> MUNICIPAL
Waste Management Acquires Oakleaf
Waste Management Inc. (WM), Houston, has closed on the acquisition of Oakleaf Global Holdings, Hartford, Conn., and its primary operations for $425 million. WM says the deal brings together one of the largest networks of directly owned hauling, recycling, diversion and disposal assets with one of the largest managed third-party networks.
Oakleaf has a North American vendor network of 2,500 preferred haulers and describes itself as North American's largest outsource firm for hauling, disposal, recycling and waste diversion services. The Oakleaf operations WM has acquired generated nearly $580 million in revenue in 2010, according to the company.
According to WM, Oakleaf shares WM's focus on technological innovation and sustainability and says its substantial base of national accounts and service relationships offer a growth opportunity for the company.
David Steiner, WM president and CEO, says, "Acquiring Oakleaf advances our growth and transformation strategies of knowing more about our customers and how best to serve them, extracting more value from the material that we manage and optimizing our operations. We substantially increase our national accounts customer base and further enhance our ability to provide comprehensive, best-in-class environmental solutions."
Steiner continues, "In addition, Oakleaf's vendor hauler network expands our service footprint to new geographies and enhances customers' one-stop shopping for environmental solutions.
"Importantly, Oakleaf's vendor network expands our partnership with third-party service providers," Steiner adds. "In many cases, we can provide Oakleaf's vendor haulers with opportunities to maintain and increase their business by utilizing our extensive post-collection network. This will generate significant benefits for WM and for the vendor haulers."
Steve Preston, Oakleaf president and CEO, says, "Oakleaf brings a waste hauling, waste diversion and recycling vendor network along with a shared focus on customers. I am confident that our customers will benefit from WM's material recovery strategies that provide customers with multiple options.
"Our vendor hauler partners will also benefit from the increased array of services that they can offer to their customers—enabling them to grow their businesses further," Preston continues. "I look forward to joining the WM team to ensure a smooth transition."
The company says the acquisition aligns with its financial goals of growing earnings, expanding margins, increasing free cash flow and increasing returns on invested capital.
WM says it expects the integration period to be from three to six months and anticipates certain costs associated with the integration and, therefore, does not expect the transaction to be accretive to earnings during that time. Subsequent to the transition period, the company forecasts generating a minimum of $80 million in EBITDA (earnings before interest, taxes, depreciation and amortization) on an annualized basis.
More information about WM is available at www.wm.com.
> SCRAP INDUSTRY NEWS
ThyssenKrupp Waupaca Re-opens Tennessee Foundry
ThyssenKrupp Waupaca Inc., based in Waupaca, Wis., has announced plans to re-open its Etowah, Tenn., foundry by the first quarter of 2012. The foundry was idled in January 2010 in light of the downturn in the North American automotive and truck markets, according to the company.
Tennessee Gov. Bill Haslam says, "This is great news for McMinn County (Tennessee). I am confident the skilled workforce in Etowah will provide a fine foundation on which the company can return to business and help grow the area economy."
The decision to re-open the facility follows a pickup in demand for its finished product and reflects the company's commitment to meeting the long-term supply requirements of its customers and confidence in future growth prospects, according to ThyssenKrupp Waupaca.
"The re-opening of our Etowah foundry is good news for our customers and for the state of Tennessee but also for the men and women we will be able to put back to work," says Gary Gigante, president and CEO of ThyssenKrupp Waupaca.
ThyssenKrupp Waupaca will start installing new melt, core and mill room equipment in the foundry for ductile iron production beginning in the third quarter of 2011. The foundry will add 20,000 square feet of manufacturing space to the plant to accommodate the new equipment.
Startup of the facility will occur in two phases, beginning with gray iron. Gray iron will begin production in early 2012, reaching full capacity by mid-to-late third quarter of 2012. Production of ductile iron will begin in the second quarter of 2012.
The company plans to reach full capacity by the first quarter of 2013.
> ELECTRONICS
Obama Administration Unveils National Strategy for Electronics Stewardship
The Obama Administration has released its "National Strategy for Electronics Stewardship," an approach to the responsible design, purchasing, management and recycling of electronics that is designed to promote the electronics recycling market and jobs in the country. (For a closer look at the new strategy, see the feature, "Stewardship Strategy," on p. 104.) U.S. Environmental Protection Agency (EPA) Administrator Lisa P. Jackson, General Services Administrator (GSA) Martha N. Johnson and White House Council on Environmental Quality Chair Nancy Sutley were joined by the CEOs of Dell Inc. and Sprint and senior executives from Sony Electronics for the announcement, which took place in mid-July at electronics recycler Round2's Austin, Texas, plant.
The announcement included the first voluntary commitments made by Dell, Sprint and Sony to the EPA's industry partnership designed to promote environmentally sound management of used electronics. The administration's strategy also commits the federal government to taking specific actions to encourage environmentally friendly design of electronic products, promote recycling of used or discarded electronics and advance a domestic market for electronics recycling to protect public health and create jobs.
The responsible management of electronics provides an opportunity to create economic development and jobs by developing a strong domestic electronics recycling market while preventing pollution at home and abroad, according to a press release issued by the GSA.
As outlined in the strategy report, the federal government will:
- Promote the development of more efficient and sustainable electronic products;
- Direct federal agencies to buy, use, re-use and recycle their electronics responsibly;
- Support recycling options and systems for American consumers; and
- Strengthen America's role in the international electronics stewardship arena.
Under the strategy, the GSA will remove products that do not comply with energy-efficiency or environmental performance standards from its information technology purchase contracts used by federal agencies and will ensure that all electronics used by the federal government are re-used or recycled properly. Several federal agencies will work together to identify methods for tracking used electronics in federal agencies to move toward re-use and recycling, the GSA says.
A key component of this strategy includes using certified recyclers and increasing safe and effective management and handling of used electronics in the United States, working with industry in a collaborative manner to achieve that goal. As a first step in this effort, EPA Administrator Jackson has signed a voluntary commitment with Dell CEO Michael Dell and Sprint CEO Dan Hesse to promote a U.S.-based electronics recycling market. Representatives from Sony Electronics also have committed to improving the safe management of used electronics.
This collaboration with industry is designed to encourage businesses and consumers to recycle their electronics with certified recyclers. The strategy also encourages electronics recyclers to become certified.
> SCRAP INDUSTRY NEWS
ISRI Study Highlights Economic Benefits of Recycling
A study released by the Institute of Scrap Recycling Industries Inc. (ISRI), Washington, D.C., shows that the U.S. recycling industry generates more than $10 billion in revenue per year and employs more than 450,000 people.
The study, conducted by John Dunham and Associates, examined different kinds of economic activity—jobs and exports—and direct and indirect economic effects at the national, state and congressional district levels.
The survey finds the total economic activity generated by scrap recycling in the United States exceeds $90.6 billion, making the industry similar in size to the nation's forestry and fishing industries combined.
Notably, according to the study, the U.S. scrap recycling industry adds as much to the nation's economy as the coal mining industry.
ISRI President Robin Wiener says, "Despite tough times, our industry is directly and indirectly putting more than 450,000 people to work while generating revenue for federal, state and local governments. All this adds up to recognition that the scrap recycling industry must be allowed to grow so it can continue to boost our economy, put people to work, protect our environment and help save energy."
The economic study can be viewed in its entirety online at www.isri.org/2011scrapjobstudy.
> SCRAP INDUSTRY NEWS
Metalico Reports Income Increase
Metalico Inc., headquartered in Cranford, N.J., has reported net income of $6.6 million for the second quarter of the fiscal year, a 50 percent increase from the same time last year.
The company posted sales of $178 million for the quarter compared with $145 million for the second quarter of last year.
Operating income for the second quarter jumped 70 percent to $11.4 million compared with $6.7 million in the prior year, according to the company.
Metalico says the year-over-year comparison with the second quarter of 2010 reflects improved financial performance on near-record ferrous shipments and moderate increases in volume, except for platinum group metals (PGM) shipments, which declined.
According to the company:
- Sales increased 23 percent.
- Operating income rose by 70 percent.
- Net income grew 50 percent to $6.6 million from $4.4 million.
- Unit volume shipments increased 40 percent for ferrous scrap and 9 percent for nonferrous scrap.
- PGM unit volumes decreased 26 percent to 28,900 troy ounces from 39,000 troy ounces.
- Minor metal shipments rose 3 percent to 432,000 pounds from 421,000 pounds.
- Lead product shipments increased 3 percent to 13.3 million pounds.
Metalico reports volume increases in all segments other than its PGM and minor metals segments. Changes in sequential unit shipments were mixed, with gains in nonferrous and lead and decreases in ferrous, PGMs and minor metals. Acquisitions added 7,900 gross tons of ferrous scrap and 1.65 million pounds of nonferrous scrap in the quarter, according to the company.
Average selling prices for all metal categories rose year-over-year. Sequentially, all categories were marginally down to flat, except for a price increase of 23 percent for minor metals, Metalico reports.
Carlos Agüero, Metalico president and CEO, says, "Our overall positive operating results again this quarter in the face of rising scrap procurement costs is a testament to our broadly diversified commodity metal mix strategy. Ferrous, nonferrous and minor metals product lines turned in stellar results, while the PGMs suffered from lower volumes and competitive cost pressures. Fabricated lead products extended their return to profitability."
Agüero continues, "General economic conditions for our industry, although still good, are not as favorable as we experienced earlier in the year. Going into the second half of 2011, we think the standout will be ferrous and nonferrous metal consumer demand, supported by relatively stable pricing. Sourcing sufficient metal units at acceptable costs, while achievable, could be challenging."
Metalico says its largest segment, ferrous and nonferrous recycling, continues to grow and be very profitable for the company, contributing 74 percent of operating income on only 60 percent of consolidated revenue so far this year.
More information on Metalico is available at www.metalico.com.
> PAPER
Manistique Papers Closes
Manistique Paper Industries (MPI) has closed its paper mill operations, filed for bankruptcy protection and is seeking a buyer. The mill, based in Manistique, Mich., had been in operation for 90 years.
The paper company, which is a large consumer of recovered fiber, blames declining demand and increasing material costs as key reasons for the decision. According to a news release issued by the company, Manistique's lender informed the company that capital needed to keep the mill running would not be provided, despite MPI having never missed a loan payment and its majority stock holders offering guaranty payments and support collateral value.
"In light of the lender's decision, we examined our few options with legal counsel and we regret having to make the decision to file bankruptcy," says Jon Johnson, MPI director and general manager. "The business circumstances leading to this decision were unforeseen—we are as shocked by this as everyone else. We had thought and hoped that the lender would allow us to continue operations while we searched for alternative financing."
The company says the volatile market also has played a role in its decision to close its doors.
"While our values and service have not changed since 1920, the American economy has changed," Johnson says. "Due to the current economic situation and the inability to obtain our working capital needs, we are left with no choice at this time but to close this chapter of Manistique and Michigan history."
The cost of raw material has increased $1 million per month since January 2011, according to MPI, which severely affected the company's bottom line. Market conditions also resulted in a significant decrease in demand, creating excess inventory and falling revenues, MPI says.
> MUNICIPAL
Balcones Resources Breaks Ground on New MRF
Balcones Resources Inc., based in Austin, Texas, has broken ground on a new material recovery facility (MRF) in that city. The new $20 million facility, scheduled to open by the third quarter of 2012, will be sited on 10 acres. When fully operational, Balcones says the MRF will be able to process 25 tons of recyclables per hour.
Balcones was recently awarded a 20-year contract by the city of Austin that calls for the company to process 60 percent of the single-stream curbside recyclables the city collects from its 177,170 residential accounts. Balcones says the MRF has been designed so it can expand as the company's partnership with Austin grows.
Bulk Handling Systems (BHS), Eugene, Ore., will manufacture the equipment to be installed at the MRF. The plant will feature screening and optical sorting technology that will allow Balcones to recover cardboard, newsprint, mixed paper, PET (polyethylene terephthalate), HDPE (high-density polyethylene), mixed plastics, mixed office paper, glass and metals at a recovery rate in excess of 95 percent with minimal labor, BHS says. The recyclables to be processed will come from residences and businesses in the area. The MRF also will have direct access to a rail line, which Balcones will use to ship much of the material processed at the plant.
Kerry Getter, Balcones CEO, says BHS was selected as the supplier because of its high-quality construction, customer service and support and industry expertise.
At the groundbreaking ceremony, Getter said, "This will be the largest capital investment by a privately held recycling company in the state of Texas and one of the most significant in the United States in the coming year."
> MUNICIPAL
Waste Management Opens New Facility in Houston
Houston-based Waste Management (WM) has launched its single-stream Houston material recovery facility (MRF).
The 40,000-square-foot facility includes two new pieces of technology: a "paper magnet" for removing small paper and recyclable residue from the container stream and a "paper spike," which mechanically removes boxboard and chipboard from ONP (old newspapers). The processing system includes magnets and eddy currents to capture the remaining metals.
Waste Management invested more than $15 million in the new MRF, which is designed to process more than 9,000 tons of recyclable newspaper, cardboard, aluminum, glass and plastics per month. Additionally, the plant accepts materials that have historically been discarded, such as film plastic and rigid plastics.
Waste Management CEO David Steiner says, "We are proud to make the investment in this facility to help move Houston and the surrounding region to the forefront of recycling."
> MUNICIPAL
Indiana Agency Offers Recycling Grants
The state of Indiana has made $500,000 in grant funds available through its Recycling Market Development Program (RMDP) to assist recycling businesses and economic development in Indiana.
Companies have until Sept. 26, 2011, to apply for the grants, which can be used to help recycling businesses purchase equipment for manufacturing recycled materials into new products.
The grants range from $50,000 to $200,000, with a required 50 percent match from the recipient. Businesses that have current RMDP projects are not be eligible to apply for this round of funding.
The RMDP will make final funding determinations of eligible projects by the end of the 2011.
Additional information about the Recycling Market Development Program is available by calling 800-451-6027 or by visiting the program's website at www.recycle.IN.gov/5745.htm.
> EVENTS
World Recycling Forum Schedule Unveiled
The World Recycling Forum, scheduled for Nov. 15-17, 2011, at the Hotel Harbour Grand Kowloon in Hong Kong, will feature programming on several topics, including multiple sessions on end-of-life vehicle (ELV) recycling, electronic scrap recycling and battery recycling.
Among the keynote speakers are entrepreneur Stephen Greer (author of Starting from Scrap: A Hong Kong Entrepreneur's Story), Hewlett-Packard Head of Environmental Management Annukka Dickens and Tsinghua University Professor Duan Weng. Weng will speak about the impact of China's population growth on the recycling industry.
Several facility tours also are being offered in coordination with the forum, including trips to:
- The Dunwell Group oil recycling plant in Hong Kong;
- The E. Tech Management electronics recycling plant located in Hong Kong;
- Ecospace Ltd.'s Hong Kong chemical waste treatment plant;
- A Wistron electronics recycling plant in Zhongshan, China;
- The GISE-MBA Polymers plastics recycling plant in Guangzhou, China;
- The Tele Battery Recycle battery recycling plant in Shenzhen, China; and
- A BYD Co. Ltd. battery manufacturing plant in Shenzhen.
The forum, hosted by ICM AG, also will include an exhibit area featuring several companies, including equipment makers TiTech Gmbh, Hammel Recyclingtechnik, Vecoplan AG, Wendt Corp. and The Shredder Co. LLC.
Additional information about the 2011 World Recycling Forum can be found on the Web at www.icm.ch/6th-world-recycling-forum-wrf-2011.
> MUNICIPAL
Seattle Reports Increase in Recycling Rate
According to the city of Seattle's annual recycling report, the amount of solid waste that city diverted from the landfill and into recycling and composting increased by 2.6 percent in 2010, the largest year-to-year increase since 2006.
Seattle's goal is to divert 60 percent of its municipal solid waste to recycling and composting by 2012 and 70 percent by 2025. Seattle Public Utilities (SPU) estimates residents and businesses in Seattle will need to recycle and compost about 45,000 more tons per year to reach the 2012 goal.
SPU cites changes to the city's curbside recycling and composting services in 2009 as the primary factor for most of last year's recycling rate gains. In April 2009, Seattle allowed more items to be recycled and composted, provided weekly collection of organics as well as allowed commingling of all recyclables into one cart.
Three of Seattle's four municipal solid waste sectors achieved record recycling rates:
- The commercial sector's recycling rate increased the most, growing from 54.9 percent in 2009 to 58.9 percent in 2010. Strong markets for recycled paper account for most of the increase, followed by increased food waste diversion, according to the report.
- The single-family sector increased by 1.6 percent to 70.3 percent. Increased food waste collection accounts for most of this gain, the report indicates.
- The multi-family sector rate rose by 2.6 percent to 29.6 percent. This sector's recycling rate decreased in 2009. Increased food waste collection drove most of this gain, the report says.
Overall, Seattle disposed 335,570 tons of waste into an Arlington, Ore., landfill in 2010—16,000 fewer tons than in 2009 and more than 140,000 tons fewer than what the city landfilled in 2000.
> MUNICIPAL
Recyclebank Enters New York State
New York City-based Recyclebank has launched its rewards-for-recycling program in Brookhaven, N.Y., making the municipality the first community in New York state to deploy the program. The program rewards people for recycling with discounts and deals from local and national businesses.
"At Recyclebank, we believe in the power of individual actions," said Beth Kean-Waddell, Recyclebank Northeast vice president, at a ceremony held in Blue Point, N.Y., Aug 1.
She continued, "We've seen how monumental the collective impact can be when members of local communities, government and businesses work together. Together, we can enable people to take small steps that make a huge impact on their communities, local economies and the planet."
Brookhaven Town Supervisor Mark Lesko said, "While earning everyday savings from Recyclebank, residents will have the opportunity to protect the environment, invigorate the local economy and keep their community clean."
> SCRAP INDUSTRY NEWS
Novelis to Expand New York Facility
Novelis, headquartered in Atlanta, says it plans to invest $200 million to expand its Oswego, N.Y., rolling operations in response to escalating domestic demand for aluminum sheet.
The expansion will increase capacity by more than 200,000 tons per year, five times the company's North America capacity for producing aluminum sheet for the automotive industry.
The investment will include the construction of two new high-performance aluminum processing lines for automotive applications.
The company says it expects the expansion to be complete by the summer of 2013.
> PLASTICS
Coll Materials Relocates Pennsylvania Facility, Loses Equipment to Fire
A fire broke out Aug. 2 at Coll Materials' Nazareth, Pa., plant as the post-consumer and post-industrial plastics recycling company was relocating equipment from there to a South Whitehall, Pa., facility it is leasing.
The building and any remaining equipment at the site was lost, according to Renee Coll of Coll Materials. The company was able to move one processing line prior to the fire as well as fiber separation equipment for processing garden hoses, she says. The cause of the fire has yet to be determined, Renee says, but is believed to be accidental.
She adds that the company has ordered eight new Cumberland grinders for the South Whitehall facility and expects the new plant to be fully operational soon as of mid-August.
As the company recovers from the fire, it has moved production to its other facilities so its customers will receive uninterrupted service, Renee says.
In late July, Pennsylvania Gov. Tom Corbett announced that state economic development efforts would enable Coll Materials to relocate its Nazareth plastics recycling facility to the South Whitehall plant, near Allentown.
The new facility is expected to result in the addition of 75 new jobs to the area.
Coll Materials received a $333,750 funding offer for the South Whitehall project from the Pennsylvania Department of Community and Economic Development, including a $150,000 opportunity grant, $33,750 in job-training assistance and $150,000 in job-creation tax credits.
"Our investments have led to a national recycling leader setting up shop in the Lehigh Valley resulting in new investment and significant job creation," Corbett says.
> PLASTICS
North American Plastics Associations Form Alliance
Three of the major trade associations for the plastics industry in the United States and Canada have announced plans to formalize existing collaborations on programs and initiatives designed to benefit the North American plastics industry.
The Plastics Division of the American Chemistry Council (ACC), the Canadian Plastics Industry Association (CPIA) and SPI: The Plastics Industry Trade Association will work on industry priorities through a virtual structure called the North American Plastics Alliance (NAPA).
The three associations say the alliance is designed to be more effective and efficient by acting in a coordinated manner on select initiatives. The initial priorities for the NAPA are:
- Pellet containment—an extension of Operation Clean Sweep to broaden pellet containment efforts in the United States, Canada and elsewhere;
- Energy recovery—the promotion and facilitation of energy recovery and conversion of used plastics to complement recycling;
- Plastics favorability—increasing the favorability of plastics with key stakeholders; and
- Advocacy—targeting policy makers to support the growth of the plastics industry.
A steering team with member and staff representatives from ACC, CPIA and SPI will direct NAPA's programs and initiatives. The steering team members are:
- Bill Carteaux, SPI president and CEO;
- Steve Russell, ACC vice president of plastics;
- Greg Wilkinson, CPIA interim president and CEO;
- Paul Cohen, president of W. Ralston (Canada) Inc. and chair of CPIA board of directors;
- Jay Cude, president and CEO of Coeur Inc. and vice chair of SPI board of directors; and
- Glenn Wright, North America plastics commercial vice president of The Dow Chemical Co. and chair, ACC Plastics Division Operating Committee.
Wilkinson says, "This new collaboration is a logical extension of the work we do on behalf of our members and will make CPIA's voice on behalf of the Canadian plastics industry even stronger. Many of our issues cross the Canada-U.S. border, and working together with other national organizations will help us focus our resources where they can make a difference for the industry."
Russell says, "We are already working closely with SPI and CPIA on a number of fronts; this North American Alliance is a way to deliver greater value to our stakeholders."
> SCRAP INDUSTRY NEWS
U.S. Army Recycles 6.5 Million Pounds of Steel
The U.S. Army Chemical Materials Agency (CMA) recently completed a project that resulted in more than 6.5 million pounds of steel being recycled.
CMA began operating the Pine Bluff Ton Container Decontamination Facility at Pine Bluff Arsenal, Ark., in September 2003 to decontaminate 4,307 ton containers (TC) stored at the arsenal. Although empty, the 1,600-pound steel containers once held hazardous materials and required decontamination prior to recycling.
Initial efforts to decontaminate the TCs involved rinsing them. However, the residual chemical agent proved difficult to remove, so a new approach had to be found. When faced with producing an additional 660,000 gallons of hazardous liquid waste to rinse the containers, CMA personnel designed a magnetic induction heating process to simultaneously decontaminate up to 10 containers. According to the CMA, it thoroughly decontaminated the TCs so they could be processed through a commercial recycling plant.
The process used an electrically energized copper coil, wrapped around the container, to generate a magnetic field that was absorbed by iron in the container. This raised the temperature of the TC to more than 1,000 degrees Fahrenheit, where it was held for one hour. Heating to 1,000 degrees destroys all chemical agents, the CMA says.
"The decision to decontaminate these legacy containers using magnetic induction heating made the recycling of the containers possible," says Laurence Gottschalk, CMA project manager for non-stockpile chemical material.
> SCRAP INDUSTRY NEWS
Premier Attains ISO Certification
Premier Metal Services LLC, Cleveland, a processor and international broker of nonferrous and ferrous scrap metal, has achieved certification to the ISO 9001:2008 quality management standard.
"Premier Metal Services was founded on the principal of creating a culture of customer satisfaction," says company founder Michael Eisner, a 25-year veteran of the scrap metal industry. "Customer satisfaction is obtained by exceeding customer expectations by providing quality service, detailed communication, competitive pricing, prompt payments, and, most importantly, doing what we say we will do. This concept, along with obtaining our ISO 9001:2008 certification, will continue to solidify our position as a leader in the industry."
Premier Metal Services, founded in 2009, is a member of the Institute of Scrap Recycling Industries Inc. (ISRI) and the American Copper Council. More information about the company can be found at www.premiermetalservices.com.
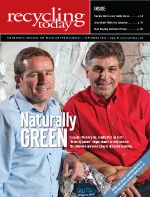
Explore the September 2011 Issue
Check out more from this issue and find your next story to read.
Latest from Recycling Today
- Electrolux commits to recycled content
- Duesenfeld system targets battery cell scrap
- Hyundai says it will make steel in the US
- APR announces Recycling Leadership Award winners
- Glass Half Full opens glass recycling facility in Louisiana
- AmpUp partners with Roundtrip EV
- Global Recycling Day event supports Pittsburgh school's recycling efforts
- President signs executive order on critical minerals