![]() |
When State Rubber & Environmental Solutions started shredding tires about a de- cade ago, the company had optimistic plans for growth and volume. In the decade since then, its actual output is nearly doubled the company’s initial projections.
Vice President Jerry Woosley credits State Rubber’s growth to its “machinery tweaking” and knowledge of how to squeeze the most from its equipment.
The operation is located in Denver City, Texas. If you’re not familiar with the area, it’s almost on the New Mexico border.
“Why Denver City with no rail and no Interstate highway nearby? Quite simply, it is home,” Woosley explains.
State Rubber collects and receives tires from within a 250-mile radius of Denver City that it processes into crumb rubber. Since 2004 it has operated a state-of-the-art, four-stage tire recycling plant.
“State Rubber was born from my need, as well as the needs of other tire dealers in West Texas and eastern New Mexico, to dispose of the scrap tires generated by our tire businesses,” Woosley says.
Woosley has sold tires in the Texas Panhandle for decades—more than 35 years. “I am acquainted with a large number of other tire dealers in the region. Those relationships have become a customer base for State Rubber,” he says.
A local group of community leaders came together to support something outside of farming and fuel that could boost the economy. Some of them, like Woosley, had expertise in the rubber industry. Others, like board member Gene Day, who is owner of several building components businesses and scrap metal recycling yards in West Texas and eastern New Mexico, brought steel recycling knowledge to the table. It all came together, thanks to the help of 50 investors.
“We are currently about halfway through an expansion of the production capability of the plant. When complete, we will double our current capacity of 33 million pounds of tires (1.5 million PTE, or passenger tire equivalents) per year,” Woosley says.
While the plant can run on “automatic,” he says a “seat of the pants” approach to screen sets, infeed percentages, ratios and other operational variables offers better control of the final products.
The Process
Tires come from a wide region into the 3,750-square-foot building that houses the plant’s infeed conveyor. This leads to the primary shredder, a Saturn 72-44BGHT, and classifier from Granutech-Saturn, Grand Prairie, Texas. The muscle of the shredder is a 300-horsepower hydraulic power unit that drives paired rotary hydraulic motors.
“The 72-44BGHT was chosen because of its infeed dimensions,” Woosley says. “We are able to put larger tires into the shredder.”
The primary shredder reduces the tires to a 3-inch nominal chip. Any tire pieces that cannot pass through the Action Taper-Slot screen repeat the loop until they are small enough to pass.
The shredder takes the tires, whether from a small auto, a farm tractor or heavy equipment, as they come. “There really is not any one tire that presents a greater challenge than others,” Woosley says. “We do have to precut some of the larger tires.”
The tire chips are then conveyed into a trailer with a live floor and are metered into a 300-horsepower Model 80 Grizzly, also manufactured by Granutech-Saturn Systems. The 3-inch chips are reduced to a three-quarter-inch material. During this process, 95 percent of the steel wire is liberated, according to State Rubber.
The steel wire is recovered using an Action free wire reclaimer. Four belt magnets carry the wire over slots in the top deck of the machine. The wire is discharged from the machine and moved via a side conveyor to a container outside of the processing building.
“All of that material is sold as scrap metal,” Woosley says.
Shredding is not finished yet, however. The three-quarter-inch tire chips move from a second walking floor trailer into a Granutech-Saturn G-3 Granulator. This machine further reduces the three-quarter-inch pieces to less than one-quarter-inch. This process also liberates approximately 90 percent of the fiber contained in the chips, according to State Rubber.
The fluff is captured with the help of five fans. The combined horsepower of those fans totals more than 300. The fluff and a small amount of rubber are then filtered by a pair of Donaldson Torit filtration towers that stand slightly taller than 65 feet. Large air ducts remove about 10,000 pounds of fluff daily.
They also contain a Flamex spark detection and arresting system. The ducts are equipped with an optical sensor that detects the glow of a spark or small flame as it passes by. A water nozzle 28 feet past the sensor extinguishes the spark.
Next, those one-quarter-inch chips are fed into a refiner mill, which powders them. When the refiner mill is done, the rubber particles are able to pass through various screens, including a 200-mesh particle screen. This is about the consistency of talcum powder, Woosley says.
“While we are a small processing facility, if gauged by the number of tires we process, it is worth noting that 90 percent of the crumb rubber State Rubber reclaims from whole tires passes through a 30-mesh screen,” Woosley says.
The material passes under a seventh—and final—magnet after it leaves the mill on its way to the Rotex 522 screener. Here the material that is within required production size is separated and sent to a final V90 Forsberg fiber separating table.
The product is then bagged in sacks typically weighing 2,000 pounds or more or is blown into storage silos. Those silos are unloaded into tractor trailers for shipment.
The Partnerships
“Only one piece of our original size reduction equipment has been replaced in nine years,” says Woosley.
He says State Rubber has had a great partnership with Granutech-Saturn. “From our construction in 2003 until now, we have both enjoyed a good relationship between our companies,” he says. “Early on, we relied on their guidance and operational support to a large extent. Now, State Rubber and 4D Corp. in Duncan, Okla., do a large amount of new equipment testing for Granutech-Saturn. We feel our experience and feedback helps them create better equipment,” he says.
This helps to keep State Rubber a step ahead of the pack when looking for new ideas and operational innovation.
![]() |
The Business Model
State Rubber processes all kind of tires, including farm and some small off-road tires, producing finely ground crumb rubber for the asphalt paving market.
About 75 percent of State’s crumb rubber production is sold into asphalt markets. The other 25 percent is sold into other niche markets. However, State Rubber does not sell into landscaping, arena, field turf or similar markets.
“All of the markets we service are expanding,” he notes.
With demand high, keeping the system running requires constant maintenance, which is performed by State’s employees.
Much of the burden for keeping things going falls on Plant Manager Dan Swanson and Plant Operator Marc Wright.
“Employee health is a concern more from an operational standpoint (machinery) than a cleanliness issue,” Woosley says. “Safety of our employees in close proximity to the plant machinery is our priority.”
To ensure delivery of a quality product, State Rubber does not provide samples to potential customers unless they are drawn from material produced from a full production run. “Put simply, we adjust the plant to produce a specified material for both particle size and percentages of those sizes,” Woosley says.
Each day brings new challenges as the company strives to “get it right” for customers. “I think we are still learning every day,” Woosley says.
“The evolution of our facility over the past few years has been both challenging and fulfilling for all of us,” he adds. “It is fun to see an idea to improve the process become a reality, especially when it is successful. We are continually trying to build a better mouse trap.”
The author is a contributing editor with the Recycling Today Media Group and can be contacted at curt@curtharler.com.
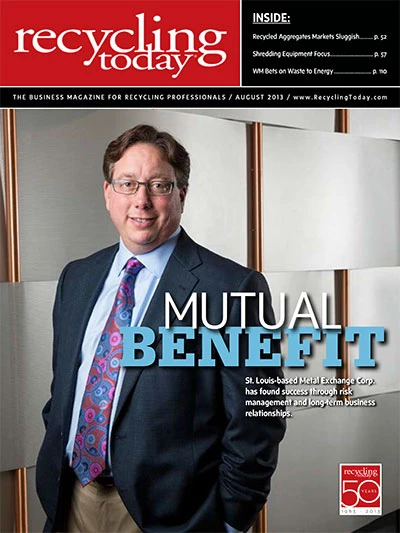
Explore the August 2013 Issue
Check out more from this issue and find your next story to read.
Latest from Recycling Today
- Reconomy brands receive platinum ratings from EcoVadis
- Sortera Technologies ‘owning and operating’ aluminum sorting solutions
- IDTechEx sees electric-powered construction equipment growth
- Global steel output recedes in November
- Fitch Ratings sees reasons for steel optimism in 2025
- P+PB adds new board members
- BlueScope, BHP & Rio Tinto select site for electric smelting furnace pilot plant
- Magnomer joins Canada Plastics Pact