Domestic recovered fiber supply continues to decline in light of the decrease in recovered fiber generation and the contraction of the paper industry. A booming export market is also taking a bite out of domestic supply. Paper recyclers and consumers of recovered fiber have had to consider new markets for material and have had to determine the best way to get that material from point A to point B.
The latest figures from the Paper Industry Association Council of the American Forest & Paper Industry (AF&PA), Washington, D.C., indicate that 40 percent of recovered fiber generated in the U.S. was exported in 2010.
Recyclers and paper mills aren't the only companies affected by these trends. Transportation firms have been competing for recovered fiber shipments.
Transportation company Norfolk Southern (NS) has implemented programs and technology designed to allow its rail system to stay competitive despite decreasing recovered fiber volumes too.
W. Baird Spicuzza is the marketing director for the paper division of Norfolk Southern's Paper, Clay & Forest Products marketing team, based in Norfolk, Va. Having held this post since 2005, he has witnessed many of the changes that have affected shipments of recovered fiber. Spicuzza's focus is on the development and yield management of rail transportation markets for pulpboard, printing paper, newsprint, wood pulp and recovered fiber.
Spicuzza told Recycling Today Associate Editor Kristin Smith about NS' strategy to grow its stake in the transportation of recovered fiber.
Recycling Today (RT): What has happened with the volume of recovered fiber shipments via rail since 2009? What factors are affecting this figure?
W. Baird Spicuzza: Norfolk Southern carload volumes dropped in 2010 by 5.7 percent in comparison to 2009. 2011 year-to-date vs. 2010, our volumes are down by 6.8 percent. Volumes are being impacted by declines in domestic paper production, resulting in reduced demand. Increased realization in the export market has caused East Coast production to migrate to the ports, usually by truck or intermodal. The resulting high cost of recovered paper has also prompted some paper producers to increase substitution of virgin fiber at the expense of recovered fiber.
RT: What are the advantages of using rail to transport paper vs. trucks? What drawbacks are there?
Spicuzza: Our focal point is boxcars. With the cubic capacity of boxcars, we can load from 28 percent in our 50-foot Plate C "standard" boxcar to 83 percent more in our 60-foot F "high cube" boxcar vs. a 53-foot truck trailer's capacity. A truck can usually carry on average 21 tons, whereas the rail car can load up to 70 tons in a 50-foot standard boxcar and up to 100 tons in a 60-foot high cube boxcar. Because of the capacity benefits of boxcars over trucks, the advantage to using rail is that we can often offer a lower cost per ton to ship scrap paper by rail, especially on medium and long hauls.
Another advantage is the reduction in CO2 (carbon dioxide) emissions/carbon footprint associated with rail deliveries vs. trucks. This is becoming increasingly important for our customers, and we have a Web-based tool to calculate the resulting reduction in CO2 emissions by using rail.
A challenge for rail deliveries: The rail industry is not as nimble as the trucking industry, and our ability to furnish equipment on short notice is sometimes difficult. That said, most supply chains are firmly established and allow for sufficient planning to leverage the benefits associated with rail.
RT: What new advancements are helping to improve railcar transportation?
Spicuzza: We have new software that helps us educate our customers to maximize the stowage of each railcar by providing a schematic of the loading as well as the placement of the dunnage to provide a secure and safe load. Again, this helps the customers to reduce their cost per ton. Plus, we have two Web-based programs for our customers to order empty rail cars or release loaded cars as well as tracing their loads. We also provide automated and customized reports to customers in addition to the two computer interfaces, so the customers can plan and track their freight.
ON THE AGENDA W. Baird Spicuzza, marketing director for the paper division of Norfolk Southern’s Paper, Clay & Forest Products marketing team, is among the speakers presenting at the 2011 Paper Recycling Conference, hosted by the Recycling Today Media Group. (See “Culture of Connection,” p. 110.) The conference is scheduled for Oct. 23-25 in Chicago at the Marriott Chicago Downtown Magnificent Mile. ![]() More information is available at www.PaperRecyclingConference.com. |
RT: What are the cost considerations?
Spicuzza: The longer transit times associated with rail deliveries may increase working capital requirements, depending upon terms of sale; but, these are usually more than offset by the lower freight rates. Generally speaking, so long as customers effectively manage the inventory pipeline, there are no cost considerations for rail vs. truck. In fact, there are often less administrative expenses, since fewer boxcars will be required to move a similar amount of product by truck.
RT: What is Norfolk Southern doing to encourage paper mills/recyclers to use railcars and has NS' Bails on Rails program been successful?
Spicuzza: We are extending the buying power of the paper mills/recyclers by providing effective rates per ton for material two to three states away from a mill that a buyer would typically buy locally. With export demand tightening supply, this pricing has been very effective by extending the sourcing of scrap paper beyond typical truck markets.
While Bails on Rails has struggled with the domestic economy as well as the strong pull of the export market, we have picked up traction with key customers who understand the impact that the supply chain can have on reducing mill furnish costs as well as driving boxcar supply for the loading of outbound paper products. We're also trying to reduce the complexity of doing business by rail by keeping our pricing simple with no hidden charges or fuel surcharge. Therefore, the customer knows upfront its whole transportation cost.
RT: What tools are available to paper mills/recyclers to track shipments?
Spicuzza: We have our Web-based accessNS e-commerce tool, where the customers can easily bill, track and trace their shipments and verify the weights of the rail cars. Within accessNS, we also have Pacesetter, an e-commerce tool that allows customers to order empty railcars in advance and release a railcar once loaded or emptied. Pacesetter also provides customers visibility of their shipment pipelines so customers can effectively manage their supply chains while reducing their opportunities for demurrage costs. These systems are customer/user friendly and efficient.
RT: Does rail represent a more viable option for shipping to from Mexico?
Spicuzza: Yes. Considering the long truck haul from east of the Mississippi River (the region Norfolk Southern directly serves), we can provide a very competitive rate vs. truck. We work very closely with the BNSF, CG Railway, Kansas City Southern Railway, Kansas City Southern de Mexico and the Union Pacific in providing through rates to Mexico. Many shippers in Mexico need cost-effective means to ship their finished goods back to the U.S. Midwest and East Coast. By shipping scrap paper to Mexico, we are in fact supplying cars to support this northbound demand.
RT: How can rail be combined with other forms of transportation?
Spicuzza: With the shortage of ocean containers in the U.S. Midwest, we have been educating export scrap paper brokers and suppliers on the advantages of shipping the scrap paper to the U.S. East Coast ports and, in particular, Southeast ports, in a boxcar. Since more freight can be loaded in a boxcar vs. a truck and sourced from an inland location where the scrap paper cost per ton is cheaper as well, it pays to ship the freight to a port via rail car and transload the scrap paper into an ocean container. The ocean container's weight can be maximized at 25 tons vs. a typical over-the-road weight of 21 tons.
The reduced cost per ton in ocean freight with more weight in an ocean container as well as the cheaper rail freight makes transloading a viable option. This helps us reposition boxcars to areas where there is demand while assisting the container steamship lines in filling their surplus containers located at the ports on the U.S. East Coast.
W. Baird Spicuzza is director of marketing for the paper side of Norfolk Southern.
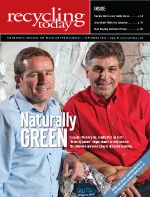
Explore the September 2011 Issue
Check out more from this issue and find your next story to read.
Latest from Recycling Today
- APR announces Recycling Leadership Award winners
- Glass Half Full opens glass recycling facility in Louisiana
- AmpUp partners with Roundtrip EV
- Global Recycling Day event supports Pittsburgh school's recycling efforts
- President signs executive order on critical minerals
- Registration opens for Scrap Expo 2025
- Toyota opens ‘circular factory’ in UK
- Agilyx works with former Plastic Energy CEO on sourcing venture