> PAPER
RISI Outlines Paper Pricing Changes
Forest products information and media company RISI Inc., Bedford, Mass., has announced that its Pulp & Paper Week publication will serve as the home of Official Board Markets (OBM) paper stock prices starting Oct. 5, 2012.
According to Todd Petracek, RISI vice president of news and prices, RISI’s acquisition of OBM in May of 2012 was followed by discussions with readers and internal research to determine the best way to combine the long-time pricing models offered by both Pulp & Paper Week (known as PPI pricing)and OBM (also known as The Yellow Sheet).
“We are going to integrate OBM into Pulp & Paper Week,” says Petracek, who indicates subscribers of both publications will receive the newly combined periodical. “There will be a transition period for three months, October through December, when readers will see one page with PPI prices and one page with the OBM prices.”
This carries the possibility of some grades having two different prices during this time frame, but Petracek says RISI determined it was important to provide continuity to readers who may have contracts pegged to either of the two published prices.
Starting Jan. 5, 2013, prices will be consolidated, says Petracek. “Roughly, for the bulk grades we will be keeping the OBM prices [and regional breakdowns], while the PPI pricing stays in place for the high grades and pulp substitutes,” he comments. “We’ve done that to try to minimize the disruptions, since OBM is used much more heavily on the bulk grades for contracts.”
Price gathering methodologies will remain similar, Petracek says, though the merger will allow RISI to provide additional staffing during that process. “We now have an editorial team that can make more contacts and extract more data out of the market,” Petracek adds.
> METALS
A&A Midwest Expands Scrap Service in Las Vegas
A&A Midwest Auto Wrecking, headquartered in the Chicago area, has opened a new end-of-life vehicle processing center in the Las Vegas area. (That operation, which also has operated under the AAEQ name, was profiled in Recycling Today in May 2010. The article is available at www.RecyclingToday.com/aaeq-cover-profile-may-2010.aspx.)
“Though a vehicle may no longer be usable to the owner, A&A Midwest Auto Wrecking sees great value in the parts that can be disassembled and reused,” says Scott Stolberg, president and CEO of the company. “We buy used vehicles and parts, sell used auto parts for remanufacturing and export used vehicles and parts. Plus, we offer top dollar whether the vehicles are running or not.”
To maximize its operations, Stolberg says A&A Midwest Auto Wrecking recently purchased a Genesis shear and a Caterpillar material handler.
He adds that the addition of auto wrecking services in Las Vegas adds capacity to the company’s auto export salvage business in Blue Island, Ill.
A&A Midwest Auto Wrecking estimates that it will process approximately 25 vehicles per month from its Las Vegas operations, shipping one or more containers to developing countries.
> METALS
CME Group to Launch Ferrous Scrap Futures
Chicago-based CME Group has announced plans to launch the first ferrous scrap futures contract in the United States. As of Sept. 10, 2012, CME began trading futures for U.S. Midwest No. 1 busheling ferrous scrap. The CME says the contract is listed by and subject to the rules of New York Mercantile Exchange (NYMEX).
“Today, the global steel industry relies on the U.S. to supply more than 20 percent of its ferrous scrap needs, making it the biggest exporter of this important raw material to the industry,” said Harriet Hunnable, CME Group managing director, metals products, at the time of the announcement in mid-August. “Continued demand for U.S. scrap and increased price volatility in ferrous products underscore the need for an effective tool to enable price risk management throughout the entire supply chain.”
The introduction of U.S. Midwest scrap futures extends CME Group’s suite of ferrous products in the United States beyond its current contracts for U.S. Midwest domestic hot-rolled coil steel futures and options.
CME says more than 60 percent of the steel produced in the U.S. currently is based on ferrous scrap.
The contract is settled against American Metal Market’s (AMM’s) new U.S. Midwest Ferrous Scrap Index and is available for trading on CME Globex and for submission for clearing through CME ClearPort beginning with the October 2012 contract month.
> PLASTICS
Companies to Recycle Marcellus Region Well Liners
The Pennsylvania Recycling Markets Center Inc. (RMC) has formed a new business partnership to collect and recycle plastic well pad liners from gas drilling sites in the Marcellus Shale region of Pennsylvania.
“This is a first-of-its-kind venture that will produce major and dramatic benefits for Pennsylvania in addition to new jobs and growth for the companies directly,” says RMC Executive Director Robert Bylone Jr.
Partners in the venture are WellSpring Environmental Services LLC, headquartered in Orwigsburg, Pa., and Ultra-Poly Corp., based in Portland, Pa. Both companies are members of the RMC’s Center of Excellence, a network that includes recycled materials processors and end users of recycled materials.
“The new recycling venture with WellSpring and Ultra-Poly is expected to take at least 20 million pounds a year of plastic well pad liner material out of the waste stream and turn it into useful new products,” Bylone says.
An estimated 100 million pounds of high-density plastic were used for well pad liners by drillers in the Marcellus Shale region in 2011. Currently, most of that material is disposed of in landfills when it needs to be replaced or removed.
Ultra-Poly, a North American recycler of polyethylene and polypropylene plastic, has designed a way to process the liner material and has built a recycling plant specifically for that purpose.
“We are supplying the recycled plastic to several existing customers, including Axion International, which turns the material into composite railroad ties and other composite building components,” says David LaFiura, vice president of Ultra-Poly. “The market is potentially huge; we have developed an environmentally responsible method, we are the only company doing this and we are in position to recycle as much of the liner material as we can get.”
Similarly, WellSpring says it has developed equipment for separating well pad liners on site so the pieces from one well site can be trucked away for recycling in a single trailer load. In the past, excavators were used to rip well pad liners into large sections, and it typically took eight to 10 trips with roll-off containers to transport the sections from a single site to a landfill for disposal.
“There’s not one well pad in Pennsylvania where this new approach doesn’t make sense,” says Jonas Kreitzer, president of WellSpring. “We can do liner removal more efficiently, at less cost, while cutting down truck traffic, protecting the environment, and generating commercially reusable material.”
An estimated 20,000 pounds of liner material is used per drilling site. The Pennsylvania Department of Environmental Protection (DEP) issued 3,510 Marcellus Shale well permits in 2011 and another 1,243 through mid-May of this year. The department has already issued permits to the two companies for the process.
“We think this will have tremendous application and value for the shale gas industry in Pennsylvania as well as elsewhere,” says Bylone. “It also gives a very big boost to our recycling industry in Pennsylvania, which is growing by leaps and bounds. In addition, it will save landfill space and will cut down on truck traffic, which everyone applauds.”
Bylone also says the recycling process used for well site liners may be applicable to recycling agricultural film plastic.
> ELECTRONICS
NAID Task Force to Examine Data Destruction on SSDs
The Phoenix-based National Association for Information Destruction (NAID) has announced the formation of a task force to develop a standard for “reasonable” destruction of information stored on solid state drives (SSDs). This task force, consisting of electronic data destruction industry professionals and outside consultants, will consider the attendant technology, knowledge, expense and likelihood of accessing or reconstructing meaningful data, according to NAID.
“Every data protection regulation in the developed world is based on the principle of reasonableness, a standard which can only be determined by understanding the risks and technology,” says NAID Chief Compliance Officer Holly Vandervort. “This task force will attempt to develop a body of knowledge that consumers can use to make informed decisions.”
The task force will establish the reasonableness of physical destruction as well as sanitization of SSDs. Sanitization involves the overwriting or removal of data on hard drives in a manner that allows the device to be reused.
In addition, the task force will evaluate methods, procedures and quality controls used in the process. Ultimately, the project will lead to a NAID whitepaper defending the consensus achieved by the task force and providing information for data custodians to form their own reasonableness standards for the destruction of information on SSDs.
> PLASTICS
APR Releases Document on Full-Sleeve Labels on PET Bottles
The Association of Postconsumer Plastic Recyclers (APR), Washington, D.C., has released a guidance document that provides information on dealing with the growing issue of full-body-sleeve labels on PET (polyethylene terephthalate) bottles.
According to the APR, “Sleeve Label Substrate for PET Bottles Critical Guidance Document” addresses several key label design issues that affect the removal of the labels in the recycling process and quantifies the effects of label residue on PET bottle recycling. The document is designed to help packaging decision makers select label substrates and materials that are more compatible with PET bottle recycling.
The APR says its new guidance protocol streamlines testing for full body labels on PET bottles, omitting some tests as irrelevant and expanding on other subjects in the Critical Guidance Document to reduce testing cost and increase protocol usage.
Dave Cornell, APR technical director, says, “Full-sleeve labels are growing in popularity with brand companies. The labels are a mixed blessing for PET reclaimers, as the labels are free of adhesive and generally mean unpigmented plastic bottles, but new problems are created, such as proper identification of the bottle resin and removal of the label from the bottle and recycle product.” He adds, “This protocol begins the effort to address all of the issues.”
The new guidance document is based, in part, on comprehensive examination of the effects of label substrate choices as investigated by Plastic Forming Enterprises under contract to APR, the group says.
APR’s Critical Guidance Documents are part of its larger Champions for Change Program in which the APR works with other industries to achieve higher quality and more economical recyclate.
The National Association for PET Container Resources (NAPCOR), based in Sonoma, Calif., has endorsed the guidance document. According to NAPCOR, full-wrap shrink labels affect the PET reclamation process at several junctures: Their full coverage impairs resin identification by automated equipment used to sort recyclables by material type, and the full-wrap shrink labels cannot be removed from containers by traditional prewash technology. However, the most problematic of these labels are those that sink in water along with the PET during processing, thus creating more contamination than can be acceptably removed during the conventional PET recycling process. (More detail can be found in NAPCOR’s position statement on this topic, www.napcor.com/pdf/NAPCORfullwrap.pdf.)
“NAPCOR became squarely involved in this issue, not just because of the adverse economic impacts these labels are currently having on PET reclaimers, but also because of their potential for rapid growth across brands and product categories,” says Dennis Sabourin, NAPCOR executive director. NAPCOR says it is communicating with several of the largest brands using this labeling technology to help them understand the scope of the problem and to find recycling-compatible alternatives.
“We see a tremendous amount of concern regarding the presence of full sleeve labels on PET bottles,” says Steve Alexander, APR president. “The vast majority of PET reclaimers report that the labels are a serious problem for recycling.”
Alexander continues, “Most PET reclaimers, drawing from many sources of raw material and with a variety of process designs, find the sleeve labels are a serious economic detriment. Label density is the one characteristic that testing shows can lead to removing label contamination from PET recycling. Labels that sink in water after hot water washing are labels that cause serious trouble.”
He concludes, “We are optimistic that this enhanced protocol provides packaging designers the clear guidance to mitigate this contamination problem.”
> METALS
UBC Recycling Rate Tops 65 Percent
The Aluminum Association, the Can Manufacturers Institute (CMI) and the Institute of Scrap Recycling Industries (ISRI) have announced that the domestic recycling rate for aluminum beverage cans (UBC) reached 65.1 percent in 2011, a sharp increase from 2010’s recycling rate of 58.1 percent.
“We are excited to have made strong progress toward our goal to increase the aluminum can recycling rate to 75 percent,” says Heidi Brock, president of the Aluminum Association, “but we need the help of every American to continue to raise the rate. There is much more work still to be done here in the United States to reach our goal by 2015.”
Robert Budway, CMI president, says, “We are thrilled about the continued growth in aluminum can recycling rates. Metal can be used forever if we keep it out of landfills, and higher recycling rates benefit the economy, people and the planet.”
Joe Pickard, chief economist at ISRI, adds, “The scrap recycling industry is dedicated to meeting manufacturing’s vital raw materials needs, including the growing demand for recycled aluminum and used beverage containers (UBCs) while serving as an environmental steward. In 2011, aluminum recovered from purchased scrap in the United States increased 8 percent to more than 3 million metric tons, while at the same time total U.S. aluminum scrap exports rose 12 percent to more than 2.1 million tons.”
> TIRES
Lehigh Technologies Receives $16 Million in Financing
Lehigh Technologies Inc., an Atlanta-based tire recycling company, has completed $16 million in financing, securing investments from a number of venture capital firms led by Leaf Clean Energy, including Kleiner Perkins Caufield Byers, Index Ventures and NGP Energy Technology Partners.
According to Lehigh, the funding will go toward expanding its geographic reach and research and development initiatives, including strengthening its ability to meet the commercial demand for its micronized rubber powder (MRP) technology.
Lehigh’s MRP technology recycles end-of-life tires and post-industrial rubber into new materials that are incorporated into high-performance tires, consumer and industrial plastics goods, asphalt and coatings and construction materials.
“Support from our financing partners enables our continued growth as we make major advancements in micronized rubber powder technology,” says Alan Barton, chief executive officer of Lehigh Technologies. “We are working with customers to support their use of MRP at increasingly higher levels as well as developing new end uses for this sustainable material. Our new funding will support our technology roadmap as well as facilitate expansion into new geographies.”
Ellen Pao of Kleiner Perkins Caufield Byers and board member of Lehigh Technologies says, “Our second investment in Lehigh Technologies is a testament to the company’s ability to deliver technology-based innovation and create new market opportunities. We believe Lehigh’s approach breaks existing paradigms of how we perceive post-consumer and post-industrial materials, fundamentally changing how they can be used in the production of new products.”
Matthew Fedors, Leaf Clean Energy vice president, adds, “A key element that motivates industrial customers to buy sustainable materials is to provide a solution that does not sacrifice quality, safety, cost or performance of the end product. Throughout its market segments, Lehigh’s technology position allows the company to achieve this goal.”
> TIRES
New Research Foundation Focuses on Use of Recycled Tires in Asphalt
Experts on rubberized asphalt processes have joined together to establish the Rubberized Asphalt Foundation (RAF), a research foundation dedicated to the science and practical use of recycled tire rubber in asphalt.
Asphalt rubber is a sustainable alternative to natural resources that provides many advantages beyond the obvious environmental benefits of recycling scrap tires,” says George Way, chairman of RAF and retired chief pavement design engineer for the Arizona Department of Transportation. “This is a cause we all believe in, and this foundation is the evolution of many years of work by individuals and organizations who are dedicated to developing rubberized asphalt for broad use.”
More information is available at www.ra-foundation.org.
> PAPER
Catalyst Paper Closes Arizona Recycled Paper Mill
Catalyst Paper, based in Richmond, British Columbia, Canada, has announced the permanent closing of its recycled paper mill in Snowflake, Ariz. Catalyst says the mill’s closure follows extensive efforts to improve the operation’s financial performance in the face of intense supply input and market pressures.
The company also has closed its Apache Railway Co. subsidiary.
“The decision to close Snowflake is an extraordinarily difficult one given the exceptional effort that employees, unions and public officials have given to address the unique challenges at this mill,” Kevin Clarke, Catalyst president and CEO, said at the time of the closure announcement in late July. “We understand and regret the difficult impact within the Snowflake community and surrounding region created by closure of the mill. I want to acknowledge and thank all who have given us their unwavering support and cooperation.” He added, “There were no stones left unturned.”
Since acquiring the mill in 2008, Catalyst says it had implemented a number of measures to address market challenges and input cost pressures. These steps included the production of higher-value specialty paper grades at what was formerly a newsprint-only mill; capital investment; productivity, quality and service improvements; full leverage of the mill’s environmental attributes; and competitive labor agreements. Catalyst says it also had explored a range of alternatives, including attempting to sell the mill on a going-concern basis.
However, with newsprint demand down more than 10 percent annually since the end of 2008, old newspapers (ONP) price volatility and higher freight, the mill’s profitability could not be restored, according to Catalyst. ONP prices have increased approximately 163 percent since 2009.
> METALS
SMS Completes Deal for All Star Metals, All Star Shredding
Scrap Metal Services LLC (SMS), a metals recycling company based in Burnham, Ill., has acquired the ship recycling company All Star Metals LLC (ASM) and All Star Shredding LLC (AS), both operating in Brownsville, Texas.
Nikhil Shah founded the ship recycling company ASM in 2003. All Star Shredding operates a Newell 98-104 auto shredder, which processes obsolete and industrial scrap.
Both companies being acquired are managed by Nikhil and by Nirav and Lopa Shah, all of whom will join SMS’ management team and continue with their management roles.
“We are extremely excited about adding the Shah family to our management team as well as their entire organization,” says Jeffrey Gertler CEO of SMS. “The addition of ASM and AS will enhance the products that we are able to offer our ferrous consumers as well as create a platform to grow our business in the Southwest region.”
Richard Gertler, SMS COO, says, “The acquisition of ASM and AS will allow SMS the opportunity to expand our scrap service capabilities to our customers in a safe and environmentally compliant fashion in a much broader geographic area. ASM and AS have one of the highest environmental and safety ratings in the country and mirror SMS’ safety responsibility to its employees and the environment.”
Shah adds, “The synergies between SMS and ourselves will allow us to grow together in an efficient manner. Our stories of how we started, our vision of how we will grow and our ability to maximize profits in today’s scrap market, is what all of us see eye to eye on.”
With the addition of ASM and AS, SMS operates seven commercial facilities and three mill services facilities in the United States.
> MUNICIPAL
CVP, Solid Waste Agency of Lake County Partner on Education Effort
The Curbside Value Partnership (CVP), Arlington, Va., has announced the creation of a partnership with the Solid Waste Agency of Lake County (SWALCO), Gurnee, Ill. The partnership will look at steps to increase recycling in Lake County, Ill., beginning this fall.
CVP is a national, invitation-only program designed to help communities grow their curbside programs through education. Since 2005, CVP has partnered with 29 communities and four states to develop, execute and measure education campaigns.
SWALCO is a municipal joint-action agency that serves 41 municipalities, including the Lake County and Naval Station Great Lakes, which includes about 230,000 households.
“CVP and SWALCO are looking forward to helping consumers get more material into their recycling containers,” says Craig Cookson, CVP board member and director of sustainability and recycling, plastics division, for the American Chemistry Council.
As part of the partnership with CVP, SWALCO and its members will implement and measure a grassroots education campaign that is designed to increase awareness for curbside recycling, grow participation and boost volume. The campaign is expected to launch this fall with planning already under way. Education tactics for the campaign are expected to include marketing, an enhanced Web and social media presence, advertising and community-level outreach.
“SWALCO is proud to partner with CVP for this important education campaign,” says Walter Willis, SWALCO executive director. “We’re particularly interested in collaborating on an effective education campaign that will help us hit the 60 percent diversion goal we set for ourselves.”
Officials plan to launch the campaign this fall.
> AUTOMOTIVE
Auto Recycling Associations Develop Single Accreditation Standard
The Automotive Recyclers Association (ARA), the Automotive Recyclers of Canada (ARC) and United Recycler’s Group (URG) have announced plans to centralize their respective accreditation programs into a single accreditation and certification standard for automotive recyclers.
“This will serve to bring increased industry unification and recognition to professional automotive recyclers who operate at the highest level of the industry,” says Michael Wilson, ARA CEO. “We look to this as a preeminent accreditation program that would be a model for other international automotive recycling organizations as well as to governments of countries across the globe.”
Under the new program, ARA’s CAR (Certified Automotive Recycler) and Gold Seal programs will be joined by URG’s 8000 program and the ARC’s Canadian Auto Recyclers’ Environmental Code (CAREC) to advance excellence in practices and standards, the groups say.
In 2011, representatives from ARA, ARC and URG say they convened a working group with the goal of developing an accreditation program that would be an asset to their respective members and a model for other countries. After research, the group recommended a draft outline that was approved by the three associations.
The CAR Gold Seal Accreditation Alliance collaborators have identified common standards among the programs and also incorporated recycled part quality assurance standards and employee training programs, adopted from URG 8000. The CAR and Gold Seal program is designed to certify and audit for best management practices at four levels: business standards, safety standards, environmental stewardship standards and consumer assurance standards and part quality assurance.
> PAPER
Cascades Expands Moka100 Line of Recycled Tissue Products
Cascades Tissue Group, a Waterford, N.Y.-based subsidiary of Canada’s Cascades Inc., has announced the expansion of its Moka 100-percent-recycled-content unbleached bathroom tissue line of commercial tissue products.
In addition to offering single rolls of Moka, launched in January 2012, Cascades Moka is available in jumbo (9-inch) rolls and a high-capacity format for Cascades Tandem dispensers.
The expanded product line “will help the company meet the growing away-from-home market demand for a product that is novel for North America and the ultimate in sustainable bathroom tissue,” Cascades says. The larger formats provide customers with options to use the product in existing dispensers that are designed to entail less frequent restocking, Cascades says.
Strong commercial demand for the beige-colored Moka bathroom tissue “demonstrates customers are willing to forgo ‘white’ to be more ‘green,’” Cascades says.
Cascades Tissue Group bills Moka as “North America’s first bathroom tissue to eliminate chemical whitening, a process introduced solely to enhance aesthetics.” As well, Cascades’ Moka gets 80 percent of its pulp mix from post-consumer material and 20 percent from recovered corrugated boxes.
“As tastes continue to evolve, and customers continue to seek the most environmentally preferred options available, we knew the time was right to introduce North America’s first-ever beige bathroom tissue,” says Cascades Tissue Group CEO Suzanne Blanchet. “The reception has been really positive, and we’re thrilled to be at the forefront in this step for greater sustainability.”
Cascades began the Moka line in the 1990s with the commercial Moka napkin. Sales of that product have experienced double-digit growth over the years, as customers became more aware of its environmental benefits, Cascades says.
> METALS
Capital Scrap Metal Adds to Florida Holdings
Capital Scrap Metal LLC (CSM), based in Deerfield Beach, Fla., has purchased Pompano Scrap Metal, Pompano Beach, Fla. The newly acquired facility is about four miles from the processing site CSM refers to as its flagship location.
The addition of the 10-acre full-service scrap metal facility will enable CSM to expand its current market share in the south Florida region, the company says.
Equipment at the site will include an Acculoader container loader, 90-foot Rice Lake scales, a Sierra RB 6000 logger, numerous excavators and several front-end loaders.
The new location is about 45 minutes from the Port of Miami and 25 minutes from Port Everglades in Fort Lauderdale, providing access for offshore shipping.
> METALS
Schupan Acquires Shapiro Metals Yard
The scrap metal recycling company Schupan & Sons Inc., headquartered in Kalamazoo, Mich., has acquired the South Bend, Ind., scrap yard from Shapiro Metals, a St. Louis-based metals recycling firm. The deal was completed Aug. 1.
Bruce Shapiro, president of Shapiro Brothers, says the transaction was a strategic move for both companies. “Schupan does business similar to us,” Shapiro says. “We respect each other.”
The South Bend facility is set up to handle ferrous and nonferrous scrap exclusively from industrial sources.
Shapiro Metals recently opened a new recycling facility in Mobile, Ala. The yard, opened in June, handles nonferrous scrap from industrial sources.
> METALS
TMS International Opens Trading Offices in Brazil, US
TMS International Corp., the Glassport, Pa.-based parent company of Tube City IMS Corp., a provider of outsourced industrial services to steel mills, has opened trading offices in Belo Horizonte, Brazil; Miami; and Austin, Texas.
David Aronson, president and COO of TMS’ Raw Material and Optimization Group, says the new offices mark the company’s first formal trading group presence in Brazil and Florida. He notes that the offices are in strategic geographies to better serve domestic and international customers and partners.
“The opening of the office in Brazil is a key step in TMS International’s increasing globalization. We look forward to better serving Brazil’s rapidly increasing demand for raw material and steel mill services,” Aronson adds.
Leading TMS’ Brazil office is Carlos Crego as general manager of its Raw Material and Optimization Group. Crego has more than 25 years of trading experience in iron ore, pig iron and scrap. He will be responsible for trading and expanding the company’s trading operations in Brazil. Prior to joining TMS, Crego was a partner at Ironmar Exports and Logistics Ltda. in Brazil. He also worked at Acesita and at Ferrobrasil Trading S.A.
“Carlos has a wealth of experience in trading and the steel industry, and we welcome him to the company,” Aronson says.
TMS’ new Miami office will support its offices in Brazil as well as its office in Monterrey, Mexico, and throughout Latin America. Hideto Hata, director of outsource purchasing and sales for Central and South America, leads the office.
Rick Groenert, a trader, will lead the Austin office.
“The Texas office is integral to the company’s initiatives to expand its market in the Southwest U.S.,” Aronson says. “Rick will be responsible for strategic planning, procurement and business development in the region and will also support the company’s trading offices in Granite City, Ill.; Fairfield, Ala.; Salt Lake City, Utah; and Monterrey, Mexico. He is an experienced trader, and we are pleased to welcome him to the team.”
> TRANSPORTATION
USDA to Track Ocean Shipping Container Availability
The U.S. Department of Agricultural (USDA) has released its first Ocean Shipping Container Availability Report (OSCAR), which uses data provided by the container lines in the Westbound Transpacific Stabilization Agreement (WTSA).
According to WTSA, OSCAR aims to provide freight shippers with a snapshot of current equipment availability at 18 inland intermodal load locations in the form of aggregate net surplus or deficit totals for participating carriers. The report also will forecast the expected availability at each location two weeks out, based on advance carrier bookings.
The report is available on USDA’s website at www.ams.usda.gov/oscar.
“OSCAR represents a model industry-government collaboration, bringing added transparency to the export supply chain,” says Brian Conrad, WTSA executive administrator. “Putting the right data collection and reporting processes in place have required persistence and hard work by both ocean carriers and USDA, and WTSA lines appreciate the critical leadership role USDA has played in launching this valuable pilot project,” he adds.
According to the WTSA, the joint USDA/WTSA pilot project is an outgrowth of discussions begun in 2010 amid severe space equipment shortages in the transpacific trade as Asia-U.S. import demand suddenly spiked and ships idled in the global downturn returned to service. Most Asian container production capacity had closed, leaving carriers scrambling to locate and deploy containers and to reposition empty containers back to Asia once they had been unloaded. The situation left U.S. exporters short of vessel space and equipment, even as export demand in Asia was strengthening.
> ELECTRONICS
US Micro Receives R2 Certification
U.S. Micro Corp., based in Las Vegas, says it has received Responsible Recycling Practices (R2) and ISO 14001:2004 certifications for its Atlanta facility after audits by Perry Johnson Registrars Inc.
The audits evaluated and tested U.S. Micro’s policies governing waste management, data security, employee health and safety, public health and the environment as well as the chain of custody processes, U.S. Micro says in a press release.
“From day one at U.S. Micro, we made data security and the environment our most important priorities,” COO Steve Bowen says. “Securing these certifications at our Atlanta facility was a way to reinforce what has already been standard operating procedure for us since our inception.”
Additionally, U.S. Micro says it has received the SOC 2 (Service of Organization Controls) designation after an audit of its processes related to data elimination information security, disposition, electronic inventory counts, human resources, change management and other criteria. U.S. Micro says its pursuit of the designation was unique within the IT asset disposition industry.
According to U.S. Micro, the R2, ISO 14001:2004 certification and SOC 2 designation are important credentials for it to assure customers that its disposition process is in compliance with industry regulations.
> TRANSPORTATION
Waste Management to Launch CNG Truck Fleet in Kentucky
Waste Management Inc. (WM), headquartered in Houston, has announced the introduction of a new fleet of compressed natural gas (CNG) trucks in Louisville, Ky. Additionally, the company says is opening a new public fueling station in Louisville.
WM is adding up to 25 CNG-powered collection vehicles in Louisville and plans to roll out additional CNG-powered collection vehicles in the area in the future. The public fueling station will refuel WM’s local fleet as well as sell CNG to commercial fleets and retail consumers with CNG vehicles.
“Since natural gas-powered collection trucks run cleaner and quieter, we’ve made the commitment to use more in our local operations and support sustainability in this community by opening a public CNG station,” says Tim Wells, area vice president for WM in Kentucky, Alabama, Arkansas and Tennessee. “We are dedicated to providing our greater Louisville area customers with outstanding service while doing business here in the most sustainable manner possible.”
WM collaborated with PetroCard to develop the first CNG fueling station in Louisville. The new Clean N’ Green Fuel facility, funded by Waste Management and PetroCard, makes CNG available to commercial fleets—transit agencies, school districts, taxis, cities and municipalities—and private individuals with CNG vehicles.
“Waste Management already operates nearly 1,700 CNG vehicles, the largest fleet of CNG recycling and waste collection trucks in North America,” Wells says. “Each additional Class 8 diesel truck we replace with natural gas reduces diesel use by an average of 8,000 gallons per year and cuts annual greenhouse gas emissions by an average of 22 metric tons.”
> METALS
Pacific Steel & Recycling Acquires Triple R Metals
Pacific Steel & Recycling, based in Great Falls, Mont., has acquired the assets of Triple R Metals, located in Medicine Hat, Alberta, Canada, north of Great Falls. The recycling facility has been in business 10 years under the ownership of Bart Campbell.
The acquisition is Pacific Steel & Recycling’s first operation outside of the United States. Pacific Steel will change the name of the newly acquired facility to PHF Steel & Recycling, which is representative of Pacific Steel & Recycling’s original name, Pacific Hide & Fur Depot. The company will retain Triple R Metals’ employees. James Knick, who previously managed Pacific Steel & Recycling’s transloading facility at the Port of Tacoma, will manage the new location.
Pacific Steel & Recycling operates 44 branches throughout Washington, Idaho, Montana, North Dakota, South Dakota, Wyoming, Nevada, Utah and Colorado.
> PLASTICS
HPRC to Study Plastic Scrap from Health Care Facilities
The Healthcare Plastics Recycling Council (HPRC), headquartered in St. Paul, Minn., has finalized an agreement with Stanford University Medical Center for a six-month pilot study of plastic waste within health care facilities. According to the HPRC, the study will analyze data related to prepatient plastic waste at Stanford Hospital and Clinics in Palo Alto, Calif.
“Stanford has been passionately active in plastics recycling within our clinical setting for some time now,” says Krisanne Hanson, director of sustainability, Stanford University Medical Center. “As a health care facility advisory board member to HPRC, we are excited to work with them to increase industry knowledge, share best practices and define solutions for other hospitals seeking greater sustainability in this area.”
The study will be fully funded and fully implemented by Stanford University Medical Center with technical support provided by HPRC.
> MUNICIPAL
WM Provides Grants to KAB Affiliates
Stamford, Conn.-based Keep America Beautiful (KAB), the national nonprofit organization, has announced that Houston-based Waste Management (WM) has awarded 10 grants worth $10,000 each to KAB affiliates. Waste Management Think Green grants are awarded to encourage community sustainability through local environmental efforts.
The merit-based grants are awarded to KAB affiliates that have designed programs to increase local recycling efforts, expand public environmental education or enhance local beautification and community greening initiatives. WM has provided support for more than 100 such KAB projects throughout the past eight years through its grants.
KAB affiliates can increase the potential of their community improvement projects with the help of Waste Management Think Green grants. For example, Gwinnett Clean & Beautiful in Duluth, Ga., and Greensboro Beautiful, Greensboro, N.C., are establishing school-based recycling programs; Hot Springs/Garland County Beautification in Hot Springs, Ark., is working to reduce the amount of pharmaceutical and personal care waste entering the local water system; and Keep Winston-Salem Beautiful, Winston-Salem, N.C., will plant hundreds of trees along the Newell/Massey Greenway and New Walkertown Road in East Winston-Salem as part of a Community Roots Day.
Waste Management is an active supporter of many of KAB’s national programs, including the Great American Cleanup, America Recycles Day and RecycleMania.
“Keep America Beautiful applauds the work of all of this year’s grant winners and their continuing efforts to create and sustain greener, more vibrant communities,” says KAB President and CEO Matthew McKenna.
> PLASTICS
California City Passes Plastic Bag Ban Ordinance
The West Hollywood City Council has passed an ordinance prohibiting the use of single-use carryout shopping bags at the point of sale from all pharmacy, grocery and retail stores in West Hollywood.
According to the West Hollywood City Council, its ordinance is based on the ban currently in effect in Los Angeles County and similar to ordinances in neighboring cities, including Santa Monica, Malibu, Calabasas and Long Beach.
The ordinance goes into effect for retail establishments measuring at least 10,000 square feet and for all supermarkets in February 2013. Retail establishments smaller than 10,000 square feet will have until June 2013 to comply with the ban.
The city says that a ban on single-use plastic bags will eliminate a major source of litter and marine debris and create local green jobs. Five percent of single-use plastic bags are recycled, according to city estimates.
Retailers are permitted to charge 10 cents for paper bags to help cover the costs of stocking them and any related outreach or promotional efforts. Paper bags will be required to contain 40 percent post-consumer recycled content. Stores are encouraged to make reusable shopping bags available for purchase, and customers are encouraged to bring their own bags when shopping.
Customers who qualify for subsidized groceries will be exempt from the paper bag fee, and lightweight plastic bags without handles for transporting produce and raw meat products to the point of sale are permitted.
Restaurants and other food service providers who provide plastic bags to customers for prepared take-out food intended for off-premises consumption and dry cleaners and farmers’ markets are not affected by the ordinance.
More information regarding West Hollywood’s proposed Plastic Bag Ban is available at www.weho.org/plasticbagban.
> TRANSPORTATION
HMM to Impose Scrap Metal Surcharge
Hyundai Merchant Marine (HMM), with U.S. headquarters in Dallas, has announced a maintenance and replacement (M&R) surcharge of $65 per container for exports of scrap metal from the United States and Canada to Pacific Rim countries. The surcharge will be effective Oct. 1, 2012.
The surcharge will be added to all bills of lading on a per-unit basis regardless of the container condition at the destination. According to HMM, the fee is intended to compensate the carrier for the aggregated cost of container repairs widely associated with shipping scrap metal.
HMM operates more than 110 ocean-going ships in more than 40 sea routes to more than 100 ports of call.
> MUNICIPAL
WM Keeps its Options Open
Waste Management Inc. (WM), Houston, may be one of the largest and most well-established waste and recycling companies in the U.S., but one of its top managers readily admitted that the company is not too old or too big to learn.
In a presentation at the Solid Waste Association of North America (SWANA) 2012 WasteCon event near Washington, D.C., in August, William Caesar, president of Waste Management Recycle America, said when it comes to waste-to-energy technologies, “Our intention is to learn … and then commercialize that technology [where] it makes sense.”
The company has made investments in more than a half-dozen waste conversion technology companies. Caesar said WM believes it is “advantageous to place a series of small bets instead of one big bet” in the waste-to-energy market. Among the conversion technology companies in which WM has invested are:
- Enerkem, a thermo-chemical fuels and energy producer headquartered in Montreal;
- Fulcrum Energy, a waste-to-transportation-fuel technology provider based in Pleasanton, Calif.;
- Genomatica, a San Diego-based company with technology to convert waste to marketable chemicals;
- Harvest Power of Waltham, Mass., a producer of anaerobic digestion and composting systems;
- Agilyx, Beaverton, Ore., a maker of plastic scrap-to-fuel systems; and
- InEnTec, a Bend, Ore.-based plasma arc gasification equipment maker.
Caesar indicated the investments—as well as joint ventures with energy companies such as Valero, Total and Linde Gas—are helping WM spread out its waste-to-energy efforts to include conversion technologies.
As the operator of 266 active landfills and the owner of closed landfills, WM also has been focusing on landfill gas-to-energy systems. When it comes to traditional mass-burn waste-to-energy plants, in which WM has a presence through its Wheelabrator subsidiary, Caesar said, “All things being equal, I think we’ll see less incineration [in the future] because there will be technologies that will be less expensive and bring more value.”
> ELECTRONICS
E-Waste LLC Obtains R2 Certification
E-Waste LLC, based in Hudson, Ohio, has reported that it has been certified to the R2 (Responsible Recycling Practices) and ISO 14001:2004 standards.
“To our customers this means that we will mitigate their e-waste disposal risks by meeting the highest industry recycling and environmental standards and will continuously be audited to ensure compliance,” says Jim Cleveland, e-Waste president and CEO.
“We will continually work directly with corporations, state and local agencies as well as the residential sector, offering environmentally responsible solutions for the handling and recycling of computers and electronics,” he adds.
The R2 Standard sets forth requirements relating to environmental, health, safety and security aspects of electronics recycling. It also requires electronics recyclers to assure that toxic material streams are managed safely and responsibly by downstream vendors through to final disposition. R2 also prohibits certified parties and their downstream vendors from exporting toxic materials to countries that have enacted laws making import of such materials illegal.
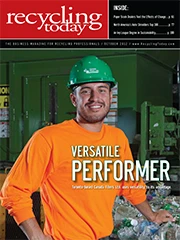
Explore the October 2012 Issue
Check out more from this issue and find your next story to read.
Latest from Recycling Today
- Astera runs into NIMBY concerns in Colorado
- ReMA opposes European efforts seeking export restrictions for recyclables
- Fresh Perspective: Raj Bagaria
- Saica announces plans for second US site
- Update: Novelis produces first aluminum coil made fully from recycled end-of-life automotive scrap
- Aimplas doubles online course offerings
- Radius to be acquired by Toyota subsidiary
- Algoma EAF to start in April