When Joel Back, production manager for Gold Metal Recyclers, describes his company’s Dallas processing facility, he challenges anyone to “think of the harshest environment possible for a forklift, such as a construction site … and then multiply it by a factor of 10.” As if this statement was not enough, Back is compelled to offer justification for the claim.
“We transport and move large pieces of metal and concrete, often in 100-degree heat. We have huge cranes picking up busses and chunks of bridges. It’s a rough and dusty application, with slick spots, large potholes and ruts, and big pieces of rebar sticking out of the ground like landmines. And that’s on a good day.”
Dallas-based Gold Metal Recyclers is one of the largest metal recycling organizations in the United States. The company currently has large recycling yards in Houston and Dallas and smaller operations in various locations throughout Texas and New Mexico. The company’s Dallas processing yard encompasses 38 acres and ships approximately 200 to 300 trailers of scrap metal and concrete—about 1.5 billion tons—per week.
Avoiding Downtime
The processing yard operates seven days per week with two shifts per day. Forklifts are primarily used to transport scrap from trucks to balers or other types of processing machinery. Given the rough terrain and harsh environment the trucks must operate within, Back says the No. 1 challenge regarding his company’s forklift fleet is downtime.
“I’ve seen industry stats that put the average usage for forklifts at around 2,000 hours a year,” he says. “In our yard we operate 22 hours a day, seven days a week. We easily average 3,000 hours a year. My two biggest issues are overheating and busted steer axles,” Back says.
“The way I look at it is time spent on repairing steer axles and blowing out the radiators is time that my trucks are not being used.”
He says that if one of the forklifts that would normally be feeding one of the company’s balers is down, Gold Metal Recyclers can lose up to $1,000 per minute.
“I’m not in the forklift business; I’m in the production business,” Back says. “I don’t have time to worry about my trucks. I need to keep things moving. That’s why I’m always on the hunt for a more durable forklift that is readily available when I need it.”
Improving Performance
In 2010, Back met with Craig Lummus and Joe Bowers from the local Crown Lift Trucks branch. They spoke to him about a new internal combustion (IC) counterbalance forklift that is specifically designed to help customers move beyond the existing limitations of forklift performance.
Back liked what he heard, and after a successful demo period where he was able to put the truck to the test, he agreed to purchase two Crown C-5 Series cushion industrial forklifts.
The Crown C-5 Series is designed to push the limits of gas forklift performance and durability and to deliver advantages to owners and operators seeking improved power, strength, comfort, safety, service and uptime. It features an industrial engine, a proactive approach to engine cooling and radiator clearing via an on-demand cooling system and design innovations that improve operator visibility, comfort and productivity.
A main feature of the forklift that quickly caught Back’s attention was the cooling system that automatically clears itself of debris and is designed to provide precise cooling to effectively manage heat in intense and dirty environments. Each time a user starts the Crown C-5, the system’s radiator-clearing feature reverses the fan direction to dislodge any debris.
“The worst thing about our environment is the amount of dust in the air. Add in the fact that Dallas summer temperatures can reach 103 to 105 degrees, and it’s no surprise that overheating forklifts is such a big issue,” Back says.
“With our other forklifts,” he adds, “operators were manually blowing out the radiators at least once a day. Each blowout would take about 15 to 20 minutes and require that the forklifts be in the maintenance bay.
“The other big selling point for me was the durability of the forklift,” Back continues. “The abusive landscape of our processing yard definitely takes a toll on the forklifts. Damaged steer axles and transmissions are common and costly occurrences I experience with my other forklifts—often as a result of the rebar sticking out of scrap concrete.”
Reducing the Tally
Two years after buying his first two Crown forklifts, Back now has six C-5s in his fleet and is pleased with their performance.
“On average, I have about 8,000 hours on each of the forklifts, and they are performing really well. My maintenance costs for the C-5s are comparably lower than my other forklifts,” Back says. “I haven’t had any overheating issues or axle or brake problems. The same can’t be said for the other forklifts in my fleet. With these other forklifts, I’ve had to replace four transmissions in the last nine months, which are about $3,300 each; I’ve had to replace four steer axles in the last 12 months, which are about $2,700 each; and I typically replace the brakes on competitor forklifts every 15 to 16 months, which costs about $700 each.”
Back adds that he’s also happy with the level of attention he receives from Crown’s service team.
“Our Crown service technician, Steve Hill, is very knowledgeable and always has the right solution. Also, whenever I have a question or issue, Lummus and Bowers are always quick to respond with an answer,” he says.
“For instance,” Back continues, “when we received the first two Crown C-5 forklifts, we realized that modifications would need to be made to accommodate unique elements of our environment. Crown engineers worked with us to come up with a solution.”
As far as Back is concerned, the Crown C-5 has passed the test.
“Our processing yard is probably the worst application for a forklift, which makes it the perfect proving ground,” he says. “Five thousand hours in our scrap yard will let you know exactly how good your forklift is, and the Crown C-5 has proven that it is more than capable of meeting the challenge.”
This article was submitted on behalf of Crown, www.crown.com.
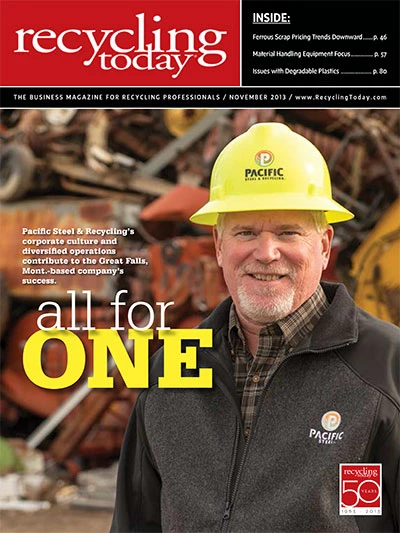
Explore the November 2013 Issue
Check out more from this issue and find your next story to read.
Latest from Recycling Today
- Aqua Metals secures $1.5M loan, reports operational strides
- AF&PA urges veto of NY bill
- Aluminum Association includes recycling among 2025 policy priorities
- AISI applauds waterways spending bill
- Lux Research questions hydrogen’s transportation role
- Sonoco selling thermoformed, flexible packaging business to Toppan for $1.8B
- ReMA offers Superfund informational reports
- Hyster-Yale commits to US production