Transportation and logistics is what Kyle Trayner, founder of KLT Industries, Ayer, Mass., says he knows best. During the past 10 years, KLT has emerged as a high-volume regional recycler of old corrugated containers (OCC) and other grades of fiber, and Trayner says knowing how to efficiently collect and move material has been a key factor in the company’s success.
Preparing materials for efficient shipment includes baling as a critical step, and KLT has recently invested to upgrade its ability to produce dense bales in a quick cycle time.
In September 2012, KLT personnel worked with Balemaster, Crown Point, Ind., on the installation of a Fat Boy baler, a Balemaster model that can draw on three motors with a combined 225 horsepower to produce up to 35 tons per hour of baled OCC.
Driving Forward
Trayner has been involved in the recycling industry in New England for several decades, but he says his initial perspective was gained in the trucking industry.
“I grew up in the trucking and logistical side—my family was in over-the-road (OTR) trucking,” says Trayner. “I left the family business at an early age,” he continues. “We had hauled a lot of scrap paper, so when I left I worked at a baling facility that I had been familiar with. Eventually I moved into brokerage and was one of the partners of KC International, until we sold that company to KTI [in the late 1990s].”
KTI Inc., formerly headquartered in Guttenberg, N.J., was an operator of numerous recycling facilities that eventually merged into Casella Waste Systems.
Not long after selling off KC International, Trayner says he was ready for his next venture. “I founded KLT in 2002 to get back into business,” he comments. Trayner turned back to the freight and logistics knowledge he gained in his youth by focusing on for-hire trucking. However, recycling soon crept back into the picture.
“One of the paper mills I was dealing with urged me to buy some trucks to both haul in scrap paper and haul out finished paper,” he says.
KLT started doing that as well as buying materials for other paper mills in New England. “In the later 2000s we shifted the focus of the business away from for-hire trucking,” says Trayner. “And then instead of brokering we focused on locating our own facilities and placing balers in warehouses.”
For a time, Trayner says KLT worked in cooperation with GP Harmon and brought flatbed trucks equipped with Moffat forklifts to industrial locations to collect fiber. “As that moved on, a lot of our customers wanted compactors as well. So the next thing you know, we had our own roll-off trucks, our own baling facilities and our own font-end trucks.”
Trayner says KLT Industries has worked in cooperation with paper mills in New England to help them secure supply in a very competitive recovered fiber market. “A lot of the mills I’ve dealt with, as they see their fiber supply being crucial, we’ve gone further down the food chain for our mills to help them be supplied.”
As of 2012, KLT refers to itself on its website (www.kltindustries.com) as “a recognized leader in commercial paper and plastic recycling.” The company’s fleet of trucks picks up some 10,000 tons per month of recyclable material. “Our growth has been phenomenal over the past few years,” says Trayner. “We just keep going forward.”
Much of that material moves through KLT’s plant in Ayer or one of its other two facilities in Putnam, Conn., and Chepachet, R.I. The Ayer plant is the largest and was the perfect candidate for a new high-volume baler.
Fat City
Trayner cites several reasons why the time was right for KLT to purchase its Fat Boy baler from Balemaster, with many of those reasons tying into shipping and material handling efficiency.
“Some of our domestic mill customers have spec’ed out super lightweight trucks to be able to haul 50,000 or 52,000 pounds of rollstock,” says Trayner. “With the Fat Boy, instead of loading 38 to 42 bales, we can do that with less than 14 bales on the truck. That’s the beauty.”
Loading and unloading 14 bales instead of 40 results in a much faster material handling process, notes Trayner. “I’ve run those forklifts myself and loaded and unloaded. When you have 48 bales, there is a time element there.”
In addition to the time- and labor-saving elements of loading fewer bales, Trayner says he won’t miss the challenge of fitting 40-plus bales into a truck. “Loading a truck with the lighter bales is like playing Jenga,” he says.
Some materials collected and processed by KTL go to export markets, and the Fat Boy will offer advantages on this front as well, says Trayner. “With the baler we have now, we struggle to get 49,000 pounds of material into containers. Now, we can negotiate knowing that hitting 57,000 to 59,000 pounds is not an issue,” he comments.
Producing fewer, heavier bales will lead to other cost advantages, says Trayner. “We also can use less baling wire and a less expensive type of baling wire. When we need to store extra tons for a while, these bales take up a tremendously smaller amount of floor space, or footprint, in our warehouse.”
Another operational advantage of the Fat Boy cited by Trayner is its large charge box. “We do a lot of reprocessing of bales from retailers and also bale Gaylord boxes,” he comments. “In a lot of two-ram models this material can cause bridge jams. When you look at the 58-inch-wide-by-43-inch-tall bale and the big charge box, this baler will swallow almost anything.”
Multiple Factors
While high-volume production is a key reason KLT selected a Fat Boy model, Trayner says the machine has been designed to adjust to whatever work load it is asked to handle on a given day.
“It’s a 225-horsepower machine but it has three 75-horsepower motors. That gives us flexibility. We can run on one motor or two or kick in the third motor and do more than 35 tons per hour of cardboard when we need to,” he comments. “The operational flexibility of that is tremendous. It’s like stepping on the accelerator on the highway.”
The baler the Fat Boy is replacing is an older model that has been in many years of solid service, but was only capable of baling seven or eight tons per hour of OCC, says Trayner.
In addition to varying the machine’s power usage, Trayner says KLT also will deploy the Fat Boy flexibly in terms of the materials it will compress on a weekly basis. “We handle sorted office paper, mixed paper, material from community collection programs and schools, plus stretch wrap and other grades of plastic from industrial generators. Everything is going to go through the Fat Boy. It can handle everything we throw at it,” he says.
At the plant in Ayer, the baler will be fed by a 20-foot long pit conveyor made by Hustler Conveyor, O’Fallon, Mo. “Everything is tipped indoors,” says Trayner. “We have multiple tipping pits for different grades. Those pits can be fed at different times to the Fat Boy.”
Finished bales are either stored in the 15,000-square-foot warehouse area or are hauled by lift truck directly to trailers waiting at one of 10 loading docks. With his freight and logistics background, Trayner makes sure KLT facilities are transportation-friendly. “You can never have too many loading docks,” he states.
Currently, the plant in Ayer handles considerably more material than the plants in Connecticut and Rhode Island. But Trayner does not preclude the possibility that additional Fat Boys will one day be installed there. “Part of our strategy is to put up baling facilities near heavily populated areas of New England. In the next 24 months, that could mean two or three new facilities.”
Trayner is not saying such growth will be easy, but he can look back with pride at what he and his colleagues have accomplished in their first decade. “The volume it takes to feed a baler this size is considerable, but we approach everything we do with an open mind,” says Trayner, adding that KLT Industries has quickly grown to “have a fleet of trucks that rivals most trucking companies in our area.”
He adds, “Our other facilities are candidates in the future for Fat Boys, just due to the efficiency of the machine. The time needed per baled ton will be cut drastically,” Trayner continues. “That creates labor savings and energy savings. The Fat Boy also is going to allow us to bring a lot more tons into our Ayer facility and have the capacity to process those tons.”
The September installation of the Fat Boy is just in time for a peak season, adds Trayner. “With the retail-related work we do, we run 24/7 through the end of January. It’ll be nice knowing we have the processing capacity.”
In the long term, says Trayner, the added baling capacity is “really going to position us to help with the overall expansion of KLT Industries. As our full-time salespeople sourcing for the facility go out and negotiate with large generators, we’re going to have that Fat Boy advantage on our side.”
The author is editorial director and associate publisher of Recycling Today and can be contacted at btaylor@gie.net.
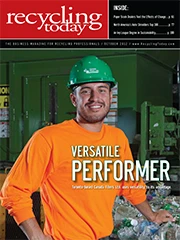
Explore the October 2012 Issue
Check out more from this issue and find your next story to read.
Latest from Recycling Today
- ReMA opposes European efforts seeking export restrictions for recyclables
- Fresh Perspective: Raj Bagaria
- Saica announces plans for second US site
- Update: Novelis produces first aluminum coil made fully from recycled end-of-life automotive scrap
- Aimplas doubles online course offerings
- Radius to be acquired by Toyota subsidiary
- Algoma EAF to start in April
- Erema sees strong demand for high-volume PET systems