![]() |
Waste Management (WM), Houston, has long been involved in the waste-to energy (WTE) industry. Its wholly owned subsidiary Wheelabrator Technologies operates 17 waste-to-energy facilities across the country, and WM has 131 landfill-gas-to-energy projects installed. From these two technologies, WM produces more than 9.8 million megawatt hours of electricity, which is enough to power nearly 1.2 million homes.
While that may seem pretty remarkable by most standards, North America’s largest solid waste company isn’t stopping there. WM has been at the forefront of the next generation of emerging waste conversion technologies by researching and developing them internally or by investing in these technologies externally.
Bill Caesar has been the man leading the charge for WM. As president of WM subsidiaries WM Recycle America LLC and WM Organic Growth Inc., Caesar has the feedstock and the capital to help WM reach its goal of powering 2 million homes by 2020 and treating the material it collects from its 21 million customers as a resource.
“When we think about our strategy going forward, it is really centered around three pillars,” says Caesar. “One is that we are trying to know our customers better than anyone else so we can serve them better; two is trying to extract as much value out of the materials we manage as possible; and three is to try to do these things as efficiently and effectively as possible.”
WM’s approach to waste conversion is very much a combination of these goals. “I think there are a lot of reasons why Waste Management would be pursuing various technologies that would allow us to either generate power or produce transportation fuel or anything else that would allow us to extract value,” Caesar says. “We also have a significant number of customers that are committed to reducing their waste profile, and one way we can help them achieve that goal is to provide an alternative to landfill for materials they produce as a byproduct of their manufacturing process or the products they sell to consumers.”
One Size Does Not Fit All
The mass-burn WTE technology employed by WM via its Wheelabrator business has been well-proven and is still a strategic part of WM’s growth strategy. (See the sidebar “Still Going Strong” at www.RecyclingToday.com/rt0813-waste-to-energy-focus.aspx.) But the answer to generating more energy and extracting more value from waste is not always as easy as building more WTE facilities, according to Caesar. He says these facilities are not appropriate in every circumstance because of economic drivers, zoning or other factors.
“The waste industry in general is a local business. The collection is local. The disposal of material is local,” explains Caesar. “Take a place like Texas that has relatively low disposal costs and relatively low power costs. The economics of a traditional waste-to-energy facility probably wouldn’t pencil out.”
Caesar says in that scenario an alternative to a mass-burn WTE facility would have to be developed. While he says electricity is a good product, the natural gas boom in North America has made it less valuable than it was a few years ago. New waste conversion technologies that can create products other than electricity are attractive in this setting.
“What we are trying to do is either be able to generate value less capital intensively or create higher value goods,” says Caesar. “If I can either find ways to produce an electron for a lot less money or through some process, or if I can produce a transportation fuel or a chemical that had significantly higher value, then I am in a better place than I otherwise would have been if I had only had traditional waste-to-energy as my alternative.”
Placing Many Bets
Caesar describes the way in which WM is proceeding with conversion technologies as a “portfolio approach.” He says, “We are trying to place a number of bets in different technologies with the hope and expectation that one or more of them will pay off in a big way, a couple of them will be viable on the commercial scale, and we’ll probably have to suffer through a couple of them not working out.”
At this stage in the development of what Caesar refers to as “second generation” waste conversion technologies, WM is not able to predict which technologies are going to work and which ones aren’t. Caesar says that even with companies that are using the same technologies, not all of them will be successful. “That is why you have a portfolio,” he says. “It is in our interest to place some bets, and we do that by taking minority equity positions in some of these companies and, at the same time, are developing some technologies internally.”
This approach appears to be beneficial for all parties involved because WM can lend its industry knowledge to these early-stage companies while learning from them how technologies will perform using the materials that it manages as feedstock.
One such firm WM has invested in is the Montreal-based gasification company Enerkem. Its gasification technology converts wastes into fuel and chemicals. Enerkem has a facility under construction in Edmonton, Alberta, and one in development in Pontotoc, Miss., each of which is designed to have a capacity of 10 million gallons of ethanol per year. (See the sidebar “Making the Investment” at www.RecyclingToday.com/rt0813-waste-to-energy-focus.aspx to learn about more companies WM has invested in.)
Caesar says no single technology WM has invested in or developed yet is operating at commercial scale. “There are several that are close,” he says. He estimates that within 12 to 18 months, more will be known about which companies have become successful at that level.
Caesar says some companies have failed at their attempts to commercialize their technologies, but he is more interested in the companies that are still out there.
Lessons Learned
One of the biggest lessons Caesar says he has learned through WM’s process of exploring different technologies is that it is possible to have a technology that performs as advertized but run into challenges in the quantity or the composition of the material needed for the process being available in a form that would allow the technology to be successful on a commercial scale.
He explains many waste conversion technology companies focus on what happens once they have their clean material and have to transform it into something of higher value rather than on material procurement. “There are a lot of challenges around getting them clean material in quantities they can process on a regular, every day, 365-days-a-year sort of schedule.”
Caesar emphasizes that overcoming that challenge is not necessarily the technology’s fault, rather, “It is whether the industry is ready to go there and whether our customers are willing to do the things that they would need to do.”
Of course, he says a whole other set of companies has technology that isn’t proven; but, for the companies that do have viable technologies, another set of challenges need to be worked through for those entities and technologies to be successful at commercial scale.
“MSW (municipal solid waste) by anyone’s account is not a homogeneous set of material. At a very large scale, it is generally the same, but on a specific scale, you probably have to do something to it to prepare it for downstream processing, and that requires incremental costs and incremental steps in the process.”
Recycling Connection
With its acquisition in February of the recycling company Greenstar, WM is processing an estimated 15 million tons of recyclables per year. Caesar says the acquisition, which included 12 material recovery facilities (MRFs), is going well.
Including assets from Greenstar, WM currently operates 129 MRFs, 49 of which process single-stream material. Caesar says processing MSW for use as a feedstock in a WTE process will operate similarly to a MRF or will come from a MRF.
“There is a lot of stuff that can get picked up and can be run through a recycling process, but at the end of the day, when you look at your residual at the MRF, it has got a lot of plastic in it. It has got a lot of paper in it, but your mill or plastics buyer would say, ‘That is not acceptable. That is a contaminant,’” says Caesar.
He adds, however, that this residue has a Btu value or carbon content.
Caesar says all of the waste conversion processes WM is contemplating will involve separation.
“I can honestly say that the front end of any process that is going to use MSW as a feedstock is going to look and feel a lot like a MRF, because you have to get the metals out,” he says. “It is in your interest to pull the high-value plastics out. It is in your interest to pull the fiber out.”
Looking Ahead
With dozens of waste conversion projects moving through various stages of development, it will only be a matter of time before this second wave of waste conversion technologies has the opportunity to be proven.
“As volumes of materials going into landfills decline and as many, if not all, energy costs go up, there is a calculus going on that makes some of these technologies very attractive,” Caesar says.
He says he expects to see commercial successes within the next year or two and thinks technologies that employ gasification will stand out. Gasification converts plastics and fiber into synthesis gas, which can be made into many products.
The success of waste gasification technology will rely on the efficiency of the gasifier and the ability to clean the gas, according to Caesar.
“People should stay tuned,” he says. “It’s going to come in fits and starts. There isn’t going to be a single solution. There are going to be a number of solutions, and that is another reason we are taking this portfolio approach.”
The author is a managing editor with the Recycling Today Media Group and can be reached at ksmith@gie.net. This article first appeared in Renewable Energy from Waste, a sister publication of Recycling Today.
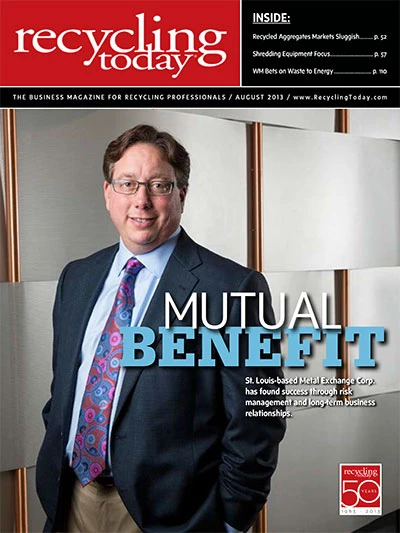
Explore the August 2013 Issue
Check out more from this issue and find your next story to read.
Latest from Recycling Today
- ReMA opposes European efforts seeking export restrictions for recyclables
- Fresh Perspective: Raj Bagaria
- Saica announces plans for second US site
- Update: Novelis produces first aluminum coil made fully from recycled end-of-life automotive scrap
- Aimplas doubles online course offerings
- Radius to be acquired by Toyota subsidiary
- Algoma EAF to start in April
- Erema sees strong demand for high-volume PET systems