that Works
With 25 years of experience, Leadpoint delivers cost-effective workforce solutions tailored to your needs. We handle the recruiting, hiring, training, and onboarding to deliver stable, productive, and safety-focused teams. Our commitment to safety and quality ensures peace of mind with a reliable workforce that helps you achieve your goals.
Sponsored Content
Labor that Works
With 25 years of experience, Leadpoint delivers cost-effective workforce solutions tailored to your needs. We handle the recruiting, hiring, training, and onboarding to deliver stable, productive, and safety-focused teams. Our commitment to safety and quality ensures peace of mind with a reliable workforce that helps you achieve your goals.
Sponsored Content
Labor that Works
With 25 years of experience, Leadpoint delivers cost-effective workforce solutions tailored to your needs. We handle the recruiting, hiring, training, and onboarding to deliver stable, productive, and safety-focused teams. Our commitment to safety and quality ensures peace of mind with a reliable workforce that helps you achieve your goals.
Preventive maintenance and training may mean paying a little now to save a lot later. How much? It’s impossible to estimate what might have been and the costs associated with it. Better to realize a steady profit from a smooth-running operation with personnel who know their jobs as well as their limitations and suppliers and vendors you can count on.
The author is president of L&P Wire-Tie (www.lpwiretie.com), Carthage, Mo.
Get curated news on YOUR industry.
Enter your email to receive our newsletters.
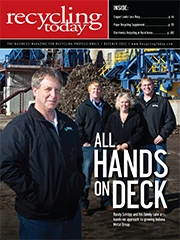
Explore the December 2012 Issue
Check out more from this issue and find your next story to read.
Latest from Recycling Today
- Toppoint Holdings expands chassis fleet
- Lego creates miniature tire recycling market
- Lux Research webinar examines chemical recycling timetables
- Plastics producer tracks pulse of wire recycling market
- Republic Services, Blue Polymers open Indianapolis recycling complex
- Altilium produces EV battery cells using recycled materials
- Brightmark enters subsidiaries of Indiana recycling facility into Chapter 11
- Freepoint Eco-Systems receives $50M loan for plastics recycling facility