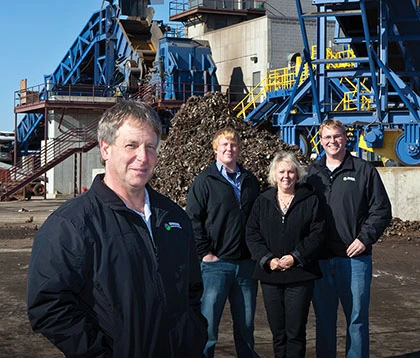
![]() |
Randy Schlipp, president of Indiana Metal Group (IMG), headquartered in New Carlisle, Ind., is serious when he says he is willing to go the extra distance to stand out from his competitors. For instance, when the company decided to add its first auto shredder, rather than hire a contracting crew to build the shredder and downstream system, Randy, his sons Nick and Ryan Schlipp and his son-in-law, Chad Medlin, worked around the clock to do the job themselves.
IMG operates a number of subsidiary companies, including Gertrude Street Metal Recycling, South Bend, Ind.; Bulldog Auto Parts, South Bend; Going Green Metal Recycling, Cicero, Ind.; Going Green II Metal Recycling, newly opened in Kokomo, Ind.; and Randy’s Metal Recycling, Eau Claire, Mich. While these locations also handle and process nonferrous metals, they act as feeder yards for IMG’s newest company, New Carlisle-based 360 Degree Metal Recycling, its first auto shredding operation, which opened in September 2012.
Family Tree
Randy is the third generation of his family in the metals recycling industry. He is joined by his sons, who began their careers outside of the family business. For Nick, vice president of IMG, that meant working as a computer technician for several years.
“I couldn’t stand working inside,” Nick says of his previous job.
Like many traditional family-owned businesses, Randy started in the industry working for his grandfather’s auto parts company, Five Corner’s Garage, in Michigan. As time went by the company added other services.
In 1995, Randy took over his grandfather’s business. In addition to expanding the company by adding new locations, he invented equipment, including an oil drainer that he calls the Auto Tap, which Randy says would help to make the company more environmentally friendly.
Gale Schlipp, Randy’s wife (while separated, she still works at the company), has done all the accounting and payroll for IMG from day one and was later joined by Nick’s wife, Jennie.
Gradual Expansion
Gradually, IMG moved into the auto crushing side of the business and currently operates six car crushers.
With the growing amount of material it was handling and growing competition from larger scrap metal companies, Randy says he needed “to get big, get bought out or go out of business.”
He decided to go big and, with the support of his family, to build an auto shredder at a new facility in Michigan.
“I was concerned about getting cut off from our supply of scrap,” Randy says of the decision to add the auto shredder. “The last piece of the puzzle was the auto shedder. We needed that to secure our future. Lots of smaller family companies’ yards were dying off or being acquired by larger companies. You have to become a larger company, sell to a larger company or be forced out.”
Randy says when he got into the business of crushing cars in 1995, 2,500 cars equaled a big job. Now, he says, 500 cars amount to a big job in light of the growing competition among recyclers for material to process.
In addressing the issue of auto shredder overcapacity, Randy hesitates. While there may be an oversupply, he says the company’s four feeder yards will help to steadily supply its shredder. Additionally, Randy says, IMG is willing to pick up material, including auto hulks.
Adding to the challenge of being a small, family-owned company competing against a number of large national scrap processing companies, he says, is that any time the small companies start making money, investors and the big guys enter that market.
“We are one of the few mom and pops out there,” Randy says.
Site Problems
While Randy originally made the decision to purchase and install an auto shredder roughly three-and-a-half years ago, finding a location for the shredder presented challenges. The initial planned location was Benton Harbor, Mich. However, partly because of the negative publicity being generated by the former Sturgis Iron & Metal mega shredder in nearby Elkhart, Ind., area residents were vocal in their opposition to IMG’s proposal. Despite the fact that IMG’s proposed auto shredder was far smaller than Sturgis’ shredder, opposition was intense.
A Closer Look The automobile shredder and downstream sorting system at 360 Degree Metal Recycling, New Carlisle, Ind., includes:
|
Randy says, “Sturgis Iron and Metal made it difficult for our project. Because they built a shredder too close to homes, it seemed to be on the news every night.” He adds, “No one understood that our shredder was different.”
Even though IMG’s proposed auto shredder was to be built in an area zoned for heavy industry in Michigan, the project was turned down. However, Randy says that in hindsight he is grateful that the shredder wasn’t approved. “If you draw a 60-mile supply radius around the proposed Michigan site, part of our supply area would be in Lake Michigan.”
After learning the community of Benton Harbor rejected the company’s proposed auto shredder, Randy says he considered locating the shredding operation in South Bend. Despite opposition from some residents, IMG eventually received approval to build the auto shredder in that Indiana city.
In an effort to clear up misperceptions that critics may have held about the shredder, Randy says he rented a Greyhound bus to take interested parties to a shredder operation that is similar to the shredder the company was proposing. “We took them to Franklin Iron & Metal in Dayton, Ohio,” he says. “We changed a lot of minds when we went there.”
Despite the support from the South Bend community, IMG eventually opted to locate its auto shredding operation in New Carlisle.
DIY Ethic
IMG has demonstrated its willingness to take a different approach to the scrap recycling industry. When it came time to install the shredder, for instance, the Schlipp family didn’t contract a crew for the project. Instead, Randy, Nick, Ryan and Chad opted to assemble the shredder, as well as the downstream sorting system, themselves.
Randy says, “We were all a part of the construction of the shredder. We hired a building group to manage the project, but the whole time we said we were going to assemble the machine [ourselves].” He adds, “There were foremen in the company who had doubts. They tried to talk us into having riggers and ironworkers do it.”
Nick adds that IMG hired Prime Construction Services, Vicksburg, Mich., to take bids on some parts of the project, including pouring the concrete, though the Schlipps were committed to installing the shredder and the downstream systems themselves.
“We assembled the box, which took us about five days,” he says. “It took us a week to put the infeed conveyor in. They told us we needed to get two-thirds of the downstream installed quickly to keep on schedule. We worked around the clock. And it took us a total of eight days, 24 hours per day, to put in the downstream in,” Nick adds.
Why the do-it-yourself approach?
Randy is quick to reply: “By assembling the shredder, we know each and every part of the shredder and how it works. By having our employees build the shredder, everyone knows how to repair the system,” he says.
The Schlipps’ hands-on approach is not limited to building the shredder.
“You can find my dad in the crane more than any office,” Nick says.
“The employees have a lot of respect for him because he isn’t one of those guys who sits in an office and looks out the window.”
Environmental Stewardship
Embracing environmental stewardship is another of IMG’s hallmarks. While many scrap metal dealers have embraced “green consciousness” in recent years, Randy says it has been a part of his company’s DNA from the beginning. In fact, Randy says he attempted to discourage his sons from entering the family business initially because of the industry’s somewhat questionable environmental record.
Demonstrating early on his interest in running an environmentally safe operation, Randy says he invented and marketed the Auto Tap, an auto fluid removal station that focuses on the fast drainage of auto fluids. It is designed to protect the environment and employees from the hazards often associated with removing flammable and other hazardous fluids from scrap vehicles.
Randy also invented the Ironsides trailer cover system, a four-walled steel containment device used to haul crushed automobiles.
He markets the Ironsides and Auto Tap through 360 Degree Resource Inc.
IMG has taken efforts to keep its environmental philosophy front and center in its daily operations. Randy says it was a foremost thought when planning the company’s auto shredding facility. “I sat down with my sons to see what we could do about protecting the environment,” he says of planning process for one of IMG’s newest locations.
The Schlipps say they wanted the site to be the most environmentally safe shredding operation in the country. The site features a seven-layer liner designed to catch any fluids that might seep through cracks in the yard’s pavement. The property’s 18 acres are paved using either concrete or asphalt. Nick says, “We have a double fail safe,” noting the liner and the 9 to 11 inches of concrete or asphalt at the site.
360 Degree Metal Recycling also has a retention pond to treat stormwater runoff. Nick says he is very proud of this feature, which includes a system of filters and screens designed to ensure that all of the water that is not recycled to cool the shredder is held in a pond. Because of the degree of filtration, Nick says the water in the retention pod is almost as clean as drinking water before it is discharged. “By doing that, we can file exemptions for our stormwater runoff permit because we control it all,” Nick says.
Randy says in the past recyclers were not as focused on protecting the environment as they are now. “They used to not worry about the fluids,” he says. “We need to do what’s right, and I think we have done that above and beyond.”
This approach may make IMG and its 360 Degree Metal Recycling subsidiary environmental leaders in the industry. However, in a market where scrap recycling companies are competing for a dwindling supply of material, IMG has to be creative to obtain enough material to meet its needs.
Service Oriented
While many scrap metal dealers may commiserate about the decline in scrap generated by industrial sources, IMG tries to avoid the sector altogether. “We don’t pursue a lot of the industrial accounts,” Randy says. “We do more of the labor-intensive jobs. We provide companies with a whole different level of service that national companies don’t want to do themselves,” he adds.
Nick says IMG has sought out other sources of material. “We have gotten into demolition work—scrap metal demolition and building demolition,” he says. “And as far as nonferrous metals, we started purchasing nonferrous 10 years ago to supplement the ferrous [business] when it was slow. It is now 40 percent of our business.”
In addition to aluminum, the company accepts other nonferrous metals in an attempt to diversify its business. Nick says IMG added copper wire granulation in 2008 at the company’s Eau Claire yard.
Attention to customer service is another way IMG can attract material, the Schlipps say. For instance, Nick says, when crushing cars at customers’ sites, the company takes care to clean up after itself. IMG also monitors and cleans its own sites, which helps to prevent damage to customers’ vehicles while visiting the company’s yards, he says.
“Dealers say that at some shredders in the Chicago area it may take a long time to unload from a truck,” Nick says. “They can’t compliment us enough about the easy flow of traffic from our site. They want to know what they can do to get more scrap out to our yard; they can get out faster, with fewer equipment repairs.”
These steps may give a small company a modest edge, though Randy and Nick say they still have to work smarter and better to compete.
“The biggest advantage we have is we are a smaller group,” Randy says. “We don’t have to come up with as much money for payroll and expenses every month. We are hands-on. You can find me in the crane. Nick, too. Ryan is often operating the shredder. We give family-type service. We don’t have to earn as much to pay the bills.”
The author is senior editor of Recycling Today and can be contacted at dsandoval@gie.net.
Randy and Nick Schlipp discuss 360 Degree Metal Recycling’s new auto shredder in New Carlisle, Ind., in a video interview at www.RecyclingToday.com/360-degree-metal-recycling-indiana-auto-shredder-video.aspx.
Get curated news on YOUR industry.
Enter your email to receive our newsletters.
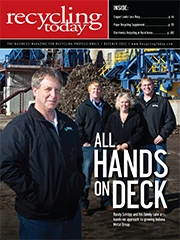
Explore the December 2012 Issue
Check out more from this issue and find your next story to read.
Latest from Recycling Today
- AF&PA report shows decrease in packaging paper shipments
- GreenMantra names new CEO
- Agilyx says Styrenyx technology reduces carbon footprint in styrene production
- SABIC’s Trucircle PE used for greenhouse roofing
- Hydro to add wire rod casthouse in Norway
- Hindalco to invest in copper, aluminum business in India
- Recycled steel price crosses $500 per ton threshold
- Smithers report looks at PCR plastic’s near-term prospects