Medium-sized scrap processors may find it is time to incorporate a stationary shear into their equipment arsenals. Stationary shear technology commonly allows recyclers to complete multiple tasks at once, adding baling and logging to the traditional shearing function. However, multitasking technology often comes at a premium, and many scrap processors will want to know what their operations are undertaking before purchasing a stationary shear.
Sierra International Machinery, headquartered in Bakersfield, Calif., has been providing processing equipment to the recycling and scrap industries since the company was founded in 1946 by Ben Sacco. Sierra was one of the first equipment providers to introduce multitasking machines such as the shear/baler/logger to the United States, which improved productivity and profitability for small to medium-sized scrap processors. In addition to shear/baler/loggers, the company also provides two-ram balers, grapples and material handlers.
Terry Mohr, Sierra International regional sales manager for the western United States, spoke with Recycling Today about the benefits a stationary shear can bring to a scrap yard and what scrap processors should consider when shopping for this type of equipment.
Recycling Today (RT): For first-time purchasers of stationary shears, what are some of the most important considerations they should weigh?
Terry Mohr (TM): The ultimate reason a scrap dealer decides it is time to buy a stationary shear generally falls into one or all three of the following categories: one, the desire to improve production of processed scrap; two, to upgrade their scrap for the final purchaser (This simply means to size or densify material to the required steel mill specifications.); and, three, to be able to process different commodities.
Shears are commonly designed to bale, log or shear. As an example, you would bale or log white goods, car parts [and] whole cars in larger shears only for shredder feed. You would shear all bulky ferrous [and] unprepared material, cutting it to the desired length. Some large, bulky nonferrous scrap also can be sized properly. These are the main reasons, coupled with safety and reduced labor costs, that [using a shear can] make a scrap yard much more efficient and much more profitable.
RT: What material types are best suited for shearing?
TM: The best material for shearing is clean, unprepared general ferrous scrap that is free of contaminants, such as rubber, plastic, wood, insulation and all nonferrous materials. Some clean tin along with high-beam rebar cut to the proper length makes for an ideal steel mill package.
Ferrous scrap tonnages vary from customer to customer, but generally 800 to 1,000 tons per month makes the medium-sized scrap dealer a candidate for a stationary squeeze-box shear.
RT: At what level of tonnage does purchasing a stationary shear make more sense than using a mobile shear at a scrap processing operation?
TM: Mobile shears are great tools and are used extensively in construction and demolition operations; however, for a yard operation, the stationary shear is much faster, and one unit does the work of several mobile shears.
RT: What are the infrastructure requirements for a basic stationary shear installation?
TM: The electrical requirements are three-phased power, 440 to 480 volts, 60 hertz that range from 200 to 500 amp service, depending on motor size.
Stationary shears on outriggers on diesel power can be moved on a limited basis. The advantage to these shears is at startup, with fewer foundation requirements and fewer permits needed along with no electrical support required.
Foundations for our stationary shears vary in thickness based on local soil conditions. However, reinforced concrete is generally used for foundations because these shears weigh between 60 and 140 tons.
We recommend elevating the shear 3 to 5 feet on either high-beam or concrete piers. This allows for easier service and better evacuation of material under the shear throat.
The size of shear you need is determined by the production you desire on a daily basis. Stationary shear boxes generally range from 17 to 30 feet in length and 7 to 10 feet fully open. The shear foot range on newer models is between 2 and 4 feet for maximum density of processed material.
RT: What are some of the core operation considerations that must be considered for day-to-day operations as well as for maintaining the equipment?
TM: Cutting-force required is determined by the amount of material under the knife and by the thickness of the scrap to be cut. The simple formula for shears is that a bigger box equals more material. Heavy materials require more cutting force, and the end result is more production.
Daily service is a must when it comes to shears or any and all equipment in a scrap operation. Complete inspection should be done at the beginning and end of each work day. It goes without saying that we work in a very hostile environment. Fixing small problems today often can prevent large and expensive costs tomorrow.
Whether the equipment is backed by a company with parts and service may be the most important consideration in your buying process.
Typical shear life should be between 20 and 25 years, with a sound maintenance program.
RT: What factors generally lead an operator to upgrade to a larger shear?
TM: When a dealer moves up in shear size it is usually because he needs more tonnage on a daily basis,it may just be a desire for new technology or a tax advantage provided by some laws.
Going to a large shear versus two smaller shears is generally regarded as a cost-per-ton advantage. The exception would be specialized markets, such as those with boundary requirements, such as 3 feet and under for dense material.
The bottom line is that stationary shears continue to play a large role in scrap processing today. The technology to be able to shear, bale and log with one piece of equipment gives the medium-sized scrap processor the ability to compete in the open market and to provide high-quality processed scrap for either export or domestic consumption.
Sierra International Machinery, based in Bakersfield, Calif., is a processing equipment provider serving the scrap and recycling markets. More information is available at www.sierraintl.com.
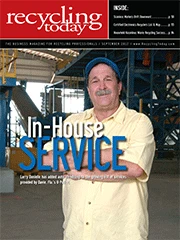
Explore the September 2012 Issue
Check out more from this issue and find your next story to read.
Latest from Recycling Today
- Massive Chinese steelmaking rebound recorded in March
- LME looks into sustainable metal pricing
- OnePlanet Solar Recycling closes $7M seed financing round
- AMCS launches AMCS Platform Spring 2025 update
- Cyclic Materials to build rare earth recycling facility in Mesa, Arizona
- Ecobat’s Seculene product earns recognition for flame-retardant properties
- IWS’ newest MRF is part of its broader strategy to modernize waste management infrastructure
- PCA reports profitable Q1