Spurred on in part by lofty metals prices, scrap recyclers in North America seem much more willing to process and upgrade scrap wire and cable than they may have been 10 years ago.
The desired result when scrap recyclers process wire and cable is the production of clean, upgraded copper and aluminum chops with a high purity rate.
If the metal being separated is cleaner as a result, it might follow that the chopped plastic coatings are largely free of metal and thus also may have a higher value.
In the United States, however, recyclers are largely not finding that to be the case, as even cleaner polyvinyl chloride (PVC) plastic can be difficult to market, especially if it contains lead.
Volume Considerations
Determining how much wire and cable is being processed in the United States versus being baled and shipped to an export destination is not necessarily distinguishable by examining industry data.
Export figures maintained by the U.S. Census Bureau and re-published by the U.S. Geological Survey (USGS, http://minerals.usgs.gov) do not clarify in precisely what form scrap leaves the country, so it is hard to draw a conclusive picture. However, those figures do show that unalloyed copper scrap volumes to China increased from 2001 to 2010.
In 2001, some 156,000 metric tons of unalloyed copper scrap was sent from the United States to China, followed by just 122,000 metric tons in 2002.
By 2009, that number had risen to 190,000 metric tons and then 247,000 metric tons in 2010. Throughout that time, recyclers in America met the domestic needs for clean, chopped copper.
Many recyclers, as well as most wire processing equipment suppliers, indicate the higher pricing of the last several years has made additional processing steps worthwhile for them, whether they ship the resulting clean copper and aluminum chops domestically or overseas.
But when asked about the plastic coating, the response can be less enthusiastic. “There is very little demand that I know of for using that material,” says Jeffrey Mallin, president of wire and cable processor Mallin Bros. Co. Inc., Kansas City, Mo.
Mallin says export brokers occasionally make inquiries and ask for samples, but these inquiries have not led to any long-term relationships with a consumer for the material. Over the course of the decades that Mallin Bros. Co. has been processing wire, “a few cement companies might express an interest,” says Mallin, but this end market also is sporadic.
Manitoba Corp., Lancaster, N.Y., runs two chopping lines, according to company president Brian Shine. The lines run several different types of material, including transformer coils.
He says, though, that he does sometimes have buyers for the “tailings,” or nonmetallic portion. “There is more interest than there had been a few years ago,” he comments. The tailings can be exported “as a low- or nominal-value material. There are about two or three entities that chase it,” says Shine.
Any plastic scrap-to-fuel energy makers who may be out there have not yet outbid these export brokers, says Shine. “They’re quoting it,” he says of fuel makers, “but at a cost that doesn’t really seem to make sense. As an option it’s better than the landfill, but they’d still charge us a cost. For export, we’re getting a nominal fee.”
On the equipment vendor side, Bobby Childers of Wendt Corp., Tonawanda, N.Y., also mentions cement kilns as potential customers, noting that some in particular like the material if it can be processed into a fuel pellet form.
Wendt, which offers wire processing equipment made by France’s MTB Recycling and separation equipment made by Hamos GmbH of Germany, says environmental regulations focused on the handling of PVC limit the creation of some markets in the United States that may exist in other parts of the world.
Another barrier to materials recycling markets in the U.S. can be the amount of labor it takes to separate the different types of cable and wire being processed by the type of coating or color.
Plastic reprocessors typically want to create a product that is uniform by resin and color. Deploying people to help sort this all out may be practical in parts of the developing world but is cost-prohibitive in the U.S.
Regarding energy applications, PVC emissions are a concern throughout the world, with the U.S. Environmental Protection Agency (EPA) having researched and offered guidance on the topic in a report released in 2008.
A Closer Look
Released by the U.S. EPA in June 2008, “Wire and Cable Insulation and Jacketing: Life Cycle Assessments for Selected Applications” was prepared by Abt Associates Inc., Cambridge, Mass., for the EPA’s Design for the Environment (DfE) Wire and Cable Partnership.
The partnership represented a cross-section of members, including manufacturers such as DuPont, Judd Wire and AlphaGary; trade groups such as the American Chemistry Council and the Society of the Plastics Industry; and scrap recycler Richard Shine from Manitoba Corp.
Although boosting recycling was not necessarily the foremost goal of the study, “Because of the large quantity of cable put into commerce every year, choosing environmentally preferable materials could have a broad impact on public health and the environment,” the study’s authors state in the introduction.
In a flow chart outlining the “end of life” stage of wire and cable products, landfilling and incineration are listed as possibilities, along with “cable chopping.” The “cable chopping” box also points to a “thermoplastics recycling” stage as another potential end-of-life option for the material.
At that time, the study’s authors concluded that while this stage was potentially part of a life-cycle flow chart, in reality little of it was occurring. “The percentage of cable insulation and jacketing resins going to recycling was another source of substantial uncertainty in the end-of-life stage,” the study says. “Using an upper estimate based on data from Europe (20 percent of recovered wire and cable resins are recycled), a range of zero percent to 20 percent of the cable resins was modeled as being recycled.”
The authors had little trouble distinguishing that, while most of the metal was recycled, the same could not be said for the plastic jackets. “PVC waste is the top contributing material flow for both [lead-bearing and lead-free] cables, representing 46 percent of the impact for each cable.”
While all aspects of wire and cable production were examined, including the production of the raw materials used, landfilling was cited as a problem area that merited attention if the life cycle scorecard of wire jackets or coating containing lead is to be improved. This was especially noted in regard to health impacts.
“Municipal solid waste landfilling was the top contributing process to the potential public noncancer toxicity and potential aquatic eco-toxicity impact categories in the baseline case,” says the study. “Lead from landfilling was the top flow contributing to the potential public noncancer toxicity and potential aquatic eco-toxicity impact categories.”
A Second Life
Western Europe has a reputation in North America of having layers of regulations in place that are at least as difficult to navigate as what is encountered in the United States or Canada.
From the aspect of recycling wire and cable exteriors, however, the climate in Europe may be a little friendlier. “I talk to recyclers in other parts of the world, including Europe, and they process that material and make sandals or some other product,” says Childers of Wendt Corp.
Among the European companies promoting wire coating recycling on their websites is Borealis AG, Linz, Austria.
The company’s primary business is as a manufacturer of polyolefins and other plastic resins. Among the services it touts on its website (www.borealisgroup.com), however, is “effective recycling solutions” for “cable waste plastic management.”
Along with the Abu Dhabi National Oil Co. (ADNOC), Borealis created joint venture company Borouge (www.borouge.com), based in Abu Dhabi, United Arab Emirates, to conduct research and develop recycling methods for the material.
“Recycling of plastic components is encouraged by authorities in Europe as disposal in landfills is not accepted,” notes a brochure published by the two companies.
Regarding the process developed by Borouge, “Waste that is generated during cable manufacturing is sorted at the source and either reprocessed or recycled for alternative applications,” states the brochure.
“Waste from end-of-life and scrapped cables that is collected from different sources constitute a broad mix of cable types and material components. A presorting of these cables is made as a first step,” according to Borouge, “then granulation and separation of the plastics from the metal occurs.”
Separation of the different types of plastics is the next step, with this being “made by a sink/float technique where heavy plastics sink in water and lighter plastics float,” the brochure continues. “A new technology that combines the sink/float techniques with a gravimetric separation allows for a further separation of metal from the light plastic making a total separation yield of 99 percent to 99.9 percent metal. This means that the purity of the light plastics is high and attractive for energy recovery or recycling,” states Borouge.
The joint venture partners note that in addition to PVC jackets, “polyethylene, either in cross-linked (XLPE) or thermoplastic (PE) form,” are the other common types of wire claddings.
“The PVC fraction can be remelted and processed to new products,” states the brochure, though “the recycled material is typically used in applications with lower quality requirements.”
Regarding the XLPE material, “It cannot be reprocessed as a 100 percent ingredient. However, it has been shown that a mix between virgin polyethylene and up to 60 percent XLPE waste gives a mixture that can be reprocessed [that] can be used, for example, in injection-molded articles.”
Energy recovery is also noted as an end-of-life option. “As the new technique for cable waste separation produces a very clean, light fraction, it can be used in such applications as complementary fuel in district heating plants or in cement kilns.”
The author is editorial director of Recycling Today and can be contacted at btaylor@gie.net.
Get curated news on YOUR industry.
Enter your email to receive our newsletters.
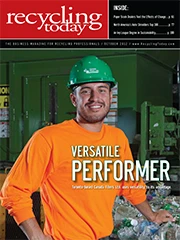
Explore the October 2012 Issue
Check out more from this issue and find your next story to read.
Latest from Recycling Today
- Astera runs into NIMBY concerns in Colorado
- ReMA opposes European efforts seeking export restrictions for recyclables
- Fresh Perspective: Raj Bagaria
- Saica announces plans for second US site
- Update: Novelis produces first aluminum coil made fully from recycled end-of-life automotive scrap
- Aimplas doubles online course offerings
- Radius to be acquired by Toyota subsidiary
- Algoma EAF to start in April