![]() |
After the nonprofit electronics recycler RecycleForce, based in Indianapolis, purchased its new shredding and sorting system in 2010, the company was able to advance to the next level of service, increasing its throughput from 2 million pounds per year before the shredder to nearly 10 million pounds today.
This year the company made another advancement with the addition of a finer screen size that allows for pulverization of specific material streams after they’ve gone through the initial shredding and separation process.
Gregg Keesling co-founded the company along with his colleague Thomas Gray, who serves as vice president.
![]() Gregg Keesling (center, wearing a tie) and employees in front of “The Beast,” RecycleForce’s shredder. |
Nontraditional Workforce
RecycleForce, which is R2 (Responsible Recycling Practices) and ISO 9001 (quality management system) certified, runs a bit differently than most electronics recyclers. Keesling has had a tradition of employing ex-felons in his prior business, an alternate staffing agency. Keesling founded RecycleForce in 2005 when his staffing agency’s product assembly contract was outsourced to China.
“I’m in electronics recycling not because of electronics recycling but because I’m looking for a way to employ ex-offenders,” Keesling says.
As a nonprofit social enterprise, RecycleForce has grown with the help of grants and foundational support. In 2011 the facility was one of seven sites across the country to receive $5.5 million in federal grant money to assist individuals with barriers to employment as part of the U.S. Department of Labor’s Enhanced Transitional Jobs Demonstration. The grant has funded the hiring of 50 of the company’s 120 employees on a temporary basis.
Hiring ex-offenders could be rife with security issues, but Keesling says measures in place prevent almost all breaches. In addition to magnetic degaussing of storage media, numerous security cameras are installed throughout the facility, and the company maintains a full-time police force detail.
Socially Focused Financing Half of the cost of Indianapolis-based RecycleForce’s $800,000 E-Vantage Separator System (the trademarked design of RRT Design and Construction, Melville, N.Y.) was financed by a loan from RSF Social Finance, a San-Francisco-based nonprofit finance organization that lends money to a variety of social enterprises. RSF focuses on making high-impact loans in three major focus areas, says Ted Levinson, director of lending: food and agriculture, education and the arts and the environment. Levinson says RSF Social Finance derives most of its funds from earned income on collateralized loans for the purchase of equipment, real estate or lines of credit. A few market sectors of interest to the organization right now: packaging technology innovations and waste to energy or renewable fuel. Most of RSF’s loans range between $200,000 and $5 million. “We’re very picky about who we work with,” says Levinson. “We want to work with those borrowers that are having a deep impact on the environment or on society.” When he first learned about RecycleForce, the enterprise was having great results addressing recidivism among the ex-felons it employs, “but the volume of waste they were actually diverting was very modest,” Levinson says. RecycleForce wanted to borrow $800,000 to finance the shredder. “I thought it was unreasonable,” Levinson recalls, noting the amount was about the same as the recycler’s operating budget. Levinson offered half that, under the condition that RecycleForce co-founder and president Gregg Keesling had to find another investor for the rest. To Levinson’s surprise, Keesling quickly managed to secure the needed funding from Japanese financier Tetsuyuki Koizumi, now president of Philo-Urban Metal Technology Corporation of Redwood City, Calif. Koizumi had been looking to finance an electronics recycling project in 2010 and coincidentally saw a news story about Keesling and his son Chancellor, a U.S. soldier who had died in 2009 while deployed in Iraq. “RecycleForce is an ideal borrower because they are improving the environment and improving re-entry results for former felons,” observes Levinson. |
![]() Items destined for the shredder at RecycleForce are grouped in like categories before processing. |
Equipment Advances
In 2010 RecycleForce was able to secure a loan and private financing that funded the purchase of the E-Vantage Separator System, a trademarked design of RRT Design and Construction, Melville, N.Y. The system includes a shredder manufactured by SSI Shredding Systems Inc. of Wilsonville, Ore., and a CRT crusher from Andela Products, Richfield Springs, N.Y.
Nicknamed “The Beast” by employees, the shredder can handle just about everything the company receives, with the exception of focus and high-end gold-containing materials, such as circuit boards, ink toner cartridges and mercury-containing items such as batteries and old thermostats.
“We are processing pretty much everything with a cord on it,” says Keesling.
In selecting the shredder, Keesling says a key consideration was safeguarding against lead dust particles inevitably created by shredding. “There is no safe level of lead,” says Keesling. “We made a really strong decision to pick a shredder that could have a dust collection system.”
The shredder’s dust collection and HEPA (high-efficiency particulate air) filtration components accounted for a large portion of the $800,000.
Incoming electronics first go to the company’s sorting area to determine disposition. With the exception of focus materials, says Keesling, “every single item that comes in here ends up in five different components: steel, copper, plastic, aluminum and then the boards containing precious metals.” Things that easily can be disassembled by hand aren’t shredded.
Beyond that, “anything that’s not a focus material is going through that shredder,” explains Keesling.
Having the shredder has opened up more processing avenues for RecycleForce. The company hosts more collection events and has partnered with colleges in Indiana.
Keesling says recyclers considering purchasing a shredder need to first determine the level of processing they want to offer. “Do you want to process everything you get, or do you want to use middlemen or other processors?”
Though RecycleForce does sell some end products to consolidators, the company doesn’t use middle men. “We like to say that we’re end of life for everything.”
Customer Connections
RecycleForce’s shredding system is followed by a series of magnets and picking stations in lieu of an eddy current, and sometimes material streams are processed through the shredder twice to recover ferrous and then nonferrous metals.
The company has two sizes of screens for its shredder: a 2.5-inch screen and the newer 1-inch screen, installed in June of 2013. It takes about 15 minutes to change between screens. The smaller screen allows a finer pulverization of product.
“It’s really going to change us dramatically in what we can do with our products,” says Keesling of the new screen. He says once buyers know the composition of the shredded material, they are more likely to opt for the second screening to help streamline their processing and reduce shipping costs.
“It’s going to allow us to sell more directly to smelters,” Keesling says. “The buyers that we have a good relationship with and that have been here to see it want the material pulverized more.”
Recently RecycleForce was hired to shred 168,000 recalled remote-controlled race car toys. After the first shred, the cars’ metallic motors and antennas were picked up by magnets, leaving the plastic behind. The motors were sent through the shredder again using the smaller screen, further liberating the copper content. “Now we’ve turned a steel scrap item into a copper scrap item,” Keesling explains.
The author is a managing editor with the Recycling Today Media Group and can be reached at lmckenna@gie.net.
Get curated news on YOUR industry.
Enter your email to receive our newsletters.
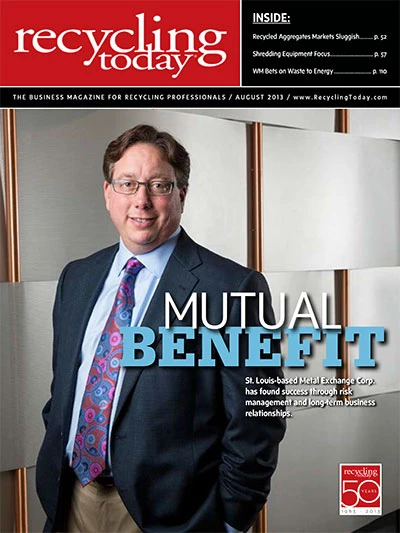
Explore the August 2013 Issue
Check out more from this issue and find your next story to read.
Latest from Recycling Today
- ReMA opposes European efforts seeking export restrictions for recyclables
- Saica announces plans for second US site
- Update: Novelis produces first aluminum coil made fully from recycled end-of-life automotive scrap
- Aimplas doubles online course offerings
- Radius to be acquired by Toyota subsidiary
- Algoma EAF to start in April
- Erema sees strong demand for high-volume PET systems
- Eastman Tritan product used in cosmetics packaging