For many scrap metal recyclers, it is a proud moment when they open a new auto shredder. Ideally, for these same scrap recyclers, installing an auto shredder is one of the best ways to boost volumes at their facilities and to increase profits.
One shredder manufacturer comments that opening an auto shredder immediately changes a small scrap recycling company’s status, making it a major player in the scrap metal market.
To some skeptics, however, the proliferation of new auto shredders intensifies the existing overcapacity issue.
Many shredder operators say they are finding it challenging to keep their machines running at more than 50 percent of capacity. In the not-too-distant past, shredder operators may not have had any competition within a 100-mile radius of their plants. However, with the growing number of auto shredder installations, some operators say competitors basically may be across the street from one other.
Bumper Crop
According to the list inserted at p. 77 of this issue of Recycling Today, more than 300 auto shredders presently are installed in the United States. While a few are idle because of challenging market forces, during the past two years many more have recently come online. Long-time plant operators are expressing concern that some regions of the country are saturated with auto shredders.
Over the past two years, there have been more than two dozen new auto shredders that have been announced or built, including some still on the drawing board. At the same time, a number of existing shredder operators are tweaking their plants to increase production and to improve their metals recovery rate.
The result, according to many sources, is that they need to extend their supply radius even further and must raise prices to outbid competitors for the needed tonnage. Even with these changes in strategy, many operators say they are running their shredders at less than 50 percent of their capacity.
One scrap metal recycler with several shredders in operation says his company is running those shredders at an average of around 40 percent of capacity, which is far less than an optimum rate.
Despite the concern about overcapacity in the shredder market, Randy Schlipp, the owner of Randy’s Recycling, a Michigan-based auto salvage and scrap recycling firm, is confident that a new shredder his company started in the middle of September will be a success. The 80-by-104 shredder opened at a greenfield site in New Carlisle, Ind., and operates under the name 360 Metals Recycling. The plant includes a downstream sorting system.
Schlipp says his company has a number of feeder yards that he says will help supply the auto shredder. He adds that the company may add additional feeder yards in the future to ensure adequate feedstock for the shredder.
Along with the installation of new auto shredders, some previously mothballed installations have reopened. Gerdau Long Steel North America, Tampa, Fla., announced plans to restart its Wilton, Iowa, auto shredding plant near its steel mill by the middle of 2012. The company idled the shredder nearly three years ago, citing the slow economy.
Gerdau began installing new equipment at the site in late 2011, including a new infeed system and updated automation and controls.
Mike Marley with the consulting group World Steel Dynamics, Englewood Cliffs, N.J., says the overall increase in auto shredder capacity on the market is causing fierce competition for feedstock, essentially erasing profitability.
Rich Brady with OmniSource Corp., Fort Wayne, Inc., echoes Marley. “Go back a dozen years and a shredder could process around 50 to 60 tons per hour. Now, shredders can do 100 tons per hour, with some [super-sized] shredders doing 300 tons per hour.”
On the bright side, shredded scrap has become a much more sought-after product. Marley estimates that overall demand for No. 2 shredded scrap has grown significantly, including export demand, which has increased to more than 5 million tons per year. As well, domestic mills have been buying significant volumes of the material, despite some earlier concerns about quality.
Is Smaller Better?
Several years ago the trend in the scrap metal industry was toward super-sized shredders that could process 20,000 tons of material per month. These machines were lauded for their ability to process hundreds of cars per day. However, with the economy languishing and new auto sales still off from the peak of the late 1990s, the challenge is how to keep machines sufficiently supplied. Thus, more recently there has been a trend toward smaller plants that can run fewer days per week and still be profitable.
During the 2012 Institute of Scrap Recycling Industries Inc. (ISRI) Commodities Roundtable Forum, Frank Goulding of Newell Recycling LLC, East Point, Ga., noted a trend toward portable shredders, which are much smaller than traditional fixed plants. He estimates that recyclers in Georgia alone are considering purchasing six of these portable shredders.
One recycler contacted wonders if these new shredders can operate profitably with fewer days and whether they can produce a clean, dense shred in one pass. Bobby Triesch, vice president of ferrous operations for Newell Recycling says these smaller shredders may produce more contaminated material.
Another recycler contacted says many of the smaller shredders are able to run fewer days per week than their larger counterparts and remain profitable; however, even at this operating rate, some new plant owners are running into problems getting enough raw material to feed their machines. “You are going to see shredders idled, mothballed or closed down due to market conditions,” the recycler says.
The most recent figures from WardsAuto (www.wardsauto.com) show that while auto and truck production has strengthened since bottoming out in 2009 (when new auto sales totaled roughly 8.7 million units), more recent figures are still down from the peak in auto sales seen in 1999.
For 2011, auto production came in at approximately 13.47 million units, while 2012’s totals could reach 14.4 million units. While this would be an increase from 2009 figures, they are still less than in 1999, when auto sales topped 17.6 million units.
Another factor affecting auto shredder capacity was the “Cash for Clunkers” program in 2009, which created a sudden spike in scrapped autos but ultimately altered the flow of vehicles in subsequent years. “The reservoir is shrinking. The shredder capacity is outstripping the supply,” Marley comments.
He adds that Texas and the Southeast are two regions that seem to be significantly oversupplied with auto shredders.
Joel Denbo, with Tennessee Valley Recycling, Decatur, Ala., says, “In our current economy, it doesn’t take a brain surgeon to see there is an overcapacity of shredders on the market.”
He continues, “There is a reduced amount of feedstock available for the auto shredders.”
Denbo notes that Tennessee Valley Recycling’s two auto shredders, 60-by-80 and an 80-by-104 models, are not running at hoped-for capacity because of the lack of supply available.
“There aren’t any margins right now. People are having to go out silly distances to get the material they need,” he says.
Brady says the present market has strained margins. In large part it is because of excess capacity, which is narrowing margins between the steel mill price and what auto shredder operators must pay to get scrap material.
Denbo is skeptical about the plethora of new shredders coming onto the market. “It just seems to me that people are making the investment without fully understanding the market.” He continues, “Just wait until they bend their first rotor or another piece of equipment needs to be replaced. The lead time (for replacement parts) has gotten long. You might be stuck with some high-priced scrap in a falling market.”
The spread between what mills pay for shredded scrap and what a dealer has to pay to buy, process and transport material narrowing, auto shredder operators say they are seeing their margins shrink significantly. Triesch says that if operators aren’t savvy and make a mathematical error, they could take a significant financial hit in today’s market.
Even among companies that have developed significant expertise in operating a shredder, “There will be a shakeout,” Triesch says. “Only the lean will survive. If you are not on the cutting edge with technology you won’t make it.”
Brady agrees with the shakeout scenario, saying there will likely be consolidation in many regions of the country, as companies struggle to find the match between supply, demand and prices.
Scott Newell of The Shredder Co., a shredder manufacturer based in San Antonio, says operators may need to add computers to their shredders to improve their overall operations.
Downstream Attention
With margins for shredded ferrous scrap being squeezed, many shredder operators have been enhancing their downstream systems to extract more nonferrous metals from auto shredder fluff.
However, a concurrent trend, several operators say, is that many auto dismantling and auto recycling companies are extracting components that contain nonferrous metals—even nonworking ones—before shipping the remainder of the vehicle to the shredder. Therefore, according to these sources, there is far less nonferrous scrap available for the auto shredder operators to recover through their downstream systems.
Denbo says this trend is resulting in steadily declining yields for auto shredder operators.
To make up for the loss of nonferrous metal in autos, operators are shredding more white goods and other material. This, several auto shredders say, can increase the overall amount of nonferrous metals that can be recovered.
During the ISRI Commodities Roundtable Forum, Fred Hauptstueck, vice president of finance, metals recycling and ferrous resources for Steel Dynamics Inc. (SDI), Fort Wayne, Ind., said his company was seeing greater scrap processing capacity and more competition for material. While SDI (which owns scrap processing firm OmniSource) ultimately gets the scrap it needs, he says the material is dispersed across more yards.
Contrary to the concerns expressed by many long-time plant operators, Schlipp expresses confidence that 360 Metal Recycling’s collection of feeder yards in Indiana and Michigan will be enough to supply his new auto shredder with the raw material required.
While acknowledging challenges with the current economy, Schlipp says his company is situated in an area that will allow it to pull from a fairly wide region. “We have a good supply.” Plus, he says the company’s background in the auto recycling business gives it an advantage over some competitors.
As more shredders come online, recyclers and consumers throughout the ferrous scrap supply chain will have a stake in how well capacity is lining up with supply and demand.
The author is senior editor of Recycling Today and can be contacted at dsandoval@gie.net.
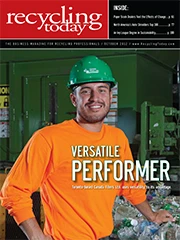
Explore the October 2012 Issue
Check out more from this issue and find your next story to read.
Latest from Recycling Today
- Commentary: navigating shipping regulations for end-of-life and damaged batteries
- Haber raises $44M to expand to North America
- Canada Plastics Pact releases 2023-24 Impact Report
- Reconomy brands receive platinum ratings from EcoVadis
- Sortera Technologies ‘owning and operating’ aluminum sorting solutions
- IDTechEx sees electric-powered construction equipment growth
- Global steel output recedes in November
- Fitch Ratings sees reasons for steel optimism in 2025