An effective safety process has identifiable elements. Each element contributes to the overall success of the strategy. The six key elements are:
- A written program;
- Safety training and communication;
- Evaluation and monitoring;
- Claims management;
- Benchmarking ; and
- Employee health and wellness.
In the feature “Effective Safety Management” in the July 2012 issue of Recycling Today (www.recyclingtoday.com/rt-0712-safety-focus.aspx), I outlined the first three elements of effective safety management. This article discusses the last three elements.
Managing Claims
The goal of a safety program is to prevent injuries and losses. However, if they do occur, they must be handled effectively. Effective claims management can provide the best medical care for an injured employee, improve recovery times and reduce the cost of a loss. Key steps to effective claims management include:
- Develop an effective incident investigation program—An incident investigation program should include investigation forms for use in the event of an injury or loss and an outline of the appropriate steps in an investigation. Supervisors should be trained to complete a thorough incident investigation. A post-incident investigation review will be key to identifying the root cause of the loss. An incident investigation should result in clear steps for preventing a repeat of the incident.
- Establish a relationship with a local occupational health provider—Local occupational health providers are often willing to visit a work location and to provide a detailed summary of the services they offer. Common services that a recycler would use include medical treatment for injured workers, respirator fit testing and medical evaluations, pre-hire and post-incident drug testing, soft tissue injury prevention training and assistance with early-return-to-work programs.
- Insurance carrier communication—In the event of a serious injury or loss, ongoing communication with the claims adjuster is needed. A strong relationship with your insurance broker can greatly enhance this. Additionally, when the employer or direct supervisor maintains contact with an injured employee, it can be helpful in reducing litigated Worker’s Compensation claims and in ensuring that the injured employee receives the proper medical care.
Measuring Results
For a recycling company, key performance indicators often are measured in tons per hour and dollars per ton. This data translates to measurement of profitability. Most companies subscribe to the idea of “if it is important, it is measured.” If your company is a for-profit organization, safety performance should be something that is important and measured.
Many recyclers have not considered how effective safety performance affects profitability. Zero losses will greatly reduce insurance and indirect costs.
Many areas of safety performance can be measured. Some common metrics are:
- Occupational Safety and Health Administration (OSHA) frequency and severity rates—The official terms are total recordable incident rate (TRIR) and days away, restricted and transfer rate. These are essentially frequency of injuries and frequency of lost-time injuries, and their calculations are outlined in the OSHA 300 log documents. The Bureau of Labor Statistics publishes rates for various industries.
- Experience modification rate—This number represents the frequency and cost of Worker’s Compensation losses during the past three years. A number of 1 is average, below 1 is better than average and above 1 is worse than average. The higher this number, the higher your premium will be for Worker’s Compensation insurance. Your insurance broker can help you find this number and how it affects your premium.
- Days worked without injuries—Many firms keep a running measurement of the number of days worked without an injury. This can be effective for keeping the entire workforce dialed into the status of your safety program. Employees understand that what is measured is important.
Maintaining Health & Wellness
Virtually every recycling company has the potential for air quality and noise level issues. OSHA publishes acceptable levels for various types of dust and for noise levels. Except in unusual cases, every recycler should conduct tests to determine baseline noise levels and should test dust. A local industrial hygiene testing company can provide information on specific tests for your facility.
Although OSHA does not require warm up, stretch and flex programs, many organizations are implementing them to help reduce employee injuries and to improve production. A local occupational health clinic may be a good first contact for resources to start this type of program.
Recycling companies should review their operations in each of the six categories identified in these two articles. Safety performance and injury reduction improvements will benefit the productivity and profitability of your operation.
Assurance’s John E. Schumacher, certified safety professional, is a safety, risk management and insurance professional with more than 20 years of experience in assisting organizations with developing strategic approaches to reducing losses and managing insurance costs. He can be contacted at jschumacher@assuranceagency.com.
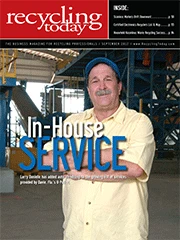
Explore the September 2012 Issue
Check out more from this issue and find your next story to read.
Latest from Recycling Today
- Acerinox names new North American Stainless CEO
- Greenwave closes 2024 books with red ink
- Steel Dynamics nets $217 million on record shipments
- Massive Chinese steelmaking rebound recorded in March
- LME looks into sustainable metal pricing
- OnePlanet Solar Recycling closes $7M seed financing round
- AMCS launches AMCS Platform Spring 2025 update
- Cyclic Materials to build rare earth recycling facility in Mesa, Arizona