The closing and consolidation of steel plants throughout the United States was a source of economic turmoil in terms of job losses and negative economic impact, particularly at the local level in traditional mill towns.
As some of these plants have been decommissioned and razed, though, the property on which they once operated is finding new life as land prime for new development.
Examples of this include the 2,400-acre Keystone Industrial Port Complex, located 20 miles north of Philadelphia at what was once U.S. Steel's Fairless Works.
Approximately 45 miles north of the Keystone Industrial Port Complex, the Bethlehem Commerce Center, which is situated on 1,600 acres of former Bethlehem Steel property near Allentown, Pa., could eventually see $1.5 billion in investment and the creation of up to 6,000 new jobs.
And the waterfront area of Buffalo, N.Y., once home to another massive Bethlehem Steel complex, is being converted into land that will host industrial, commercial and retail facilities as well as alternative energy generation plants.
Considerable Effort
Taking such sites from housing idled plants that are empty shells of their former selves to prime, marketable real estate is one of the areas in which Beaver Valley Slag (BVS) excels.
One of the company's most recent efforts involved a decommissioned tin mill in the western Pennsylvania town of Aliquippa, near Pittsburgh, which also is home to BVS. The abandoned plant was so solidly constructed that it presented a host of challenges.
BVS says it met those challenges head-on, however, by augmenting its existing fleet with new demolition and recycling tools, including some from Genesis Attachments, Superior, Wis. The move enabled BVS to keep pace despite facing some of the heartiest materials the company's employees say they have ever seen.
In addition to being 76 acres in size, the Aliquippa site featured buildings designed for stoutness. According to Ron Cross, BVS director of sales and service, the project started with asbestos abatement, followed by an initial demolition of all the above-ground structures. It was during that phase, he says, that the project's scope really became apparent.
"Because of the tin mill's design, a good portion of the facility was below grade—some as much as three stories," he says. "That, in itself, made for a challenging project. However, it was really the size of the concrete and rebar we were encountering that changed everything. Much of the concrete was better than 36 inches thick in many spots, and all of it was double-matted rebar."
Cross adds that the rebar ranged in diameter from 0.5 inch to 3 inches thick. "It was like trying to demo a reinforced bunker," he says.
Expanding the Arsenal
BVS initially planned to rely solely on excavators fitted with hammers and buckets to tackle the plant demolition, a decision the company based on its past experience and prior practice.
When personnel on site developed a better understanding of what they were facing—more than 1 million cubic yards of heavily reinforced concrete—they began to look into alternative processing methods.
A call to equipment supplier Gibson Machinery LLC (www.gibson machinery.com), with locations in Cleveland and Pittsburgh, led to the eventual purchase of a Genesis Model LXP 400 Logix Processor and a Genesis Rebar Shear (GRS).
"We did a lot of research and looked at attachments from most of the major manufacturers," Cross says. "Based on Genesis' reputation and value and Gibson Machinery's willingness to help secure us a quick delivery, we felt they were the way to go. Once our operators put it to work, it was all over—it's that productive."
The LXP multi-jaw attachment retains a separate pivot group for each jaw set to provide what Genesis describes as a truly simple and fast jaw changeover. The pulverizer jaw used at the tin mill project has been designed with a tooth profile intended to maximize crushing force and a bolt-on tooth bed (essentially a fully replaceable crushing surface) designed to eliminate the need for welding.
"We only took delivery of the LXP in July 2010 [and] it's been outstanding for us at Aliquippa," says Cross. "Our guys say it's been virtually unstoppable."
The demolition process at the Aliquippa tin mill developed into a repeatable process that BVS describes this way: The LXP 400 (mounted on a new Hyundai 450 LC-7A) would reach into the area to be processed, grab a jaw full of concrete and make its bite, pulverizing the concrete and freeing up the mats of rebar contained within. The uptick in production was immediate after the tool was added, Cross says.
"Because they'd never run anything like an LXP, there was a slight learning curve for our operators," he says. "Once they had their comfort level, however, they found there was almost nothing they couldn't do with it. They would crush the concrete, expose the bar—cutting it, if necessary, using the LXP's shear blade—set the rebar off to one side and continue along. It was amazing to see how much more productive we'd become," Cross adds.
After a particular section of the structure was completed, a BVS crew would come in with either a bucket or magnet to pull the ferrous material from that location and set it off to one side for separation by type and grade.
"A lot of ferrous is left behind after concrete has been crushed," says Cross. "That can include anything from rebar to plate steel to rail to wire and more. Obviously we wanted to recover as much as possible. The rebar, which was the bulk of what we were getting out of here, was then piled for subsequent downsizing using the Genesis Rebar Shear."
The Rebar Shear, says Cross, was another late addition to the project's game plan. "Once we saw the volumes of bar with which we were dealing, we felt we needed a tool that could prepare it to lengths, both to improve efficiency during transportation to the mill and to increase its overall value. The Genesis Rebar Shear did that for us. It simply spent the whole day biting into a pile of rebar, getting it down to size."
In addition to its new specialty tools, BVS also had a number of hammers on site, pounding away at concrete that was too large for pulverizing, and a pair of Caterpillar 385 and 374 excavators, pulling up huge concrete slabs that ran beneath the site.
While all the ferrous metal was being recycled, virtually all of the million-plus yards of concrete were reduced in size using the LXP and placed back into the ground to help ensure below-grade voids were eliminated following completion of the demolition.
"There's no doubt that the LXP has been the go-to tool at this site, and I definitely see it playing an important role in our demolition efforts from here on in," Cross says. "In the past, we've lacked the ability to reach down into a pit or reach over a wall to crack or crush concrete. We have that now and are a better demolition firm because of it."
Cross adds that BVS plans to have the tin mill project wrapped up by the end of 2011—a timeline that at one point seemed unrealistic.
"When we are done, we will leave behind a clean, level property that is ready for new development," he says. "And this site can be particularly attractive to an investor or company, since it already has barge and highway access and a rail spur. BVS' efforts help get rid of an existing eyesore, eliminate the risk of injury from anyone wandering on site and take a major step in helping bring jobs and a tax base back to the area. Who can argue with that?"
This article, which first appeared in the May/June issue of Recycling Today's sister publication Construction & Demolition Recycling, was submitted on behalf of Genesis Attachments (www.genesisattachments.com), Superior, Wis.
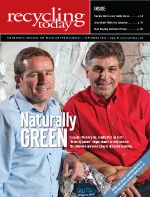
Explore the September 2011 Issue
Check out more from this issue and find your next story to read.
Latest from Recycling Today
- Lautenbach Recycling names business development manager
- Sebright Products partners with German waste management equipment company
- WasteExpo transitions to biennial format for enhanced experiences
- Study highlights progress, challenges in meeting PCR goals for packaging
- Washington legislature passes EPR bill
- PureCycle makes progress on use of PureFive resin in film trials
- New copper alloy achieves unprecedented high-temperature performance
- Gränges boosts profits and sales volume in Q1 2025