![]() |
Allied-Gator Offers New Blade Design
Youngstown, Ohio-based Allied-Gator is now offering what it calls an innovative new blade design made exclusively for the company’s MT mobile shear line. Allied-Gator says its new Serrated Gator Blades have undergone extensive field testing that has “proven Serrated Gator Blades outlast traditional shear blades by up to 50 percent longer when processing general scrap and up to 90 percent longer when shearing steel wire and cable.”
The new technology is available to any current Allied-Gator MT customer regardless of tool size, and no product modifications are needed to the MT, according to the company.
“The serrations of the MT’s new blades are designed to progressively pass through material like a saw blade, rather than forcing the shear to chop through a large mass of material like an ax,” says Mike Ramun, Allied-Gator sales and marketing manager. “This new blade design does not rely solely on sharp shear blade edges to achieve the cut. Instead of a snipping effect, these blades generate a tearing action. This allows the MT shear to grip and tear scrap materials, which is a far more efficient cutting method than the traditional ‘scissoring effect’ utilized by all other mobile shear blades,” he adds.
As the MT’s dual moving shear jaws close on structural steel, each serration systematically yields and tears scrap material along the blades’ cutting path, Allied-Gator says. “This new method of shearing greatly reduces the overall wear and tear to the tool. It’s like perforating a sheet of paper as you tear it,” Ramun says.
Traditional blades force steel wire and cable to the throat of the jaw and can cause severe uneven wear and damage to that specific blade area, he says, and uneven blade wear has caused many recyclers to dread cutting steel wire and cable with their mobile shears. With Serrated Gator Blades in the MT, the serrations trap steel wire and cable along the blades as the jaws close. This allows the blades to progressively rip and tear the cable apart on its way to the throat, according to Allied-Gator.
Ramun says the new technology also is effective in processing notoriously troublesome materials such as stainless steel and thin sheeting.
The Allied-Gator Serrated Gator Blades are available for all 11 sizes of the MT Series Multi-Tool line.
International Baler Expands its Dealer Network
International Baler Corp. (IBC) and Randy Gibson, its director of sales and marketing, have announced two additions to the company’s global dealer network.
Paper & Recycling Solutions, Keller, Texas, is the new IBC dealer for Texas and Oklahoma.
“Owner Mike Schwinn offers 20-plus years of industry knowledge, service capability and the willingness to take care of the customer, which also is the philosophy of International Baler,” says R. Jefre Hicks, western sales manager for IBC.
Gibson also has announced that Steco Miljø AS, based in Drammen, Norway, is IBC’s dealer for Norway, Sweden, Denmark and Finland.
Steco Miljø AS “offers a tremendous amount of industry experience, knowledge, and service capability as well as sharing International Baler’s philosophy of making customer service its first priority,” says Gibson.
IBC, Jacksonville, Fla., says customers in these regions can contact these dealerships for their recycling equipment needs or can find out more about the International Baler product line at www.intl-baler.com.
![]() |
Triple M Metal Commissions New Wendt Shredder
Triple M Metal LP has commissioned a new Wendt Corp. Model M6090 shredder in Sault Ste. Marie, Ontario.
Triple M, founded more than 40 years ago by Mike Giampaolo, is a ferrous and nonferrous scrap metal recycler with 16 facilities in North America.
Wendt says the recent installation of the M6090 will provide Triple M with the opportunity to sell the majority of its scrap metal locally while growing its customer base in and near Sault Ste. Marie.
Triple M says the transportation savings gained from having a shredder on site justifies its investment in the equipment. “We were looking at pricey shipping costs if we didn’t invest in a shredding facility for this yard,” says Tom Anderson, Triple M vice president of engineering. “We would have had to ship shreddable materials to one of our southern Ontario shredders and then transport the finished goods back up to our local steel mill customer in Sault Ste. Marie.”
When determining what shredder to purchase, Triple M says it found the M6090 to be the appropriate fit. “The Model M6090 was the right size for this yard,” says Anderson. “Our material flow was not sufficient enough to support anything larger, and the decision supports regional shredding as opposed to centralized shredding.”
![]() |
Vecoplan Sponsors NASCAR Racer
Vecoplan, a manufacturer of waste processing systems for the production of biofuel and bioenergy feedstock, sponsored car No. 23 at the NASCAR Nationwide Feed the Children 300 event held June 28 at Kentucky Speedway, Sparta, Ky.
The No. 23 Vecoplan Ford Mustang was fielded by Rick Ware Racing and driven by Harrison Rhodes. The race was sponsored by Feed the Children and, through this partnership with Speedway Children’s Charities, Feed the Children will deliver 500,000 pounds of food and supplies to families in racing communities across the country.
“This race was the perfect opportunity for Vecoplan,” said Len Beusse, COO of Vecoplan LLC. Beusse noted that the company is located in the South, the birthplace of NASCAR, and its subsidiary Vecoplan Midwest is about 30 minutes from the Kentucky Speedway.
Beusse also noted that the company’s mission, “Technology for a sustainable tomorrow,” ties in well with the objectives of the Feed the Children 300 event.
On July 1, Rhodes, Ware and other members of the race team took the No. 23 car to Vecoplan’s headquarters in High Point, N.C. The car was unloaded into one of Vecoplan’s manufacturing bays, where employees met Rhodes and Ware, got autographs and had their pictures taken with the car and crew.
After a question-and-answer session, Rhodes and Rick Ware Racing members toured Vecoplan’s test lab, engineering departments, manufacturing plant, parts and service departments and offices.
As an engineering major at North Carolina State University, Rhodes took special interest in Vecoplan’s engineering teams. “The shredders they design for recycling, plus the size and sophistication of the systems they engineer and build for turning waste into a fuel, [are] truly impressive,” Rhodes said. “You need sponsors to be competitive in NASCAR, and it’s great to have a sponsor like Vecoplan that manufactures products you really believe in.”
Get curated news on YOUR industry.
Enter your email to receive our newsletters.
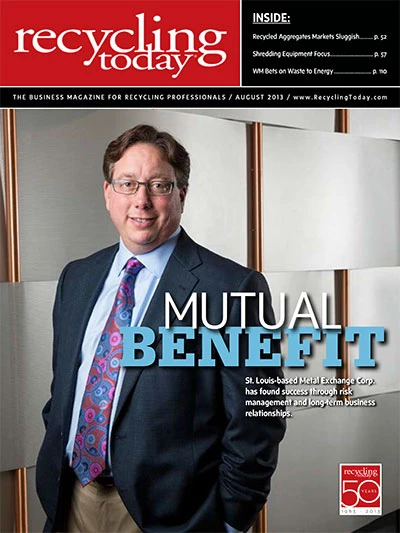
Explore the August 2013 Issue
Check out more from this issue and find your next story to read.
Latest from Recycling Today
- ReMA opposes European efforts seeking export restrictions for recyclables
- Fresh Perspective: Raj Bagaria
- Saica announces plans for second US site
- Update: Novelis produces first aluminum coil made fully from recycled end-of-life automotive scrap
- Aimplas doubles online course offerings
- Radius to be acquired by Toyota subsidiary
- Algoma EAF to start in April
- Erema sees strong demand for high-volume PET systems