With the rise in mobile computing in the form of smartphones, handheld computers, tablets and mobile apps, recycling industry software companies have adapted their programs and introduced new add-ons in recent years to take advantage of the newest capabilities.
As a result, both recycling company managers and employees can now accomplish a wide variety of tasks and make informed business decisions from outside the traditional office or workspace setting. Alternatively, recyclers can use mobile devices while out in their yards, helping to save time and to eliminate paperwork.
We asked a number of recycling industry software company executives serving this multi-dimensional industry for their perspectives on how industry software is helping recyclers work remotely, whether from home, on the road or out in their own scrap yards.
Server Setups
Most all recycling industry software firms say there’s virtually no limit to the number of yards that can be managed remotely with today’s inventory management programs. Even so, the companies hold multiple philosophies, strategies and techniques for achieving these ends.
In many cases, but not all, remote access to company records is accomplished using the Internet and a remote desktop connection set up on a laptop, tablet or another mobile device.
When recyclers have multiple yards to manage, some software programs are configured to utilize multiple databases or multiple servers for storing purchasing, inventory and customer information across their multiple locations. Meanwhile, many other companies have adopted the single-database approach, in which all of a recycling company’s inventory and purchasing records for multiple yards or even multiple subsidiaries are stored on a single server, enterprise-wide.
Barry Grahek, president of Jacksonville, Fla., based DesertMicro, says he believes the single-server approach keeps information access simple for managers and remote yard operators.
“It is very common that our customer has to manage remote operations and remote inventory, so our application utilizes a centralized server and single database for all remote yards to log in to,” Grahek says.
Similarly, Bryan Anderson of Herndon, Va.-based Anderson Essentials, says because the data reside in one database, reporting is simple with such a system. “By filtering the data, you can see just the information you want to see, or you can see everything,” Anderson says.
Personalize Your Pickups Mobile apps—They’re not just for recyclers. The ScrAPPSmart App, introduced by recycler Eli Cohen, based in Ontario, Calif., lets industrial and commercial customers request pickups right from their mobile phones. What’s more, recycling companies can personalize the mobile app with their own logos, colors and company information, then provide it to existing customers to simplify the pickup request process. “Customers love it,” says Cohen, who originally designed the app for his own customers. It’s another way for customers to use their smartphones.” To use the app, existing customers simply click on the material type and select a box to request a pickup. Within seconds, the scrap yard receives an email showing all the details of the request needed to schedule a pickup. “We can respond by link, letting the customer know we received it and this is a confirmation of when we’re going to pick it up,” Cohen explains. Cohen, who owns a scrap company in Southern California, says he created the app to help automate and streamline the pickup process. Other recyclers who saw the app loved the idea, Cohen says. “We started to make it for others,” Cohen says. “You’ll see no two apps alike. If a company wants a particular look or a particular feature, we’re going to do it,” he says. For example, Cohen says, he created a French language version for a Canadian recycler. More information is available at www.scrappsmart.com. |
However having a single database for inventory data is not always feasible, says John Underwood, president of Systems Alternatives International, based in Maumee, Ohio. This is particularly true with large, multinational scrap metal buyers that operate across the country or across the globe.
Toward that end, his company offers both regional and central server configurations for inventory and financial data, depending on customer needs.
Philip Rafle, national sales manager for 21st Century Programming, Long Beach, Calif., says the company’s ROM (Recycling Operations Manager) software is loaded onto multiple servers, with each yard typically having its own database. “That way you’re not Internet-dependent,” Rafle explains. He says that in remote geographical areas where Internet access is spotty, yards need the physical stability of an in-house server.
In terms of the software application itself, one company that has taken a unique approach to remote information management is PopScrap, based in San Diego. Company President Stacy Duty describes his PopScrap application, launched in August 2011, as the only “full scrap recycling software solution in a mobile app format for phones and tablets.”
According to Duty, PopScrap is a 50-state-compliant Android app that offers all of the same features as competitive programs, but in a mobile operating system environment that works with or without an Internet connection. He says the cross-platform application can be used on phones, tablets or Windows computers. The cloud-based application is installed on a local PC or Android device, while the data is saved to the cloud.
Meanwhile, Paradigm Software, based in Hunt Valley, Md., uses a technique called Message Queuing to keep track of activity among multiple remote locations that may not have a consistent Internet connection, explains Jackie Barlow, vice president of the company. “Any changes that are made or transactions that are processed will be stored locally, and once the connection between the two applications is re-established, the system will automatically transfer the information,” Barlow explains.
And Joe Floam, president of ScrapWare Corp., Rockville, Md., says while his company prefers the single-server approach, that server need not be housed at any of the recycler’s locations. “The server does not need to be at a physical location that’s either a yard or the company’s offices,” he says. “It could be at a server farm, what you commonly think of as the cloud.” Floam adds that over the last couple of years, more customers are putting their servers off site at server farms to reduce the risk of downtime.
Remote Feats
Many company executives say with today’s technologies, there’s almost no limit to what procedures and tasks can be accomplished remotely, as long as the user is given the proper security clearance.
Larry Galbraith, chief financial officer of RECY Systems Inc., based in Collegeville, Pa., says with RECY’s system, the user’s sign-on credentials determine what language preferences have been selected as well as the specific information he or she is allowed to see.
Anderson says, “You may not want a scale operator in a small remote yard to be able to view everything throughout your organization. However, you may want the manager of that same yard to be able to see inventory at all locations.”
Rafle says with ROM, recyclers can pay tickets, inspect loads and cut checks from wherever they happen to be.
Remote access also is particularly important for company CEOs and managers, who can see their No. 2 copper positions worldwide, for example, from a hotel room using today’s software.
SAI’s Underwood says along with providing operational information remotely, his company’s software provides Web-based access to analytical reports and key financial forecasting tools. “We have very specialized financial systems that recost inventory daily,” he explains. “One of our key reports is a margin analysis, and it’s used by almost all of our large clients to understand how much money they literally made as of last night.”
As one example, Underwood says the reports can provide managers with a summary of all shredder feed purchased across the country, its average landing cost that day compared with two weeks prior and projections relating to month end. “Those are the tools that are, at the high end, the end result of all the transactions processed at the local level,” he says.
Besides providing management reports, remote reporting also can help consolidate tasks that need to be done enterprise wide. Floam says one example of that is compliance reporting. “From one yard, you can administer all of your anti-theft reporting,” he says. “We see that a lot, where the anti-theft requirements might be compiled at a back office for multiple states.”
And Rafle notes that being able to view and take action with regard to pending orders, on a multi-yard level, can have an impact on profitability. Managers can, for example, find out which locations are closest to the end user or mill, then adjust sales orders to optimize shipping costs.
“An enterprise level system gives you the advantage of being able to see what you have in your total inventory,” Rafle says. “These days with the growing cost of fuel [and] drayage charges, it can change a simple deal where you’re just marginally making money on the transaction into an extremely profitable deal,” he adds.
Powerful Add-ons
In the drive to add mobile computing power, industry software companies have introduced upgraded hardware and software options, as well as complementary mobile apps often designed to link with the company’s flagship program.
For instance Perry Jacobs, executive vice president of Shared Logic, based in Holland, Ohio, says the company offers a subset of programs geared toward use on smaller handheld devices.
Jacobs explains how Shared Logic has helped a Michigan recycler save time and streamline the upgrading process by equipping crane operators in yards with “ruggedized” Android tablets that run the company’s RIMAS (Recycling Industry Management and Accounting) software. The operators enter receipts while they are unloading using an Internet connection and a remote desktop app.
“As he is unloading a rail car or track car full of material, he’s in an inspection screen on the tablet actually entering it,” Jacobs explains.
Building dashboards with InetSoft InetSoft Technology offers business intelligence software that the company says can be used to build dashboards and monitoring applications for any industry, including recycling yards. Visit www.RecyclingToday.com/inetsoft-features-2012.aspx to read more about this solution. |
The company also has made other changes in recent years, Jacobs says, including redesigning the program’s graphical user interface for use with touch-screen devices.
Similarly, DesertMicro’s Grahek says one of the company’s most popular upgrades has been its ruggedized Motorola handheld computers, introduced two years ago for grading of materials in the yard, capturing the information to the central database and also integrating ATM functions. “It eliminates an entire transaction as well as any re-entry of data, and makes it much faster for a buyback center and an industrial customer,” Grahek says.
One of the newest trends to hit the industry is the release of a wide variety of mobile apps designed to automate some sector of the inventory or purchasing process. Toward this end, several software companies have introduced mobile apps designed to work in concert with their software programs, helping to offer some remote functionality.
For instance, Everett Duty, president of BuyBackPro Inc., based in Woodland, Calif., says the company’s various Remote Site apps are designed to be small working versions of the company’s larger management application.
“Remote site apps typically don’t require all of the back-end features but just need to process a transaction of purchasing scrap very quickly,” Everett explains. The company’s BiBack app, for instance, works on an iPad and facilitates the capturing of drivers’ license information, fingerprints and signatures.
“Without Remote Site software, the operator would have to do things by hand,” he explains.
ScrapRight has recently released ScrapRight Mobile, a weighing work station app that complements the company’s ScrapRight software and is available for download to the iPhone, iPad, Android phones and Android tablets. The app allows recyclers to start tickets, take pictures, add materials, capture vehicle plate numbers and print tickets to a wireless printer or existing network printer, says ScrapRight President Shon Duty.
21st Century is offering its iROM app, a customer information tool that provides a dashboard on each customer showing accounts receivable, accounts payable and positions. The app also ties into Google Maps.
Similarly, cieTrade Systems recently introduced the free cieMobile app, which provides recyclers access to customer records, available inventory and shipping information for any of their facilities, using the Apple iPad.
David Haber, president of cieTrade, says the app was designed to improve customer service and support business development by providing instant access to financial, logistics and inventory information from the road or when visiting with a customer.
It’s clear that remote management is a priority for many recyclers by the number of software options available.
The author is managing editor of Recycling Today Global Edition and can be reached at lmckenna@gie.net.
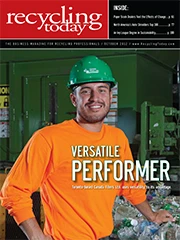
Explore the October 2012 Issue
Check out more from this issue and find your next story to read.
Latest from Recycling Today
- Commentary: navigating shipping regulations for end-of-life and damaged batteries
- Haber raises $44M to expand to North America
- Canada Plastics Pact releases 2023-24 Impact Report
- Reconomy brands receive platinum ratings from EcoVadis
- Sortera Technologies ‘owning and operating’ aluminum sorting solutions
- IDTechEx sees electric-powered construction equipment growth
- Global steel output recedes in November
- Fitch Ratings sees reasons for steel optimism in 2025