According to the Corrugated Packaging Alliance, 31.7 million tons of corrugated cardboard were recovered and recycled in the United States in 2010—that’s 85.1 percent of all containerboard produced in that same year. For processors of old corrugated containers (OCC) throughout the country, however, that high recycling rate does not mean their access to material is always consistent.
To boost short-term and long-term revenue, processors need to provide mills that consume recovered fiber with steady, scheduled OCC deliveries to receive the best payments.
Processors have tried several approaches to regulate their OCC supply. One such approach is to streamline their supply chain at the source by working with their customers to compact and bale their OCC on site.
OCC that have been compacted, baled, stacked and are ready for pickup take up less space and, therefore, require fewer pickups by processors—a major savings in transportation costs.
Customer Benefits
Retail stores, restaurants and other commercial establishments accumulate considerable OCC, requiring as many as three pickups each week.
Some of these companies have realized that if they compact and bale their cardboard, they not only save on tipping fees—the price landfills charge to dispose of material at their facilities—but may actually eliminate those fees altogether. In some parts of the country, processors will pick up OCC for free and may even pay the generator a rebate for the material.
In addition to the cost savings involved in pickup and transport, organizations also can benefit from the space savings. When cardboard boxes are compacted and baled, they take up considerably less space, which allows more square footage for revenue-generating activities.
Compacting and baling also eliminates employee visits to the Dumpster, allowing workers to focus their attention on customers instead. And, fewer boxes piled up means a cleaner, more manageable premises, eliminating potential hazards, such as fire, mildew and pests.
Many small and medium-sized establishments believe that compaction equipment is too large and expensive for them. What many don’t realize is that compactors and balers can be small enough to fit into a storage room at the back of the house—taking up less than 6 square feet of floor space and only requiring standard 110-volt power.
Processor Benefits
From a processor’s perspective, baling and compacting OCC at the source can boost revenue and reduce costs.
The compacted, baled OCC takes up less space; thus, the processor can decrease the number of pickup days, saving on costs related to transportation, such as gasoline, and labor expenses.
For example, a store or restaurant with an 8-yard container may have pickups three times per week. However, if all of that customer’s OCC was baled, the processor could reduce its pickups to once each week, or even twice per month.
Fewer visits to each customer reduces gasoline costs, prevents wear and tear on vehicles and requires fewer staff members to manage. It also significantly reduces the processor’s carbon dioxide emissions. It also creates the opportunity for the same processing company to visit more locations and ultimately collect more material using the company’s existing truck fleet.
In some cases, recyclers are now actively seeking baling and compacting equipment for their customers and facilitating the sale or lease of the equipment to those establishments. In many areas of the U.S., it makes economic sense to do so, as baled compacted material helps processors simplify logistics and reduce costs while gaining consistent access to salable material.
Influencing Factors
This model is most effective in regions where trash haulage fees and the value of OCC are high. A case in point is the corridor that encompasses Boston, New York and Washington, D.C.
In these East Coast cities, the cost of hauling trash away is high. For retailers, restaurants and other businesses, the prospect of getting their OCC picked up for free is compelling—as is the prospect of a rebate. Generally, processors offer a rebate on OCC while haulers don’t.
For instance, if a grocer or restaurant in Boston wants to have its cardboard taken away by a trash hauler, it would cost approximately $170 per haul and $90 to $95 per ton removed. However, if the business instead chooses to contract with a recycling processor to collect the OCC it generates, the processor usually does so for free. Depending on the customer contract and the overall commodity value, processors also will offer a rebate for the material. The high density of businesses in Boston means the recycler can pick up more OCC from more customers without having to travel long distances.
Sponsored Content
Labor that Works
With 25 years of experience, Leadpoint delivers cost-effective workforce solutions tailored to your needs. We handle the recruiting, hiring, training, and onboarding to deliver stable, productive, and safety-focused teams. Our commitment to safety and quality ensures peace of mind with a reliable workforce that helps you achieve your goals.
Although the pricing benchmarks vary from month to month, recycling processors on both coasts of the United States as well as in those the Chicago area find that the baling business model works well for them.
At Orwak, we facilitate this relationship by introducing recycling processors to customers that may be a source of steady OCC supply. By connecting the two, the customer benefits from reduced haulage costs, and the processor improves efficiency and gains access to a reliable stream of material that can be sold to mills at a higher rate. In many cases, the processor is able to secure new customers on three-year contracts and to provide these clients with a competitive rebate for the material.
“This arrangement makes economic sense for both us and the customer,” says Dawn Jessel, vice president at Georgetown Paper Stock, a recycling processor with plants in Washington and in Baltimore. “The customer is able to yield cost savings, and we are able to get a steady supply of material and receive more material per pickup.”
The author is senior vice president of sales at Tomra North America, a wholly owned subsidiary of Tomra Systems ASA and a global provider of recycling solutions. He can be reached at mlanning.orwak@tomrana.com. Information on Orwak, Tomra’s compaction unit, is available at www.orwak.us.
Get curated news on YOUR industry.
Enter your email to receive our newsletters.
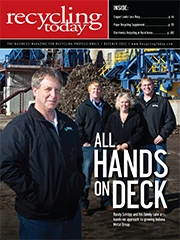
Explore the December 2012 Issue
Check out more from this issue and find your next story to read.
Latest from Recycling Today
- AF&PA report shows decrease in packaging paper shipments
- GreenMantra names new CEO
- Agilyx says Styrenyx technology reduces carbon footprint in styrene production
- SABIC’s Trucircle PE used for greenhouse roofing
- Hydro to add wire rod casthouse in Norway
- Hindalco to invest in copper, aluminum business in India
- Recycled steel price crosses $500 per ton threshold
- Smithers report looks at PCR plastic’s near-term prospects