Plastics once considered difficult or impossible to recycle are being converted into fuels. Items such as carpeting, construction and demolition plastics, tires and industrial polymer scrap that most often are shipped to a landfill for disposal now are being collected by energy producers that have developed technology that can turn this material into crude oil, natural gas or other fuel products. Several common methods are used to convert plastics to energy.
Kim Holmes, principal consultant at 4R Sustainability Inc., Ore., says, "Some systems operate in a vacuum, some operate at atmospheric pressure, some replace oxygen with a gas."
Pyrolysis, the thermal treatment of plastics that results in a gas, is a common conversion method. Depolymerization, a chemical process that separates the large molecules (polymers) into smaller molecules (monomers), also is being used by some companies. While they employ different techniques, these conversion methods offer once unrecyclable (or costly to recycle) plastics a different end-of-life dispositon.
Effective Conversion
Residue-to-energy conversion of plastics has several advantages say advocates of the process, besides being a viable alternative to landfilling tons of plastics each year. Conversion technology is believed to create little pollution, Holmes says. "These systems can all operate under a simple air permit. Information suggests that converting plastics to oil produces much fewer environmental problems than incineration," she adds.
It's also believed to be a smart business endeavor, judging by the number of companies who are investing in the technology. Many operations are joint ventures between feedstock suppliers and convertors, and collection costs are generally low.
Vadxx Energy, a Cleveland-based company, says it uses a continuous depolymerization process that takes long chains of polymers and breaks them down into shorter chains of hydrocarbons in the form of light, sweet synthetic crude and hydrocarbon gas.
Sean Arnold, Vadxx Energy chief operating officer, says he has found the continuous depolymerization process to be energy efficient. It also allows his company to use different sources of feedstock while achieving a consistent process "that meets the specifications of the refining marketplace," he says.
Chris Ulum, Agilyx CEO, Tigard, Ore., says, "The Agilyx base system consists of four primary vessels and is capable of converting approximately 10 tons of plastic into approximately 60 barrels, or 2,400 gallons, of oil per day."
Polyflow LLC, Akron, Ohio, says it uses a patented thermal pyrolysis process that breaks apart the polymers into a set of reactive species and then allows them to reform into aromatic chemicals, which are the lightest and most valuable chemical compounds produced from crude oil.
Jay Schabel, Polyflow CEO, says, "The benefit of our process is that it can take all forms of polymer waste without sorting and cleaning, so the raw material and processing cost is very low. Just as important is the fact that it produces a light, clean and valuable end product that was previously made from crude oil. The net result is a business model that works without government subsidies or requiring special contracts to make it financially viable. It is both financially and environmentally sustainable."
Additionally, the proximity of the systems to the plastics generators is typically beneficial to everyone. Holmes says, "They are generally 7,000-to-10,000-tons-per-year systems. They can be placed at the MRF (material recovery facility), paper mill or other generator of non-recyclable plastic material." Systems that cannot be placed at the same location as the feedstock source in light of space restrictions are placed nearby.
Ulum says it is typically simple to accommodate plastics-to-energy solutions that suite large and small markets.
Arnold says, "While not every implementation will be able to supply 100 percent of the required tonnage using existing material at one existing partner facility, there are significant economies of scale in minimizing the percentage and range from which feedstock material is pulled." He adds, "So local and regional implementations are preferred, but the real test is the total cost, including transportation, of getting material to the joint venture dock door. Insomuch as efficient lanes can be designed to keep such costs reasonable, there is no physical limit to the area that can be served by a specific facility."
The convenient locations of these plants can reduce the carbon footprint of hauling waste and transporting oil from the other side of the world to supply fuel to that city.
Free Fuel
Because these conversion technologies work on a variety of plastics, gathering feedstock can be fairly simple, sources say. For instance, every system can handle packaging materials. Companies say they are finding a sizable volume of material to choose from at MRFs.
"The easiest is the waste from the recycling facilities that is presently flowing to the landfills," Schable says. "Recycling facilities are typically not able to recycle all of the plastics that are put in the bins. In fact, most often it is just the pop/water bottles and the milk jugs that offer a viable market worth picking them out."
Plastics that are not practical for recyclers to recover and sell can then be diverted for conversion into energy; but, energy companies know they must be cautious when it comes to certain types of plastics. Holmes says, "PVC and PET can be a problem, as can some additives, such as BFRs (brominated flame retardants), which all become acidic in the process. Those acids then need to be removed, so you end up with a quality product. Some systems can handle carpet, some can handle BFRs."
Once the feedstock is collected, it must be reduced in size and dried before it is ready to go through the conversion system. The recycler that is supplying the feedstock may be responsible for this, though some plastics-to-energy producers are able to shred the material at their facilities.
The economic model for most residues-to-energy companies assumes there will be little to no cost per ton of material collected. However, return on investment usually is around five years, according to Holmes.
Arnold says, "The solid feedstock input for each unit ranges from 12,000 to 16,400 tons per year, depending on the feedstock, and produces 80,000 barrels of oil per year." He adds that the technology is profitable when oil is above $35 to $45 per barrel, depending on the feedstock. "Oil futures going out at least five years predict world oil prices in excess of $100 per barrel," Arnold says.
Another way to look at the potential returns is by measuring an average daily production capability.
"The size of an operational system varies based on the client's feedstock supply," Ulum says. "The smallest unit is one vessel, which processes 2.5 tons of plastic per day into about 2 tons of fuel (about 16 barrels). The vessels are modular and can be added to increase capacity over time."
Noticeable Returns
Energy recovery also varies among energy companies. Some processes produce a fleet-ready fuel product, while others produce a crude oil that must be further refined by a third party.
Ulum says Agilyx finds it most efficient to manage the off-take contracts for its waste and recycling clients. Waste materials generated by the process also can be managed this way, as in Agilyx' case, where it found end users for its solid carbon residue (char).
Char, the by-product of this technology, can be sold to manufacturers who are experimenting with alternative uses for the material, including carpet, roofing or road materials. Some facilities have the ability to incinerate char on site for additional energy recovery. Schabel says the char can sometimes be burned at 30 percent of the Btus (British thermal units) needed to heat 1 pound of water. It is believed to be safe to send char to a municipal landfill, if necessary.
Holmes says, "The amount of char produced will vary by how contaminated the load is with non-plastic material and how many additives and fillers are present in the plastics." She cites calcium carbonate, clay and carbon black as common additives.
Energy recovery measurements also can vary by company. Vadxx Enery, a depolymerization process user, measures its crude oil yield to determine how much energy it recovers.
"It ranges between 55 percent to 75 percent by weight on input tonnage, depending on the feedstock in question," Arnold says. "The balance of the input tonnage is converted to hydrocarbon gas and char."
Polyflow, which uses pyrolysis, compares the amount of Btus per average ton of mixed polymer scrap that would otherwise enter the landfills with the amount of Btus it can capture using its conversion process.
Schabel says, "The average ton of mixed polymer waste entering our landfills contains 33 million Btus. Polyflow is able to capture 27 million Btus by adding only 1.7 million Btus of external energy. That is a 15 times yield of energy in to energy out."
* An earlier version of this article incorrectly attributed comments from Agilyx to Jamil Karim. Those comments come from Chris Ulum.
The author is assistant editor of Recycling Today and can be contacted at kstoklosa@gie.net.
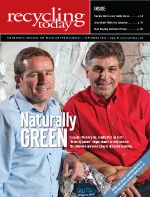
Explore the September 2011 Issue
Check out more from this issue and find your next story to read.
Latest from Recycling Today
- Hyundai says it will make steel in the US
- APR announces Recycling Leadership Award winners
- Glass Half Full opens glass recycling facility in Louisiana
- AmpUp partners with Roundtrip EV
- Global Recycling Day event supports Pittsburgh school's recycling efforts
- President signs executive order on critical minerals
- Registration opens for Scrap Expo 2025
- Toyota opens ‘circular factory’ in UK