>> METALS
Alcoa Assumes Control of Evermore Recycling
As of Aug. 31, 2012, Pittsburgh-based Alcoa assumed full control of Evermore Recycling, its previous joint venture with Atlanta-based Novelis. Evermore Recycling purchases used beverage cans (UBC) for the manufacture of new aluminum products.
As a result of the new agreement, Alcoa will take over full ownership and operation of Evermore Recycling and make it part of Alcoa’s Global Packaging group. Evermore Recycling will continue to be based in Nashville, Tenn.
The joint venture was first established in 2009 with plans to continue through 2014. In December 2011, Novelis approached Alcoa about withdrawing from the joint venture before the specified date, according to Alcoa.
“Alcoa’s Evermore Recycling is known throughout the world for its strong and committed relationships across the recycling supply chain and for its ability of making it easy to work together effectively,” says Alcoa Global Packaging President Andrey Donets. “When the opportunity first presented itself, we immediately said we wanted Evermore. We are confident the strong relationships we have in the scrap market will grow even stronger as we take over full control of the company.”
Alcoa’s Kevin Lowery says it is too early to predict other changes that may take place as Alcoa assumes ownership of Evermore. However, he adds that according to supplier feedback, they found Evermore somewhat difficult to work with. “The complexity of a joint venture made it a bit challenging,” he says. With Alcoa as the exclusive owner of Evermore, some of those problems can be alleviated, Lowery says.
>> METALS
Novelis to Establish UBC Buying Organization
Atlanta-based aluminum producer Novelis has announced that it will establish a new organization for procuring used beverage cans (UBCs) in North America. The announcement follows the company’s early withdrawal from the joint venture it formed with Pittsburgh-based Alcoa in 2009, known as Evermore Recycling.
Novelis will procure UBCs for its recycling plants in Greensboro, Ga.; Berea, Ky.; and Oswego, N.Y., directly through the new organization.
“This move is in line with our global strategy to enhance our scrap procurement and recycling assets to support our goal of achieving 80 percent recycled content in our products by 2020,” says Derek Prichett, Novelis vice president, global recycling. “The ability to independently control our assets and manage our business will provide us with more flexibility to execute our strategic plans. This is the primary driver behind our exit of Evermore.”
Novelis says it currently buys the equivalent of 40 billion cans each year, worth an estimated $1 billion, and expects its global consumption of UBCs to grow to more than 60 billion cans by 2015.
Chris Anderson, former Evermore supply chain manager, rejoined Novelis as of Aug. 1 to lead its new UBC procurement venture. He reports to Silverio Colalancia, director of recycling, Novelis North America.
>> PLASTICS
Midwest Exchange to Expand Illinois PET Recycling Plant
Midwest Exchange Enterprises Inc., a minority-owned plastics recycler based in Gurnee, Ill., has announced plans to expand its PET (polyethylene terephthalate) recycling plant to produce 100-percent-recycled PET (RPET).
The project involves securing an additional 40,000-square-foot industrial building and the purchase of specialized plastics processing equipment from AMUT S.p.A., based in Novara, Italy, to clean the PET stream.
“We believe this to be a great step in our sustainability program,” says Alex Casillas, president and founder of Midwest Exchange Enterprises. “It provides our clients with an environmentally friendly and cost-effective option to using virgin resin. Our goal is to eliminate our country’s dependency upon foreign virgin PET resin by producing locally and manufacturing recycled resin RPET from local sources of PET plastic.”
He continues, “When you evaluate what is happening here in North America, you see the demand for RPET increasing, especially in the thermoforming market.”
Concerning the supplier of the equipment for the new plant, Casillas says, “After careful consideration, we felt that AMUT would be the ideal company to partner with in this project.” He adds, “The equipment cleans the materials extremely well and will meet and exceed our clients’ requirements.”
The companies say the plant will be operational by March 2013.
>> ELECTRONICS
SRS Seeks E-Stewards Certification Across North American Facilities
Sims Recycling Solutions (SRS) Americas, with headquarters in Chicago, has announced plans to obtain e-Stewards certification at all 14 of its electronics processing facilities in North America. The company says its North American facilities already have ISO 14001, OHSAS 18001 and R2 (Responsible Recycling Practices) certifications as well as EPSC RVQP (Electronics Product Stewardship Canada Recycling Vendor Qualification Committee) certifications.
SRS says it has been working closely with Seattle-based Basel Action Network (BAN), the creators of the e-Stewards Standard and certification program, on a number of issues, including global waste trade policy and the improvement of the e-Stewards standard and its management.
Sims says it believes that e-Stewards provides the clearest, most unambiguous and robust approach to domestic electronic scrap processing and applauds the recent announcement by BAN to find a third-party host organization to administer for the e-Stewards program.
According to BAN, SRS has signed a contract with Orion Registrars. The company will conduct audits at all 14 of SRS’ North American electronics processing sites during the next year and a half as part of the certification process.
“As the largest electronics recycler in North America,” Steve Skurnac, president of SRS Americas, says, “Sims takes a very considered approach to legislative and market-based initiatives. The addition of the e-Stewards certification to our facilities demonstrates our commitment to meet the highest industry standards with respect to human health and the environment. Sims is a sustainability leader that will continue to pursue the most promising partnerships with other sustainability leaders in industry, in government and environmental organizations.”
BAN Executive Director Jim Puckett says, “Sims is not only the largest e-waste recycler in North America but they are among the true leaders in global sustainability as well.”
>> RUBBER/TIRES
Tennessee Awards $2.8 Million in Tire Recycling Grants
Tennessee Gov. Bill Haslam and Environment and Conservation (DEC) Commissioner Bob Martineau have announced that the state has issued 41 grants to help its communities recycle tires.
The tire recycling grants, totaling more than $2.8 million in fiscal year 2013-14, are supported by Tennessee’s Solid Waste Management Fund, which receives revenue from a pre-disposal fee on the purchase of new tires.
“Working with our local county partners is vital to the success of this program,” Haslam says. “The Solid Waste Management Fund continues to provide support to Tennessee’s communities, assisting in the diversion of waste tires from landfills for the benefit of the environment.”
The DEC administers the fund, and $1.25 from the $1.35 pre-disposal fee supplements costs for tire recycling and related services.
>> ELECTRONICS
GIA Releases Report on Global Electronics Recycling Market
The research firm Global Industry Analysts Inc. (GIA), San Jose, Calif., has released a report, “Electronics Recycling: A Global Strategic Business Report,” that looks at the global electronics recycling market.
The report finds that, driven by the growing awareness of recycling and environmentally safe disposal practices and the enforcement of government regulations, the global market for electronics recycling is expected to reach $34.5 billion by 2018. The authors of the report also say they expect regulations for managing obsolete electronics to ultimately benefit the recycling sector.
The report provides an overview of the electronic scrap market, environmental regulations, recycling markets, current market trends, key growth drivers, recent industry activity and profiles of major/niche global market participants. Separate analytics are provided for the U.S., Canada, Japan, Europe and the Asia-Pacific region. The 633-page report also provides annual revenue estimates and projections for the years 2009 through 2018 in value terms for a number of markets.
“Electronics Recycling: A Global Strategic Business Report” also profiles 262 companies, including AERC Recycling Solutions, American Retroworks Inc., Dlubak Glass Co., Eco International, Fortune Plastic & Metal Inc., MBA Polymers Inc., Sims Metal Management Ltd. and UniversalRecyclers.com.
The report is available for purchase at www.strategyr.com/Electronics_ Recycling_Market_Report.asp.
>> METALS
Airplane Dismantling Rates Could Soar
Larry Schneider, Boeing vice president for product development, said he expected the number of airplanes leaving the global fleet to nearly double in the next decade. Currently, nearly 400 planes are scrapped per year.
Speaking at the Aircraft Fleet Recycling Association (AFRA) Annual Meeting in Seattle in June, the Boeing executive said accelerated fleet replacement would “rapidly increase the demand for aircraft dismantling and recycling services and introduce unique challenges to the sector.”
Accelerated fleet renewal is being driven by higher fuel costs associated with older planes, Boeing says, which now make up some 60 percent of total operating costs, up from 30 percent in the not-too-distant past.
According to AFRA, around 44 percent of the global fleet—roughly 13,000 airplanes—will be replaced in the next 20 years.
“Our new generation of airplanes can reduce fuel burn costs by more than 20 percent. This is clearly a key factor driving the replacement of the fleet at higher rates,” Schneider said.
The age profile of airplanes being replaced also is dropping significantly, which should provide a boost to the dismantling and recycling industries, AFRA says.
Schneider said, “AFRA is leading the industry in the development of recycling technologies.”
He added that collaboration would be key in developing recycling processes and technologies if Boeing was to reach its stated aim of recycling 90 percent of airplanes by 2016. “Boeing looks for collaborative opportunities in the fields of dismantling and recycling; we look to work with the best people who have the capacity and the skills to accelerate the development of these technologies. It will take an enormous amount of collaboration when the rates of airplanes leaving the fleet are more than 400 a year,” he said.
The Boeing executive stressed the need for technologies that reduce the full life-cycle costs of recycling to give a higher recycling value to aircraft, so owners and airlines would want to recycle. “There needs to be a greater economic incentive to recycle,” he said.
Martin Fraissignes, AFRA executive director, said, “There needs to be greater market demand for recycled material. Manufacturers have to design these material options into their products, and recyclers have to develop new technologies and produce the volumes that encourage the whole process.”
According to Chicago-based Boeing, its closed-loop manufacturing system aims to deliver airplanes than can be reclaimed and recycled with less effort, placing more of a focus on the life-cycle value of the airplane.
Information on Boeing’s sustainability efforts is available at www.boeing.com/newairplane/environment/#/AirplaneProductionAndRecycling/Recycling.
>> METALS
Sadoff Iron & Metal Co. Plans Major Expansion
The scrap metal company Sadoff Iron & Metal has announced plans to significantly expand its recycling operations in Lincoln, Neb. The project will include relocating the company’s 2.5-acre site in Lincoln to a new 13-acre site that was formerly used by the U.S. Air Force as a fuel storage area.
“We are extremely pleased and excited by this project,” says Mark Lasky, Sadoff CEO. “We have a 12-year history in Lincoln and have outgrown our current facility. We are confident that this expansion will allow us to better serve the industrial and scrap retail markets in this region.”
Sadoff Iron & Metal is a part of Sadoff and Rudoy Industries, a scrap metal recycling firm headquartered in Fond du Lac, Wis. The company opened its Lincoln scrap metal yard in 1999 at the request of Deeter Foundry. In addition to its Lincoln plant, Sadoff has six scrap metal recycling facilities in Wisconsin.
The new Lincoln facility will be built in partnership with the Lincoln Airport Authority, which will issue industrial revenue bonds to cover the cost of the project. The scrap metal company will repay the Lincoln Airport Authority through fulfillment of a long-term lease agreement.
The project will include a 15,000-square-foot nonferrous metal warehouse, a 7,000-square-foot area for a baler, a 3,000-square-foot office area and a roof-covered area for scrap metal drop off. The parcel will be paved and engineered for “ease of use” ingress and egress traffic patterns, the company says.
According to Sadoff, the site will include Department of Environmental Quality-certified stormwater and environmental compliance features, security cameras and radiation detection equipment.
>> ELECTRONICS
Round2’s Ohio Plant Receives R2/RIOS Certification
The electronics recycling firm Round2 Inc., Austin, Texas, has earned the Responsible Recycling (R2) Practices/Recycling Industry Operating Standard (RIOS) Certified Electronics Recycler designation.
Round2 is a subsidiary of Avnet, Inc.’s electronics aftermarket company, Avnet Integrated.
Round2 achieved its certification following audits at its Grove City, Ohio, plant. The company also holds R2, ISO 9001, ISO 14001 and OHSAS 18001 certifications at all of its other North American processing centers.
“We have a long-standing reputation in the industry for our commitment to excellence,” says Randy Weiss, Round2 president. “Receiving our R2/RIOS certification clearly demonstrates this commitment, while recognizing the rigorous standards to which we adhere in all aspects of our operations.”
R2/RIOS combines two industry standards. The R2 standard establishes a hierarchy for the safe and responsible handling of electronic scrap. RIOS, developed by the Institute for Scrap Recycling Industries Inc. (ISRI), outlines a framework for a comprehensive, integrated management system.
>> METALS
Covanta Commences Metal Recycling System in Virginia
Covanta Energy Corp., a waste management and renewable energy services company, has officially opened a metal recycling system at its energy-from-waste (EFW) facility in Fairfax County, Va. The company, headquartered in Morristown, N.J., says the new metals recycling system is the first of its kind in North America and has been designed to recover small particles of nonferrous metal.
“Improving efficiency and sustainability are key aspects of our culture, and, as such, we are continuously looking for new ways to recover value from waste and divert materials from landfills,” says Covanta COO Seth Myones. “I’m proud of the way our team recognized the opportunity to recycle additional nonferrous metal and quickly got this new system up and running,” he adds.
In March Covanta announced a strategic alliance with Steinert US Inc. to implement nonferrous systems at Covanta facilities that currently do not have them and to enhance existing systems, such as Covanta’s Fairfax operations.
“We are proud to have achieved one of the highest recycling rates in the state at 47 percent and work hard to continually improve the recovery of recyclable materials,” says Joyce Doughty, Fairfax County Division of Solid Waste Disposal and Resource Recovery director. “The new recycling system at the EFW facility complements our recycling initiatives very nicely and is a great example of how energy recovery and robust recycling programs can go hand in hand.”
Covanta says its 41 EFW plants in North America recovered more than 400,000 tons of ferrous and more than 15,000 tons of nonferrous metals for recycling in 2011, converted 20 million tons of solid waste into 9 million megawatt hours of electricity and created more than 9 billion pounds of steam.
>> ELECTRONICS
Redemtech Becomes Canada’s First E-Stewards-Certified Recycler
The IT asset disposition firm Redemtech, headquartered in Columbus, Ohio, has announced that its Guelph, Ontario, Canada, technology change management (TCM) center has been certified to the e-Stewards Standard.
“As Canada’s first e-Stewards-certified recycler, we are uniquely qualified to meet the demands of government agencies and companies in Canada for e-waste disposition practices that meet the highest standards for protecting the environment and ensuring corporate social responsibility,” says Kuljit Parmar, president, Redemtech Canada. “Our deep understanding of the Canadian marketplace and regulatory environment enables us to eliminate risk from the recycling process and deliver a solution that exceeds customer expectations.”
Redemtech’s U.S. and U.K. operations also are e-Stewards certified, with the U.K. location becoming Europe’s first certified recycler in September 2010, the company says.
Its Ontario TCM center also is ISO 14001, ISO 9001 and OHSAS 18001 certified, while its British Columbia facility is in the process of completing these certifications and e-Stewards.
Redemtech President Robert Houghton says, “These certifications demonstrate our commitment to serving large enterprises as a global partner that can deliver a consistent offering across borders, languages and industries that surpasses customer expectations and delivers on world-class standards of practice.”
Jim Puckett, executive director of Seattle-based Basel Action Network, administrator of e-Stewards, says, “As the first e-Steward in Canada, Redemtech is ensuring the highest standards of environmental stewardship as it expands its global presence.”
>> METALS
Alter Shredder in Nebraska Clears Hurdle
The Norfolk, Neb., Planning Commission has approved Alter Metal Recycling’s plan to locate an auto shredder at its scrap processing yard in the city. Alter Metal Recycling is a subsidiary of St. Louis-based Alter Trading Corp.
The next step in the approval process is going in front of the Norfolk City Council.
The company plans to install a 5,000-horsepower Metso 88-by-116 auto shredder with a smart water-injection system and a cyclone cleaning system.
The City of Norfolk's Trent Howard says the company will pour concrete on site and will include a retention pond to capture run-off water.
In approving the auto shredder, the planning commission stipulated a number of conditions, including resurfacing the roads leading to the yard and providing dust control; limiting the shredder’s hours of operation to between 7 a.m. and 5 p.m. Monday through Friday; and filing a stormwater pollution-prevention plan and authorization to discharge with the city.
>> METALS
ISA Opens Auto Recycling Operation
Industrial Services of America (ISA), a Louisville, Ky.-based scrap metal recycling company, has opened its first auto recycling facility on the site of its main scrap processing location in Louisville. ISA says it expects the new business, called ISA Pick.Pull.Save, to help supply its auto shredder with a steady supply of auto hulks.
Bob Coleman of ISA says that at full capacity the new company will be able to house 1,500 vehicles.
“ISA made the decision to get into the auto parts business in order to secure scrap metal at its earliest point of entry into the market and reduce its supply chain risk,” says Brian Donaghy, ISA president and COO. “The obvious benefit to this is that we are also able to provide customers with a cost-effective way to buy auto parts.”
The company says ISA Pick.Pull.Save features a streamlined, computerized inventory system that catalogs parts on site and will be staffed by experienced mechanics.
>> METALS
Grede to Supply GM Truck Components
Grede Holdings LLC has secured contracts for about $150 in content per vehicle with various tier 1 suppliers for General Motors’ upcoming K2XX truck platform. The company will supply parts made in its iron foundries for the K2XX platform, which includes the Chevy Silverado, Tahoe and Suburban, the GMC Sierra and Yukon and the Cadillac Escalade.
Grede will produce several components, including brake calipers, control arms and differential carriers and cases, at its foundries in Wisconsin, Virginia, Minnesota, Alabama and Mexico. As of 2010, Grede foundries had 600,000 tons of iron-making capacity, with scrap as its key feedstock. (Read our 2010 profile of Grede Holdings at www.RecyclingToday.com/ferrous-consumer-feature-april-2010.aspx.)
The iron components will be sent to various General Motors’ tier 1 suppliers in North America, who will assemble them into components and systems for the auto manufacturer. The K2XX truck platform will be assembled by General Motors at plants in Indiana, Michigan, Texas and Mexico, with volumes approaching 1 million trucks per year.
“We are very excited about expanding our relationship with General Motors and the tier 1 suppliers for this platform, which is one of the top selling in North America year-in-and-year-out,” says Tony Lovell, vice president of global sales and marketing at Grede. “We have a long-standing relationship with General Motors and supplied similar content on the predecessor T900 platform.”
Grede Holdings LLC manufactures ductile, gray and specialty iron castings at 17 foundries and four machining operations in North America for the global transportation and industrial markets.
>> ELECTRONICS
GEEP Opens Facilities in Alberta, Quebec
GEEP (Global Electric Electronic Processing) Calgary, Canada, has relocated its operations within that Alberta city.
Anthony Jones, GEEP general manager, says, “To keep pace with the changes in our industry, the move into our new facility will allow GEEP Calgary to streamline our processes to better meet our customers’ needs. With our new footprint we have customized our new building to better fit our requirements and help meet future expansion. Our goal is to meet and exceed current customer requirements and ensure we are prepared for future expansion while keeping our costs in line.”
The new site will continue to offer services such as technology asset management, end-of-life electronics collection, metal recycling and computer equipment wholesale.
In related news, Barrie, Ontario-based GEEP recently opened a new facility in Laval, Quebec. The move to Laval follows the company’s strong growth in recycling activities, which have increased from 1 million to 12 million pounds of material per year since 1998, GEEP reports.
The new 77,000-square-foot premises is more than double the size of its previous facility in Dorval, Quebec. The company says the new plant will serve customers in Quebec, the Maritimes and eastern Ontario. The relocation project required an investment of $2 million and will create 20 new jobs, according to the company.
After evaluating opportunities across the greater Montreal region, the management of GEEP chose to settle in Laval for strategic reasons. “Here, we have a major road network and public transit that make it easier for our employees to commute. Laval has the only park that meets our diverse industrial needs and offers retail opportunities,” says Guy Messier, president of GEEP Montreal.
The company says it plans to double the volume of material the Laval facility handles in the next three years and to invest in equipment to process glass from televisions and CRTs on site.
>> METALS
Severstal Hosts Dearborn Steel Mill Grand Opening
Severstal North America, based in Dearborn, Mich., has reopened the historic River Rouge steel mill in Dearborn. The North American branch of Russia’s OAO Severstal has invested $1.4 billion in the Detroit area steelmaking complex.
“From the day we first acquired the Rouge assets eight years ago, we had a long-term vision for this plant,” said Alexey Mordashov, CEO of OAO Severstal. “Being located here in the heart of the automotive industry with a strong heritage and spirit of innovation, we are proud to be able to continue on the traditions of the great past and on to the bright future.”
Upgrades at the River Rouge mill include constructing a pickle line tandem cold mill (PLTCM) and hot-dip galvanizing line (HDGL). The $450 million PLTCM includes accompanying control systems. The $285 million HDGL has been designed to ensure consistent coating thickness and surface texture, according to Severstal.
>> PLASTICS
MRC Polymers Introduces Recycling Solutions Division
MRC Polymers, a Chicago-based plastics recycling company, has launched a new division known as Recycling Solutions. According to MRC, the new division seeks to help companies derive the highest value possible from their scrap.
“We want to make sure material is recovered to its highest potential,” says Dean Eberhardt, president of MRC’s Recycling Solutions Division. “Recycling into low-end products is great for keeping things out of the landfill, but we like to take it to the next level, ideally by closing the loop.”
The company will seek rigid plastics from industrial manufacturing plants, particularly those within the auto industry.
Paul Binks, MRC Polymers CEO, says the company recovers post-consumer bumpers, which it grinds, washes and compounds into pellets using a proprietary process.
>> PLASTICS
EPI to Expand North Carolina Plastics Operation
EPI Recycling Solutions LLC, based in Erie, Pa., has announced plans to expand its Sanford, N.C., plastics operations to allow the company to handle most grades of plastic scrap. The company will invest $1 million to add a new recycling line that will allow it to recycle more than 14 million pounds of plastics per each year.
EPI says the core of the expansion is the addition of the S:GRAN recycling machine, produced by the Austrian company NGR.
“We are excited to add the NGR equipment to our offering of services and see this is as a long-term investment in North Carolina,” says EPI President Kurt Duska. “We believe that coupling the latest design in recycling equipment with our creative recycling concepts will allow companies to convert waste plastic cost to revenue and improve their environmental position.”
Duska also is president of Engineered Plastics LLC, a plastic recycler and molder that develops, implements and manages industrial sustainability programs.
>> METALS
Utah’s Metro Group Opens New Plant
Metro Group Inc. has opened a new recycling facility in Salt Lake City. It is one of four plants the company operates in that metropolitan area. The latest plant processes scrap metal and recovered fiber.
The company has installed a Harris baler and a Sierra 900 model shear at the site. Chris Bond, a spokesman for Metro Group, says the goal of the new facility is to process 25,000 tons of ferrous scrap per year and 8 million pounds of nonferrous metals per month. The new facility also will be used as Metro’s main yard and headquarters location. Its other facilities will be used as feeder yards.
The new facility is located on 40 acres in the city with 25 acres being used currently. The new location will be on concrete and includes an 80,000-square-foot building that will be used as a warehouse and a 16,000-square-foot office building.
The plant also has an 80-car rail spur on its site designed to give the company greater flexibility in shipping material. The rail spur also allows the company to offer customers the cost advantages of rail freight without requiring the capital investment of railroad access, additional personnel or equipment needed to unload rail cars, according to Metro Group.
Metro Group currently operates transloading stations in Salt Lake City and Carlin, Nev.
Metro Group has been in business under its present name for the past 35 years. In addition to the four Metro Group-branded facilities in the Salt Lake City area, the company operates three additional recycling facilities under different names in Utah.
>> ELECTRONICS
Natural Evolution Receives E-Stewards Certification
Natural Evolution, a Native American, woman-owned electronics recycling company based in Tulsa, Okla., has become the state’s first recycler certified to the e-Stewards Standard for Responsible Recycling and Reuse of Electronics, according to the Basel Action Network (BAN). Seattle-based BAN administers the e-Stewards program.
Natural Evolution says it received e-Stewards certification after passing an audit to ensure it was responsibly handling electronic scrap. Companies applying for e-Stewards certification also must have an ISO 14001 environmental management system certification. Natural Evolution also received R2 (Responsible Recycling Practices) certification, another certification for the electronics recycling industry.
Traci Phillips, CEO of Natural Evolution, says the certification confirms the company’s commitment to recycling electronics without causing environmental, economic or social harm.
“It is our belief that the e-Stewards Standard is by far the most rigorous and responsible standard that exists today for the electronics recycling industry,” she says. “It provides for the continuous monitoring and auditing of downstream recyclers and material flow, ensures the proper handling of e-waste and prevents the illicit export of hazardous waste to developing countries.”
Get curated news on YOUR industry.
Enter your email to receive our newsletters.
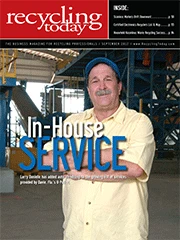
Explore the September 2012 Issue
Check out more from this issue and find your next story to read.
Latest from Recycling Today
- Lautenbach Recycling names business development manager
- Sebright Products partners with German waste management equipment company
- WasteExpo transitions to biennial format for enhanced experiences
- Study highlights progress, challenges in meeting PCR goals for packaging
- Washington legislature passes EPR bill
- PureCycle makes progress on use of PureFive resin in film trials
- New copper alloy achieves unprecedented high-temperature performance
- Gränges boosts profits and sales volume in Q1 2025