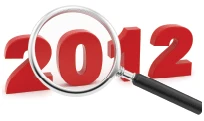
When asked to provide a summary of North American scrap markets for a November recycling conference in China, Michael Lion of Sims Metal Management Asia Ltd. chose the word “challenged.”
The crux of the challenge, according to Lion: “Too little scrap being chased by too many people.”
Across many recycling markets and throughout most of 2012, the enduring challenge for recyclers was finding enough scrap materials.
Mixed in for many recyclers (especially those in the paper sector) was temperamental price volatility and hiccups in demand that combined to create a year that, while not among the worst, also did not present the post-2008 rebound that many in the industry were hoping to see.
On Low Flame
Judging by steel production rates in the United States and globally, the ferrous scrap market remained one where furnaces were melting enough scrap to keep demand healthy (and prices in the $350 to $400 per ton range).
On the demand side of the ferrous scrap equation, steel output has been on a largely upward trajectory since the U.S. economy reached its low point in late 2008 and early 2009.
At the end of 2008 and in early 2009, steelmakers and the scrap processors who serve them experienced historic drop-offs in business, according to figures from the American Iron and Steel Institute (AISI), Washington, D.C.
AISI figures show that U.S. mills in one week in mid-February 2008 produced 2.1 million tons of steel and the capability utilization rate was 91.6 percent. Twelve months later, in the week ending Feb. 14, 2009, production was slashed in half, with slightly more than 1 million tons of steel being made. That represented a capability utilization (mill capacity) rate of 45.4 percent.
Throughout the rest of 2009 and into 2010, the weekly output and capacity rate figures climbed their way back up. By April 2012, output was just shy of 2 million tons and the capacity rate was just shy of 80 percent.
The summer and fall of 2012 saw the introduction of some negative influences, with pre-election uncertainty cited by many analysts and pundits as the reason for a manufacturing slump that affected steel output.
In the week ending Nov. 10, 2012, domestic raw steel production was 1.74 million net tons at a capability utilization rate of 70.7 percent. This was down from the 1.81 million tons produced in the week ending Nov. 10, 2011, when the capability utilization was 73 percent.
Also in mid-November, the AISI reported that for the month of September 2012, U.S. steel mills shipped 7.23 million net tons of steel, which was a 13.7 percent decrease from the 8.37 million net tons they had shipped in the month of August 2012. The figure also marked a 9 percent decrease from the 7.95 million net tons shipped in September 2011.
Export markets have continued to soak up their share of scrap in 2012. Turkey, the single largest export destination, produced more than 30 million metric tons of steel in the first 10 months of 2012, according to the WorldSteel Association, Brussels. This was up from 28.1 million metric tons in the same period last year and just 23.8 million metric tons produced in the first 10 months of 2010.
Those markets could be even more strained if the steel industry in China follows the wishes of some of the country’s central planners for a more “circular economy.” Professor Wang Yangzu of China’s Ministry of Environmental Protection, speaking at the Electronics Recycling Asia conference in Guangzhou, China, in November, said Chinese leaders were concerned that the country’s steelmakers use scrap as only 14 percent of their steelmaking feedstock, while steelmakers in European and North American nations use from 58 percent to 83 percent scrap.
China’s 14 percent rate amounted to 80 million tons of ferrous scrap melted in 2011, according to Wang, who added that China “plans to reach 200 million tons [melted] in the future.”
While some of the demand signs are encouraging, scrap processors reported throughout the year that lackluster construction and demolition work levels continued to hinder scrap flows. Many processors also decried the continued introduction of more shredder capacity in the United States (See “Too Much of a Good Thing,” p. 76 in the October 2012 issue of Recycling Today.)
The competitive shredder market in many parts of the country has resulted in plants running at just 20 percent to 50 percent of the number of hours they may have operated in 2007 or early 2008, according to some sources.
Still Glowing Red
While supply and demand factors caused several $50-per-month price swings in the ferrous scrap market, nonferrous traders continued to ride the roller coaster caused by several metals (but copper in particular) being investment products on the commodities market.
On the London Metal Exchange (LME), copper traded for as much as $8,655 per metric ton ($3.97 per pound) in February before falling to its low, thus far, of $7,251 per metric ton ($3.32 per pound) in June.
Fundamentally, copper-bearing scrap remains in demand, particularly in China, where annual copper production figures continue to climb.
At the 2012 CMRA (China Nonferrous Metals Industry Association Recycling Metal Branch) Recycling Metal International Forum in Beijing in November, Hank Qiu, a senior consultant with the China branch of the New York-based International Copper Association (ICA), noted that some 22.1 million metric tons of copper were consumed globally in 2011, with nearly 30 percent of that (9.75 million metric tons) consumed in China.
For the past 15 years, both state-owned enterprises and entrepreneurs have been furiously adding copper production capacity—much of it secondary copper production—to keep pace with that consumption.
As China embarks on its 12th Five-year Plan in 2013, more metals production is forecast, with sustainability initiatives such as the “circular economy” and “scientific development” favoring the ongoing use of scrap materials.
Industry analysts and reporters in the financial press, however, are beginning to wonder whether some Chinese building and infrastructure projects are beginning to outpace the actual growth in China’s middle class and urban migration.
Reports of “ghost cities”—entire residential and retail complexes without tenants and with rents set too high to realistically attract any—have caused some concern. Analysts point out that such complexes also exist in Spain, a country where banks and the economy ultimately suffered from such miscalculations.
Media organizations such as Bloomberg News also have been tracking what is being referred to as “shadow banking.” In China, this has taken the form of guaranteed-return trust funds with portfolios heavy on real estate. According to a mid-November Bloomberg.com news article, trusts “make up more than a quarter of [China’s] estimated $3.35 trillion in non-bank lending,” a UBS economist says.
Some of these trusts “are facing repayment risks,” the article continues. “As many as 15 percent of the nation’s $89.8 billion of property-linked trusts that come due by the end of 2013 may default, according to brokerage firm China International Capital Corp.”
Buyers and sellers of copper-bearing scrap will be watching closely for signs that the Chinese economy can navigate through these concerning issues.
Nonferrous scrap generation, as noted by Sims Metal Management’s Lion, remains a challenge for scrap processors. While sophisticated downstream auto shredding systems and ramped up electronics recycling capacity are helping to recover more copper-bearing scrap, reduced construction, demolition and renovation activity means less red metal is coming across scrap yard scales.
Summer Swoon
Just as metals traders experienced ups and downs in 2012, recyclers and traders who deal in scrap paper and plastic can look back on some difficult stretches.
Scrap paper markets took a plunge in pricing in the summer and early fall months in particular, with recyclers citing the disappearance of export orders as the leading culprit.
A combination of customs-related clog-ups at Chinese ports as well as production curtailments in China and North America caused what many perceived to be a demand-side price drop.
Supply throughout 2012 was seldom described in North America as anything better than “steady” and often referred to as “disappointing.” Newsprint and the old newspapers (ONP) grade continue to struggle, while printing and writing paper production and office grades scrap supplies also are languishing.
For several years, the Chinese export market has been the sponge to absorb recovered fiber, and the boxes in which China exports finished goods have been a steady source of supply.
A September 2012 presentation by Cao Zhenlei, the secretary general of the China Technical Association of the Paper Industry (CTAPI), pointed to the potential of limits being reached in China’s ability to keep absorbing scrap paper.
Cao said that while recycling remained part of the “guiding ideology” of China’s 12th Five-year Plan, so did a paper industry “changing from big to strong.”
He said China’s newsprint industry had “entered a steady declining period” and that printing and writing production capacity also was “in a difficult period.”
Contrarily, Cao said packaging paper and board “still has development opportunities” and finding new uses for paperboard in China “has remarkable potential.”
China’s tissue mills could offer another growth area for fiber, Cao said, since “domestic per-capita consumption still can be elevated.” He added that in 2012 and 2013, tissue production capacity would be increased “intensively.”
Plastics recyclers experienced a summer swoon in pricing as well, though demand for high-volume grades such as No. 1 PET (polyethylene terepthalate) bottles remained strong, according to sources.
Virgin production that exceeded demand was cited by these same sources for the price drop, but demand from domestic PET consumers has remained steady. As with recovered fiber, customs back-ups at Chinese ports made the shipment of some grades of plastic scrap difficult throughout much of 2012.
The firming of markets for engineering-grade plastics used by consumer electronics producers continued in 2012. Even as PET and HDPE (high-density polyethylene) prices drifted down in the summer, the biggest problem with engineering plastics such as ABS (acrylonitrile butadiene styrene) was finding enough to fill orders. “It seems like there is no ABS out there,” one trader told Recycling Today in July.
On the export side, Kingfa Sci. & Tech. Co. Ltd., based in Guangzhou, has risen in less than two decades to become the fourth largest plastics producer in the world, says Steven Tan, an associate director in the company’s circulation economical project department.
Tan said Kingfa will produce as much as 2 million metric tons of plastic in 2012. While much of that is virgin production, he said the company will produce 150,000 to 160,000 metric tons of recycled-content plastic using about 100,000 metric tons of plastic scrap.
Whether they most commonly ship just across the county line or across the Pacific Ocean, recyclers will benefit if company’s like Kingfa continue to seek large volumes of scrap.
The author is editorial director of Recycling Today and can be contacted at btaylor@gie.net.
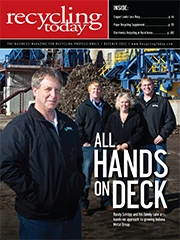
Explore the December 2012 Issue
Check out more from this issue and find your next story to read.
Latest from Recycling Today
- AF&PA report shows decrease in packaging paper shipments
- GreenMantra names new CEO
- Agilyx says Styrenyx technology reduces carbon footprint in styrene production
- SABIC’s Trucircle PE used for greenhouse roofing
- Hydro to add wire rod casthouse in Norway
- Hindalco to invest in copper, aluminum business in India
- Recycled steel price crosses $500 per ton threshold
- Smithers report looks at PCR plastic’s near-term prospects