Conveyors are one of the earliest forms of automation and possibly one of the best productivity enhancing tools available in the recycling industry today. These machines have dramatically increased production flows and bottom lines for many companies in the recycling industry.
Today, elaborate separation systems are being added to existing operations, and conveyor belts are major components of these systems.
Stay Safe
The conveyor is a great tool because it can move material efficiently and safely. But, as with other moving machinery within a recycling facility, conveyors are safe only when used correctly.
The U.S. Bureau of Labor Statistics reports more than 50 workplace fatalities per year in which conveyors are the primary source of injury.
However, conveyor systems are generally safer than other material handling alternatives if they are well-designed, properly maintained and safely operated.
Conveyors come in many shapes and sizes, and each is designed to do a specific job. For those reasons, it is not easy to sum up conveyor safety in a few sentences. However, with the right processes, design and training, recycling companies can reduce and eliminate injuries at their facilities and their related costs.
As a safety professional and someone who has worked in the industry for many years, I feel that we owe safety and awareness training to the individuals who work around this equipment. With this article I want to focus on what recycling facility owners, managers and supervisors must do to keep personnel who work with and around conveyor systems safe while they are on the job.
The Basics
Every facility owner must share 12 basic rules with his or her employees. These are guidelines that no operation using a conveyor should ignore. Adhering to these rules is the start, but certainly not the end, of successful conveyor safety programs. (A simple Web search will reveal additional information.) The 12 basic rules of conveyor safety are:
- Do not service a conveyor until the motor disconnect is locked out.
- Service the conveyor using only authorized maintenance personnel.
- Keep clothing, fingers, hair and other parts of the body away from conveyor.
- Do not climb, step, sit or ride on the conveyor at any time.
- Do not load the conveyor outside of the design limits.
- Do not remove or alter conveyor guards or safety divides.
- Know the location and function of all stop and start controls.
- Keep all stopping and starting control devices free from obstructions.
- All personnel must be clear of the conveyor before starting.
- Operate the conveyor with trained personnel only.
- Keep the area around conveyors clear of obstructions.
- Report all unsafe practices to the facility supervisor.
Follow the Rules
It is important to know and remember that a large majority of rules and regulations in the safety business are written in the blood of others who have come before us. This is to say that through other people’s mistakes, mishaps, accidents or injuries, we get new safety rules and regulations designed to keep us out of harm’s way.
No one I’ve ever met likes to be contained by rules and regulations; however, it is my business and job as a safety outreach trainer to explain in a sensible manner why and how people should act and react around the potential hazards in their workplaces. Let’s take a closer look at each of these safety rules and think about why they need to be adhered to.
Lockout/tagout/try out [Rule No. 1] is perhaps one of the most important concepts for employees who work around conveyors (and other stored energy hazards) to understand. Failure to have and follow a lockout/tagout/try out program is to set yourself, your employees and your company up for an eventual injury.
Remember that only authorized personnel [Rule No. 2] are allowed to service the equipment. Unauthorized service personnel do not have the education, training or experience to safely work on conveyors.
Nip points, pinch points and extended shafts can all be potential grab areas. By this I mean that they can grab on to hands, fingers, hair, rings, watches or loose clothing. Be sure to educate employees on the location of these hazard areas and teach them to keep the above named items and any other body parts away from these points at all times [Rule No. 3].
Oftentimes we find temporary employees working around conveyor systems in our industry. They are usually picking nonconforming material from the flow, or they might be assigned to a cleanup crew. Many of these “temps” have never worked around moving conveyors, so it is very important that a safety program address these employees in addition to a facility’s regular employees. Teach them the hazards associated with conveyor systems and to never climb, step, sit or ride on conveyors [Rule No. 4].
All equipment has design limitations. Because conveyor systems are an integral part of an operation, it is important not to overloaded them [Rule No. 5]. Staying within the design limits will prevent jams and breakdowns. These jams and breakdowns inevitably stress the entire operation and cause individual employees to make bad decisions, which can result in accidents or injuries to the workforce.
Proper machine guarding is one of the most overlooked pieces to a safely operating conveyor system. Guards, barriers or devices that are designed to keep a person from getting too close to a nip point or from placing a body part into a nip point are mandatory. If the guard or awareness barrier is missing, then the machine should not be in operation. Don’t remove or alter conveyor guards or safety divides [Rule No. 6]. Machine guarding, as with lockout/tag-out/try out is considered a “blood rule” in the safety business. That is to say that if one fails to follow the procedures, then the possibility of bloodshed is very real.
Training is essential for all personnel who work with conveyors. A proper understanding of the mechanics of the system is knowledge that must be shared with employees who work in those areas. Training must include the recognition of potential hazards, how to properly de-energize the system and the importance of good housekeeping practices [Rules Nos. 7 through 11]. This important piece to a conveyor safety program must not be overlooked. It is going to be through a solid training and education program that employees will excel at their jobs. This training and education will enable them to make the best possible practical- and safety-minded decisions as they go about their daily jobs.
Rule No. 12 is the foundation of all good safety programs: Report all unsafe practices to the supervisor. Having open, two-way communication within the workforce is vital to the success of the operation. Employees have to be able to communicate safety issues to supervisors, and supervisors must be able to offer feedback and solutions to the problems found on the job site. Open communication is the water and sunlight that will enable a safety program to flourish and grow.
Conveyors are an integral part of a recycling business, and a safety program must not overlook this important area.
The author is safety outreach manager for the Institute of Scrap Recycling Industries Inc. (ISRI), Washington, D.C., and can be reached at tonysmith@isri.org.
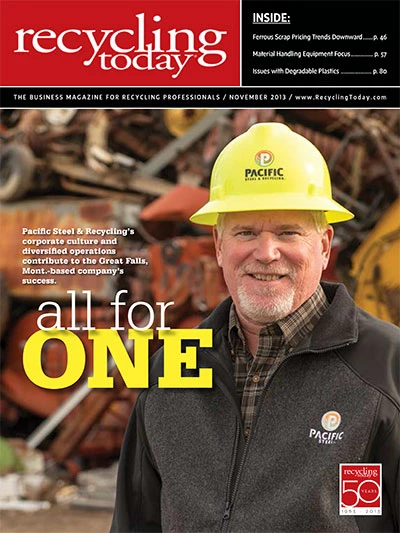
Explore the November 2013 Issue
Check out more from this issue and find your next story to read.
Latest from Recycling Today
- Aqua Metals secures $1.5M loan, reports operational strides
- AF&PA urges veto of NY bill
- Aluminum Association includes recycling among 2025 policy priorities
- AISI applauds waterways spending bill
- Lux Research questions hydrogen’s transportation role
- Sonoco selling thermoformed, flexible packaging business to Toppan for $1.8B
- ReMA offers Superfund informational reports
- Hyster-Yale commits to US production